Fitness for Service (FFS) ist nicht nur ein technischer Begriff, sondern eine Lebensader für die Industrie, insbesondere in Sektoren, in denen eine alternde Infrastruktur erhebliche Risiken birgt. Stellen Sie sich eine geschäftige Bohrinsel oder ein ausgedehntes Pipelinesystem vor, bei dem jeder Zentimeter Metall und jede Schweißnaht ständig unter die Lupe genommen wird. Diese Anlagen sind die Adern unserer Wirtschaft, und die Gewährleistung ihrer Integrität ist entscheidend für Sicherheit und Effizienz.
In diesem Blogbeitrag werden wir uns auf eine Reise begeben, um das Wesen von FFS-Bewertungen zu verstehen, wobei wir uns besonders auf Rohrleitungen konzentrieren, die Defekte aufweisen, die zu Materialverlusten führen.
Was ist Diensttauglichkeit?
Im Kern istFitness for Serviceein quantitatives technisches Verfahren zur Bewertung des Zustands in Betrieb befindlicher Industrieanlagen, wie z. B.Pipelines, Druckbehälter und Lagertanks. Das Ziel? Es soll festgestellt werden, ob diese kritischen Komponenten ihre beabsichtigten Funktionen weiterhin sicher und effektiv erfüllen können.
Dieser Prozess beinhaltet eine sorgfältige Bewertung verschiedener Faktoren: Konstruktionsspezifikationen, Materialeigenschaften, Betriebsbedingungen und vorhandene Mängel oder Schäden. Diese umfassende Analyse folgt etablierten Industrienormen wie API 579-1/ASME FFS-1, BS 7910, DNV RP-F101 und ASME B31G, die Methoden zur Bewertung der Eignung von Komponenten während ihres gesamten Lebenszyklus beschreiben.
Die Vorteile von Diensttauglichkeitsbeurteilungen
Die Vorteile der Durchführung von FFS-Bewertungen sind vielfältig:
- Verlängerte Lebensdauer der Anlagen: Durch die Ermittlung des aktuellen Zustands der Geräte können Unternehmen fundierte Entscheidungen treffen, die die Lebensdauer ihrer Anlagen verlängern.
- Kosteneinsparungen: Genaue Bewertungen minimieren unnötige Reparaturen und Ersatzbeschaffungen, was zu erheblichen Einsparungen bei den Wartungskosten führt.
- Erhöhte Sicherheit: Regelmäßige Bewertungen gewährleisten den sicheren Betrieb der Geräte und verringern das Risiko von Ausfällen, die eine Gefahr für Personal und Umwelt darstellen könnten.
- Verbesserte Zuverlässigkeit: Die Aufrechterhaltung der mechanischen Integrität stellt sicher, dass kritische Systeme zuverlässig funktionieren, was für die betriebliche Effizienz unerlässlich ist.
- Optimierte Wartungsplanung: Die Erkenntnisse aus den FFS-Bewertungen fließen in die Wartungspläne ein und verhindern ungeplante Ausfallzeiten.
- Einhaltung gesetzlicher Vorschriften: Die Einhaltung von Industriestandards durch FFS-Bewertungen verringert die rechtliche Haftung und erhöht die betriebliche Glaubwürdigkeit.
Fundierte Entscheidungsfindung: Ein strukturierter Rahmen für die Bewertung des Anlagenzustands ermöglicht bessere Entscheidungen über Reparaturen oder den weiteren Betrieb.
Überblick über die FFS-Bewertungsebenen
Die Norm API 579-1/ASME FFS-1 sieht drei Bewertungsstufen vor:
- Stufe 1-Bewertungen (FFS1): Diese unkomplizierten Bewertungen verwenden Methoden wie B31G und DNV RP-F101, um auf der Grundlage minimaler Daten schnelle Erkenntnisse zu gewinnen. Sie sind zwar kostengünstig, können aber kritische Variablen übersehen.
