Korrosionsdaten spielen eine Schlüsselrolle im Korrosions- und Integritätsmanagement von Anlagen. Sie liefern wichtige Informationen, um die Sicherheit und Langlebigkeit von Anlagen zu gewährleisten. Dies gilt insbesondere für prozessintensive Industrien, die flüchtige Materialien verwenden, wie z. B. die Öl- und Gasindustrie oder die Petrochemie, wo Korrosion eine häufige Schadensursache ist.
Ein wirksames Korrosionsmanagement erfordert qualitativ hochwertige Korrosionsdaten. Um diese Daten jedoch in nützliche Informationen umzuwandeln, müssen sie zunächst analysiert und interpretiert werden. Der Einsatz von Datenanalyse- und Visualisierungstools kann den Prozess der Abschätzung der verbleibenden Lebensdauer von Anlagen präziser machen und das Vertrauen in datengestützte Entscheidungen erhöhen, was zu potenziellen Kosteneinsparungen führt.
In diesem Blogbeitrag untersuchen wir den Wert genauer Korrosionsdaten und erörtern, wie Korrosionsanalyse und -visualisierung in das Korrosionsinspektionsmanagement einfließen.
Was sind Korrosionsdaten?
Korrosionsdaten sind Informationen über die allmähliche Verschlechterung von Metallen durch chemische oder elektrochemische Einwirkung von Umweltelementen und Prozessflüssigkeiten. Diese Daten geben Aufschluss über den aktuellen Zustand einer Anlage und können helfen, zukünftige Korrosion vorherzusagen und zu verhindern.
Zu den wichtigsten Arten von Korrosionsdaten gehören u. a. die folgenden:
- Lage der korrodierten Stellen
- Art der vorhandenen Korrosion
- Messungen der Wanddicke
- Korrosionsrate
Die Intervalle und Ergebnisse einer risikobasierten Inspektion (RBI) oder einer Korrosionsstudie gelten ebenfalls als Korrosionsdaten. Überfällige Inspektionspläne und Daten, die während visueller Inspektionen gesammelt werden, können ebenfalls als Korrosionsdaten verwendet werden.
Um sicherzustellen, dass bei der Korrosionsinspektion und -überwachung relevante Korrosionsdaten gewonnen werden, müssen Sie wissen, was Sie zu erwarten haben und welche Zersetzungsmechanismen in dem System vorhanden sind. Mit diesen Informationen können Sie gute Inspektionspläne erstellen und genaue und zuverlässige Korrosionsdaten sammeln, die Ihnen helfen, potenzielle Schäden zu erkennen und zu beheben, bevor sie zu einem größeren Problem werden.
Wenn Sie zum Beispiel davon ausgehen, dass Spannungsrisskorrosion der Degradationsmechanismus in Ihrem System ist, sich aber nur auf den Verlust der Wanddicke konzentrieren, entgehen Ihnen möglicherweise wertvolle Informationen, die sich auf die Integrität der Anlage auswirken könnten.
In der Entwurfsphase einer Anlage können Sie auf der Grundlage theoretischer Untersuchungen potenzielle Degradationsmechanismen berücksichtigen. Dies kann Vorhersagen über die Auswirkungen von Faktoren wie Temperatur, Feuchtigkeit, mechanische Belastung und chemische Wechselwirkungen beinhalten.
Darüber hinaus können Sie theoretische Ansätze verwenden, um die Lebensdauer einer Anlage und die langfristigen Auswirkungen einer Verschlechterung abzuschätzen. Aber erst wenn die Anlage in Betrieb ist, können Sie durch Inspektionen echte Korrosionsdaten sammeln.
Die Rolle von Korrosionsschleifen bei der Erfassung umfassender Korrosionsdaten
Sobald die Anlage in Betrieb ist, können Sie damit beginnen, Korrosionsdaten aus verschiedenen Quellen zu sammeln, eine der wichtigsten sind Korrosionsschleifen. Korrosionsschleifen fassen Anlagen und Rohrleitungen mit ähnlichen Abbauprozessen in überschaubaren Abschnitten zusammen, die gemeinsam überwacht und analysiert werden können, um die Wahrscheinlichkeit eines Ausfalls zu ermitteln.
