You’ve invested loads of money into software to manage equipment schedules, thinking it’s your safety net against downtime and costly failures. But here’s the deal: what if it’s not working as well as you think? Are you really sure that all those inspections, maintenance routines, and repairs are actually reducing risk – or are they just giving you a false sense of security?
Here’s the truth: Most traditional equipment schedules fail to live up to their promise. Instead of being tools for proactive risk mitigation, they often devolve into compliance-driven box-checking exercises. This approach doesn’t just waste resources, it leaves you vulnerable to hidden risks that could lead to catastrophic failures.
At the same time, oil and gas companies are under pressure to maximize their return on investment while operating their physical assets safely and sustainably. To succeed, resources must be used efficiently, and equipment failures proactively avoided. If you want to stay ahead, it’s time to rethink your equipment schedules and ask tough questions.
What Exactly Is an Equipment Schedule?
An equipment schedule is a structured framework for planning, executing, and tracking activities throughout an asset’s lifecycle. It outlines when, how, and on which equipment tasks will be completed. Here’s a quick look at the key types of schedules:
- Inspection Schedules: Define the frequency and scope of checks to detect issues early, such as corrosion monitoring and weld inspections.
- Assessment Schedules: Set timelines for technicians to analyze findings and assess conditions.
- Test Schedules: Specify when performance tests must occur.
- Preventive Maintenance Schedules: Focus on routine tasks to prevent failures.
- Repair Schedules: Address reactive maintenance when breakdowns occur.
By systematically organizing these activities, equipment schedules aim to reduce risks while maximizing uptime and asset utilization. However, their effectiveness depends on more than just adherence – they must evolve with operational demands and leverage advanced technologies for optimization.
The Risk-Reduction Illusion: Common Pitfalls
Despite their importance, not all equipment schedules deliver on their promise of reducing risk. Several critical shortcomings often undermine their effectiveness:
- Data Overload: Traditional scheduling methods can generate vast amounts of data without providing actionable insights. For that reason, teams often struggle to sift through this noise to identify critical signals that indicate potential equipment failures or safety issues. This data overload can lead to analysis paralysis, where valuable information is lost amid irrelevant data, hindering timely decision-making, resulting in unplanned downtime and increased safety risks. For instance, failing to replace worn components on time can result in cascading failures across interconnected systems.
- Static Time-Based Intervals: Rigid schedules that don’t account for real-time asset conditions can lead to inefficiencies—either by performing unnecessary maintenance or overlooking emerging risks in high-stress environments like offshore platforms.
- Limited Scope: Many traditional schedules focus primarily on compliance, aiming to meet minimum regulatory requirements rather than adopting a comprehensive approach to risk mitigation. In the context of oil and gas, frameworks like API 580 and API 581 ensure legal compliance but often overlook unique industry risks such as equipment failures or environmental hazards.
- Siloed Data Management: Disconnected systems or manual processes create blind spots in tracking overdue tasks or prioritizing critical repairs, delaying responses to potential hazards. This fragmentation often stems from a “silo mentality” where departments focus solely on their own indicators, rather than aligning with overall project objectives. This lack of integration, particularly between essential systems like CMMS and ERP, hinders the seamless flow of data, making it difficult to achieve a unified view of maintenance operations, inventory levels, and work orders.
- Lack of Risk-Based Prioritization: Failure to focus on high-consequence assets—such as pipelines, compressors, or pressure vessels—can amplify the impact of failures, both financially and operationally. For example, a sudden failure in a main compressor can halt production entirely, leading to significant downtime, lost revenue, and delivery delays.
- Absence of Standardized Practices: Inconsistent maintenance practices result in reactive strategies and arbitrary timelines. Critical assets are left under-monitored and under-serviced as a result.
Proving Your Equipment Schedule Reduces Risk
Alright, so we’ve established the problem: traditional equipment schedules often fail to deliver on their promise. They’re rigid, compliance-driven, and leave you vulnerable to risks you didn’t even know existed. In the chemical and oil and gas industry, this is not just an inconvenience, it is a critical issue. If you’re relying on these outdated systems, you’re playing defense when you should be playing offense. Here’s how you can turn things around and ensure your equipment schedule delivers real risk reduction.
Define Clear KPIs
First things first – if you don’t measure it, you can’t improve it. Focus on metrics that are directly relevant to oil and gas operations, such as:
- Reducing unplanned downtime caused by equipment failures.
- Cutting safety incidents related to corrosion or structural integrity issues.
