In this business case, we take a closer look at how this Oil and Gas supermajor addressed the complexities of maintaining offshore assets in a cost-effective and efficient manner.
Through their choice of implementing Cenosco’s IMS Fabric Maintenance solution, the company enhanced its maintenance processes, improved asset longevity, and optimized budget management.
The Need
The need for change arose for this oil and gas supermajor partly due to documentation practices that had not kept pace with their current needs. Relying on basic spreadsheets, the team categorized maintenance needs in vague terms like “need to paint now” or “need to paint later,” which didn’t allow for detailed insights or prioritized planning. This system also limited the leadership’s ability to make informed decisions and, more critically, made it challenging to allocate budgets effectively, especially as maintenance costs continued to rise.
With fabric maintenance facing intense budget constraints, the company needed a solution that could demonstrate the value of these preventive efforts in prolonging asset life and minimizing future replacement costs.
The company’s legacy maintenance approach presented three primary challenges:
Lack of Prioritization and Risk Assessment
Tasks were not prioritized based on risk, urgency, or asset condition, which meant that maintenance activities were often reactive rather than proactive, leading to inefficiencies.
Limited Visibility and Planning
Managing hundreds of individual maintenance tasks across multiple asset locations was overwhelming, as spreadsheets did not provide the structured, visual representation required for efficient planning.
Data Limitations for Budget Justification
Without a structured system, it was nearly impossible to generate data to support budget requests, making it difficult to defend preventive maintenance spending, particularly in areas like painting, which are crucial for asset longevity.
The Solution
These challenges highlighted the need for a comprehensive, data-driven solution to streamline maintenance activities and provide leadership with actionable insights.
As this supermajor was already leveraging the existing use of other IMS modules, such as IMS PEI, IMS Civil, IMS RCM, and IMS PLSS — implementing IMS Fabric Maintenance became a strategic choice, ensuring seamless integration within the same ecosystem and maximizing the benefits of their current investments.
Essentially, IMS Fabric Maintenance is a specialized use case of IMS PEI with IMS Civil. One of the key capabilities IMS introduced was the concept of “block areas.” With this feature, assets could be organized into manageable zones or “blocks,” allowing the maintenance team to prioritize work by specific locations and conditions.
For the first time, maintenance efforts could be allocated based on actual asset conditions and urgency, bringing structure and visibility to the overall fabric maintenance plan. This enhanced organization was complemented by IMS’s Dynamic Forms – a flexible tool that replaced spreadsheet-based records. With this tool checklists were designed to document each quality assurance checkpoint, providing a clear visibility into the steps executed during the maintenance process, ensuring consistent monitoring and upholding the company’s rigorous quality standards for every task.
IMS also enabled a risk-based scoring system that transformed maintenance prioritization. Each maintenance task could now be evaluated based on the area’s condition (good / fair / poor), complexity (derived from things like number of corrective actions for that area), and the specific location within the asset.
This scoring system not only helped prioritize tasks based on risk but also supported planning around other maintenance activities, like inspections or replacements, ensuring the most efficient use of time and resources. Additionally, the platform allowed inspectors to estimate square footage requirements and assess the manpower, budget, and materials needed, giving leadership a clear picture of the resources required for each project.
This predictive ability made it possible to create a more accurate, transparent budget, allowing the team to allocate resources efficiently and justify spending on fabric maintenance, particularly on high-value items like paint.
The Result
Enhanced Maintenance Efficiency
Following the implementation of IMS FMA, the company found that their maintenance efficiency had greatly improved. With a clearer prioritization structure in place, the team can now execute maintenance tasks more efficiently, achieving a higher volume of work with fewer resources. This optimized approach has not only reduced costs but also maintained the high-quality standards necessary for long-term asset performance.
Long-Term Cost Savings and Asset Longevity
One of the most substantial benefits of IMS has been its impact on long-term cost savings and asset longevity. Thanks to the new scoring and prioritization systems, the company can address maintenance proactively, which is far more cost-effective than reactive approaches. For example, timely painting is now strategically managed to extend the life of critical assets, avoiding the steep costs associated with asset replacement. In fact, the company estimates that delaying painting for certain assets would have resulted in replacement costs approximately four times higher than the costs to paint. Additionally, the consistent use of the Dynamic Form Checklist has proven to be cost-effective, as following these procedures consistently yields the best results.
Empowering Leadership with Real-Time Insights
Leadership now has access to powerful, real-time insights into asset conditions, thanks to IMS’s reporting capabilities. The platform enables data-driven decisions that balance the cost of maintenance with the risk of asset deterioration, helping to preserve asset value over time. The increased visibility into maintenance requirements has also allowed for better budget forecasting and resource allocation. Leadership can now approach maintenance budgets with a high degree of confidence, knowing they have a clear view of the condition, cost, and criticality of each asset.
Conclusion
The adoption of IMS Fabric Maintenance has marked a turning point in the company’s approach to asset management. By moving away from a reactive, spreadsheet-based system and embracing Cenosco’s data-driven platform, the company has been able to make strategic decisions that optimize maintenance efforts, protect asset integrity, and reduce costs. IMS Fabric Maintenance has empowered the company to align its maintenance program with both operational and budgetary goals, proving that data-driven insights can drive both immediate and long-term value.