Korrosionsschleifen können dazu dienen, Ihre Inspektionsstrategie zu verbessern und alle relevanten Informationen in einem Dokument zusammenzufassen. Dieses Dokument hat in der Regel das Format eines Prozessflussdiagramms und enthält Konstruktionsmaterialien, Medien, Betriebsbedingungen und erwartete Verschlechterungsmechanismen. Dies bildet die Grundlage für alle Korrosionsmanagementkonzepte, denn sobald die Degradationsmechanismen definiert sind, können Sie über die Barrieren nachdenken, die Sie einführen wollen, um zu verhindern, dass diese Mechanismen in ihren Prozessen auftreten.
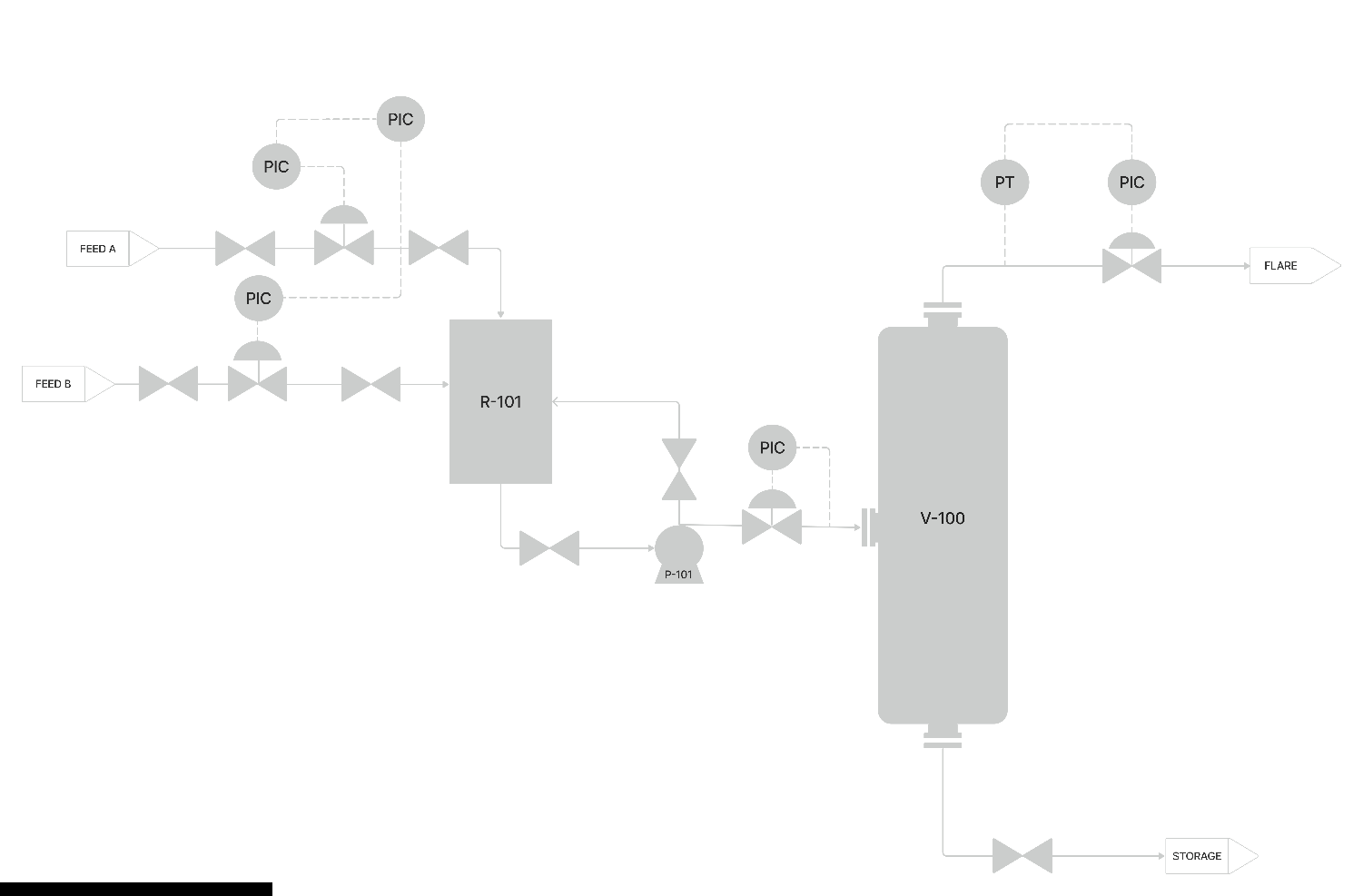
Wie man effizientes Korrosionsmanagement betreibt
Erfolgreiches Korrosionsmanagement wird durch den Aufbau einer Historie von Überwachungsergebnissen und die Korrelation dieser Daten erreicht, um Trends und Muster zu erkennen. Sie können visuelle Elemente verwenden, um Daten auf aussagekräftige Weise darzustellen, um die Leistung und den Zustand Ihrer Anlagen zu bestimmen und zu überwachen. Datenvisualisierungstools bieten eine zugängliche Möglichkeit, Trends, Muster und Ausreißer in Datensätzen zu sehen und zu verstehen, was Ihnen hilft, Bereiche zu erkennen, die verbessert werden müssen oder Ihre Aufmerksamkeit erfordern.
