En un mundo ideal, los equipos a presión nunca explotarían, los tanques nunca fallarían y las tuberías nunca tendrían fugas. En realidad, estos equipos pueden fallar y fallan, a veces con consecuencias devastadoras. Los fallos de los equipos pueden provocar la pérdida de vidas humanas, catástrofes medioambientales y cuantiosas pérdidas económicas, sobre todo en sectores con muchos activos, como el del petróleo y el gas, el petroquímico y el de generación de energía. La necesidad de prevenir los fallos ha llevado a estos sectores a adoptar rigurosos protocolos de inspección y mantenimiento, que garantizan la detección de posibles problemas antes de que se conviertan en catástrofes.
Aunque las causas de los fallos de los equipos a menudo pueden identificarse retrospectivamente, confiar en un análisis a posteriori dista mucho de ser lo ideal. Por ejemplo, si falla una caldera o un recipiente a presión, los investigadores pueden recoger muestras del equipo averiado para analizarlas en el laboratorio y determinar la causa.
Este proceso de investigación proporciona información inestimable que puede incluirse en futuros diseños de equipos y programas de supervisión y mantenimiento, pero sólo si ya se ha producido el fallo. En la mayoría de los casos, esperar a que el equipo falle para tomar medidas no es una estrategia viable, sobre todo cuando el fallo puede acarrear graves consecuencias.
Uno de los principales métodos para prevenir fallos en los equipos consiste en evaluar su integridad utilizando modelos basados en el riesgo para establecer calendarios y alcances adecuados para las inspecciones de los equipos. Estos modelos priorizan y programan las inspecciones de los equipos en función de los riesgos potenciales, teniendo en cuenta la probabilidad de fallo y la gravedad de las consecuencias.
Este enfoque permite a las empresas concentrar sus recursos en los equipos que presentan mayor riesgo, garantizando que los fallos se identifiquen y mitiguen antes de que se produzcan. Al dar prioridad a los equipos de alto riesgo, pueden evitarse los resultados costosos y potencialmente catastróficos que pueden derivarse de un fallo inesperado de los equipos.
Un componente esencial de esta estrategia de inspección es el uso de ensayos no destructivos (END) para evaluar el estado de los equipos. Los ensayos no destructivos permiten a los inspectores identificar posibles problemas -como corrosión, grietas o defectos- sin causar ningún daño al equipo. A menudo, los ensayos no destructivos pueden realizarse mientras el equipo sigue en servicio, lo que permite que las operaciones continúen mientras se protege la salud humana y el medio ambiente.
Ensayos no destructivos: ¿Qué son?
Como su nombre indica, los ensayos no destructivos engloban una serie de métodos que permiten a los inspectores identificar posibles problemas en los equipos sin causar daños. Estas técnicas son importantes para los equipos que aún están en servicio o que deben volver a ponerse en servicio rápidamente. A diferencia de otros métodos de ensayo más intrusivos que pueden dañar los equipos inspeccionados, los ensayos no destructivos permiten detectar a tiempo el desgaste, los daños y los defectos.
Gracias a los END, los técnicos pueden identificar problemas ocultos como grietas internas, corrosión o adelgazamiento del metal, problemas que de otro modo serían indetectables sólo con una inspección superficial. Los END no sólo minimizan el tiempo de inactividad, sino que también ayudan a mantener la longevidad de los equipos, mejoran la seguridad y contribuyen al cumplimiento de la normativa. A continuación se indican algunas de las técnicas END más utilizadas.
Pruebas visuales (VT)
Cómo funciona: El ensayo visual es la forma más sencilla y antigua de ensayo no destructivo, ya que utiliza la inspección visual para detectar irregularidades en la superficie o signos visibles de desgaste. Puede implicar el uso de herramientas como boroscopios, cámaras o drones para inspeccionar zonas de difícil acceso. En algunos casos, las inspecciones visuales se mejoran con inteligencia artificial, que puede analizar imágenes para detectar signos tempranos de defectos.
