Corrosion data plays a key role in asset corrosion and integrity management. It provides vital information to ensure the safety and longevity of assets. That is particularly the case in process-intensive industries that use volatile materials like Oil & Gas or Petrochemicals where corrosion is a common source of damage.
Effective corrosion management requires good-quality corrosion data. But to turn that data into useful information, it must be analyzed and interpreted first. Using data analysis and visualization tools can make the process of estimating remaining equipment life more accurate and provide increased confidence in data-driven decision-making, leading to potential cost savings.
In this blog post, we explore the value of accurate corrosion data and discuss how corrosion analysis and visualization reflect in corrosion inspection management.
What is corrosion data?
Corrosion data is information related to the gradual deterioration of metals by chemical or electrochemical exposure to environmental elements and process fluids. This data can provide insight into the current state of any given asset and can help in predicting and preventing future corrosion.
Core types of corrosion data include but are not limited to the:
- Location of corroded areas
- Type of corrosion present
- Wall thickness measurements
- Corrosion rate
The intervals and outcomes of a risk-based inspection (RBI) or a corrosion study are also considered corrosion data. Overdue inspection plans and data collected during visual inspections can also be used as corrosion data.
To ensure that relevant corrosion data is obtained from corrosion inspection and monitoring, you need to know what to expect and what degradation mechanisms are present in the system. You can use this information to create good inspection plans and gather accurate and reliable corrosion data which will help you to detect potential damage and fix it before it becomes a bigger problem.
For example, if you expect stress corrosion cracking to be the degradation mechanism in your system, but you only focus on wall thickness loss, you may miss valuable information that could impact the integrity of the asset.
During the design phase of an asset, you can consider potential degradation mechanisms based on theoretical examination. This can include predictions of the effects of elements such as temperature, humidity, mechanical stress, and chemical interactions.
Additionally, you can use theoretical approaches to estimate the service life of an asset and the long-term effects of degradation. But only when the asset is operational will you be able to collect real corrosion data by doing inspections.