- Improving compliance with inspection protocols like API 580/581 standards.
- Boosting assets’ uptime by preventing premature degradation.
- Lowering maintenance costs through optimized scheduling.
Advanced metrics like planned maintenance ratios, mean time between failures (MTBF), and adherence to preventive measures provide deeper insights into system performance. These data points don’t just look good, they validate whether your schedule is actively protecting critical assets and improving operational reliability.
Implement a Risk-Based Approach
In oil and gas operations, certain assets – such as pipelines, pressure vessels, or offshore platforms – pose significantly higher risks than others. A risk-based approach allows engineers to prioritize inspections and maintenance tasks based on the likelihood and consequences of failure for each asset.
Corrosion engineers can use techniques like Risk-Based Inspection (RBI) to identify the components most susceptible to failure or those whose failure would have the most significant consequences. Subsequently, inspection efforts are focused on these high-risk components to facilitate early detection of potential problems.
Reliability Centered Maintenance (RCM) helps optimize maintenance strategies through detailed root cause analysis and failure mode identification for each equipment. RCM enables you to:
- Figure out why each piece of equipment might fail (like bearing failure or fouling, etc.).
- Decide which task to perform and when to perform it in order to prevent the equipment from failing.
- Only do maintenance when it’s really needed, balancing risks and costs to ensure reliability while minimizing unnecessary interventions
For assets integral to daily production goals, RCM provides a roadmap for prioritizing and assigning maintenance activities based on their importance to operational continuity. By leveraging RBI to identify high-risk components and RCM to optimize maintenance strategies, these methodologies refine equipment schedules to prioritize critical assets and minimize operational risks, ensuring continuity in oil and gas operations.
Embrace Dynamic Scheduling and AI
While static schedules have long been a standard in the oil and gas industry, today’s fast-paced environment is opening up exciting new possibilities for inspection and maintenance equipment schedules. Dynamic scheduling, for example, allows plans to adapt in real time based on actual equipment health, using data from IoT sensors, condition monitoring systems, and predictive analytics tools. Imagine receiving automated alerts when corrosion rates exceed thresholds or when vibration analysis indicates early signs of wear in rotating machinery. This allows engineers to act before minor issues escalate into major failures. Flexibility isn’t just a buzzword. It’s how inspection teams stay ahead of risks while optimizing resource allocation in complex environments like offshore rigs or refineries.
Multi-agent systems (MAS) offer another smart way to manage inspection and maintenance schedules dynamically. Powered by AI and leveraging reinforcement learning, these systems consist of multiple autonomous agents that collaborate and continuously learn from real-time data to optimize scheduling decisions. For example, a MAS model developed for a petroleum refinery in Algeria used reinforcement learning (SARSA algorithm) to dynamically plan maintenance tasks, demonstrating efficient scheduling for predictive and corrective maintenance. Multi-level systems adapt quickly to changes like equipment issues or unexpected events, rescheduling tasks to minimize downtime and optimize resources. Over time, the system improves its scheduling efficiency by learning from past outcomes. This makes maintenance planning more flexible, proactive, and efficient compared to traditional static schedules.
Integrate Your Systems
Disconnected systems pose a significant obstacle to effective scheduling in oil and gas operations. Integrating your equipment schedule with CMMS (Computerized Maintenance Management Systems), ERP (Enterprise Resource Planning), and IoT platforms ensures seamless data flow across departments to comply with industry regulations. This integration enables:
- Real-time alignment of maintenance schedules with inventory availability to avoid delays caused by missing parts.
- Coordination between inspection teams and production timelines to minimize disruptions during shutdowns or repairs.
- Holistic visibility into asset health for informed decision-making at every level of operation.
Key Components of an Effective Equipment Schedule
An effective equipment schedule must be more than a static document – it should be a dynamic tool powered by advanced technologies that meet the unique challenges of the industry. In this section, we will outline the essential features every equipment scheduling system must have, along with additional capabilities that can elevate its functionality.
Core Components
At the foundation of any equipment scheduling system, there are essential features that ensure smooth operations and risk reduction:
- Precise scheduling by date/time for inspections, tests and maintenance tasks.
- Detailed equipment identification (type, model, serial number).
- Specific location data for assets across facilities or offshore sites.
- Precise inspection points mapped to specific areas prone to degradation, such as weld seams, flange connections, or designated measurement locations on pipelines and pressure vessels.