Lassen Sie uns sehen, wie der ideale Prozess des Korrosionsdatenmanagements aussehen sollte:
Schritt 1 - Erfassung von Korrosionsdaten im Feld
Die Methode der Datenerfassung hängt von der Art der benötigten Daten ab und kann über eine Checkliste oder sogar über einen Messsatz erfolgen. Sie können zwar jederzeit Checklisten ausdrucken und die erfassten Korrosionsdaten später in die Inspektionssoftware importieren, doch ist dies sicherlich mit zusätzlichem Aufwand verbunden und anfällig für menschliche Fehler.
Hier kann eine Inspektionssoftware mit einem integrierten Tool, das die Konfiguration von personalisierten Checklisten vereinfacht, für Sie wertvoll sein. Dynamic Forms in der IMS-Software ist zum Beispiel ein Werkzeug, das den Arbeitsablauf bei Inspektionen durch die Standardisierung der Checklisten optimiert.
Um Ihren Inspektionsprozess zu rationalisieren, müssen Sie zunächst digitale, standardisierte Checklisten für Ihren spezifischen Standort erstellen. Erwägen Sie den Einsatz von Inspektionssoftware, die offline genutzt werden kann. Mit dieser Software können Sie die Inspektionsergebnisse in Echtzeit direkt in Ihrer digitalen Checkliste auf einem Tablet oder Mobilgerät aufzeichnen, während Sie vor Ort sind. Auf diese Weise wird sichergestellt, dass die erfassten Daten sofort für die Analyse zur Verfügung stehen, da sie automatisch an Ihr Inspektionsdatenmanagementsystem übermittelt werden.
Schritt 2 - Visualisierung und Analyse von Korrosionsdaten
Es gibt zwei Hauptmethoden, um Korrosionsdaten zu verarbeiten und zu analysieren:
- Durch wichtige Leistungsindikatoren (KPIs)
- Durch Erkennung von Anomalien
KPI-Dashboards sind eine standardisierte Methode, um Daten zu verarbeiten und Trends zu verstehen. Sie bieten ein konfigurierbares Format, das zusätzliche Aktionen auslösen kann, um Fehler zu vermeiden. Wenn Sie alle KPIs in einem Dashboard zusammenfassen, erhalten Sie eine Visualisierung, die einen klaren Überblick über die Daten bietet.
Ein Beispiel dafür, wie Sie Korrosionsdaten über KPI-Dashboards verwalten und visualisieren können, sind Integrity Operating Windows (IOWs). Durch die Überwachung der Injektionsraten von Korrosionsschutzmitteln können Sie Abweichungen von den Spezifikationen erkennen. Dann können Sie diese Informationen nutzen, um Probleme anzugehen, bevor sie die Integrität Ihrer Anlagen beeinträchtigen.
Ein weiteres Beispiel ist die Durchführung eines Änderungsmanagements (MOC) oder einer betrieblichen Risikobewertung. Wenn Sie Probleme mit den Pumpen haben, die für die Injektion eines Korrosionsinhibitors oder Biozids verwendet werden, können Sie das Risiko der Situation einschätzen und festlegen, wie damit umzugehen ist. Da alle Informationen an einem Ort verfügbar sind, können Sie bessere Entscheidungen treffen und proaktive Maßnahmen ergreifen, um korrosionsbedingte Ausfälle zu verhindern.