The Role of Corrosion Loops in Collecting Comprehensive Corrosion Data
Once the asset is operational, you can start gathering corrosion data from various sources, one of the most important ones being corrosion loops. Corrosion loops group equipment and piping with similar degradation mechanisms into manageable sections that can be monitored and analyzed together to determine the likelihood of failure.
Corrosion loops can be used to improve your inspection strategy and gather all relevant information in one document. Typically, this document is in the process flow diagram format and includes materials of construction, media, operating conditions, and expected degradation mechanisms. This forms the basis for all corrosion management frameworks because once the degradation mechanisms are defined, you can think about the barriers you want to implement to avoid these mechanisms taking place in their processes.
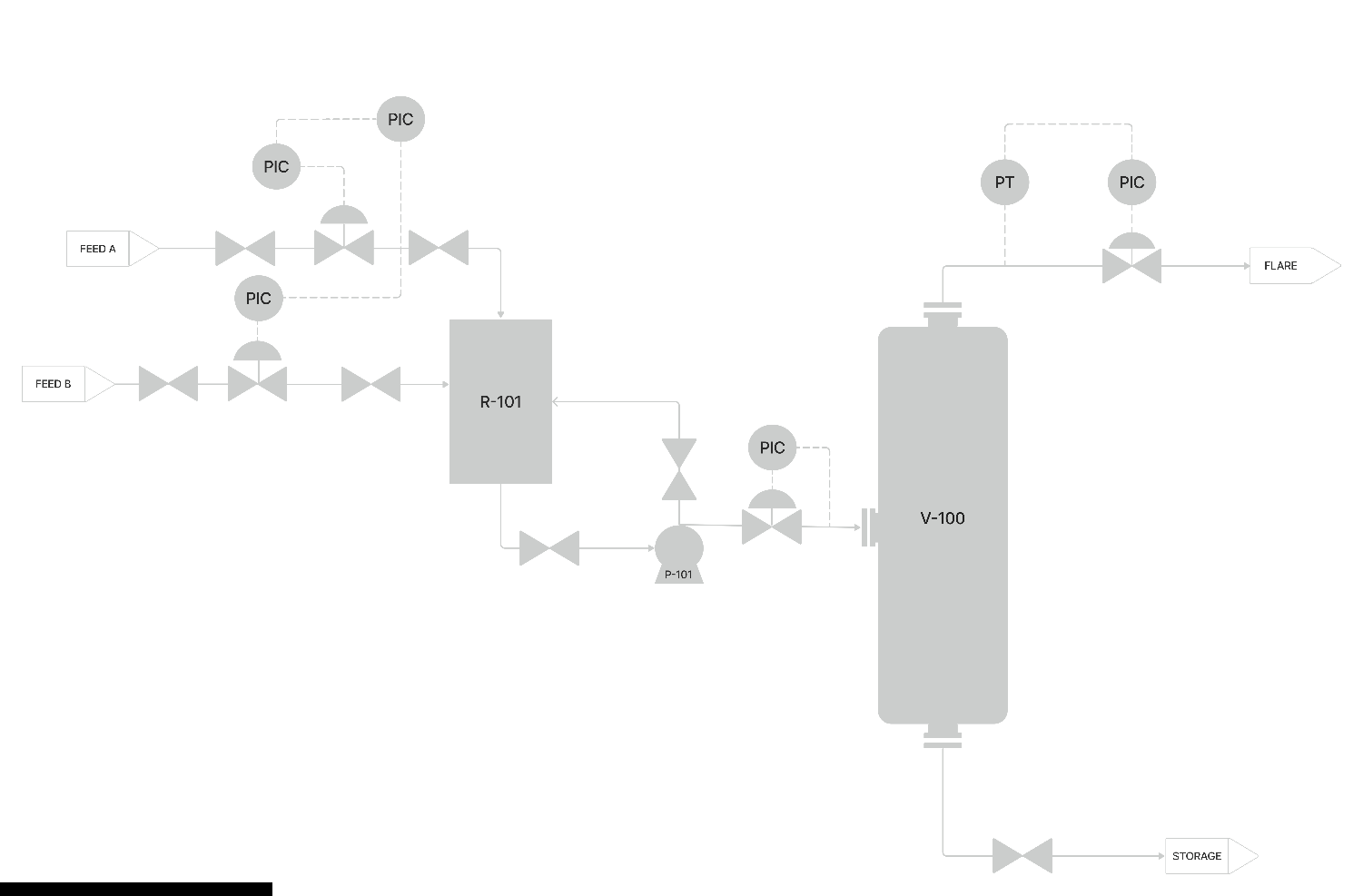
How to do efficient corrosion management
Successful corrosion management is achieved through building a history of monitoring results and correlating that data to identify trends and patterns. You can use visual elements to represent data in a meaningful way to determine and monitor the performance and condition of your assets. Data visualization tools provide an accessible way to see and understand trends, patterns, and outliers in data sets which helps you to figure out areas that require improvement or require your attention.
Let us see what the ideal process of corrosion data management should look like:
Step 1 – Capturing corrosion data in the field
The method of collecting data depends on the type of data you need and can be done through a checklist or even through a measurement set. While you can always print checklists and later import the captured corrosion data into the inspection software, it certainly involves additional effort and is prone to human errors.
This is where inspection software with an integrated tool that simplifies the configuration of personalized checklists could be valuable to you. For instance, Dynamic Forms within IMS software is a tool that optimizes the inspection workflow by standardizing the inspection checklists.
To streamline your inspection process, you need to create digital standardized checklists for your specific site first. Consider using inspection software that allows for offline use. With this software, you can record inspection results in real-time directly in your digital checklist on a tablet or mobile device while in the field. This ensures that the captured data is readily available for analysis as it is automatically submitted to your inspection data management system.