- Stufe-2-Bewertungen (FFS2): Hier kommen komplexere Analysen ins Spiel, bei denen die ursprünglichen Signaldaten und nicht nur die Fehlermessungen verwendet werden. Stufe-2-Bewertungen verfeinern die Analyse, indem sie zusätzliche Parameter berücksichtigen, wenn Stufe 1 auf mögliche Probleme hinweist.
- Stufe 3-Bewertungen (FFS3): Durch den Einsatz fortschrittlicher Techniken wie der Finite-Elemente-Analyse (FEA) bietet diese Stufe umfassende Einblicke in den Zustand der Anlagen, indem komplexe Wechselwirkungen und Spannungsverteilungen berücksichtigt werden.
Der Zweck der FFS-Bewertung von Pipelines
Das Hauptziel von Gebrauchstauglichkeitsuntersuchungen ist einfach, aber entscheidend: Es soll festgestellt werden, ob ein Bauteil mit vorhandenen Mängeln noch für den weiteren Betrieb geeignet ist. Für Rohrleitungen bedeutet dies, dass sichergestellt werden muss, dass der sichere Betriebsdruck (PSW) den maximal zulässigen Betriebsdruck (MAOP) übersteigt.
Die FFS beantwortet auch die Frage, wie lange sie einsatzfähig bleiben wird. Die Bewertung umfasst auch die Berechnung der Korrosionstoleranz und die Bestimmung, wie viel Korrosion auftreten kann, ohne die strukturelle Integrität zu beeinträchtigen. Diese Bewertung sichert nicht nur den Betrieb, sondern hilft auch bei der Vorhersage der verbleibenden Lebensdauer einer Pipeline. Mit diesen Informationen und der Hilfe der risikobasierten Bewertung können wir den Termin für die nächste Inspektion berechnen.
Berechnung des sicheren Betriebsdrucks einer Pipeline
Der sichere Betriebsdruck (Safe Working Pressure,PSW) ist eine Messgröße, die den maximalen Druck definiert, den eine Pipeline während des normalen Betriebs sicher bewältigen kann. DerPSW muss immer über dem maximal zulässigen Betriebsdruck (MAOP) liegen, d. h. dem höchsten Druck, bei dem eine Pipeline betrieben werden kann, ohne dass ein Ausfall oder eine Beschädigung droht.
Verständnis von Ringspannung und Auslegungsdruck
Lassen Sie uns nun tiefer in die Mechanik eintauchen. Stellen Sie sich die inneren Kräfte vor, die wirken, wenn Flüssigkeiten durch die Rohrleitung strömen. Hier kommt dieRingspannungins Spiel - ein stiller Wächter, der das Rohr umhüllt und seiner natürlichen Tendenz, unter Druck zu bersten, entgegenwirkt.
Ingenieure untersuchen die Ringspannung, um festzustellen, wie viel Innendruck ein Rohr aushalten kann. Das ist so, als ob man die Festigkeit einer Brücke prüft, bevor man sie für den Schwerlastverkehr freigibt. Die Formel hinter dieser Bewertung ist die Barlowsche Gleichung, mit der Ingenieure die Ringspannung auf der Grundlage von Innendruck, Rohrdurchmesser und Wandstärke berechnen können.
σh=P(D-t)/2t
Wo:
- σh= Umschlingungsspannung
- P= Innendruck
- D= Durchmesser des Rohrs
- t= Wandstärke des Rohrs
Aus der Ringspannung ergibt sich ein weiteres wichtiges Konzept: derAuslegungsdruck. Dieser Parameter gibt den maximalen Druck an, den eine Pipeline sicher bewältigen kann, wobei die erforderlichen Sicherheitsmargen berücksichtigt werden. Ingenieure berücksichtigen Faktoren wie Wandstärke und Materialfestigkeit, um sicherzustellen, dass Pipelines für Drücke ausgelegt sind, die weit über dem liegen, was sie unter realen Bedingungen aushalten müssen. Das ist proaktives Engineering vom Feinsten - die Verhinderung potenzieller Ausfälle, bevor sie auftreten.
