Time-based inspections have been the default for decades. They’re familiar, easy to plan, and they create a sense of routine.
The trouble is, not all equipment carries the same level of risk. Some assets might be inspected far too often, while others (the ones most likely to cause major issues), don’t get the attention they deserve. This is where risk-based inspection changes the game. Instead of treating all assets equally, RBI focuses on what matters most: the likelihood of failure and the consequences if it happens. In this article, we’ll look at how time-based and risk-based inspections differ, where each approach fits, and what it takes to move toward a smarter, more proactive way of managing asset integrity.
Index
Time-Based vs Risk-Based Inspection
International Standards Guiding Risk-Based Inspection
How Risk-Based Inspection Works in Practice
Approaches to Risk-Based Inspection
Choosing the Right RBI Approach
Key Factors for Successful RBI Adoption
Choosing the Right Inspection Strategy for Your Assets
IMS PEI: Risk-Based Inspection Software
Time-Based vs Risk-Based Inspection
Inspections are essential for keeping equipment functioning safely and reliably, but not all inspection strategies are created equal. The way you plan and schedule them can mean the difference between wasted effort and a truly effective maintenance program. At their core, there are two very different approaches worth understanding.
Time-Based Inspection
Time-based inspection schedules equipment checks at fixed, pre-determined intervals, regardless of the equipment’s actual condition or usage. For instance, a valve might be inspected every 12 months because that’s what the schedule dictates, not because it necessarily needs attention.
How Time-Based Inspection Works
Driven by regulations and routines: Inspections are often set based on legal obligations, standard maintenance practices, and site experience. During shutdowns: Maintenance teams inspect or overhaul everything to ensure assets are left “as new.”
Benefits of Time-Based Inspection
- Straightforward to plan and execute.
- Creates a predictable workflow for maintenance teams.
Limitations of Time-Based Inspection
- High costs: Inspections during shutdowns are extensive and expensive.
- Inefficiencies: Resources are used on low-risk assets while high-risk issues could emerge between intervals.
- No data-driven focus: Often relies on site knowledge and lacks a systematic, targeted approach—leading to surprises and missed failure modes.
Risikobasierte Inspektion (RBI)
Risk-based inspection introduces a smarter, more strategic method. Here, inspections are planned based on the risk profile of each asset, prioritizing equipment with a higher likelihood of failure and significant consequences.
Benefits of Risk-based Inspection
- Improves plant availability by reducing unnecessary shutdowns.
- Shorter turnarounds and better forecasting for repairs.
- Establishes a systematic, data-driven approach to managing asset threats.
- Demonstrates proof of plant integrity to regulators, insurers, and internal stakeholders.
Limitations of Risk-based Inspection
- Requires a detailed risk assessment.
- More complex to implement than traditional time-based systems.
Time-Based vs Risk-Based: Key Differences at a Glance
Time-Based and Risk-Based Inspections both aim to keep assets safe and reliable, but they go about it in very different ways. One emphasizes simplicity and predictability, while the other focuses on efficiency and long-term value.
To help you see how they compare, let’s take a closer look at their differences across key factors like implementation effort, adaptability, and overall performance.
