Num mundo ideal, o equipamento sob pressão nunca explodiria, os tanques nunca falhariam e as condutas nunca teriam fugas. Na realidade, esses equipamentos podem falhar e falham, por vezes com consequências devastadoras. As falhas de equipamento podem levar à perda de vidas, a desastres ambientais e a perdas financeiras significativas, especialmente em indústrias com muitos activos, como a indústria do petróleo e do gás, a petroquímica e a produção de energia. A necessidade de evitar falhas levou estas indústrias a adotar protocolos rigorosos de inspeção e manutenção, assegurando que os potenciais problemas são detectados antes de se transformarem em desastres.
Embora as causas principais das falhas de equipamento possam ser frequentemente identificadas retrospetivamente, confiar na análise após o facto está longe de ser o ideal. Por exemplo, se uma caldeira ou um recipiente sob pressão falhar, os investigadores podem recolher amostras do equipamento avariado para análise laboratorial, a fim de determinar a causa.
Este processo de investigação fornece informações valiosas que podem ser incluídas em futuros projectos de equipamento e programas de monitorização e manutenção, mas apenas se a falha já tiver ocorrido. Na maioria dos casos, esperar que o equipamento falhe para tomar medidas não é uma estratégia viável, especialmente quando a falha pode levar a consequências graves.
Um dos principais métodos de prevenção de falhas de equipamento consiste em avaliar a integridade do equipamento utilizando modelos baseados no risco para estabelecer calendários e âmbitos adequados para as inspecções do equipamento. Estes modelos dão prioridade e programam as inspecções dos equipamentos com base nos riscos potenciais, tendo em conta a probabilidade de falha e a gravidade das consequências.
Esta abordagem permite que as empresas concentrem os seus recursos no equipamento que apresenta o maior risco, assegurando que as falhas são identificadas e mitigadas antes de ocorrerem. Ao dar prioridade ao equipamento de alto risco, podem ser evitados os resultados dispendiosos e potencialmente catastróficos que podem surgir de uma falha inesperada do equipamento.
Um componente essencial dessa estratégia de inspeção é a utilização de ensaios não destrutivos (NDT) para avaliar o estado do equipamento. Os ensaios não destrutivos permitem aos inspectores identificar potenciais problemas - tais como corrosão, fissuras ou defeitos - sem causar qualquer dano ao equipamento. Os ensaios não destrutivos podem frequentemente ser efectuados enquanto o equipamento permanece em serviço, permitindo que as operações continuem a decorrer, salvaguardando a saúde humana e o ambiente.
Ensaios não destrutivos: O que é?
Como o nome indica, os ensaios não destrutivos englobam uma variedade de métodos que permitem aos inspectores identificar potenciais problemas no equipamento sem causar danos. Estas técnicas são importantes para o equipamento que ainda está em serviço ou que precisa de voltar a funcionar rapidamente. Ao contrário dos métodos de ensaio mais intrusivos que podem danificar o equipamento a ser inspeccionado, os ensaios não destrutivos permitem a deteção precoce de desgaste, danos e defeitos.
Utilizando o NDT, os técnicos podem identificar problemas ocultos, como fissuras internas, corrosão ou afinamento do metal - problemas que, de outra forma, seriam indetectáveis apenas com uma inspeção da superfície. O NDT não só minimiza o tempo de inatividade, como também ajuda a manter a longevidade do equipamento, melhora a segurança e apoia a conformidade regulamentar. Abaixo estão algumas das técnicas NDT mais utilizadas.
Testes visuais (VT)
Como funciona: O teste visual é a forma mais simples e mais antiga de teste não destrutivo, utilizando a inspeção visual para detetar irregularidades na superfície ou sinais visíveis de desgaste. Pode envolver a utilização de ferramentas como boroscópios, câmaras ou drones para inspecionar áreas que, de outra forma, seriam difíceis de alcançar. Em alguns casos, as inspecções visuais são melhoradas pela inteligência artificial, que pode analisar imagens para detetar sinais precoces de defeitos.
