When Marko Verdes, a former Shell and Motiva engineer with three decades of experience, took the stage at our recent Integrity & Reliability Summit, he had one goal: to help professionals rethink the basics. With 24 years at Shell and hands-on knowledge of inspection systems like IMS, Marko shared powerful takeaways from a career spent balancing safety, technology, and operational excellence.
Here are three must-hear lessons from his talk that every reliability engineer, inspector, and asset manager in oil and gas should take seriously.
1. Integrity Culture Isn’t a Buzzword — It’s the Backbone of Your Strategy
Integrity culture is essential across all disciplines and teams. It ensures reliability and safety. Without a strong culture, even the best strategies will fail. It requires alignment across the organization and active communication to break silos between departments like pressure equipment, process safety, maintenance, and operations.
Marko emphasized, “If you don’t have the culture, your strategy won’t work.” It’s not enough to roll out procedures or audits—teams must truly believe in integrity and live it daily. Create an environment where people at all levels feel responsible.
That means:
- Breaking silos between departments through communication (mechanical, rotating, electrical, etc.)
- Empowering staff to stop unsafe work
- Making asset integrity part of everyday decisions
- Everyone must be involved
“Corrosion doesn’t sleep. Integrity has to be constant,” Marko reminds the audience.
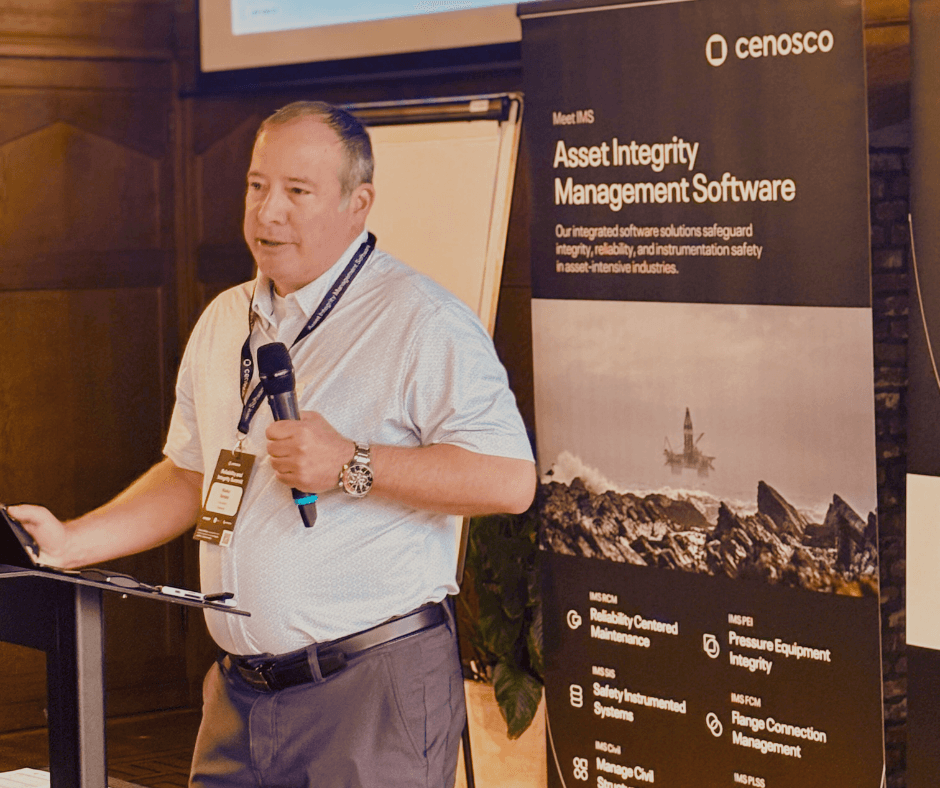
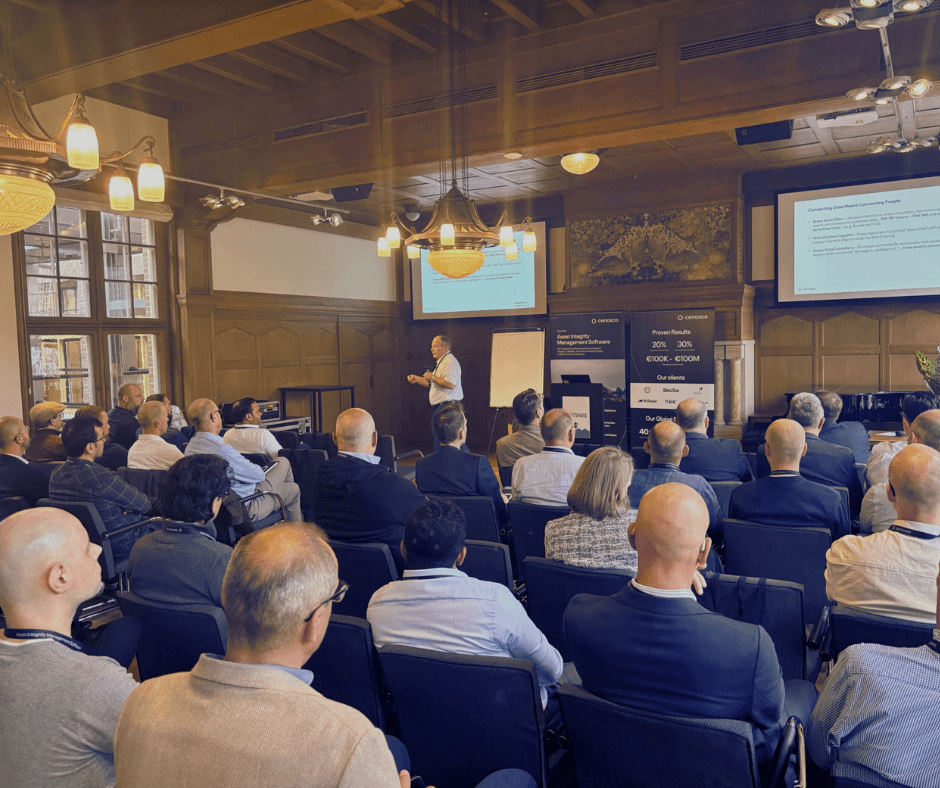
2. Digital Tools Are Great — But Only if They Add Real Value
As a former IMS (Integrity Management System) user, Marko knows the power of connected data. But he warned against going digital just to look modern. In one example, he talked about sites using the IMS PI Viewer to let production teams view inspection data in real-time, leading to faster decisions and fewer blind spots.
If your digital solution makes things take three times longer, it’s not a solution—it’s a new problem. True digital transformation enhances collaboration across departments, eliminates repetitive tasks, and leads to measurable performance gains, not added complexity. To make this work, data must be accessible to all relevant teams, as it empowers informed decision-making at every level, with clear ownership to ensure accountability and shared understanding.