Step 2 – Visualizing and analyzing corrosion data
There are two primary ways you can process and analyze corrosion data:
- Through key performance indicators (KPIs)
- Through anomaly detection
KPI Dashboards are a standardized way to crunch data and understand trends. They provide a configurable format that can trigger additional actions to prevent failure. By putting all KPIs together into a dashboard, you will have a visualization that provides a clear overview of the data.
One example of how you can manage and visualize corrosion data through KPI Dashboards is through Integrity Operating Windows (IOWs). By monitoring corrosion inhibitor injection rates, you can detect deviations from specifications. Then you can use this information to address issues before they impact the integrity of your assets.
Another example is when you carry out a management of change (MOC) or operational risk assessment. If you are having issues with the pumps used for the injection of a corrosion inhibitor or biocide, you can assess the risk of the situation and determine how to handle it. By having all the information accessible in one place, you can make better decisions and take proactive measures to prevent corrosion-related failures.
Anomaly detection is used when there is a failure or anomaly in the data. You will need to analyze the data from different angles and correlate it with external sources. This approach is useful for identifying potential risks and taking proactive measures to prevent corrosion-related failures.
Step 3 – Calculating Remnant life
Once you have collected and analyzed your data, you will still need to calculate the remnant life (RL) of the asset. The RL calculation is rather simple, as the RL is calculated using the corrosion rate. However, accurate corrosion rates are required for this calculation, and that is where good data enters the equation.
Step 4 – Adjusting Inspection plan
Once you have calculated the remnant life of your equipment, this data can help you to decide whether to increase or reduce the inspection frequency. Furthermore, it can be used to make informed decisions on which components to inspect and to what extent.
Corrosion data in the distinct phases of the asset integrity lifecycle
Asset Integrity Management is an ongoing process of improvement, best demonstrated as a cyclical loop that finishes only when the equipment is retired. In each phase, the more quality corrosion data you have, the better for the process’s flow.
