Dans un monde idéal, les équipements sous pression n'exploseraient jamais, les réservoirs ne tomberaient jamais en panne et les pipelines ne fuiraient jamais. En réalité, ces équipements peuvent tomber en panne et le font, parfois avec des conséquences dévastatrices. Les pannes d'équipement peuvent entraîner des pertes de vies humaines, des catastrophes environnementales et des pertes financières considérables, en particulier dans les secteurs où les actifs sont importants, comme le pétrole et le gaz, la pétrochimie et la production d'énergie. La nécessité de prévenir les défaillances a conduit ces industries à adopter des protocoles d'inspection et de maintenance rigoureux, garantissant que les problèmes potentiels sont détectés avant qu'ils ne se transforment en catastrophes.
Si les causes profondes des défaillances des équipements peuvent souvent être identifiées rétrospectivement, il est loin d'être idéal de s'en remettre à une analyse a posteriori. Par exemple, si une chaudière ou un récipient sous pression tombe en panne, les enquêteurs peuvent prélever des échantillons de l'équipement défectueux pour les analyser en laboratoire afin d'en déterminer la cause.
Ce processus d'investigation fournit des informations précieuses qui peuvent être incluses dans les conceptions futures des équipements et dans les programmes de surveillance et de maintenance, mais seulement si la défaillance s'est déjà produite. Dans la plupart des cas, attendre que l'équipement tombe en panne avant d'agir n'est pas une stratégie viable, en particulier lorsque la défaillance peut avoir des conséquences graves.
L'une des principales méthodes de prévention des pannes d'équipement consiste à évaluer l'intégrité de l'équipement à l'aide de modèles fondés sur les risques, afin d'établir des calendriers et des champs d'application appropriés pour les inspections de l'équipement. Ces modèles permettent de hiérarchiser et de programmer les inspections des équipements en fonction des risques potentiels, en tenant compte de la probabilité d'une défaillance et de la gravité des conséquences.
Cette approche permet aux entreprises de concentrer leurs ressources sur les équipements qui présentent le risque le plus élevé, en veillant à ce que les défaillances soient identifiées et atténuées avant qu'elles ne se produisent. En donnant la priorité aux équipements à haut risque, il est possible d'éviter les conséquences coûteuses et potentiellement catastrophiques qui peuvent résulter d'une défaillance inattendue d'un équipement.
Un élément essentiel de cette stratégie d'inspection est l'utilisation d'essais non destructifs (END) pour évaluer l'état de l'équipement. Les essais non destructifs permettent aux inspecteurs d'identifier les problèmes potentiels, tels que la corrosion, les fissures ou les défauts, sans endommager l'équipement. Les essais non destructifs peuvent souvent être réalisés alors que l'équipement reste en service, ce qui permet de poursuivre les opérations tout en protégeant la santé humaine et l'environnement.
Essais non destructifs : Qu'est-ce que c'est ?
Comme son nom l'indique, le contrôle non destructif englobe une série de méthodes qui permettent aux inspecteurs d'identifier les problèmes potentiels d'un équipement sans causer de dommages. Ces techniques sont importantes pour les équipements qui sont encore en service ou qui doivent être remis en service rapidement. Contrairement aux méthodes d'essai plus intrusives qui peuvent endommager l'équipement inspecté, les essais non destructifs permettent de détecter rapidement l'usure, les dommages et les défauts.
Grâce aux CND, les techniciens peuvent identifier des problèmes cachés tels que la fissuration interne, la corrosion ou l'amincissement du métal - des problèmes qui seraient autrement indétectables à partir d'une simple inspection de surface. Les CND permettent non seulement de minimiser les temps d'arrêt, mais aussi de maintenir la longévité des équipements, d'améliorer la sécurité et de favoriser la conformité aux réglementations. Voici quelques-unes des techniques de CND les plus couramment utilisées.
Test visuel (VT)
Comment cela fonctionne-t-il ? Le contrôle visuel est la forme la plus simple et la plus ancienne de contrôle non destructif. Il utilise l'inspection visuelle pour détecter les irrégularités de surface ou les signes visibles d'usure. Il peut impliquer l'utilisation d'outils tels que des endoscopes, des caméras ou des drones pour inspecter des zones difficiles d'accès. Dans certains cas, les inspections visuelles sont améliorées par l'intelligence artificielle, qui peut analyser les images pour détecter les premiers signes de défauts.
