В идеальном мире оборудование, работающее под давлением, никогда не взорвется, резервуары никогда не выйдут из строя, а трубопроводы никогда не протекут. В реальности же такое оборудование может выйти из строя, причем иногда с катастрофическими последствиями. Отказы оборудования могут привести к гибели людей, экологическим катастрофам и значительным финансовым потерям, особенно в таких отраслях промышленности, где много активов, как нефтегазовая, нефтехимическая и энергетическая. Необходимость предотвращения отказов заставила эти отрасли принять строгие протоколы инспекции и технического обслуживания, гарантирующие, что потенциальные проблемы будут обнаружены до того, как они перерастут в катастрофу.
Хотя первопричины отказов оборудования часто можно выявить задним числом, полагаться на анализ "постфактум" - далеко не идеальный вариант. Например, если из строя вышел котел или сосуд под давлением, следователи могут собрать образцы вышедшего из строя оборудования для лабораторного анализа, чтобы определить причину.
Этот процесс расследования дает бесценную информацию, которая может быть включена в будущие проекты оборудования, программы мониторинга и технического обслуживания, но только в том случае, если отказ уже произошел. В большинстве случаев ожидание отказа оборудования до принятия мер не является жизнеспособной стратегией, особенно если отказ может привести к серьезным последствиям.
Одним из основных методов предотвращения отказов оборудования является оценка его целостности с помощью моделей, основанных на оценке рисков, для составления соответствующих графиков и объемов проверок оборудования. Эти модели определяют приоритеты и график проверок оборудования на основе потенциальных рисков, учитывая вероятность отказа и тяжесть последствий.
Такой подход позволяет компаниям сосредоточить свои ресурсы на оборудовании, представляющем наибольший риск, обеспечивая выявление и устранение неисправностей до их возникновения. Приоритетность оборудования с высоким риском позволяет избежать дорогостоящих и потенциально катастрофических последствий, которые могут возникнуть в результате неожиданного отказа оборудования.
Важным компонентом такой стратегии инспекции является использование неразрушающего контроля (NDT) для оценки состояния оборудования. Неразрушающий контроль позволяет инспекторам выявлять потенциальные проблемы, такие как коррозия, трещины или дефекты, не причиняя никакого вреда оборудованию. Неразрушающий контроль часто можно проводить, пока оборудование остается в эксплуатации, что позволяет продолжать работу, сохраняя здоровье людей и окружающую среду.
Неразрушающий контроль: Что это такое?
Как следует из названия, неразрушающий контроль включает в себя различные методы, которые позволяют инспекторам выявлять потенциальные проблемы в оборудовании, не причиняя ему вреда. Эти методы важны для оборудования, которое все еще находится в эксплуатации или должно быть быстро возвращено в строй. В отличие от более интрузивных методов тестирования, которые могут повредить проверяемое оборудование, неразрушающий контроль позволяет обнаружить износ, повреждения и дефекты на ранней стадии.
С помощью неразрушающего контроля специалисты могут выявить скрытые проблемы, такие как внутренние трещины, коррозия или истончение металла - проблемы, которые иначе невозможно было бы обнаружить только при поверхностном осмотре. Неразрушающий контроль не только минимизирует время простоя, но и помогает поддерживать долговечность оборудования, повышает безопасность и способствует соблюдению нормативных требований. Ниже приведены некоторые из наиболее часто используемых методов неразрушающего контроля.
Визуальное тестирование (VT)
Как это работает: Визуальный контроль - это самая простая и старая форма неразрушающего контроля, использующая визуальный осмотр для обнаружения неровностей поверхности или видимых признаков износа. Для осмотра труднодоступных мест могут использоваться такие инструменты, как бороскопы, камеры или беспилотники. В некоторых случаях визуальный контроль дополняется искусственным интеллектом, который может анализировать изображения для выявления ранних признаков дефектов.
Области применения: Визуальный контроль используется для проверки внешних поверхностей резервуаров, емкостей и трубопроводов на наличие видимых повреждений, таких как утечки, коррозия или другие формы деградации. Дроны и роботы могут использоваться для осмотра труднодоступных мест, что позволяет проводить комплексную визуальную оценку без использования строительных лесов и длительных простоев.
Ультразвуковой контроль (UT)
Как это работает: Ультразвуковой контроль использует высокочастотные звуковые волны, которые передаются через материалы. Когда эти волны встречаются с дефектом, они отражаются по-разному, позволяя специалистам обнаружить и определить размеры внутренних дефектов. Процесс похож на то, как ультразвук используется в медицинской визуализации, но адаптирован для промышленного применения.
Области применения: UT широко используется для измерения толщины, обнаружения внутренних дефектов и коррозии. Он особенно ценен для проверки трубопроводов, сварных швов и резервуаров для хранения, где проблемы могут быть не видны на поверхности. Ультразвуковой контроль может даже обнаружить ранние стадии коррозии или истончения, обеспечивая систему предупреждения о потенциальных местах разрушения.