Aplicaciones: Las pruebas visuales se utilizan para inspeccionar las superficies externas de tanques, recipientes y tuberías en busca de daños visibles, como fugas, corrosión u otras formas de degradación. Pueden utilizarse drones y robots para inspeccionar zonas de difícil acceso, lo que permite realizar evaluaciones visuales exhaustivas sin necesidad de andamios ni largos periodos de inactividad.
Pruebas ultrasónicas (UT)
Cómo funciona: Las pruebas ultrasónicas utilizan ondas sonoras de alta frecuencia que se transmiten a través de los materiales. Cuando estas ondas encuentran un defecto, se reflejan de forma diferente, lo que permite a los técnicos localizar y dimensionar los defectos internos. El proceso es similar al de los ultrasonidos en medicina, pero adaptado al uso industrial.
Aplicaciones: La UT se utiliza ampliamente para medir espesores, localizar defectos internos y detectar la corrosión. Es especialmente valioso para inspeccionar tuberías, soldaduras y depósitos de almacenamiento, donde los problemas pueden no ser visibles en la superficie. Los ensayos por ultrasonidos pueden detectar incluso las primeras fases de corrosión o adelgazamiento, lo que supone un sistema de alerta avanzado para posibles puntos de fallo.
Pruebas radiográficas (RT)
Cómo funciona: Las pruebas radiográficas consisten en utilizar rayos X o rayos gamma para crear imágenes de los componentes de los equipos. La radiación atraviesa los materiales y crea imágenes en películas o sensores digitales. Las variaciones de densidad causadas por fallos o defectos aparecen como sombras en la imagen, lo que permite a los técnicos identificarlas y evaluarlas.
Aplicaciones: La RT se utiliza con frecuencia para inspeccionar la integridad de las soldaduras, detectar la corrosión y localizar grietas, sobre todo en zonas inaccesibles de tuberías, codos y recipientes a presión. Esta técnica es especialmente eficaz para evaluar soldaduras, que suelen ser puntos vulnerables en entornos de alta tensión. Los ensayos radiográficos también pueden utilizarse para inspeccionar componentes de paredes gruesas, garantizando la integridad estructural donde más se necesita.
Prueba de partículas magnéticas (MPT)
Cómo funciona: La prueba de partículas magnéticas aplica un campo magnético a la superficie del equipo y, a continuación, esparce partículas magnéticas sobre ella. Cuando hay defectos superficiales o cercanos a la superficie, estos perturban el campo magnético, haciendo que las partículas se agrupen alrededor de la zona del defecto, haciéndolo visible.
Aplicaciones: La MPT es especialmente eficaz para identificar defectos superficiales y subsuperficiales poco profundos en materiales ferromagnéticos. Se utiliza habitualmente para inspeccionar tuberías, equipos de boca de pozo, piezas de fundición y otros materiales ferromagnéticos. Dado que la MPT es un proceso relativamente sencillo, también es una opción rentable para las inspecciones rutinarias de equipos susceptibles.
Pruebas de corrientes de Foucault (ECT)
Cómo funciona: El ensayo por corrientes de Foucault utiliza una bobina electromagnética para generar corrientes dentro de los materiales conductores, que pueden variar en intensidad en respuesta a los defectos del material base. La herramienta mide las corrientes de Foucault inducidas en el material base, lo que permite a los técnicos detectar y caracterizar defectos o corrosión.
Aplicaciones: La ECT es ideal para inspeccionar materiales no ferromagnéticos como el acero inoxidable, que suele encontrarse en sistemas de tuberías, intercambiadores de calor y plataformas marinas. Dado que es sensible a los pequeños cambios, la ECT se utiliza a menudo para inspeccionar tuberías de pared delgada, detectando la corrosión en sus primeras etapas o pequeñas grietas que podrían dar lugar a problemas más graves.