Applications : Les tests visuels sont utilisés pour inspecter les surfaces externes des réservoirs, des cuves et des pipelines à la recherche de dommages visibles, tels que des fuites, de la corrosion ou d'autres formes de dégradation. Des drones et des robots peuvent être déployés pour inspecter les zones difficiles d'accès, ce qui permet de réaliser des évaluations visuelles complètes sans échafaudage ni temps d'arrêt prolongé.
Contrôle par ultrasons (UT)
Comment cela fonctionne-t-il ? Le contrôle par ultrasons utilise des ondes sonores à haute fréquence qui sont transmises à travers les matériaux. Lorsque ces ondes rencontrent un défaut, elles se réfléchissent différemment, ce qui permet aux techniciens de localiser et de dimensionner les défauts internes. Le processus est similaire à l'utilisation des ultrasons dans l'imagerie médicale, mais il est adapté à l'usage industriel.
Applications : L'UT est largement utilisée pour mesurer l'épaisseur, localiser les défauts internes et détecter la corrosion. Il est particulièrement utile pour inspecter les pipelines, les soudures et les réservoirs de stockage, où les problèmes peuvent ne pas être visibles à la surface. Le contrôle par ultrasons peut même détecter les premiers stades de la corrosion ou de l'amincissement, ce qui constitue un système d'alerte avancé pour les points de défaillance potentiels.
Tests radiographiques (RT)
Comment cela fonctionne-t-il ? Le contrôle radiographique consiste à utiliser des rayons X ou des rayons gamma pour créer des images des composants de l'équipement. Le rayonnement traverse les matériaux et crée des images sur des films ou des capteurs numériques. Les variations de densité causées par les défauts apparaissent sous forme d'ombres sur l'image, ce qui permet aux techniciens de les identifier et de les évaluer.
Applications : La RT est fréquemment utilisée pour contrôler l'intégrité des soudures, détecter la corrosion et localiser les fissures, en particulier dans les zones inaccessibles des tuyaux, des coudes et des appareils à pression. Cette technique est particulièrement efficace pour évaluer les soudures, qui sont souvent des points de vulnérabilité dans les environnements soumis à de fortes contraintes. Les essais radiographiques peuvent également être utilisés pour inspecter les composants à parois épaisses, afin de garantir l'intégrité structurelle là où elle est le plus nécessaire.
Contrôle par magnétoscopie (MPT)
Comment cela fonctionne-t-il ? Le contrôle magnétoscopique applique un champ magnétique à la surface de l'équipement, puis y répand des particules magnétiques. Lorsque des défauts apparaissent à la surface ou près de la surface, ils perturbent le champ magnétique, ce qui a pour effet de regrouper les particules autour de la zone du défaut et de le rendre visible.
Applications : La TPM est particulièrement efficace pour identifier les défauts de surface et de subsurface peu profonde dans les matériaux ferromagnétiques. Elle est couramment utilisée pour inspecter les pipelines, les équipements de tête de puits, les pièces moulées et d'autres matériaux ferromagnétiques. La magnétoscopie étant un procédé relativement simple, elle constitue également une option rentable pour les inspections de routine des équipements sensibles.
Contrôle par courants de Foucault (ECT)
Comment cela fonctionne-t-il ? Le contrôle par courants de Foucault utilise une bobine électromagnétique pour générer des courants dans les matériaux conducteurs, dont l'intensité peut varier en fonction des défauts du matériau de base. L'outil mesure les courants de Foucault induits dans le matériau de base, ce qui permet aux techniciens de détecter et de caractériser les défauts ou la corrosion.
Applications : L'ECT est idéal pour inspecter les matériaux non ferromagnétiques comme l'acier inoxydable, que l'on trouve couramment dans les systèmes de tuyauterie, les échangeurs de chaleur et les plates-formes offshore. Parce qu'elle est sensible aux petites variations, l'ECT est souvent utilisée pour inspecter les tubes à parois minces et détecter les premiers stades de la corrosion ou les petites fissures susceptibles d'entraîner des problèmes plus graves.
