API 581, entwickelt vom American Petroleum Institute (API), ist ein zentraler Standard für risikobasierte Inspektionen (RBI).
Es bietet eine quantitative Methodik für die Erstellung von Inspektionsplänen, die auf das mit den einzelnen Ausrüstungsgegenständen und ihren Komponenten verbundene Risiko zugeschnitten sind.
Dieser Ansatz gilt für verschiedene Arten von unter Druck stehenden ortsfesten Ausrüstungen, einschließlich Druckbehältern, Rohrleitungen, Tanks, Druckentlastungsvorrichtungen (PRDs) und Wärmetauscherrohrbündeln.
Bevor wir uns näher mit API 581 befassen, sollten wir sie von API 580 unterscheiden: API 580 legt die allgemeinen Grundsätze und Mindestrichtlinien für RBI fest.
Andererseits geht API 581 noch einen Schritt weiter, indem es präzise quantitative Methoden für die Formulierung eines Inspektionsplans bereitstellt. In diesem Artikel werden wir die Berechnungsmethoden der API 581 näher erläutern.
Die API 581 Risikoberechnung
Die Risikoberechnung nach API 581 umfasst zwei Hauptkomponenten:
- Ausfallwahrscheinlichkeit (Probability of Failure - POF): Sie wird durch die Analyse der Wahrscheinlichkeit eines Geräteausfalls bestimmt. Dabei werden Faktoren wie Materialeigenschaften, Betriebsbedingungen und Schadensmechanismen berücksichtigt.
- Versagensfolgen (COF): Bei der Bewertung werden die potenziellen Auswirkungen eines Geräteausfalls berücksichtigt, darunter Sicherheitsrisiken, Umweltschäden und finanzielle Verluste.
Das Risiko ist die Ausfallwahrscheinlichkeit (Probability of Failure, POF) in Kombination mit der Ausfallfolge (Consequence of Failure, COF):
Risiko = POF x COF
Die Norm API 581 ist in verschiedene Teile untergliedert. Teil 2 konzentriert sich auf die Bestimmung der Ausfallwahrscheinlichkeit in einer API-RBI-Bewertung, während Teil 3 die Durchführung einer Folgenanalyse in einer API-RBI-Bewertung behandelt. Schauen wir uns die Details an, die in der Norm beschrieben sind.
API 581 - Ausfallwahrscheinlichkeits-Methode (POF)
API 581 Teil 2 befasst sich mit der Berechnung der Ausfallwahrscheinlichkeit (Probability of Failure, POF). Es werden zwei Methoden empfohlen:
- Die GFF-Methode: Die GFF-Methode (Generic Failure Frequency) prognostiziert die Ausfallwahrscheinlichkeit (Probability of Failure, POF) für den Verlust des Sicherheitsbehälters bei druckbegrenzten Anlagen. Sie passt die generischen Ausfalldaten der Industrie an die spezifische Ausrüstung an, indem sie einen Schadensfaktor (DF) und einen Managementsystemfaktor (FMS) einbezieht.
- Die Zwei-Parameter-Weibull-Verteilungsmethode: Die Weibull-Verteilungsmethode wird zur Vorhersage der Ausfallwahrscheinlichkeit (Probability of Failure, POF) für Druckentlastungsvorrichtungen (PRDs) und Wärmetauscherbündel verwendet. Diese Methode nutzt die statistische Weibull-Verteilung zusammen mit Skalen- und Formparametern, um die exponentielle Darstellung der POF über einen bestimmten Zeitraum zu liefern.
Die GFF-Methode
Gehen wir ein wenig näher auf die allgemeinere GFF-Methode ein. Die GFF-Formel bestimmt die Wahrscheinlichkeit, dass ein Ausrüstungsgegenstand aufgrund einer bestimmten Art von Schaden versagt:
Pf(t) = gff * FMS * Df(t)
wo:
- Pf(t) is the Probability of failure (POF) as a function of time;
- gff ist die generische Ausfallhäufigkeit;
- FMS ist der Faktor Managementsystem; und
- Df(t) ist der Gesamtschadensfaktor in Abhängigkeit von der Zeit.
Die generische Fehlerhäufigkeit (GFF)
Die generische Fehlerhäufigkeit (GFF) ist auf einen Wert festgelegt, der für die Fehlerdaten der Raffinerie- und Petrochemieindustrie repräsentativ ist. Diese GFFs sind in API 581, Teil 2, Tabelle 3.1 aufgeführt. Für die Modellierung von Freisetzungsszenarien (von einem kleinen Leck bis zu einem Bruch) werden vier Lochgrößen verwendet, und die Fehlerquote wird auf 3 % bis 10 % festgelegt.
Der Faktor Verwaltungssystem (FMS)
Der Management-System-Faktor (FMS) berücksichtigt die Wahrscheinlichkeit, dass sich anhäufende Schäden, die zu einem Verlust des Sicherheitsbehälters führen, erkannt werden, bevor sie kritisch werden. Er steht in direktem Zusammenhang mit der Wirksamkeit des mechanischen Integritätsprogramms einer Anlage und wird einheitlich auf alle Komponenten innerhalb der Anlage angewendet. Dabei werden Faktoren wie die Qualität der Inspektionen, die Wirksamkeit des Korrosionsschutzes und die Einhaltung geeigneter Materialien und Konstruktionsvorschriften berücksichtigt. Die Bestimmung des FMS beinhaltet in der Regel eine strukturierte Bewertung, die einen Fragebogen oder ein Punktesystem umfassen kann.
Der Schadensfaktor (DF)
Die grundlegende Funktion des Schadensfaktors (DF) ist die statistische Bewertung des Schadensausmaßes, das in Abhängigkeit von der Betriebszeit vorhanden sein kann, und der Wirksamkeit der Inspektionstätigkeit zur Quantifizierung dieses Schadens. Der DF wird auf der Grundlage von Faktoren wie:
- Anwendbare Schadensmechanismen;
- Materialien der Konstruktion;
- Prozessdienst;
- den physischen Zustand des Bauteils; und
- Inspektionstechniken (und Häufigkeit) zur Quantifizierung des Schadens.
API 581 enthält DFs für die folgenden acht Mechanismen:
- Ausdünnung (sowohl allgemein als auch lokal);
- Beschädigung der Bauteilauskleidung;
- Äußere Schäden (Ausdünnung und Rissbildung);
- Spannungsrisskorrosion (SCC);
- Hochtemperatur-Wasserstoffangriff (HTHA);
- Mechanische Ermüdung (nur Rohrleitungen);
- Sprödbruch, einschließlich Sprödbruch bei niedrigen Temperaturen, Versprödung bei niedrigen Legierungen, Versprödung bei 885 °F; und
- Sigma-Phasenversprödung.
In the API 581 standard, you’ll find detailed instructions for carrying out each of these DF calculations. Typically, a multitude of input parameters are needed for a single damage factor calculation.
API 581 - Methodik der Fehlerfolge (COF)
In Teil 3 der Norm API 581 werden Techniken zur Berechnung der Versagensfolge (COF) vorgestellt, wobei zwei Methoden angeboten werden:
- Stufe 1: Verwendet vordefinierte Variablen für häufig vorkommende Flüssigkeiten.
- Stufe 2: Ein strengerer Ansatz, der sich für jede Fluidstromzusammensetzung eignet.
Stufe 1 stützt sich auf Gleichungen mit einer Reihe bekannter Variablen, die auf typische Flüssigkeiten in Raffinerien und petrochemischen Anlagen zugeschnitten sind. Sie eignet sich für Situationen, in denen die Zusammensetzung der Flüssigkeit bekannt ist und in den Bereich der Standardparameter fällt.
Stufe 2 hingegen bietet eine gründliche Analyse komplexer oder undefinierter Flüssigkeitszusammensetzungen. Sie ermöglicht eine detailliertere Bewertung durch Berücksichtigung zusätzlicher Variablen im Vergleich zu Stufe 1. Beachten Sie, dass die COF-Berechnung unabhängig vom Schädigungsfaktor ist.
Stufe 1 COF-Methode
Schauen wir uns die am häufigsten verwendete Methode der Stufe 1 genauer an. Hier werden in der API 581 Referenzflüssigkeiten angegeben. Die Referenzflüssigkeit, die in Bezug auf Siedepunkt und Molekulargewicht der fraglichen Substanz am nächsten kommt, sollte für die Bewertung ausgewählt werden.
API 581 beziffert die Folgen des Verlusts von Sicherheitsbehältern in Form von:
- Betroffener Einwirkungsbereich; und
- Finanzielle Bedingungen.
Betroffener Einwirkungsbereich Folge
The affected impact area assesses flammable, toxic, and non-flammable & non-toxic consequences, and accounts for both the component damage consequence area and the personnel injury consequence area.
Finanzielle Folgen
Die finanziellen Folgen umfassen Kosten aufgrund von: Bauteilschäden, Produktionsausfälle, Verletzungen (oder) Todesfälle von Mitarbeitern und Umweltschäden.
COF-Berechnungsschritte der Ebene 1
Die Umsetzung der Fehlerfolgenstufe 1 (COF) in API 581 umfasst folgende Schritte:
- Schätzen Sie die Freisetzungsrate.
- Berechnen Sie die Bestandsfreigabe.
- Identifizieren Sie die Art der Freisetzung (kontinuierlich oder sofort).
- Bewertung der Systeme zur Leckerkennung und -isolierung.
- Adjust the release rate and mass.
- Estimate the consequence area.
- Abschätzung der finanziellen Folgen.
You can find comprehensive guidance on executing each of these calculations in the API 581 standard.
Das Ergebnis von API 581
Das Ergebnis einer API 581 RBI-Bewertung sind die Inspektionshäufigkeiten oder -intervalle, der Arbeitsumfang und die Prioritäten. Lassen Sie uns sehen, wie wir zu diesem Ergebnis kommen.
API 581 verwendet Risikomatrizen, um die mit verschiedenen Ausrüstungsteilen verbundenen Risiken zu visualisieren und nach Prioritäten zu ordnen. Eine Risikomatrix ist ein einfaches grafisches Werkzeug, das das Risikoprofil einer Anlage veranschaulicht.
In der Regel handelt es sich um ein Diagramm mit der Ausfallwahrscheinlichkeit (Probability of Failure, POF) auf der einen Seite und der Ausfallfolge (Consequence of Failure, COF) auf der anderen. Jede Zelle in der Matrix steht für eine bestimmte Kombination aus POF und COF und damit für ein bestimmtes Risikoniveau.
Anhand dieser Matrix kann festgestellt werden, welche Geräte ein hohes Risiko aufweisen und dringend überprüft werden müssen und welche Geräte ein geringes Risiko aufweisen und daher seltener überprüft werden können.
Die POF- und COF-Berechnungen führen zu einer POF-Kategorie (1, 2, 3, 4 oder 5) und einer COF-Kategorie (A, B, C, D oder E), die auf den in der API 581-Norm festgelegten Bereichen basieren. Diese beiden Kategorien werden in die Risikomatrix eingetragen (wie in der Abbildung unten mit dem blauen "R" dargestellt).
Außerdem muss ein Ziel-Risikokriterium, wie z. B. "mittel" (wie in der Abbildung unten dargestellt), festgelegt werden.
Beachten Sie, dass das Zielrisikokriterium in API 581 nicht definiert ist, so dass Ihr Unternehmen es selbst festlegen kann. Nachfolgende iterative Berechnungen (durch Erhöhung des Alters) werden durchgeführt, um festzustellen, wann das Zielrisiko überschritten wird (gekennzeichnet durch den blauen Pfeil in der Abbildung unten). Daraus werden das maximale Inspektionsintervall und der nächste Inspektionstermin ermittelt.
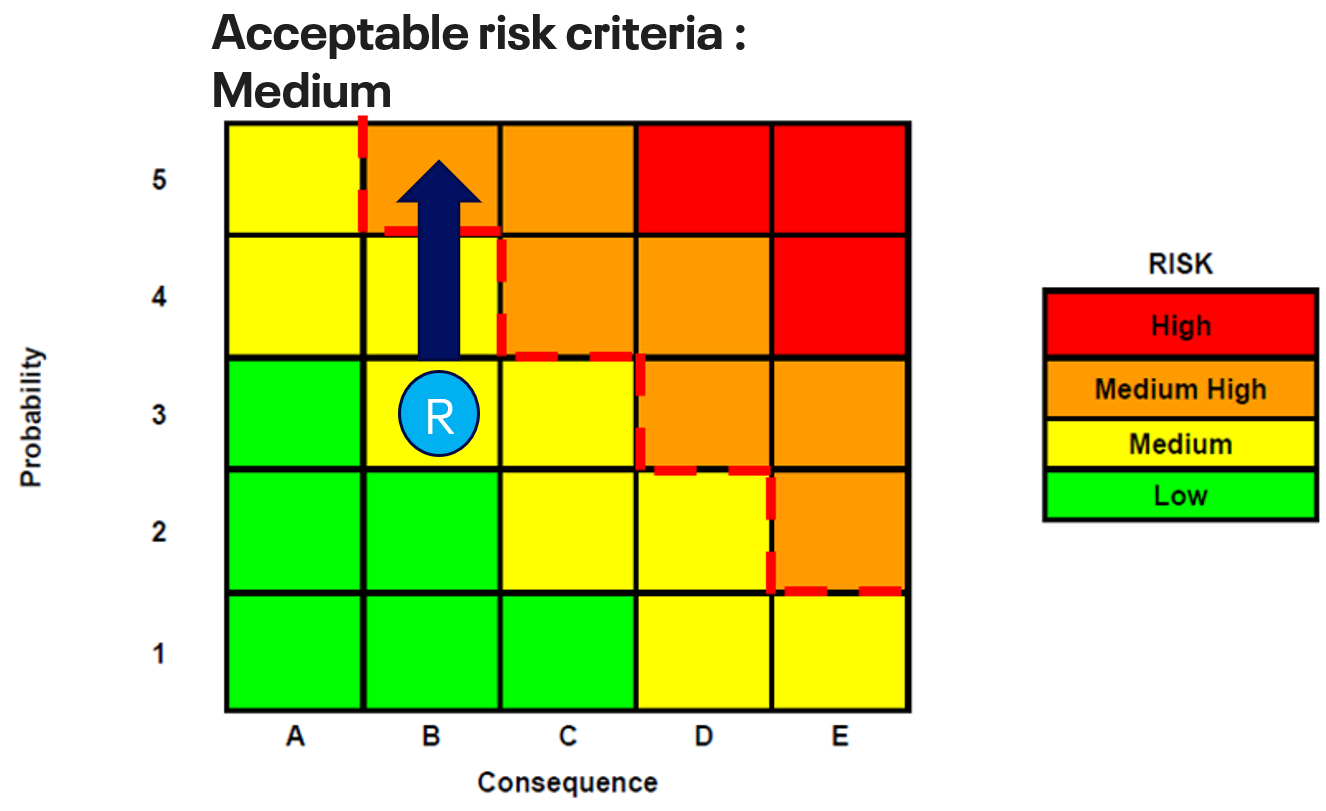
Letztendlich führen die Berechnungen nach API 581 zu einem detaillierten Inspektionsplan, der auf das Risiko der einzelnen Ausrüstungsteile zugeschnitten ist.
Dieser Plan gibt an, wann (nächster Inspektionstermin) und wie (Inspektionsmethoden und -umfang) inspiziert werden soll. Die Risikoberechnungen nach API 581 helfen bei der Identifizierung und Messung von Risiken für alle erfassten Ausrüstungen und liefern ein klares Verständnis von Risiken und deren Bewältigung, was letztlich zu einer Verringerung der Risiken in Verarbeitungsanlagen führt.
IMS PEI: Stärkung integrierter risikobasierter Inspektionslösungen
In conclusion, our IMS (PEI) software offers robust support for API 581-based RBI for pressure equipment such as piping, pressure vessels, and tanks. While we do not currently support API 581 for PRVs or bundle exchangers, our capabilities are designed to be flexible, powerful, and compliant with industry standards.
Our current implementation adheres to the 2016 edition, including the 2019 and 2020 addenda – providing a proven and mature framework that many of our clients already trust.
Our solution includes (but is not limited to) the following capabilities:
- 20+ damage factor calculations
- Configurable generic failure frequencies
- Probability and consequence of failure assessments
- Customizable inspection effectiveness criteria
- Risk and interval target configuration
- Integration of RBI outputs into inspection schedules and maintenance plans
- Degradation management with DMs (from API 571) linked to API 581 damage factors, updating barriers and linking IOWs
If you’re reviewing your RBI strategy or considering how to apply API 581 in a practical, scalable way, we’re here to support you. API 581 may not always be the optimal choice for every scenario – which is why we also offer the S-RBI methodology as an alternative. Together, we can identify the RBI approach that best fits your needs – whether it’s qualitative, semi-quantitative, or fully quantitative.
Reach out to us today to start the conversation.
Möchten Sie mehr über IMS erfahren?
Fordern Sie unten eine Demo an, um sich einen Eindruck von den Möglichkeiten zu verschaffen!
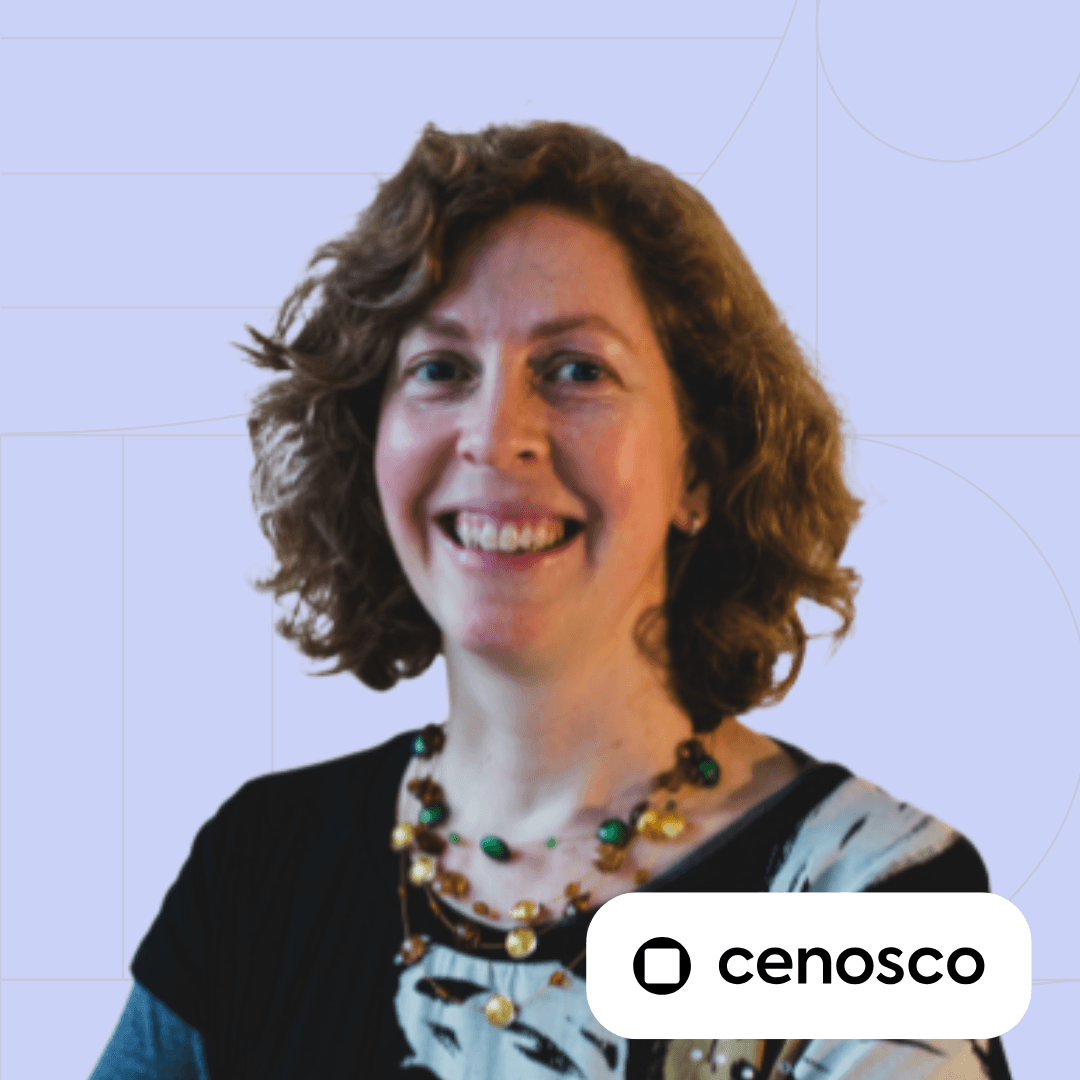
Elsa Tolsma-de Klerk Technical Writer
Elsa is an engineer with a passion for sharing knowledge. She holds a Master’s in Electronic Engineering and spent over a decade at Sasol as an Advanced Process Control Engineer, where she gained hands-on experience in optimization, control systems, and writing technical documentation. Since 2019, she’s been a Technical Writer at Cenosco, now leading the IMS knowledge base and training Academy team.