Ventajas de los ensayos no destructivos en la industria
Los END han transformado la forma en que las industrias gestionan el mantenimiento y la inspección de equipos. Ofrecen numerosas ventajas, entre ellas
- Reducción del tiempo de inactividad: Muchos métodos END pueden realizarse mientras el equipo permanece en servicio, lo que minimiza las interrupciones operativas y permite una supervisión continua.
- Ahorro de costes: La detección proactiva de problemas ayuda a evitar costosas reparaciones de emergencia o sustituciones completas de los equipos. Los END permiten a las empresas programar el mantenimiento de forma más estratégica, lo que reduce los costes a largo plazo.
- Mayor seguridad: Los END permiten la detección temprana de posibles puntos de fallo, reduciendo la probabilidad de incidentes catastróficos que podrían poner en peligro vidas humanas y el medio ambiente.
- Prolongación de la vida útil de los equipos: La inspección periódica con técnicas END ayuda a mantener los equipos en condiciones óptimas, lo que prolonga su vida útil y mejora la rentabilidad de la inversión.
- Cumplimiento de la normativa: Muchas industrias están fuertemente reguladas, con estrictas directrices de seguridad y medioambientales. Los END desempeñan un papel fundamental para garantizar que las empresas cumplan estas normas.
El futuro de los ensayos no destructivos
A medida que avanza la tecnología, los métodos de END siguen evolucionando. Las imágenes avanzadas, la automatización, la inteligencia artificial y el aprendizaje automático están transformando los procesos de inspección tradicionales, haciéndolos más rápidos, precisos y fiables. Por ejemplo, el análisis de imágenes de inspecciones visuales basado en IA puede detectar irregularidades que los inspectores humanos pasarían por alto. Del mismo modo, los sistemas robóticos equipados con capacidades de ensayo por ultrasonidos o corrientes de Foucault están mejorando el alcance y la eficacia de las inspecciones.
En el futuro, los END podrían integrarse aún más en la gestión de activos, con sistemas que utilicen datos en tiempo real para anticipar posibles problemas antes de que surjan. Estos avances podrían revolucionar el enfoque del mantenimiento de equipos, pasando de las medidas preventivas a soluciones predictivas que permitan a las empresas abordar los riesgos de forma preventiva.
En un mundo ideal, los equipos nunca fallarían, pero con el poder de los ensayos no destructivos, podemos acercarnos más a ese ideal minimizando los riesgos y maximizando la seguridad, la eficacia y la longevidad de los activos críticos.
Implantación de un programa eficaz de gestión de inspecciones
Diseñar y poner en marcha un programa de inspección y supervisión para industrias de gran volumen de activos no es una tarea trivial. Una tarea aún más difícil es hacer un seguimiento y dar sentido a la información recopilada. En Cenosco, nuestro objetivo es permitirle asegurarse de que sus programas de inspección y supervisión están diseñados e implementados para garantizar la integridad, fiabilidad y seguridad de sus operaciones.
IMS - el Sistema de Gestión de la Integridad - está diseñado desde cero para ayudar a diseñar e implementar programas de inspección eficaces, utilizando modelos basados en el riesgo para priorizar y programar las inspecciones de los equipos. Nuestras incomparables capacidades de modelado de la corrosión utilizan los datos recopilados de su programa de inspecciones de equipos para perfeccionar sus intervalos de inspección, de modo que pueda garantizar que los limitados recursos de inspección y mantenimiento se asignan de forma eficiente y eficaz.
Para obtener más información sobre cómo IMS puede mejorar los resultados de sus programas de inspección y supervisión, rellene el siguiente formulario o haga clic aquí para obtener más información sobre IMS PEI.
Solicitar una demostración
Descubra cómo IMS puede transformar y optimizar sus operaciones...