Avantages des essais non destructifs dans l'industrie
Les CND ont transformé la manière dont les industries gèrent la maintenance et l'inspection des équipements. Ils offrent de nombreux avantages, notamment
- Réduction des temps d'arrêt : De nombreuses méthodes d'essais non destructifs peuvent être exécutées alors que l'équipement reste en service, ce qui minimise les interruptions d'exploitation et permet un contrôle continu.
- Réduction des coûts : La détection proactive des problèmes permet d'éviter des réparations d'urgence coûteuses ou des remplacements complets d'équipements. Les essais non destructifs permettent aux entreprises de programmer la maintenance de manière plus stratégique, ce qui réduit les coûts à long terme.
- Sécurité accrue : Les essais non destructifs permettent la détection précoce des points de défaillance potentiels, réduisant ainsi la probabilité d'incidents catastrophiques susceptibles de mettre en danger des vies humaines et l'environnement.
- Prolongation de la durée de vie des équipements : L'inspection régulière à l'aide de techniques de contrôle non destructif permet de maintenir l'équipement dans un état optimal, ce qui prolonge sa durée de vie et améliore le retour sur investissement.
- Conformité réglementaire : De nombreuses industries sont fortement réglementées, avec des directives strictes en matière de sécurité et d'environnement. Les essais non destructifs jouent un rôle essentiel en garantissant que les entreprises restent conformes à ces normes.
L'avenir des essais non destructifs
À mesure que la technologie progresse, les méthodes de CND continuent d'évoluer. L'imagerie avancée, l'automatisation, l'intelligence artificielle et l'apprentissage automatique transforment les processus d'inspection traditionnels, les rendant plus rapides, plus précis et plus fiables. Par exemple, l'analyse par l'IA d'images provenant d'inspections visuelles permet de détecter des irrégularités que les inspecteurs humains pourraient manquer. De même, les systèmes robotiques dotés de capacités de contrôle par ultrasons ou par courants de Foucault améliorent la portée et l'efficacité des inspections.
À l'avenir, les essais non destructifs pourraient faire partie intégrante de la gestion des actifs, avec des systèmes utilisant des données en temps réel pour anticiper les problèmes potentiels avant qu'ils ne surviennent. Ces avancées pourraient révolutionner l'approche de la maintenance des équipements, en passant de mesures préventives à des solutions prédictives qui permettent aux entreprises de faire face aux risques de manière préventive.
Dans un monde idéal, les équipements ne tomberaient jamais en panne, mais grâce à la puissance des essais non destructifs, nous pouvons nous rapprocher de cet idéal en minimisant les risques et en maximisant la sécurité, l'efficacité et la longévité des actifs critiques.
Mise en œuvre d'un programme efficace de gestion des inspections
Concevoir et mettre en œuvre un programme d'inspection et de surveillance pour les industries lourdes n'est pas une tâche triviale. Une tâche encore plus difficile est de garder la trace et de donner un sens aux informations collectées. Chez Cenosco, notre objectif est de vous permettre de vous assurer que vos programmes d'inspection et de surveillance sont conçus et mis en œuvre pour garantir l'intégrité, la fiabilité et la sécurité de vos opérations.
IMS - le système de gestion de l'intégrité - est conçu dès le départ pour aider à concevoir et à mettre en œuvre des programmes d'inspection efficaces, en utilisant des modèles basés sur le risque pour hiérarchiser et planifier les inspections des équipements. Nos capacités inégalées de modélisation de la corrosion utilisent les données collectées dans le cadre de votre programme d'inspection des équipements pour affiner vos intervalles d'inspection afin que vous puissiez vous assurer que les ressources limitées d'inspection et de maintenance sont allouées de manière efficace et efficiente.
Pour en savoir plus sur la manière dont IMS peut améliorer les résultats de vos programmes d'inspection et de surveillance, remplissez le formulaire ci-dessous ou cliquez ici pour en savoir plus sur IMS PEI.
Demander une démonstration
Découvrez comment l'IMS peut transformer et optimiser vos opérations...