- Detailed list of tasks that need to be performed depending on the schedule type, like ultrasonic testing of weld seams for inspection schedules or replacing worn gaskets for corrective ones.
- Allocation of tasks to specific personnel or teams for accountability.
- Real-time status tracking for all scheduled activities (pending/in-progress/completed).
- Notes for documenting observations during inspections or repairs.
- Cross-disciplinary integration enabling departments to share and coordinate tasks and schedules effectively, fostering enhanced collaboration and operational efficiency.
Advanced Features for Optimization
To elevate your equipment schedule’s performance and adaptability, consider integrating advanced features:
- Centralized Database: Store all asset details for easy access across teams.
- Real-Time Tracking: Use IoT sensors to monitor equipment health, dynamically schedule maintenance based on actual condition.
- Automated Scheduling: Reduce manual errors with software-driven task planning.
- Integration with Other Systems: Enable holistic management and informed decision-making.
- Risk Assessment: Prioritize tasks based on RBI and RCM methodologies.
- Mobile Accessibility: Enable field engineers to access and update schedules remotely, ensuring real-time adjustments and offline functionality with automatic synchronization upon reconnection.
- Reporting and Analytics: Leverage real-time dashboards and customizable reports to monitor key metrics such as equipment utilization, maintenance costs, and downtime trends.
- Deferral Management: Incorporate a structured process for assessing risks and obtaining approval when tasks cannot be executed as planned, ensuring accountability while mitigating potential impacts on safety and operations.
- Notification Systems: Automated alerts for schedule changes or compliance issues keep personnel informed and proactive.
- Lifecycle Management: Planning equipment integrity management from acquisition to disposal optimizes maintenance strategies to extend lifespan and reduce costs.
By combining core components with advanced features like real-time tracking and lifecycle management, your equipment scheduling system becomes a dynamic tool capable of adapting to real-world challenges while minimizing risks and maximizing efficiency.
Best Practices for Effective Equipment Scheduling
To maximize the impact of your equipment schedules, follow these best practices:
- Centralize Data with an Integrity Management System (IMS): Create a single source of truth for all equipment-related information, including availability, maintenance history, and status, by leveraging an advanced Integrity Management System (IMS). These tools integrate seamlessly with systems like CMMS and ERP, offering features such as risk-based inspection (RBI) modules, dashboards, and predictive analytics to prioritize tasks effectively and reduce downtime.
- Standardize Processes: Establish uniform procedures for inspections, repairs, and preventive maintenance to eliminate confusion among teams.
- Train Your Team: Even the most advanced tools are only as good as the people using them—invest in training programs.
- Leverage Automation: Use automation tools to handle routine tasks like sending reminders for upcoming maintenance or flagging conflicts in schedules.
- Continuously Monitor and Adjust: Regularly review schedules using feedback from technicians, comprehensive data (including equipment performance and condition histories), and operational priorities to ensure alignment with evolving integrity and reliability needs, and improve overall efficiency.
Linking these best practices to risk reduction guarantees that each action taken contributes to safer operations by removing blind spots in asset management and enhancing consistency across teams, ultimately minimizing vulnerabilities associated with human error or outdated processes.
Leveraging Cenosco’s IMS for Proactive Risk Reduction
To truly transform your equipment schedules into proactive risk mitigation tools, consider leveraging a comprehensive Integrity Management System (IMS) like Cenosco’s. Cenosco IMS streamlines the scheduling of all types of maintenance and inspection activities, from routine inspections to critical repairs, helping you standardize your processes along the way. Data and findings are recorded within the IMS as Equipment Condition Histories (ECHs), allowing you to see the history and status of your equipment, plan for the future, and connect schedules to your ECHs. These IMS schedules enable automatic generation of notifications and work orders, updating inspection and maintenance plans, and linking directly to your CMMS.
By supporting Risk-Based Inspection (RBI) and Reliability Centered Maintenance (RCM) methodologies, IMS provides detailed risk analysis, enabling more efficient planning of inspections and maintenance based on risk levels, degradation mechanisms, and potential failure modes.
IMS features easy-to-read dashboards that offer at-a-glance insights into asset health, allowing you to proactively identify and address potential issues before they escalate. With IMS, you gain visibility into schedules and tasks across multiple disciplines. This fosters better alignment and optimization of resources, ensuring that all teams are working from the same up-to-date information. You can also track every step, from planning to scheduling to execution, and stay on top of tasks that are due.
You’ve got a choice. You can keep thinking your equipment schedules are keeping you safe. Or you can start knowing.