Materialeigenschaften und Versagensmechanismen
Um wirklich zu verstehen, wie sich Pipelines unter Belastung verhalten, müssen wir ihre Materialeigenschaften und potenziellen Versagensmechanismen untersuchen. Hier veranschaulicht die Spannungs-Dehnungs-Kurve, wie Materialien auf einwirkende Kräfte reagieren.
- Streckgrenze (σy)stellt die maximale Spannung dar, die ein Material ertragen kann, während es nach der Entlastung immer noch in seine ursprüngliche Form zurückkehrt.
- Höchstzugkraft (σUTS)gibt die maximale Spannung an, bevor ein Material zu versagen beginnt.
Ein Versagen tritt typischerweise zwischen diesen Schwellenwerten auf und markiert den Übergang von elastischem Verhalten - bei dem die Materialien zurückfedern können - zu plastischer Verformung, bei der dauerhafte Veränderungen auftreten.
Bewertung der Versagensbedingungen
In der Praxis tritt das Versagen einer Rohrleitung ein, wenn die Ringspannung einen kritischen Schwellenwert erreicht, der alsFließspannung(σflow) bezeichnet wird. Dieser Punkt bedeutet, dass die Rohrleitung ihre strukturelle Integrität unter Druck nicht mehr aufrechterhalten kann. Ingenieure analysieren diese Bedingungen, um Grunderwartungen für die Materialleistung unter idealen Bedingungen festzulegen.
Wenn Korrosion ins Spiel kommt, wird es noch schwieriger. Die Ingenieure müssen alle Defekte bewerten, die die strukturelle Integrität beeinträchtigen könnten.
Wenn unsere Rohrleitung beispielsweise einen Defekt aufweist, der durch eine bestimmte Länge (L) und Tiefe (d) gekennzeichnet ist, können wir die Fläche des Defekts wie folgt berechnen:
A0= L x t
Wo:
- A0= Fläche des Fehlers
- t = Wandstärke des Rohrs
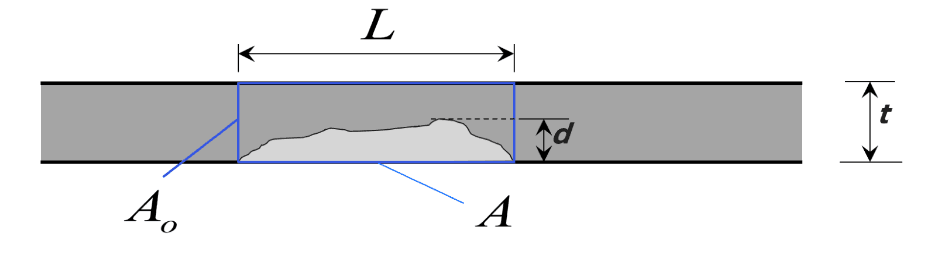
Um den Versagensdruck des korrodierten Rohrs zu bestimmen, gehen wir vom Versagensdruck eines unbeschädigten Rohrs aus und wenden einen Faktor an, den so genanntenRestfestigkeitsfaktor (RSF), der die Auswirkungen der Korrosion berücksichtigt:
RSF = (1 - A / A0) / 1 - (A / A0 x 1 / M)
Wo:
- A = Von Korrosion betroffene Fläche
- M = Beulfaktor, der die Auswirkungen des Innendrucks auf die strukturelle Integrität eines Rohrs mit Defekten berücksichtigt.
Der Versagensdruck (Pfailure) einer korrodierten Rohrleitung kann dann ausgedrückt werden als Versagensdruck eines unbeschädigten Rohrs mal Restfestigkeitsfaktor (RSF) aufgrund von Korrosion:
Ausfall = 2tσflow / (D - t) x RSF
Oder
Ausfall = 2tσflow / (D - t) x ((1 - A / A0) / 1 - (A / A0 x 1 / M))
Diese Gleichung dient als universelle Methode zur Berechnung sicherer Arbeitsdrücke in verschiedenen Rohrleitungs- und FFS-Bewertungscodes.