Die Erkennung von Anomalien kommt zum Einsatz, wenn ein Fehler oder eine Anomalie in den Daten vorliegt. Sie müssen die Daten aus verschiedenen Blickwinkeln analysieren und sie mit externen Quellen korrelieren. Dieser Ansatz ist nützlich, um potenzielle Risiken zu erkennen und proaktive Maßnahmen zu ergreifen, um korrosionsbedingte Ausfälle zu verhindern.
Schritt 3 - Berechnung der verbleibenden Lebensdauer
Nachdem Sie Ihre Daten gesammelt und analysiert haben, müssen Sie noch die Restnutzungsdauer (RL) der Anlage berechnen. Die RL-Berechnung ist recht einfach, da die RL anhand der Korrosionsrate berechnet wird. Für diese Berechnung sind jedoch genaue Korrosionsraten erforderlich, und genau hier kommen gute Daten ins Spiel.
Schritt 4 - Anpassung des Inspektionsplans
Sobald Sie die Restlebensdauer Ihrer Geräte berechnet haben, können Sie anhand dieser Daten entscheiden, ob Sie die Inspektionshäufigkeit erhöhen oder verringern wollen. Außerdem können Sie damit fundierte Entscheidungen darüber treffen, welche Komponenten in welchem Umfang inspiziert werden sollen.
Korrosionsdaten in den verschiedenen Phasen des Lebenszyklus der Anlagenintegrität
Asset Integrity Management ist ein kontinuierlicher Verbesserungsprozess, der sich am besten als zyklischer Kreislauf darstellen lässt, der erst mit der Ausmusterung der Anlage endet. In jeder Phase gilt: Je mehr qualitativ hochwertige Korrosionsdaten Sie haben, desto besser für den Ablauf des Prozesses.
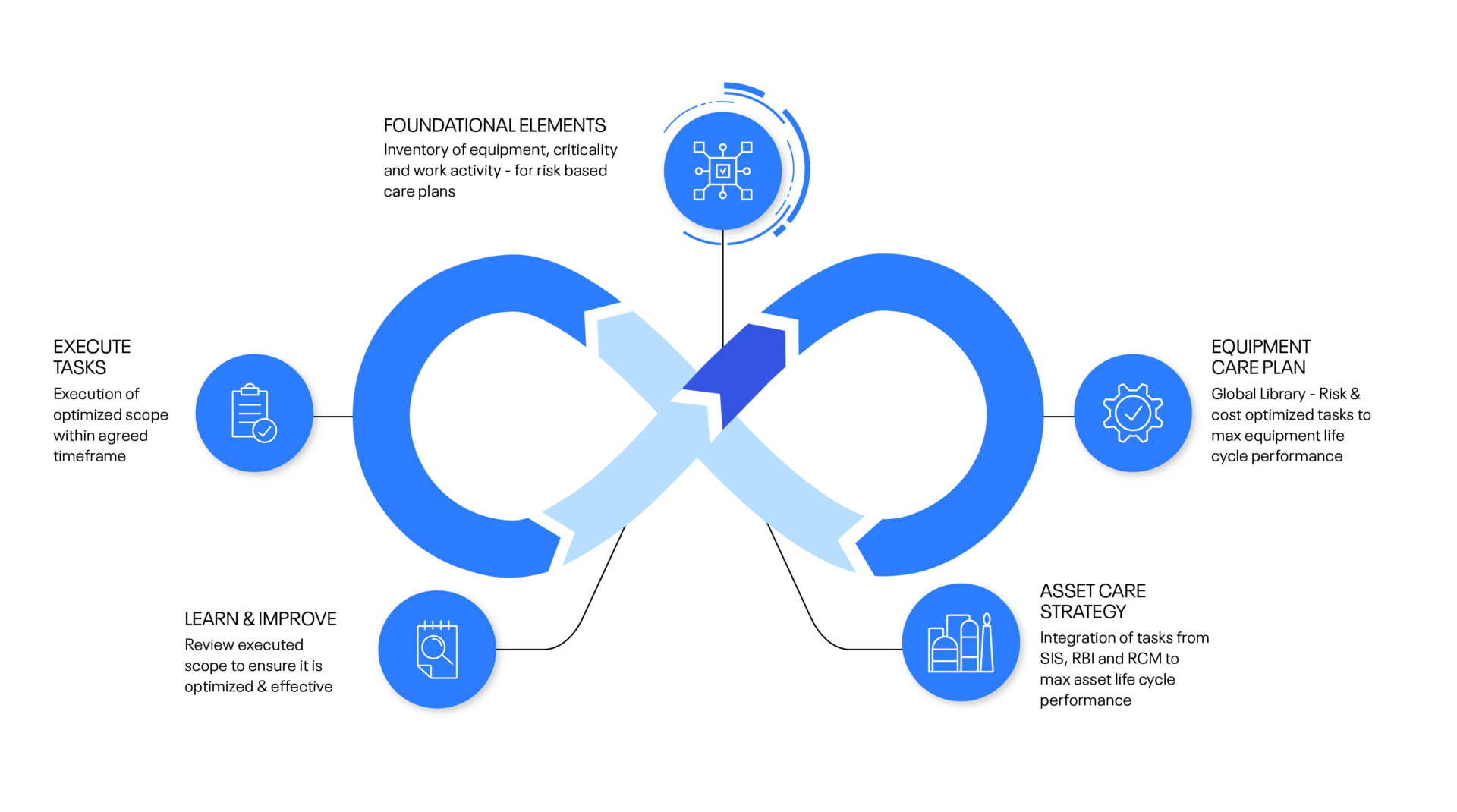
Der Kreislauf beginnt mit grundlegenden Elementen - wie technische Daten, Konstruktionsmaterialien, Startdatum, Prozessbedingungen, Material und RBI-Daten - die zur Entwicklung eines Anlagenpflegeplans verwendet werden, der die Häufigkeit und den Umfang der Inspektion bestimmt.
In der Phase der Asset-Care-Strategie arbeiten Sie an der Optimierung des Plans, indem Sie Daten aus verschiedenen Disziplinen für die betreffende Anlage und die betroffenen und beeinträchtigten Anlagen analysieren.