Aplicações: Os testes visuais são utilizados para inspecionar as superfícies externas de tanques, recipientes e condutas para detetar danos visíveis, como fugas, corrosão ou outras formas de degradação. Os drones e os robôs podem ser utilizados para inspecionar áreas de difícil acesso, permitindo avaliações visuais abrangentes sem necessidade de andaimes ou de grandes períodos de inatividade.
Ensaio por ultra-sons (UT)
Como funciona: Os testes ultra-sónicos utilizam ondas sonoras de alta frequência que são transmitidas através dos materiais. Quando estas ondas encontram um defeito, reflectem-se de forma diferente, permitindo aos técnicos localizar e dimensionar as falhas internas. O processo é semelhante à forma como os ultra-sons são utilizados na imagiologia médica, mas adaptado para utilização industrial.
Aplicações: O UT é amplamente utilizado para medir a espessura, localizar defeitos internos e detetar a corrosão. É especialmente valioso para inspecionar tubagens, soldaduras e tanques de armazenamento, onde os problemas podem não ser visíveis à superfície. Os testes ultra-sónicos podem mesmo detetar fases iniciais de corrosão ou desbaste, fornecendo um sistema de alerta avançado para potenciais pontos de falha.
Ensaios radiográficos (RT)
Como funciona: Os testes radiográficos envolvem a utilização de raios X ou raios gama para criar imagens dos componentes do equipamento. A radiação passa através dos materiais e cria imagens em película ou sensores digitais. As variações de densidade causadas por falhas ou defeitos aparecem como sombras na imagem, permitindo que os técnicos as identifiquem e avaliem.
Aplicações: A RT é frequentemente utilizada para inspecionar a integridade das soldaduras, detetar corrosão e localizar fissuras, particularmente em áreas inacessíveis de tubos, cotovelos e recipientes sob pressão. Esta técnica é particularmente eficaz para avaliar as soldaduras, que são frequentemente pontos de vulnerabilidade em ambientes de elevada tensão. Os testes radiográficos também podem ser utilizados para inspecionar componentes de paredes espessas, garantindo a integridade estrutural onde é mais necessária.
Ensaio de partículas magnéticas (MPT)
Como funciona: O teste de partículas magnéticas aplica um campo magnético à superfície do equipamento e, em seguida, espalha partículas magnéticas sobre ela. Quando existem defeitos superficiais ou próximos da superfície, estes perturbam o campo magnético, fazendo com que as partículas se agrupem à volta da área do defeito, tornando-o visível.
Aplicações: O MPT é especialmente eficaz para identificar defeitos superficiais e subsuperficiais pouco profundos em materiais ferromagnéticos. É normalmente utilizado para inspecionar condutas, equipamento de cabeça de poço, peças fundidas e outros materiais ferromagnéticos. Como o MPT é um processo relativamente simples, é também uma opção económica para inspecções de rotina de equipamento suscetível.
Ensaios de correntes parasitas (ECT)
Como funciona: O teste de correntes parasitas utiliza uma bobina electromagnética para gerar correntes dentro de materiais condutores, que podem variar de intensidade em resposta a falhas no material de base. A ferramenta mede as correntes parasitas induzidas no material de base, permitindo aos técnicos detetar e caraterizar defeitos ou corrosão.
Aplicações: O ECT é ideal para inspecionar materiais não ferromagnéticos como o aço inoxidável, normalmente encontrado em sistemas de tubagens, permutadores de calor e plataformas offshore. Uma vez que é sensível a pequenas alterações, o ECT é frequentemente utilizado para inspecionar tubagens de paredes finas, detectando a corrosão em fase inicial ou pequenas fissuras que podem conduzir a problemas mais graves.