Рентгенографическое исследование (RT)
Как это работает: Рентгенографическое тестирование предполагает использование рентгеновского или гамма-излучения для создания изображений компонентов оборудования. Излучение проходит через материалы и создает изображения на пленке или цифровых датчиках. Изменения плотности, вызванные дефектами или недостатками, проявляются в виде теней на изображении, что позволяет специалистам выявить и оценить их.
Области применения: RT часто используется для проверки целостности сварных швов, выявления коррозии и обнаружения трещин, особенно в труднодоступных местах труб, колен и сосудов под давлением. Этот метод особенно эффективен для оценки сварных швов, которые часто являются уязвимыми местами в условиях высоких нагрузок. Радиографическое тестирование также может использоваться для проверки толстостенных компонентов, обеспечивая структурную целостность там, где это больше всего необходимо.
Испытание магнитных частиц (MPT)
Как это работает: При испытании магнитными частицами к поверхности оборудования прикладывается магнитное поле, а затем по ней распределяются магнитные частицы. При наличии поверхностных или близких к поверхностным дефектов они нарушают магнитное поле, заставляя частицы скапливаться вокруг дефекта, делая его видимым.
Области применения: MPT особенно эффективен для выявления поверхностных и неглубоких подповерхностных дефектов в ферромагнитных материалах. Он обычно используется для проверки трубопроводов, устьевого оборудования, отливок и других ферромагнитных материалов. Поскольку MPT - относительно простой процесс, он также является экономически эффективным вариантом для плановых проверок чувствительного оборудования.
Испытание вихревыми токами (ECT)
Принцип работы: В вихретоковых испытаниях используется электромагнитная катушка для создания токов в проводящих материалах, интенсивность которых может меняться в зависимости от дефектов в основном материале. Инструмент измеряет вихревые токи, индуцированные в основном материале, позволяя специалистам обнаружить и охарактеризовать дефекты или коррозию.
Области применения: ЭСТ идеально подходит для проверки неферромагнитных материалов, таких как нержавеющая сталь, обычно встречающихся в трубопроводных системах, теплообменниках и морских платформах. Поскольку этот метод чувствителен к небольшим изменениям, ЭКТ часто используется для проверки тонкостенных труб, выявляя раннюю стадию коррозии или небольшие трещины, которые могут привести к более серьезным проблемам.
Преимущества неразрушающего контроля в промышленности
Неразрушающий контроль изменил подход к обслуживанию и проверке оборудования в промышленности. Они предлагают множество преимуществ, включая:
- Сокращение времени простоя: Многие методы неразрушающего контроля можно выполнять, пока оборудование остается в рабочем состоянии, что сводит к минимуму перебои в работе и позволяет осуществлять непрерывный мониторинг.
- Экономия средств: Проактивное обнаружение проблем помогает предотвратить дорогостоящий аварийный ремонт или полную замену оборудования. Неразрушающий контроль позволяет компаниям более стратегически грамотно планировать техническое обслуживание, снижая долгосрочные затраты.
- Повышение безопасности: Неразрушающий контроль позволяет заблаговременно обнаружить потенциальные точки отказа, снижая вероятность катастрофических инцидентов, которые могут угрожать жизни людей и окружающей среде.
- Увеличение срока службы оборудования: Регулярный контроль с помощью методов неразрушающего контроля помогает поддерживать оборудование в идеальном состоянии, продлевая срок его эксплуатации и повышая рентабельность инвестиций.
- Соответствие нормативным требованиям: Многие отрасли промышленности жестко регламентированы, в них действуют строгие правила безопасности и охраны окружающей среды. Неразрушающий контроль играет важную роль в обеспечении соответствия компаний этим стандартам.
Будущее неразрушающего контроля
По мере развития технологий методы неразрушающего контроля продолжают совершенствоваться. Передовые средства визуализации, автоматизации, искусственного интеллекта и машинного обучения изменяют традиционные процессы контроля, делая их более быстрыми, точными и надежными. Например, анализ изображений при визуальном контроле с помощью искусственного интеллекта позволяет обнаружить нарушения, которые могут быть пропущены человеческим инспектором. Аналогичным образом, роботизированные системы, оснащенные возможностями ультразвукового или вихретокового контроля, повышают охват и эффективность инспекций.
В будущем неразрушающий контроль может стать еще более неотъемлемой частью управления активами, а системы, использующие данные в режиме реального времени, позволят предвидеть потенциальные проблемы еще до их возникновения. Эти достижения могут коренным образом изменить подход к обслуживанию оборудования, перейдя от профилактических мер к предиктивным решениям, которые позволят компаниям упреждать риски.
В идеальном мире оборудование никогда не выходит из строя, но благодаря возможностям неразрушающего контроля мы можем приблизиться к этому идеалу, минимизируя риски и максимально повышая безопасность, эффективность и долговечность критически важных активов.
Внедрение эффективной программы управления инспекциями
Разработка и внедрение программы инспекции и мониторинга для тяжелых производств - задача не из простых. Еще более сложной задачей является отслеживание и осмысление собранной информации. Наша цель в Cenosco - дать вам возможность убедиться, что ваши программы инспекции и мониторинга разработаны и реализованы для обеспечения целостности, надежности и безопасности вашей деятельности.