In der nächsten Phase führen Sie den optimierten Plan aus und sammeln Daten aus verschiedenen Quellen wie IOWs, Wanddickenmessung, visuelle Inspektion, zerstörungsfreie Prüfung usw...
Der Zyklus setzt sich in einer Lern- und Verbesserungsphase fort, in der Sie die gesammelten Daten mithilfe von KPIs, Anomalieanalysen und Ursachenanalysen analysieren, um den Zustand der Ausrüstung zu bewerten und die grundlegenden Elemente zu verbessern. Und dann beginnt der Kreislauf von neuem.
Erschließen Sie die Leistungsfähigkeit von Korrosionsdaten mit IMS-Software
Wie wir inzwischen gesehen haben, ist es wichtig, während des gesamten Prozesses des Asset-Integrity-Managements gute Korrosionsdaten zu erhalten, um effektive Korrosions-Trends und Datenanalysen für jede Art von altersbedingter Verschlechterung sicherzustellen. Aber Daten, die nicht verarbeitet und analysiert werden, sind nicht nützlich, da sie nicht zur Entscheidungsfindung beitragen können. Der Einsatz von Technologien, wie z. B. digitalen Checklisten, kann bei der Eingabe von Daten in einem strukturierten Format helfen, was die Verwaltung, Visualisierung und Analyse von Korrosionsstudien und Verschlechterungen im Allgemeinen erleichtert.
Mit IMS ist es möglich, einen Rahmen für das Korrosionsmanagement zu entwickeln, der eine umfassende Verwaltung von Korrosionsdaten ermöglicht. IMS integriert verschiedene Arten von Integritätsanalysetools, einschließlich eines risikobasierten Inspektionsmoduls und Analysetools wie S-IDAP, zur Visualisierung und zum Korrosionsmanagement. Darüber hinaus bietet IMS eine Schnittstelle zu CMMS und Enterprise Asset Management, wodurch die Integration von Felddaten in Ihre bestehenden Instandhaltungssysteme erleichtert wird. Da alle Teams über den aktuellen Stand der Anlagen informiert sind, können Sie sich auf IMS als umfassendes Asset-Integrity-Management-Tool verlassen.
Möchten Sie die IMS-Checklisten und Dynamic Forms ausprobieren?