Complemento del paquete IMS
IMS Fabric Maintenance (IMS FMA) is designed to complement and integrate seamlessly with other IMS modules like IMS Pressure Equipment Integrity (IMS PEI) and IMS Civil. While IMS PEI focuses on the integrity of pressure equipment, IMS FMA extends this by managing the condition of the asset’s fabric, such as coatings and surface maintenance. Additionally, IMS FMA works alongside IMS Civil to address the structural aspects of assets, ensuring a comprehensive approach to asset integrity. This interconnectedness allows for better coordination, prioritization, and decision-making, enabling a holistic, data-driven maintenance strategy that maximizes asset performance and extends asset life.
Solicitar una demostración
Fill out the form below to get your IMS Journey started.
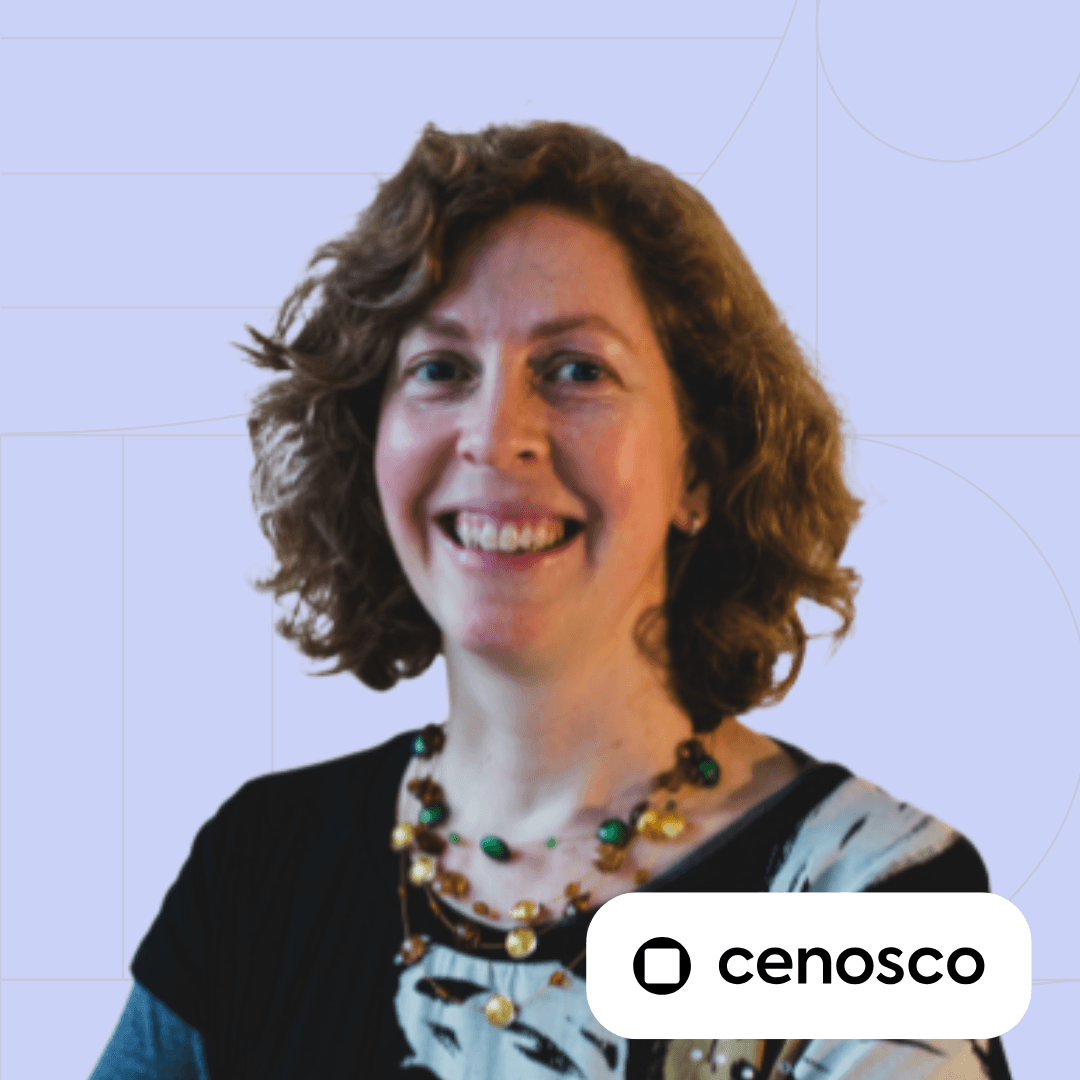
Elsa Tolsma-de Klerk Technical Writer
Elsa is an engineer with a passion for sharing knowledge. She holds a Master’s in Electronic Engineering and spent over a decade at Sasol as an Advanced Process Control Engineer, where she gained hands-on experience in optimization, control systems, and writing technical documentation. Since 2019, she’s been a Technical Writer at Cenosco, now leading the IMS knowledge base and training Academy team.