This isn’t about feel-good metrics; it’s about real-world risk. Centralize your data, integrate your systems, and use real-time insights.
The roadmap is here. Execute. Then measure it thoroughly. Your assets, your people, and your bottom line depends on it.
开始
Do you want to see IMS in action? Fill out the form below and get started with a demo.
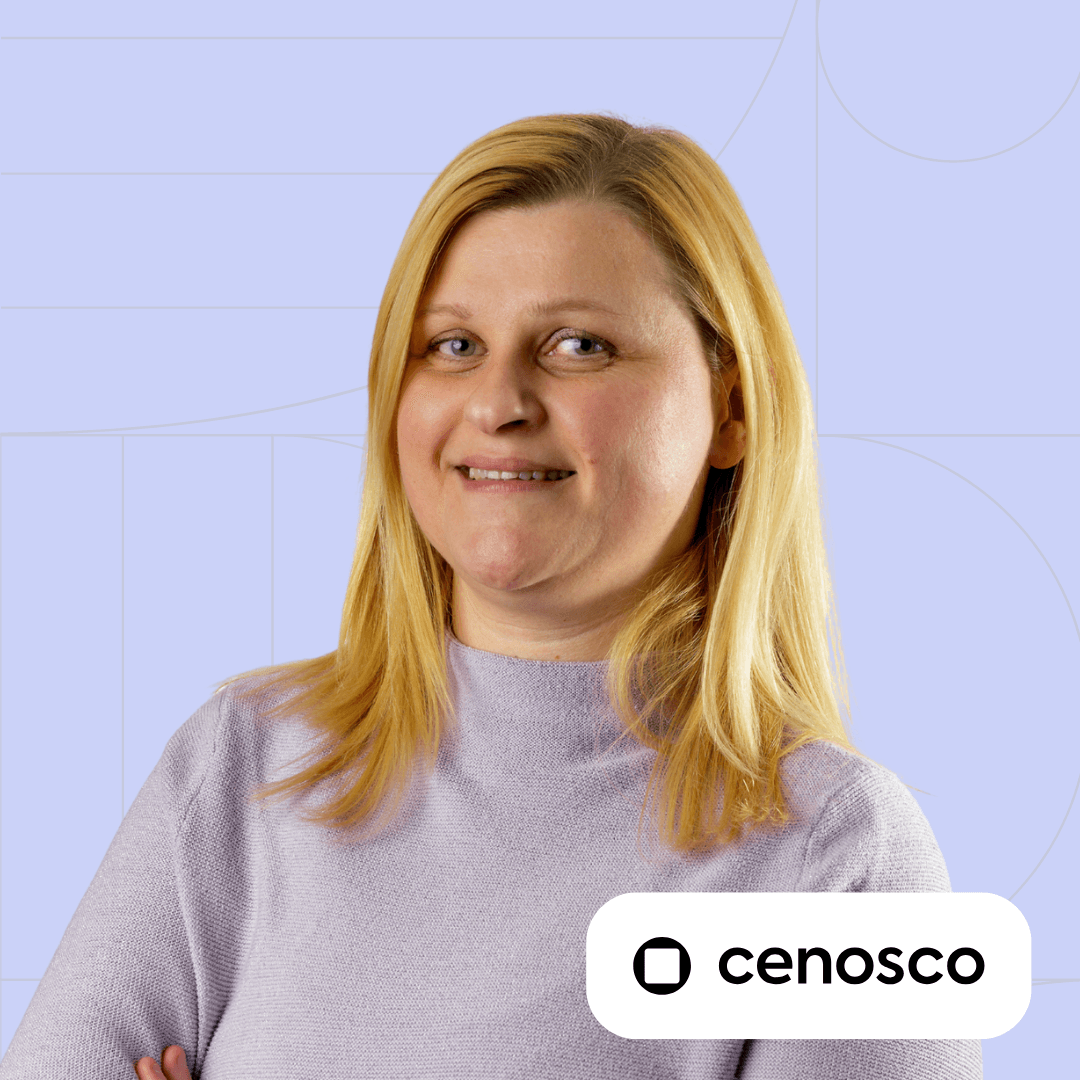
Denis Tkalec Technical writer
Denis Tkalec is a technical writer at Cenosco, specializing in asset integrity management software since 2022. With a background in education and six years in marketing, she turns complex topics into clear, user-friendly content. Inspired by Camus’s belief that “a writer keeps civilization from destroying itself,” she brings precision and care to every manual.