IMS - система управления целостностью - разработана с нуля, чтобы помочь разработать и внедрить эффективные программы инспекций, используя модели, основанные на оценке рисков, для определения приоритетов и составления графика проверок оборудования. Наши непревзойденные возможности моделирования коррозии используют данные, собранные в рамках программы проверок оборудования, для уточнения интервалов между проверками, чтобы обеспечить рациональное и эффективное распределение ограниченных ресурсов на проверки и техническое обслуживание.
Чтобы узнать больше о том, как IMS может улучшить результаты ваших программ инспекции и мониторинга, заполните форму ниже или нажмите здесь, чтобы узнать больше об IMS PEI.
Запрос на демонстрацию
Узнайте, как IMS может преобразовать и оптимизировать ваши операции...
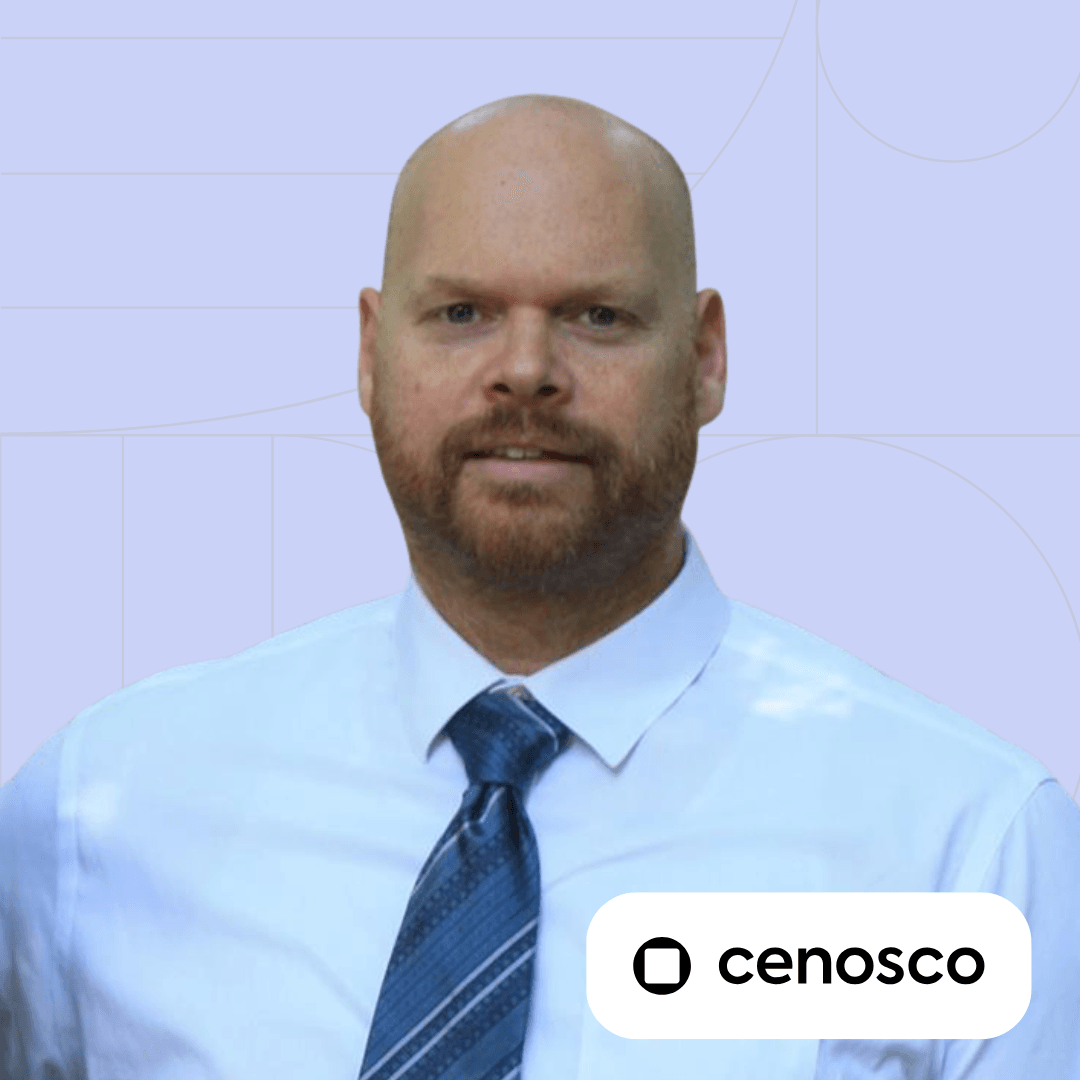
Tomislav Renić Technical Writer
Tomislav is an experienced engineer and technical communicator with over 20 years in complex systems, modeling, and project management. As a Technical Writer at Cenosco, he translates engineering concepts into clear, user-friendly documentation for software in the oil, gas, and refining industries.