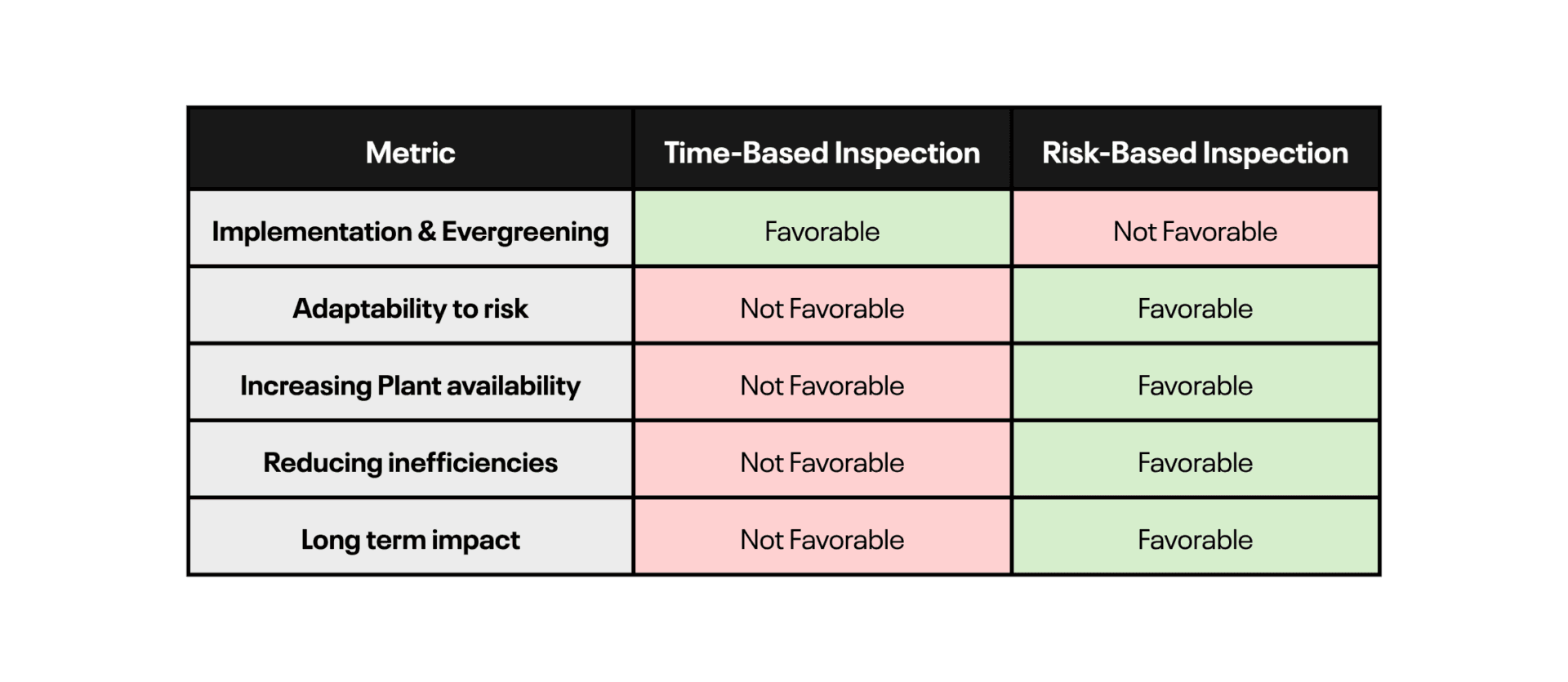
This high-level snapshot gives you a quick sense of how the two approaches compare, but there’s more to the story. To really understand the trade-offs between Time-Based and Risk-Based Inspections, we need to look deeper at how they perform in practice and where each one excels.
Let’s break it down further to see why Risk-Based Inspection is increasingly becoming the preferred choice for organizations aiming to optimize resources and improve long-term asset performance.
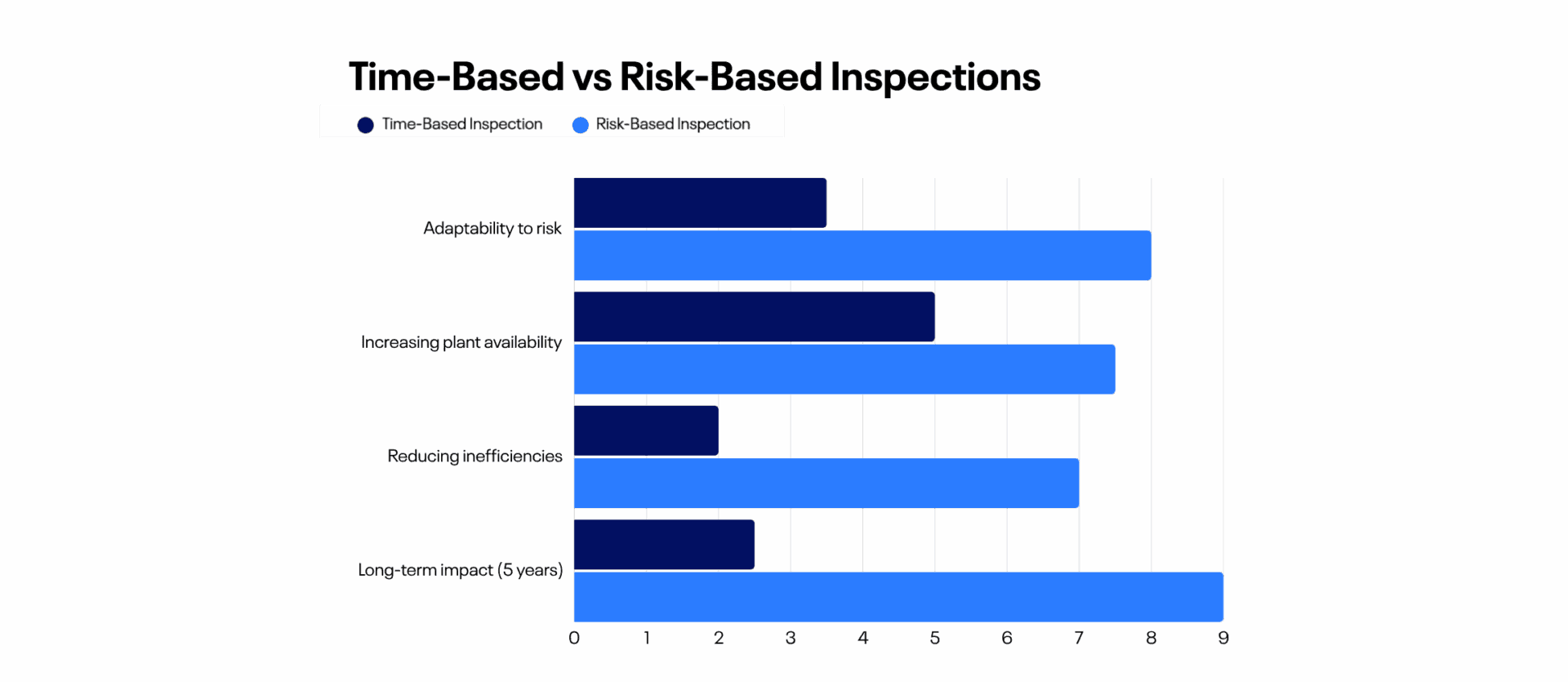
International Standards Guiding Risk-Based Inspection
One of the reasons risk-based inspection has become a trusted methodology across industries is its foundation on well-established international standards and guidelines. These frameworks provide the structure, methodologies, and best practices to ensure RBI programs are consistent, reliable, and effective.
Key RBI Standards and Guidelines
- API 580: Outlines the core concepts and principles of risk-based inspection, serving as a foundational document for RBI programs.
- API 581: Provides a quantitative methodology for calculating risk and determining inspection priorities.
- DNV-RP-G101: Focuses on the RBI of offshore topside static equipment, particularly valuable in oil and gas industries.
- DS/CWA 15740: Covers RBI and maintenance procedures as part of the RIMAP (Risk-based Inspection and Maintenance Procedures) initiative.
- EEMUA 206: A practical guide for the effective use of RBI processes in industrial settings.
Additional references such as API 571, detailing damage mechanisms affecting fixed equipment, and inspection codes like API 510/570/653/576, provide essential technical guidance for implementing RBI programs.
Why Standards Matter
These standards not only help organizations adopt a structured approach to RBI but also:
- Ensure compliance with regulators and insurers.
- Provide consistency across global operations.
- Enable integration of RBI with existing maintenance and inspection systems.
How Risk-Based Inspection Works in Practice
Risk-based inspection is more than just a concept; it’s a structured process supported by data, analysis, and international standards. Let’s break down how it works and explore the different approaches organizations use to implement it effectively.
The RBI Workflow
At its core, RBI is a systematic process for identifying and prioritizing risks, so inspection efforts can be focused on where they need to be most.
- Data and Information Collection: The process begins with gathering operational, maintenance, and inspection data about equipment.
- Risk Analysis: Risk is assessed by evaluating:
- Probability of failure: How likely is the equipment to fail?
- Consequence of failure: What would happen if it does? (cost, safety, environmental impact, etc.)
- Risk Ranking: Each asset is ranked based on its risk profile.
- Inspection Planning: An inspection plan is created, prioritizing high-risk assets while optimizing resources.