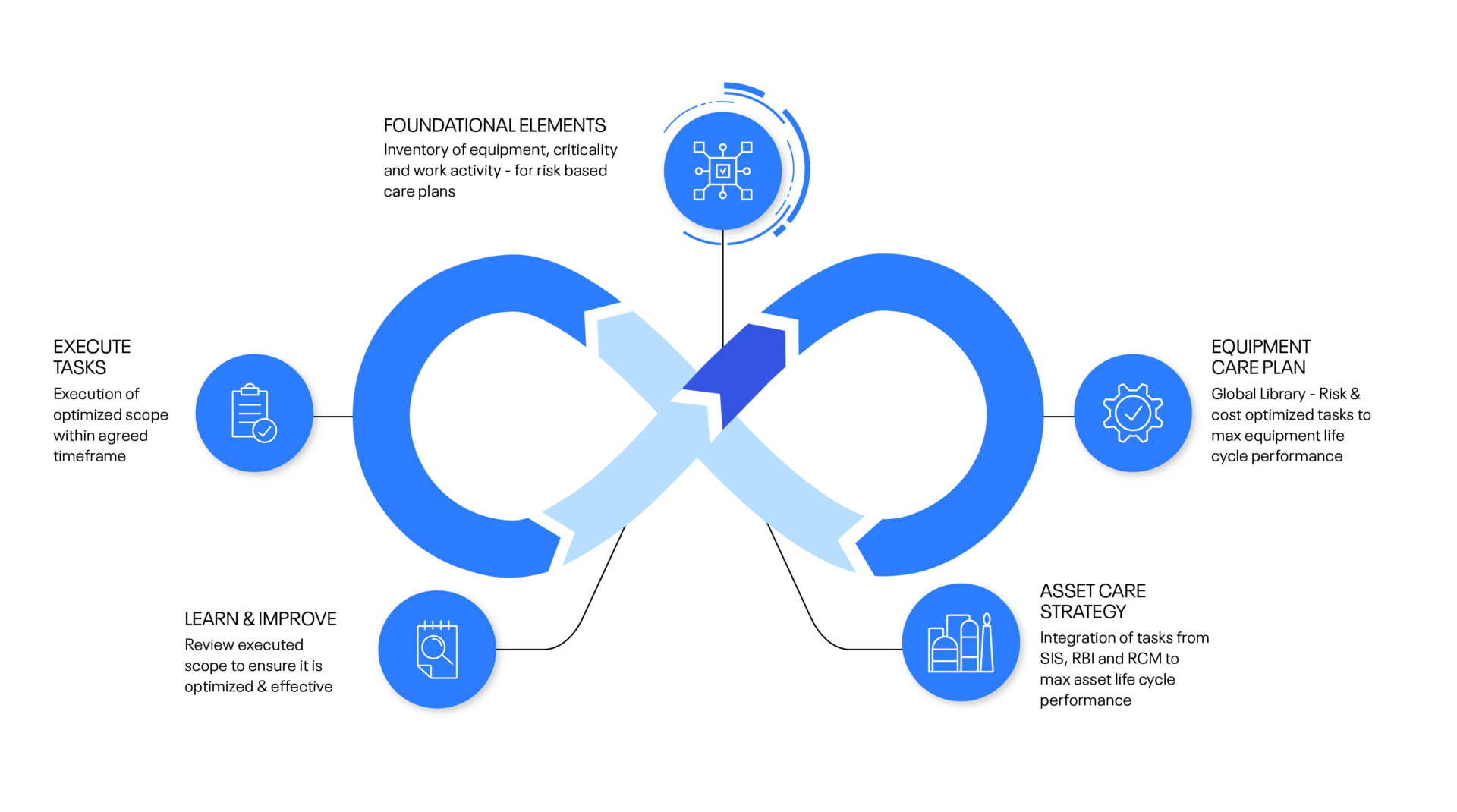
The loop starts with foundational elements – such as engineering data, construction materials, start date, process conditions, material, and RBI data – which are used to develop an equipment care plan determining the frequency and extent of the inspection.
In the asset care strategy phase, you will work on optimization of the plan by analyzing data from different disciplines for that equipment and the affected and affecting equipment.
In the next phase, you will execute the optimized plan and collect data from various sources like IOWs, wall thickness measurement, visual inspection, non-destructive testing, etc…
The cycle continues through a learning and improving phase, during which you will do the analysis of the collected data via KPIs, anomaly analysis, and root cause analysis to evaluate the state of the equipment and improve the foundational elements. And then the loop starts again.
Unlock the power of Corrosion Data through IMS Software
As we have seen by now, it is important to maintain good corrosion data throughout the complete process of asset integrity management to ensure effective corrosion trending and data crunching for any kind of age-related degradation. But the data that is not processed and analyzed is not useful as it cannot help decision making. The use of technology, such as digital checklists, can help with inputting data in a structured format, making it easier to manage, visualize and analyze for corrosion studies and degradation in general.
With IMS, it is possible to develop a corrosion management framework that provides comprehensive management of corrosion data. IMS integrates several kinds of Integrity analysis tools, including a risk-based inspection module and analysis tools like S-IDAP, for visualization and corrosion management. Additionally, IMS provides an interface back to CMMS and Enterprise asset management, making it easier to integrate field data with your existing maintenance systems. By keeping all teams up to date about what is happening with the equipment, you can rely on IMS as a complete asset integrity management tool.
Would you like to check out IMS checklists and Dynamic Forms?
Fill out the form below to get in touch with us and find out more.