3. Leadership Means Getting the Basics Right — And Holding the Line
In asset integrity management, leadership isn’t about fancy dashboards or the latest tech—it’s about mastering the fundamentals and having the backbone to uphold them. Whether it was clear expectations (“zero overdue” policies) or refusing to accept inspection shortcuts, Marko drove home a simple truth: Basics are not optional.
Great asset integrity programs are built on: leading by example, speaking up when something is off, auditing honestly and welcoming feedback, and learning from every failure, leak, or oversight. Leadership in reliability isn’t about fancy tools—it’s about consistency, accountability, and empowering people to care.
“You don’t hide missed inspections. You own them, learn, and improve.”
Audits and inspections aren’t traps—they’re opportunities. A mature program welcomes them, sees trends, and drives improvements. Technology should make it easier to do things right, not just faster. This means anchoring every process in purpose, not just compliance, and avoiding blind habits (like annual drip pan checks) unless they’re justified.
Core Principles of Integrity Leadership
- Close the Loop – Inspections and findings are only as good as the following actions.
- Lead by Example – Walk the talk. Reliability starts with the way leaders show up every day.
- Communicate Openly – Mistakes happen. Hiding them kills trust. Own them and move forward.
- Empower the Frontline – Foster a culture where technicians feel safe speaking up or halting unsafe work.
- Set Clear Expectations – Be firm but fair, back up expectations with tools, training, and time.
- Build Community – Create channels to share learnings and improvements across teams and sites.
Final Words: Smart Work = Strong Values
As technology evolves in oil and gas, Marko’s message is crystal clear: integrity culture, empowered teams, and practical digitalization distinguish top-performing sites.
If you’re trying to reduce failures, extend asset life, or build a culture of safety, start with these basics. And remember: “It takes everyone.”
Interested in smarter integrity strategies?
Explore our resources on IMS best practices, digital twins in asset management, and integrity audits that work.
Watch the entire presentation here: