In einer idealen Welt würden Druckgeräte niemals explodieren, Tanks niemals versagen und Pipelines niemals undicht werden. In der Realität können solche Geräte versagen und tun es auch, manchmal mit verheerenden Folgen. Anlagenausfälle können zum Verlust von Menschenleben, zu Umweltkatastrophen und zu erheblichen finanziellen Verlusten führen, insbesondere in anlagenintensiven Branchen wie der Öl- und Gasindustrie, der Petrochemie und der Energieerzeugung. Die Notwendigkeit, Ausfälle zu verhindern, hat diese Branchen dazu veranlasst, strenge Inspektions- und Wartungsprotokolle einzuführen, um sicherzustellen, dass potenzielle Probleme erkannt werden, bevor sie sich zu Katastrophen ausweiten.
Zwar lassen sich die Ursachen von Anlagenausfällen oft im Nachhinein ermitteln, doch ist es alles andere als ideal, sich auf nachträgliche Analysen zu verlassen. Wenn beispielsweise ein Kessel oder Druckbehälter ausfällt, können die Ermittler Proben des ausgefallenen Geräts zur Laboranalyse entnehmen, um die Ursache zu ermitteln.
Dieser Untersuchungsprozess liefert unschätzbare Informationen, die in künftige Gerätekonstruktionen sowie Überwachungs- und Wartungsprogramme einfließen können, allerdings nur, wenn es bereits zu einem Ausfall gekommen ist. In den meisten Fällen ist es keine praktikable Strategie, zu warten, bis eine Anlage ausfällt, bevor man Maßnahmen ergreift, insbesondere wenn ein Ausfall schwerwiegende Folgen haben könnte.
Eine der wichtigsten Methoden zur Vorbeugung von Anlagenausfällen ist die Bewertung der Anlagenintegrität anhand von risikobasierten Modellen, um geeignete Zeitpläne und Umfänge für Anlageninspektionen festzulegen. Diese Modelle setzen Prioritäten und planen die Inspektionen von Anlagen auf der Grundlage potenzieller Risiken, wobei die Wahrscheinlichkeit eines Ausfalls und die Schwere der Folgen berücksichtigt werden.
Auf diese Weise können Unternehmen ihre Ressourcen auf die Geräte mit dem höchsten Risiko konzentrieren und sicherstellen, dass Ausfälle erkannt und gemindert werden, bevor sie auftreten. Durch die Priorisierung von Hochrisikogeräten können die kostspieligen und potenziell katastrophalen Folgen eines unerwarteten Geräteausfalls vermieden werden.
Ein wesentlicher Bestandteil einer solchen Inspektionsstrategie ist der Einsatz von zerstörungsfreien Prüfungen (NDT) zur Bewertung des Zustands der Ausrüstung. Die zerstörungsfreie Prüfung ermöglicht es den Inspektoren, potenzielle Probleme - wie Korrosion, Risse oder Defekte - zu erkennen, ohne die Anlage zu beschädigen. Die zerstörungsfreie Prüfung kann oft durchgeführt werden, während die Anlage in Betrieb bleibt, so dass der Betrieb weiterläuft und gleichzeitig die menschliche Gesundheit und die Umwelt geschützt werden.
Zerstörungsfreie Prüfung: Was ist das?
Wie der Name schon sagt, umfasst die zerstörungsfreie Prüfung eine Vielzahl von Methoden, die es den Inspektoren ermöglichen, potenzielle Probleme in Geräten zu erkennen, ohne sie zu beschädigen. Diese Techniken sind wichtig für Geräte, die noch in Betrieb sind oder die schnell wieder in Betrieb genommen werden müssen. Im Gegensatz zu invasiveren Prüfmethoden, die die zu prüfenden Geräte beschädigen können, ermöglicht die zerstörungsfreie Prüfung die frühzeitige Erkennung von Verschleiß, Schäden und Mängeln.
Mithilfe der zerstörungsfreien Prüfung können Techniker verborgene Probleme wie innere Risse, Korrosion oder Metallausdünnung erkennen, die bei einer reinen Oberflächeninspektion nicht aufgedeckt werden könnten. Die zerstörungsfreie Prüfung minimiert nicht nur die Ausfallzeiten, sondern trägt auch zur Langlebigkeit der Anlagen bei, verbessert die Sicherheit und unterstützt die Einhaltung von Vorschriften. Im Folgenden werden einige der am häufigsten verwendeten NDT-Techniken vorgestellt.
Visuelle Prüfung (VT)
Wie sie funktioniert: Die Sichtprüfung ist die einfachste und älteste Form der zerstörungsfreien Prüfung, bei der Oberflächenunregelmäßigkeiten oder sichtbare Verschleißerscheinungen durch visuelle Inspektion festgestellt werden. Dabei können Werkzeuge wie Endoskope, Kameras oder Drohnen zum Einsatz kommen, um Bereiche zu inspizieren, die sonst nur schwer zu erreichen sind. In einigen Fällen wird die visuelle Inspektion durch künstliche Intelligenz unterstützt, die Bilder auf frühe Anzeichen von Defekten analysieren kann.
Anwendungen: Visuelle Prüfungen werden eingesetzt, um die Außenflächen von Tanks, Behältern und Pipelines auf sichtbare Schäden wie Lecks, Korrosion oder andere Formen der Verschlechterung zu untersuchen. Drohnen und Roboter können zur Inspektion von schwer zugänglichen Bereichen eingesetzt werden und ermöglichen umfassende visuelle Beurteilungen, ohne dass Gerüste oder lange Ausfallzeiten erforderlich sind.
Ultraschallprüfung (UT)
Wie es funktioniert: Bei der Ultraschallprüfung werden Hochfrequenz-Schallwellen verwendet, die durch Materialien übertragen werden. Wenn diese Wellen auf einen Defekt treffen, werden sie unterschiedlich reflektiert und ermöglichen es den Technikern, interne Fehler zu lokalisieren und zu messen. Das Verfahren ähnelt dem Einsatz von Ultraschall in der medizinischen Bildgebung, ist aber auf den industriellen Einsatz zugeschnitten.
Anwendungen: UT wird häufig zur Messung der Dicke, zur Lokalisierung von inneren Defekten und zur Erkennung von Korrosion eingesetzt. Sie ist besonders wertvoll für die Prüfung von Rohrleitungen, Schweißnähten und Lagertanks, wo Probleme an der Oberfläche möglicherweise nicht sichtbar sind. Mit der Ultraschallprüfung können sogar frühe Stadien von Korrosion oder Ausdünnung erkannt werden, was ein fortschrittliches Warnsystem für potenzielle Fehlerstellen darstellt.
Durchstrahlungsprüfung (RT)
Wie es funktioniert: Bei der Durchstrahlungsprüfung werden Röntgen- oder Gammastrahlen eingesetzt, um Bilder von Gerätekomponenten zu erstellen. Die Strahlung durchdringt Materialien und erzeugt Bilder auf Filmen oder digitalen Sensoren. Schwankungen in der Dichte, die durch Fehler oder Defekte verursacht werden, erscheinen als Schatten auf dem Bild und ermöglichen es den Technikern, sie zu identifizieren und zu bewerten.
Anwendungen: RT wird häufig eingesetzt, um die Integrität von Schweißnähten zu prüfen, Korrosion zu erkennen und Risse zu lokalisieren, insbesondere in unzugänglichen Bereichen von Rohren, Bögen und Druckbehältern. Diese Technik ist besonders effektiv bei der Beurteilung von Schweißnähten, die in hochbelasteten Umgebungen oft Schwachstellen darstellen. Die Durchstrahlungsprüfung kann auch zur Prüfung dickwandiger Komponenten eingesetzt werden, um die strukturelle Integrität dort zu gewährleisten, wo sie am dringendsten benötigt wird.
Magnetische Partikelprüfung (MPT)
Wie es funktioniert: Bei der Magnetpulverprüfung wird ein Magnetfeld an die Oberfläche des Geräts angelegt, auf dem dann Magnetpartikel verteilt werden. Bei Oberflächenfehlern oder oberflächennahen Fehlern wird das Magnetfeld gestört, so dass sich die Partikel um den Bereich des Fehlers gruppieren und ihn sichtbar machen.
Anwendungen: MPT ist besonders effektiv bei der Identifizierung von Oberflächen- und oberflächlichen Untergrundfehlern in ferromagnetischen Materialien. Sie wird häufig zur Prüfung von Rohrleitungen, Bohrlochkopfanlagen, Gussteilen und anderen ferromagnetischen Materialien eingesetzt. Da es sich bei der MPT um ein relativ einfaches Verfahren handelt, ist sie auch eine kosteneffiziente Option für die routinemäßige Inspektion anfälliger Anlagen.
Wirbelstromprüfung (ECT)
Wie sie funktioniert: Bei der Wirbelstromprüfung wird eine elektromagnetische Spule verwendet, um in leitfähigen Materialien Ströme zu erzeugen, deren Intensität in Abhängigkeit von Fehlern im Grundmaterial variieren kann. Das Gerät misst die im Grundmaterial induzierten Wirbelströme und ermöglicht es den Technikern, Defekte oder Korrosion zu erkennen und zu charakterisieren.
Anwendungen: ECT ist ideal für die Prüfung nicht ferromagnetischer Materialien wie Edelstahl, die häufig in Rohrleitungssystemen, Wärmetauschern und Offshore-Plattformen zu finden sind. Da ECT auf kleine Veränderungen empfindlich reagiert, wird es häufig zur Prüfung dünnwandiger Rohre eingesetzt, um Korrosion im Frühstadium oder kleine Risse zu erkennen, die zu schwerwiegenderen Problemen führen könnten.
Vorteile der zerstörungsfreien Prüfung in der Industrie
Die zerstörungsfreie Prüfung hat die Art und Weise verändert, wie die Industrie die Wartung und Inspektion von Anlagen handhabt. Sie bieten zahlreiche Vorteile, darunter:
- Geringere Ausfallzeiten: Viele ZfP-Methoden können durchgeführt werden, während die Geräte in Betrieb sind, wodurch Betriebsunterbrechungen minimiert werden und eine kontinuierliche Überwachung möglich ist.
- Kosteneinsparungen: Die proaktive Erkennung von Problemen trägt dazu bei, teure Notreparaturen oder den Austausch kompletter Anlagen zu vermeiden. NDT ermöglicht es Unternehmen, die Wartung strategischer zu planen und so die langfristigen Kosten zu senken.
- Erhöhte Sicherheit: Die zerstörungsfreie Prüfung ermöglicht die frühzeitige Erkennung potenzieller Fehlerstellen und verringert so die Wahrscheinlichkeit katastrophaler Zwischenfälle, die Leben und Umwelt gefährden könnten.
- Verlängerte Lebensdauer der Ausrüstung: Regelmäßige Inspektionen mit NDT-Techniken tragen dazu bei, die Ausrüstung in einem optimalen Zustand zu halten, ihre Lebensdauer zu verlängern und die Rentabilität der Investition zu verbessern.
- Einhaltung gesetzlicher Vorschriften: Viele Branchen sind stark reguliert und unterliegen strengen Sicherheits- und Umweltrichtlinien. Die zerstörungsfreie Prüfung spielt eine wichtige Rolle, wenn es darum geht, dass Unternehmen diese Normen einhalten.
Die Zukunft der zerstörungsfreien Prüfung
Mit dem technologischen Fortschritt entwickeln sich auch die NDT-Methoden weiter. Moderne Bildverarbeitung, Automatisierung, künstliche Intelligenz und maschinelles Lernen verändern herkömmliche Prüfverfahren und machen sie schneller, genauer und zuverlässiger. So kann beispielsweise die KI-gestützte Analyse von Bildern aus visuellen Prüfungen Unregelmäßigkeiten aufdecken, die menschlichen Inspektoren möglicherweise entgehen. Ebenso verbessern Robotersysteme, die mit Ultraschall- oder Wirbelstromprüfungsfunktionen ausgestattet sind, die Reichweite und Effizienz von Inspektionen.
In Zukunft könnte die zerstörungsfreie Prüfung noch stärker in die Anlagenverwaltung integriert werden, mit Systemen, die Echtzeitdaten nutzen, um potenzielle Probleme zu erkennen, bevor sie entstehen. Diese Fortschritte könnten den Ansatz der Anlagenwartung revolutionieren, indem sie von präventiven Maßnahmen zu prädiktiven Lösungen übergehen, mit denen Unternehmen Risiken präventiv angehen können.
In einer idealen Welt würden Anlagen nie ausfallen, aber mit den Möglichkeiten der zerstörungsfreien Prüfung können wir diesem Ideal näher kommen, indem wir die Risiken minimieren und die Sicherheit, Effizienz und Langlebigkeit wichtiger Anlagen maximieren.
Implementierung eines wirksamen Inspektionsverwaltungsprogramms
Die Ausarbeitung und Umsetzung eines Inspektions- und Überwachungsprogramms für die Schwerindustrie ist keine triviale Aufgabe. Eine noch schwierigere Aufgabe ist es, den Überblick zu behalten und die gesammelten Informationen sinnvoll auszuwerten. Unser Ziel bei Cenosco ist es, Sie in die Lage zu versetzen, sicherzustellen, dass Ihre Inspektions- und Überwachungsprogramme so konzipiert und implementiert werden, dass die Integrität, Zuverlässigkeit und Sicherheit Ihres Betriebs gewährleistet ist.
IMS - das Integrity Management System - wurde von Grund auf so konzipiert, dass es Sie bei der Entwicklung und Umsetzung effektiver Inspektionsprogramme unterstützt und risikobasierte Modelle zur Priorisierung und Planung von Anlageninspektionen einsetzt. Unsere unübertroffenen Korrosionsmodellierungsfähigkeiten nutzen die von Ihrem Anlageninspektionsprogramm gesammelten Daten, um Ihre Inspektionsintervalle zu verfeinern, so dass Sie sicherstellen können, dass begrenzte Inspektions- und Wartungsressourcen effizient und effektiv zugewiesen werden.