Benefícios dos Ensaios Não Destrutivos na Indústria
Os NDT transformaram a forma como as indústrias lidam com a manutenção e inspeção de equipamentos. Oferecem inúmeras vantagens, incluindo:
- Redução do tempo de paragem: Muitos métodos NDT podem ser executados enquanto o equipamento permanece em serviço, minimizando as interrupções operacionais e permitindo uma monitorização contínua.
- Poupança de custos: A deteção proactiva de problemas ajuda a evitar reparações de emergência dispendiosas ou substituições completas do equipamento. O NDT permite às empresas programar a manutenção de forma mais estratégica, reduzindo os custos a longo prazo.
- Maior segurança: O NDT permite a deteção precoce de potenciais pontos de falha, reduzindo a probabilidade de incidentes catastróficos que podem pôr em perigo vidas e o ambiente.
- Aumento da vida útil do equipamento: A inspeção regular com técnicas NDT ajuda a manter o equipamento nas melhores condições, prolongando a sua vida operacional e melhorando o retorno do investimento.
- Conformidade regulamentar: Muitas indústrias estão fortemente regulamentadas, com diretrizes ambientais e de segurança rigorosas. O NDT desempenha um papel vital na garantia de que as empresas permanecem em conformidade com estas normas.
O futuro dos ensaios não destrutivos
À medida que a tecnologia avança, os métodos NDT continuam a evoluir. A imagiologia avançada, a automação, a inteligência artificial e a aprendizagem automática estão a transformar os processos de inspeção tradicionais, tornando-os mais rápidos, mais precisos e mais fiáveis. Por exemplo, a análise de imagens de inspecções visuais baseada em IA pode detetar irregularidades que poderiam passar despercebidas aos inspectores humanos. Do mesmo modo, os sistemas robóticos equipados com capacidades de teste ultrassónico ou de correntes de Foucault estão a melhorar o alcance e a eficiência das inspecções.
No futuro, os NDT poderão tornar-se ainda mais integrados na gestão de activos, com sistemas que utilizam dados em tempo real para antecipar potenciais problemas antes de estes surgirem. Estes avanços poderão revolucionar a abordagem à manutenção de equipamentos, passando de medidas preventivas para soluções preditivas que permitam às empresas enfrentar os riscos de forma preventiva.
Num mundo ideal, o equipamento nunca falharia, mas com o poder dos ensaios não destrutivos, podemos estar mais perto de alcançar esse ideal, minimizando os riscos e maximizando a segurança, a eficiência e a longevidade dos activos críticos.
Implementação de um programa eficaz de gestão de inspecções
Conceber e implementar um programa de inspeção e monitorização para indústrias pesadas de activos não é uma tarefa trivial. Uma tarefa ainda mais difícil é manter o controlo e dar sentido às informações recolhidas. Na Cenosco, o nosso objetivo é permitir-lhe certificar-se de que os seus programas de inspeção e monitorização são concebidos e implementados para garantir a integridade, fiabilidade e segurança das suas operações.
O IMS - Sistema de Gestão da Integridade - foi concebido desde o início para ajudar a conceber e implementar programas de inspeção eficazes, utilizando modelos baseados no risco para dar prioridade e programar as inspecções ao equipamento. As nossas capacidades inigualáveis de modelação da corrosão utilizam os dados recolhidos do seu programa de inspecções de equipamento para aperfeiçoar os intervalos de inspeção, de modo a garantir que os recursos limitados de inspeção e manutenção são atribuídos de forma eficiente e eficaz.
Para saber mais sobre como o IMS pode melhorar os resultados dos seus programas de inspeção e monitorização, preencha o formulário abaixo, ou clique aqui para saber mais sobre o IMS PEI.
Pedir uma demonstração
Descubra como o IMS pode transformar e otimizar as suas operações...