Wo:
- σflow= Fließspannung (die Spannung, bei der das Versagen auftritt)
- D = Durchmesser des Rohrs
Indem sie das Ausmaß der Korrosion und ihre Auswirkungen auf die Drucktoleranz bewerten, bestimmen sie, wie viel Druck ein korrodiertes Rohr sicher aushalten kann - und gewährleisten so eine genaue Bewertung auch unter weniger idealen Bedingungen.
Sichere Grenzen setzen: Sicherer Arbeitsdruck
Dersichere Betriebsdruck (PSW)ergibt sich aus diesen Bewertungen als eine wesentliche Richtlinie für Betriebsgrenzen. Er kann nach der folgenden Formel berechnet werden:
PSW = f x 2tσflow / (D - t) x RSF
oder
PSW = f x 2tσflow / (D - t) x ((1 - A / A0) / 1 - (A / A0 x 1 / M))
Wo:
f = Bemessungsfaktor oder Sicherheitsfaktor, der Unsicherheiten bei den Materialeigenschaften und den Betriebsbedingungen berücksichtigt.
Der Reparatur-Faktor: ERF navigieren
Sobald wir den sicheren Betriebsdruck ermittelt haben, berechnen wir anhand der Inspektionsergebnisse einengeschätzten Reparaturfaktor (ERF). ERF ist definiert als:
ERF = MAOP xPSW
Dieser Faktor hilft bei der Entscheidung, ob Korrekturmaßnahmen erforderlich sind:
- Wenn der ERF kleiner als 1 ist, bedeutet dies, dass der MAOP unter dem sicheren Arbeitsdruck liegt, so dass der Betrieb sicher fortgesetzt werden kann.
- Überschreitet der ERF hingegen den Wert 1, signalisiert er, dass sofortige Maßnahmen erforderlich sind, z. B. Reparaturen oder Anpassungen der Betriebsgrenzen.
Wenn beispielsweise bei einer Inspektion zu einem bestimmten Zeitpunkt ein ERF von 0,8 festgestellt wird, spätere Bewertungen jedoch einen Anstieg auf über 1 ergeben, zeigt dies, dass ein sofortiges Eingreifen erforderlich ist, um die Sicherheit zu gewährleisten.
Methode zur Bewertung von Mängeln
Um die Gebrauchstauglichkeit der Rohrleitung zu beurteilen, müssen wir die Mängel bewerten, um die Korrosionstoleranz zu bestimmen. Auf dieser Grundlage können wir dann die verbleibende Lebensdauer des Rohrs und den nächsten Inspektionstermin berechnen. In diesem Bereich dominieren zwei Hauptmethoden:ASME B31GundDNV RP-F101.
ASME B31Gwar die erste Norm, die sich der Herausforderung stellte, den sicheren Betriebsdruck bei Vorhandensein von Fehlern zu berechnen. Sie enthält die ursprüngliche Norm, die die Fließspannung als das 1,1-fache der spezifizierten Mindeststreckgrenze (SMYS) definiert, und eine modifizierte Version, die diese auf SMYS plus zusätzliche 69 MPa (etwa 10 KSI) für eine größere Genauigkeit verfeinert.
Andererseits konzentriert sich die 2010 eingeführteDNV RP-F101 auf die Zugfestigkeit (UTS) und sagt ein Versagen beim 0,9-fachen der UTS voraus. Diese Norm vereinfacht die Fehlerformen, indem sie sie als rechteckig behandelt, während ASME B31G die Fehler ursprünglich als parabolisch annäherte, später aber beliebige Formen zuließ.
Ein weiterer kritischer Aspekt ist derAusbeulfaktor, der angibt, wie sich Defekte unter Druck verformen. Kleinere Defekte vermindern seine Bedeutung, während größere ihn verstärken.