- Mitigation and Reanalysis: If necessary, mitigation measures are applied, and the process is repeated periodically to adapt to changes in risk.
This structured workflow allows for proactive maintenance and optimized plant performance.
Approaches to Risk-Based Inspection
Risk-Based Inspection (RBI) is not a one-size-fits-all methodology. Organizations can tailor the approach to match their resources, risk tolerance, and operational complexity. At its core, RBI can be implemented in three ways: Qualitative, Semi-Quantitative, and Quantitative. Each approach offers different levels of precision, data requirements, and ease of use.
Qualitative Risk-Based Inspection
- Based on expert judgment and experience.
- Best for early-stage implementations or when data is limited
Semi-Quantitative Risk-Based Inspection
- Combines qualitative insights with numerical scoring to enhance objectivity.
- A good balance between simplicity and rigor.
Fully Quantitative
- Relies on numerical data and probabilistic methods.
- Ideal for complex operations with rich datasets and a need for high precision.
Comparing RBI Approaches
This comparison outlines the strengths and trade-offs of each method to help organizations determine which approach or combination of approaches best fits their needs.
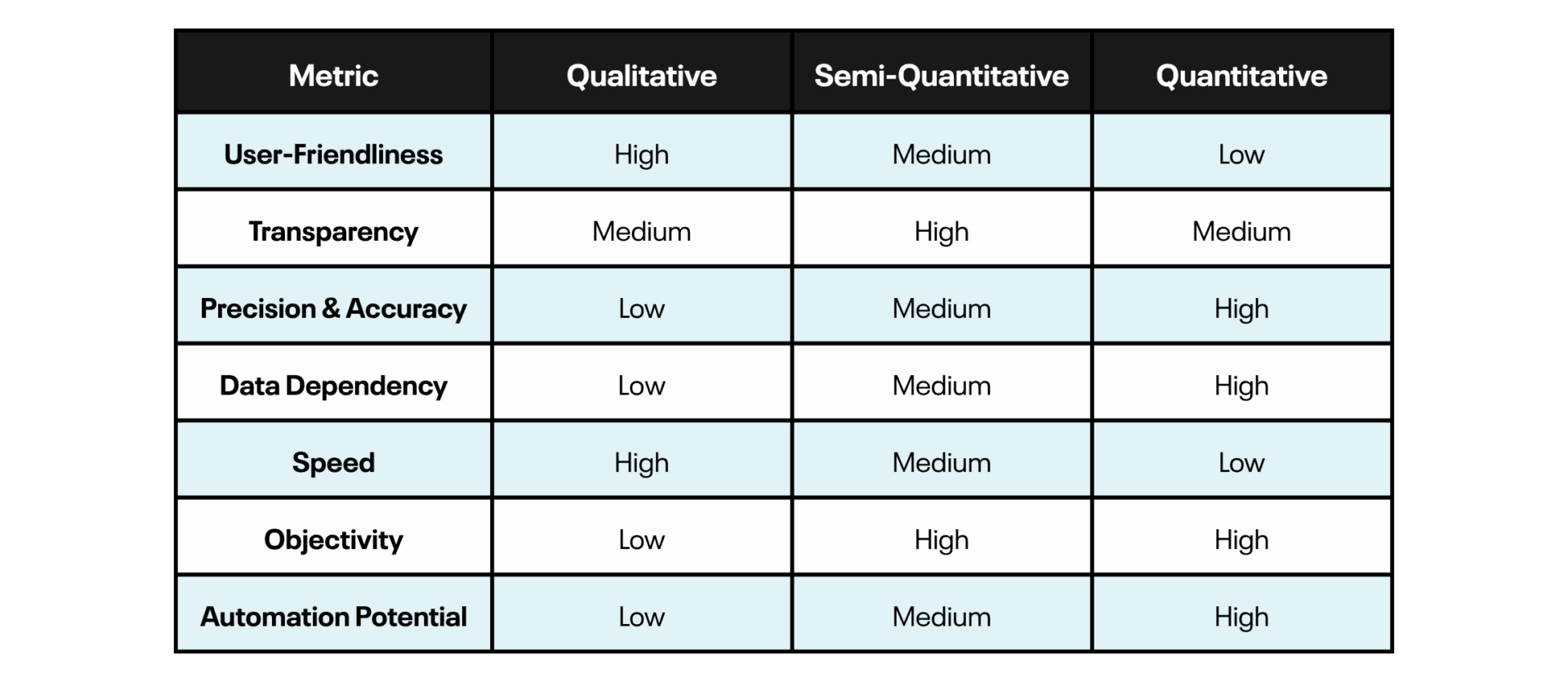
After understanding the strengths and trade-offs of each approach, the next logical step is choosing the right fit. This depends on your resources, risk tolerance, and goals.