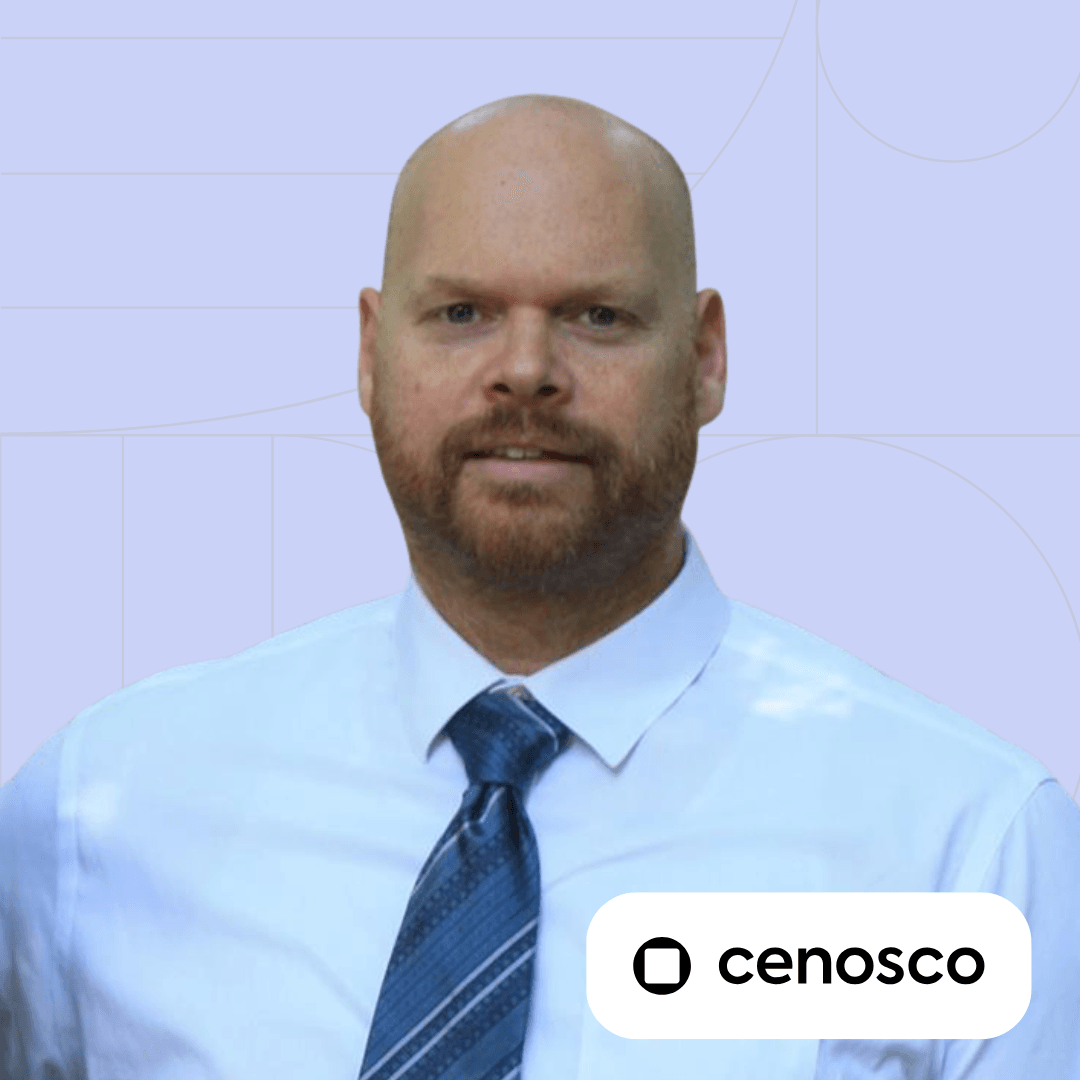
Tomislav Renić Technical Writer
Tomislav is an experienced engineer and technical communicator with over 20 years in complex systems, modeling, and project management. As a Technical Writer at Cenosco, he translates engineering concepts into clear, user-friendly documentation for software in the oil, gas, and refining industries.