Zur Veranschaulichung des sicheren Arbeitsdrucks verwenden beide Normen dasFehlerbewertungsdiagramm (FAD), das die Gleichung für den sicheren Arbeitsdruck (PSW = f x 2tσflow / (D - t) x ((1 - A / A0) / 1 - (A / A0 x 1 / M)) in ein grafisches Format überträgt, in dem die Defektlänge gegen die Tiefe aufgetragen wird. Punkte unterhalb der Kurve zeigen sichere Bedingungen an, während Punkte oberhalb der Kurve potenzielle Ausfallrisiken signalisieren.
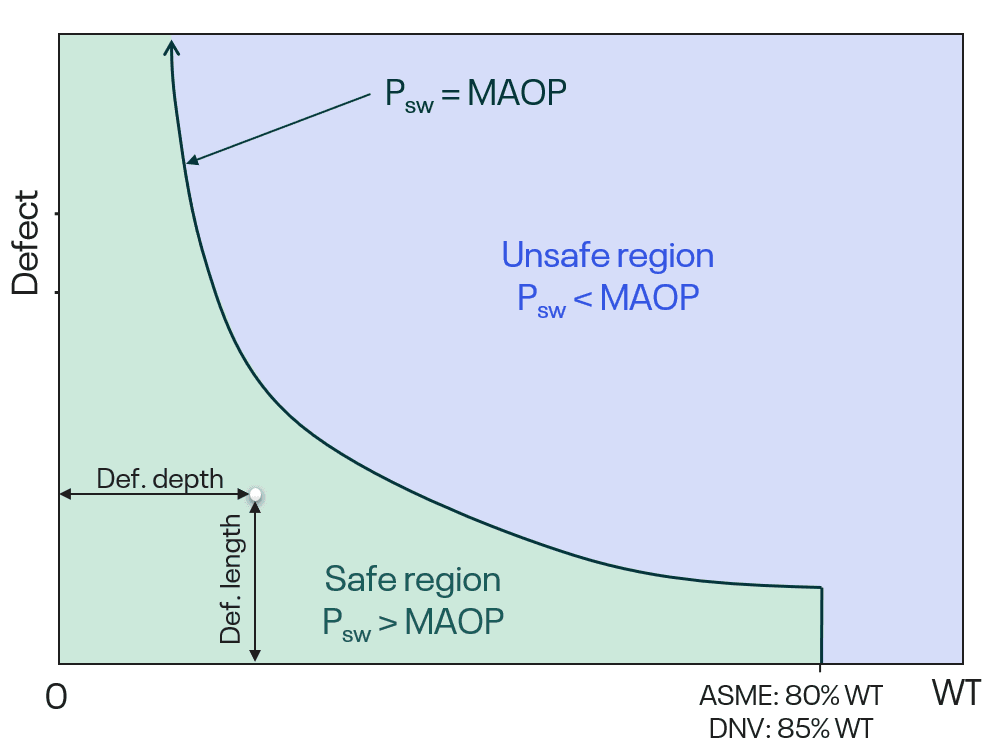
Bei der Bewertung von Mängeln aus In-Line-Inspektionsberichten (ILI) ist es wichtig, die maximal zulässige Tiefe zu berücksichtigen - 80 % der Wanddicke (WT) für ASME und 85 % für DNV. Ein Überschreiten dieser Schwellenwerte macht die Defekte unsicher.
Regeln für das Zusammenwirken von Defekten
In der Welt der Pipelines stehen Mängel selten allein. Sie treten oft zusammen auf und bilden ein komplexes Netz potenzieller Schwachstellen. ASME B31G bewertet die Defekte einzeln, erkennt aber an, dass eng beieinander liegende Defekte als ein einziger größerer Defekt zusammenwirken können, wenn sie innerhalb der dreifachen Nennwanddicke (3t) liegen. Diese Wechselwirkung kann die strukturelle Integrität erheblich beeinträchtigen.