Füllen Sie das nachstehende Formular aus, um mit uns in Kontakt zu treten und mehr zu erfahren.
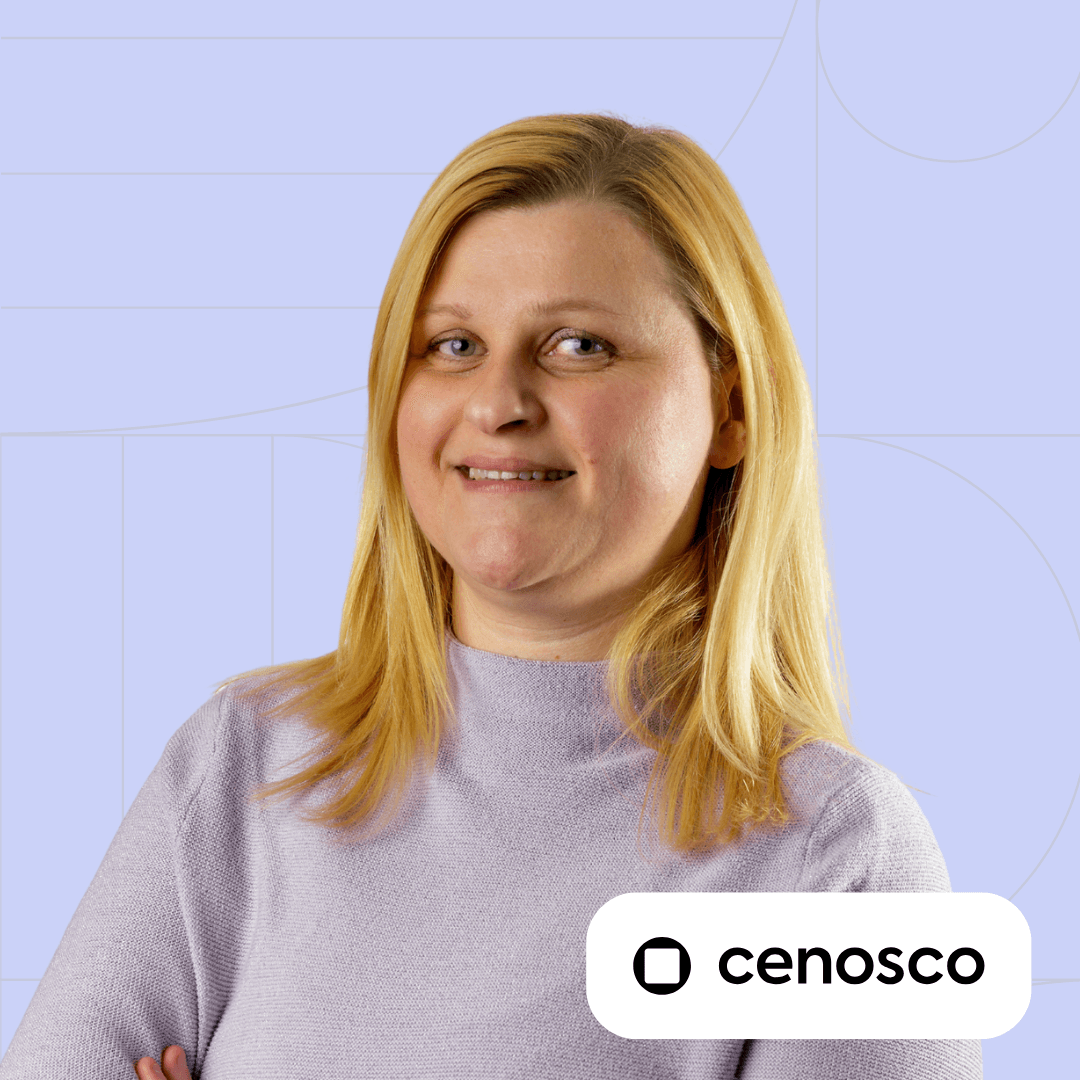
Denis Tkalec Technical writer
Denis Tkalec is a technical writer at Cenosco, specializing in asset integrity management software since 2022. With a background in education and six years in marketing, she turns complex topics into clear, user-friendly content. Inspired by Camus’s belief that “a writer keeps civilization from destroying itself,” she brings precision and care to every manual.