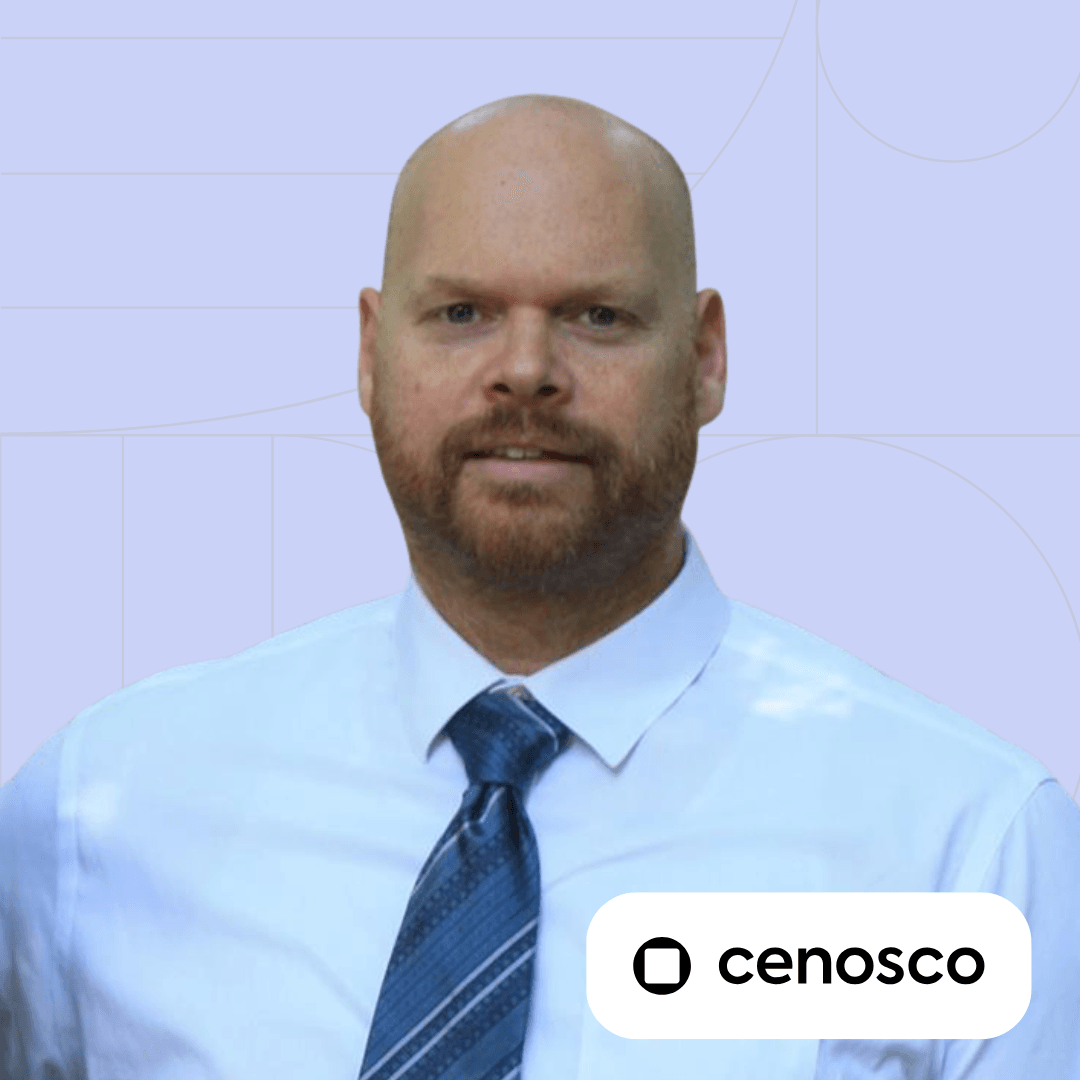
Tomislav Renić Technical Writer
Tomislav is an experienced engineer and technical communicator with over 20 years in complex systems, modeling, and project management. As a Technical Writer at Cenosco, he translates engineering concepts into clear, user-friendly documentation for software in the oil, gas, and refining industries.