Choosing the Right RBI Approach
The real question isn’t which approach is best overall, but which one makes sense for you. That decision comes down to a few key considerations:
- Risk tolerance: How much uncertainty can your organization accept?
- Data availability: Do you have the necessary data for quantitative analysis, or would a qualitative approach be more realistic?
- Time and resources: How much effort can you dedicate to implementing and maintaining the RBI program?
By thoughtfully evaluating these factors, organizations can select an RBI approach that aligns with their goals and constraints. In many cases, a hybrid strategy that combines qualitative and quantitative elements provides the best balance of accuracy and flexibility.
To make this decision easier, it helps to understand where each approach really shines. Some organizations benefit from a straightforward, qualitative method, while others need the precision of a fully quantitative strategy, like API RBI 581. And in many cases, a hybrid approach offers the best of both worlds. To guide your thinking, we’ve pulled together a quick comparison to show where each method brings the most value.
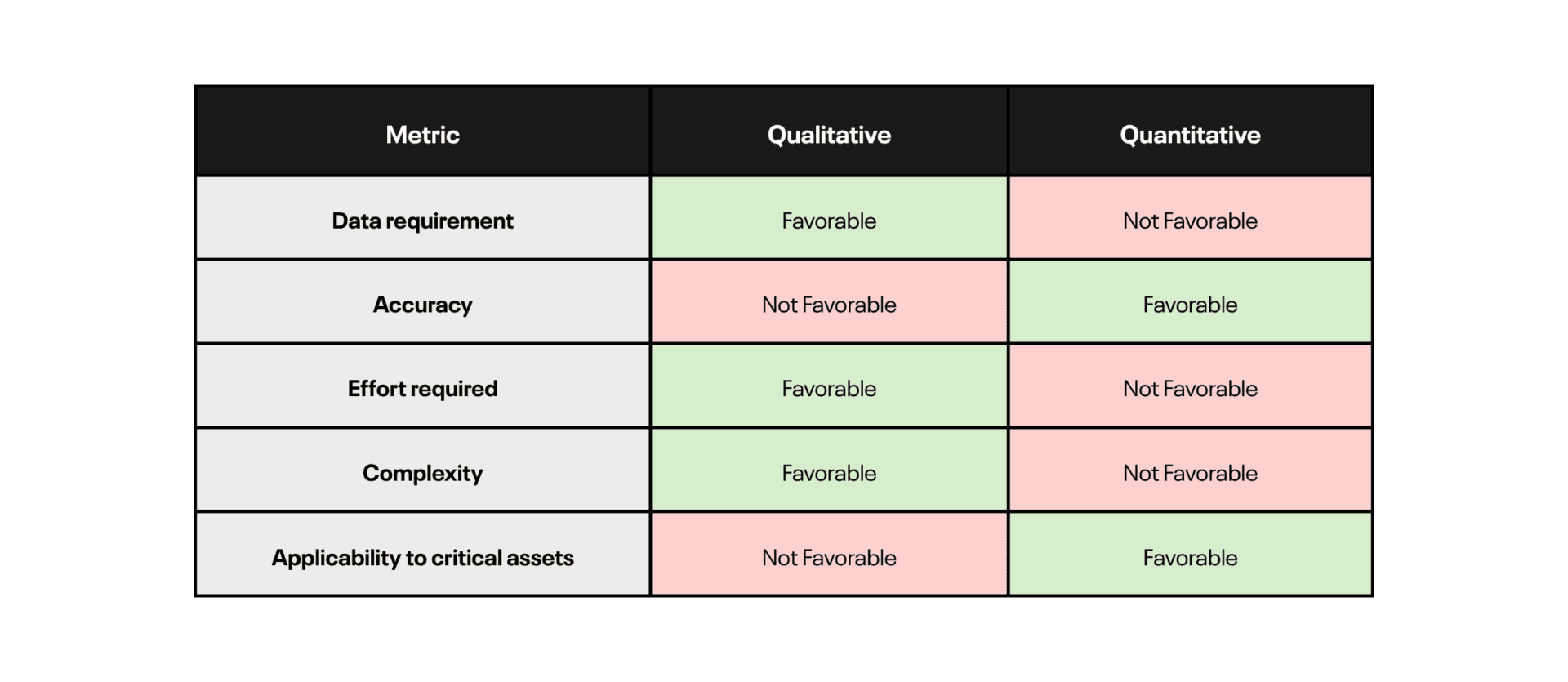
Key Factors for Successful RBI Adoption
Moving to Risk-Based Inspection isn’t just about adopting a new process. It requires the right systems, skills, and mindset across the organization. Here are the key elements that drive successful RBI adoption:
Data Availability
For RBI to work, organizations need access to accurate, timely, and comprehensive data. This enables:
- Data-Driven Decisions: Making inspection plans and risk assessments based on evidence rather than assumptions.