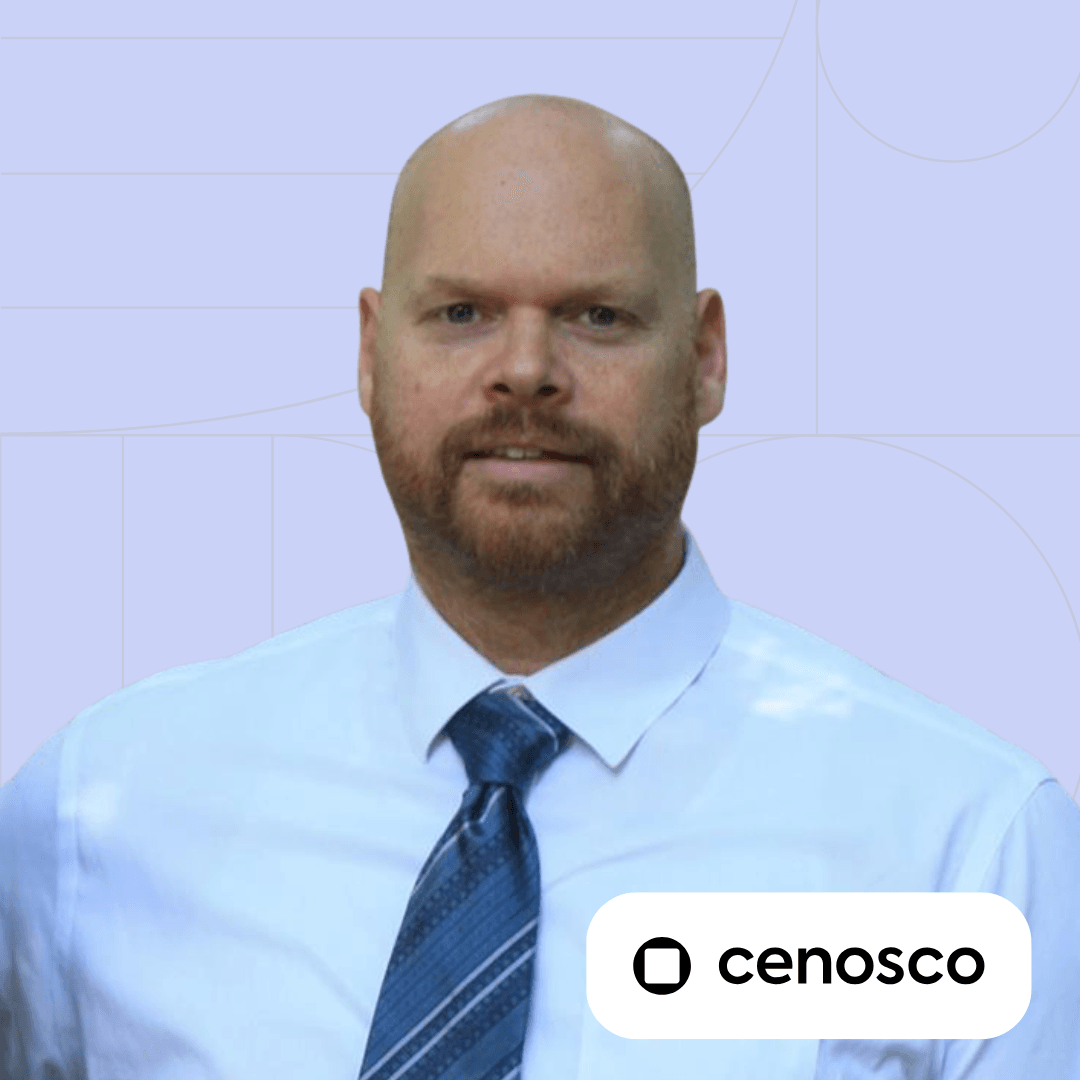
Tomislav Renić Technical Writer
Tomislav is an experienced engineer and technical communicator with over 20 years in complex systems, modeling, and project management. As a Technical Writer at Cenosco, he translates engineering concepts into clear, user-friendly documentation for software in the oil, gas, and refining industries.