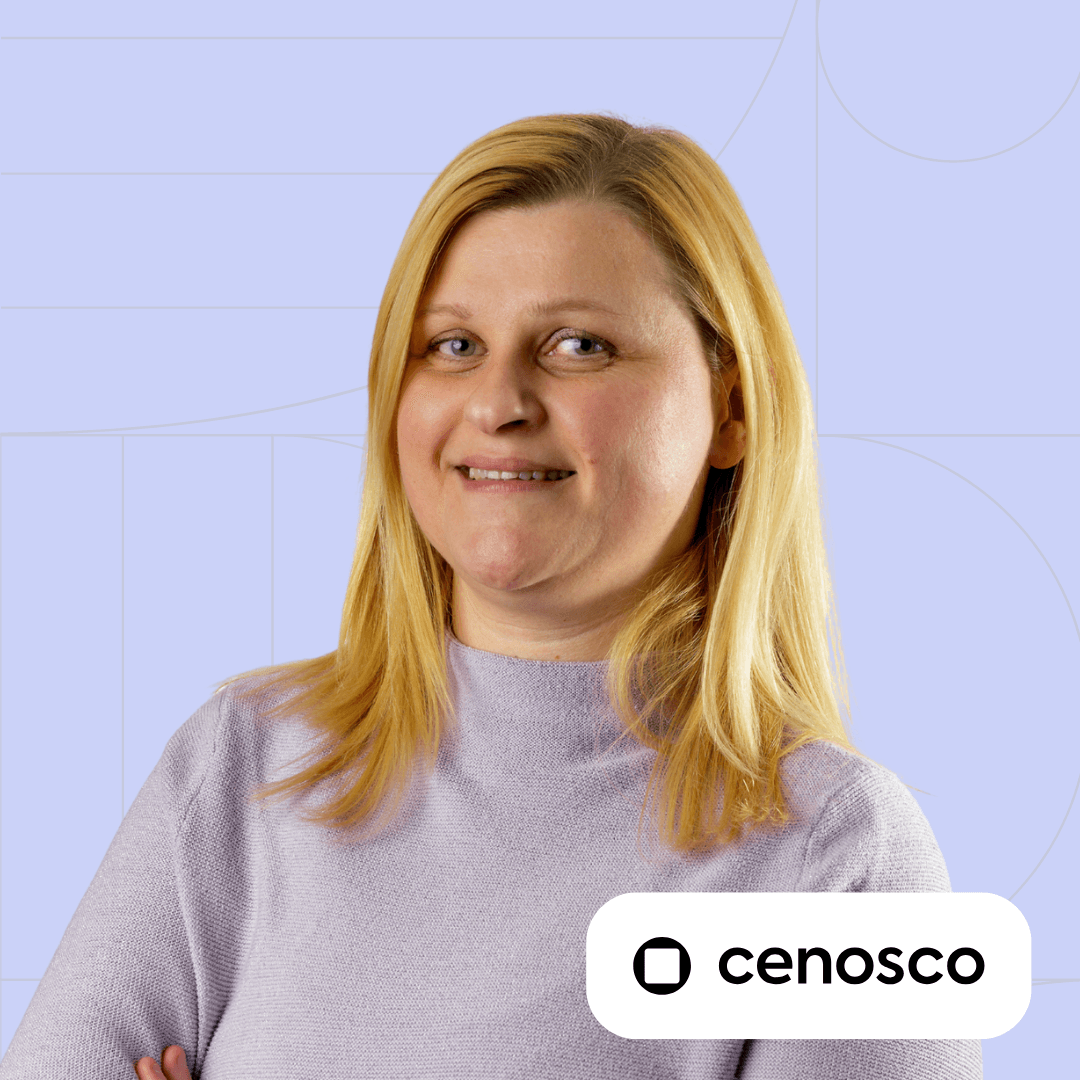
Denis Tkalec Technical writer
Denis Tkalec is a technical writer at Cenosco, specializing in asset integrity management software since 2022. With a background in education and six years in marketing, she turns complex topics into clear, user-friendly content. Inspired by Camus’s belief that “a writer keeps civilization from destroying itself,” she brings precision and care to every manual.