- Leverage Technology: Using modern tools to collect, analyze, and visualize data effectively.
Evergreening
RBI isn’t static. Programs must evolve as new risks, technologies, and data emerge. Evergreening ensures your RBI system stays relevant by:
- Leveraging Technology: Integrating digital tools that support real-time updates and risk reassessment.
- Continuous Improvement: Regularly reviewing and refining processes to align with operational changes.
Cultural Change
Adopting RBI requires a shift in how teams work together. Success depends on fostering:
- Multi-Discipline Collaboration: Bringing together operations, engineering, safety, and maintenance teams.
- Data-Driven Decisions: Building trust in data as the foundation for planning and prioritization.
Knowledge and Skills
People are at the heart of RBI. Building internal capabilities ensures long-term success:
- Training & Expertise: Equipping teams with the technical knowledge and confidence to manage RBI systems.
- Multi-Discipline Collaboration: Encouraging knowledge sharing across teams to improve decision-making and consistency.
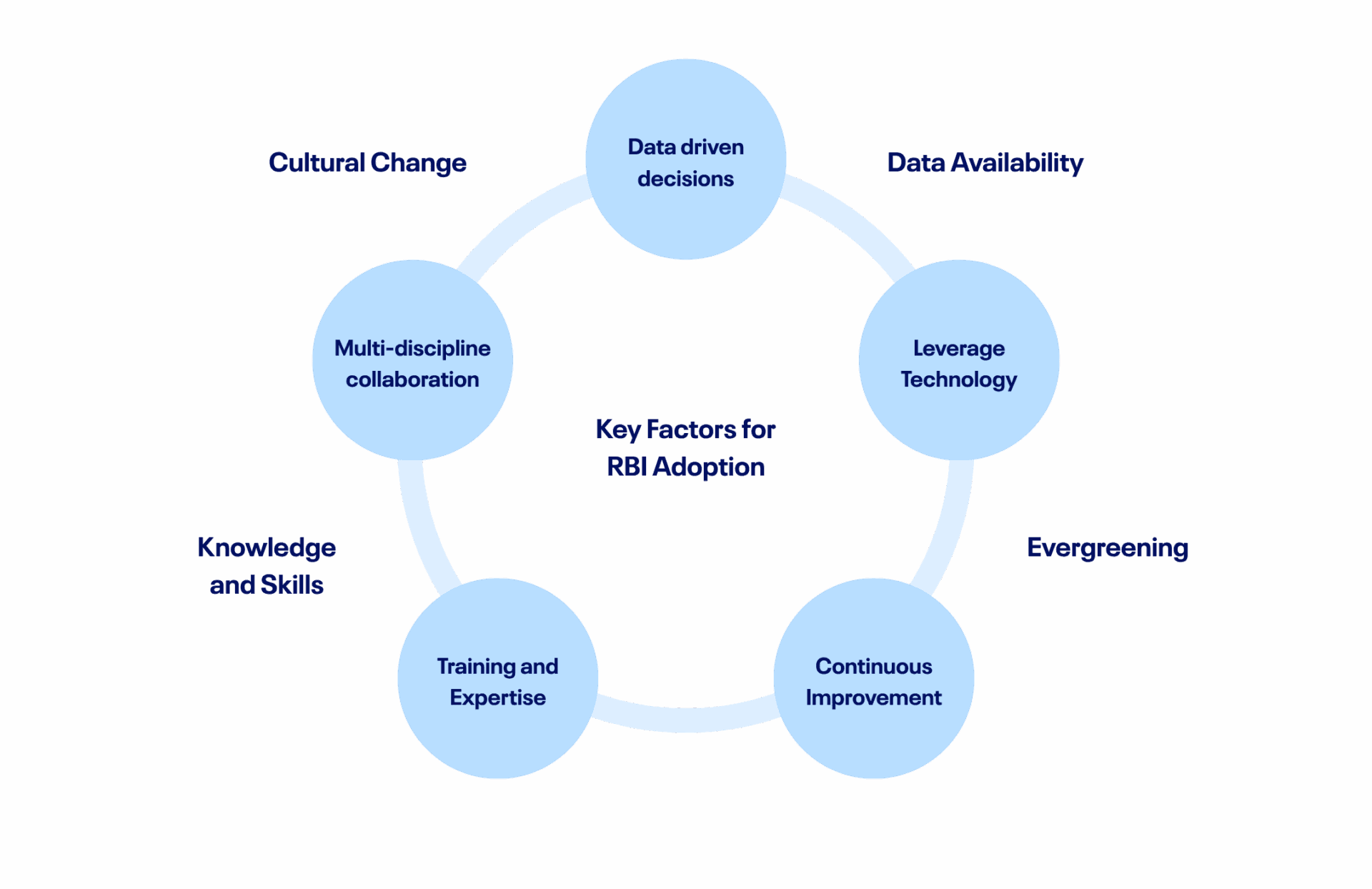
Choosing the Right Inspection Strategy for Your Assets
Time-Based Inspections can still play an important role in environments where risks are low and asset behavior is predictable. They are also a practical choice when regulatory requirements or fixed asset lifespans make Risk-Based Inspections less feasible.
However, for organizations managing complex, high-criticality assets, Risk-Based Inspection offers significant advantages. By focusing on the areas of greatest risk, RBI provides better insight into potential threats and empowers teams to proactively plan and execute mitigations. While implementing RBI requires effort and investment, the long-term return on investment often justifies the resources spent.