Wenn Sie mehr darüber erfahren möchten, wie IMS die Ergebnisse Ihrer Inspektions- und Überwachungsprogramme verbessern kann, füllen Sie das folgende Formular aus, oder klicken Sie hier, um mehr über IMS PEI zu erfahren.
Demo anfordern
Finden Sie heraus, wie IMS Ihre Abläufe verändern und optimieren kann...
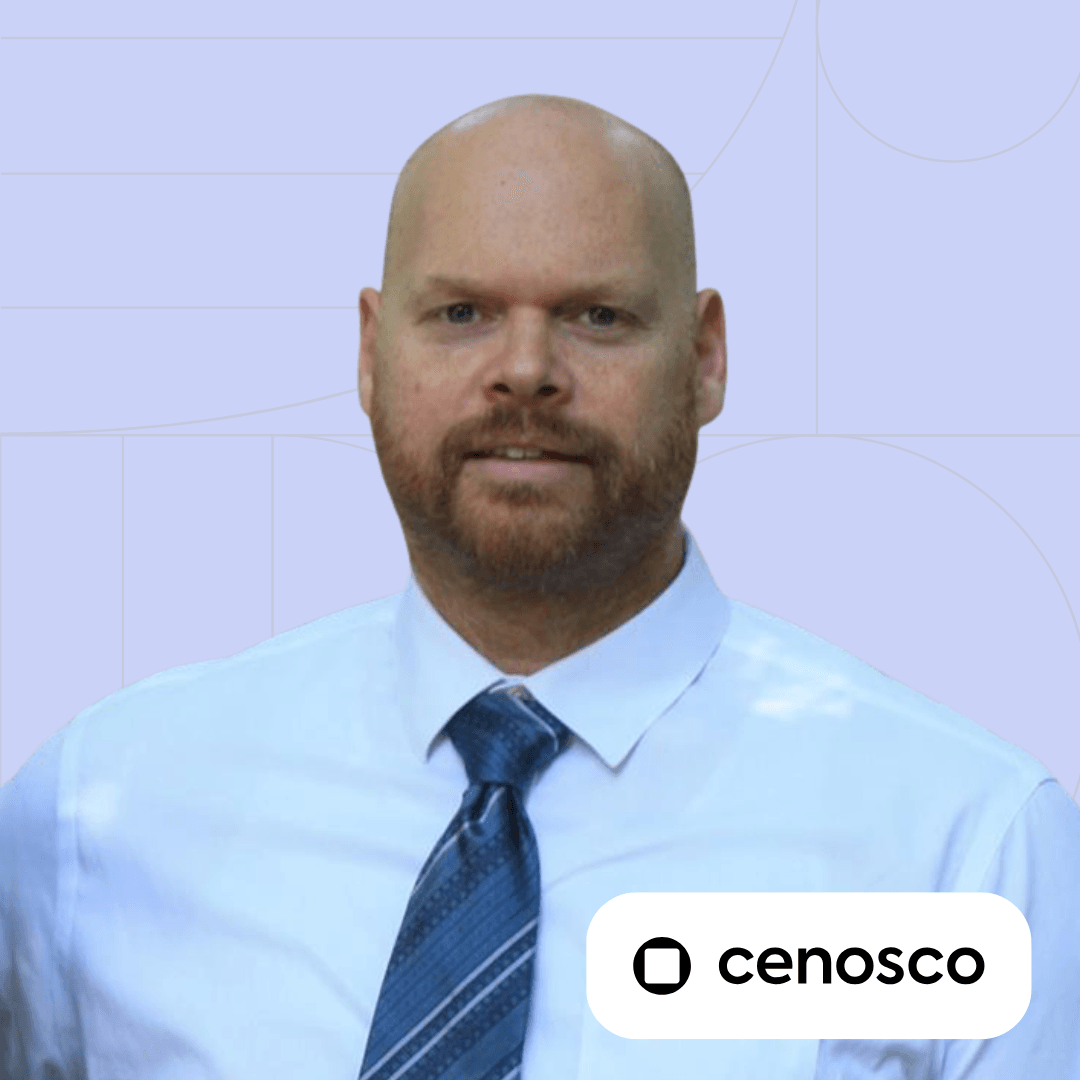
Tomislav Renić Technical Writer
Tomislav is an experienced engineer and technical communicator with over 20 years in complex systems, modeling, and project management. As a Technical Writer at Cenosco, he translates engineering concepts into clear, user-friendly documentation for software in the oil, gas, and refining industries.