Organizations that leverage technology and embrace data-driven decision-making will be best positioned to unlock the full benefits of RBI, improving plant availability, reducing inefficiencies, and extending asset life.
IMS PEI: Risk-based Inspection Software
We’ve talked about the shift from time-based to risk-based inspection and why it matters. But the real question is, how do you take these ideas off the page and make them work in the day-to-day reality of your plant?
This is where IMS PEI comes into play. IMS PEI is more than a tool for tracking inspections. It provides a structured environment to design, execute, and sustain a robust RBI program.
With IMS PEI you can:
- Organize circuits and damage mechanisms into a clear risk framework
- Build inspection plans based on probability and consequence, not arbitrary intervals
- Visualize critical measurement points in 2D and 3D to support decision-making
- Keep your RBI program alive through evergreening as plant conditions change
IMS PEI turns RBI from theory into practice, delivering the precision and consistency needed to make risk-based inspection effective. It supports multiple methodologies, including S-RBI, a Shell-developed approach aligned with API 580 and API 571, available in both qualitative and semi-quantitative formats. Since 2025, it also offers support for the quantitative API 581 methodology, based on the 2016 edition with the 2019 and 2020 addenda.
Ready to begin your Risk-based inspection journey? Cenosco can guide you in selecting the approach: qualitative, semi-quantitative, or fully quantitative, that best suits your operations. Then bring it to life with IMS PEI, the system that transforms strategy into action.
Not Sure Which RBI Approach is Right for You?
Whether you’re exploring qualitative, semi-quantitative, or fully quantitative Risk-Based Inspection, we’re here to help you choose the path that fits your operations best. Request a demo and take the first step toward smarter, safer asset integrity.