Im Gegensatz dazu bewertet DNV RP-F101 jeden Fehler einzeln und berücksichtigt Kombinationen von benachbarten, zusammenwirkenden Fehlern. Von einer Wechselwirkung wird ausgegangen, wenn der axiale Abstand zwischen den Fehlern kleiner ist als ein bestimmter Schwellenwert, der auf dem Rohrdurchmesser und der Wandstärke basiert. Dieses Kriterium hilft zu erkennen, welche Fehler sich gegenseitig beeinflussen können.
Die DNV RP-F101-Methode umfasst einen strukturierten dreistufigen Prozess:
- Unterteilung der Rohrleitung: Die Rohrleitung wird anhand der Formel√(D/t), wobeiDder Durchmesser undtdie Wanddicke ist, in Umfangsabschnitte unterteilt. Diese Unterteilung ermöglicht eine strukturierte Vorgehensweise bei der Analyse von Defekten.
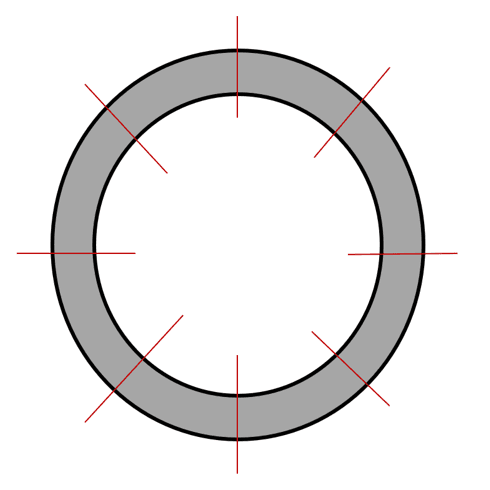
- Projizieren von Defekten: Für jede Projektionslinie, die diesen Abschnitten entspricht, werden Defekte aus benachbarten Abschnitten auf die Linien abgebildet. Befindet sich beispielsweise ein Defekt im ersten Abschnitt, wird er sowohl auf die erste als auch auf die zweite Linie projiziert. Wenn es in der zweiten Sektion Fehler gibt, werden diese auf die zweite und dritte Linie abgebildet. In der DNV RP-F101 2010 wirken auch überlappende innere und äußere Fehler zusammen. Die resultierende Tiefe für die Kombination ist di=d1+d2.
- Berechnung des sicheren Betriebsdrucks: Der Psw wird für alle möglichen Kombinationen dieser interagierenden Fehler berechnet. Der niedrigste Psw aus diesen Berechnungen wird zum sicheren Betriebsdruck für das korrodierte Rohr.
In der Version 2010 der DNV RP-F101 wurden sich überlappende Fehler als ein einziger Fehler mit einer kombinierten Länge vom Beginn des ersten Fehlers bis zum Ende des letzten Fehlers im Cluster behandelt, wobei die Tiefe des tiefsten Fehlers innerhalb dieses Clusters verwendet wurde. In der Aktualisierung von 2015 werden überlappende Defekte jedoch nicht zu einem einzigen Defekt zusammengefasst; stattdessen werden ihre individuellen Beiträge bei der Berechnung des sicheren Betriebsdrucks separat berücksichtigt.
Verständnis der Korrosionstoleranz
Wenn wir uns eingehender mit der Bewertung der Integrität von Pipelines befassen, stoßen wir auf das Konzept derKorrosionstoleranz - diemaximal zulässige Korrosion, die eine Pipeline aushalten kann, während sie noch als betriebsfähig gilt. Dieses Konzept ist mit demGrenzzustand verflochten, der definiert, wann eine Pipeline für den Betrieb unsicher wird.
Berechnung der Korrosionstoleranz in Fällen ohne Defekte
Wenn eine Pipeline frei von Defekten ist, müssen die Betreiber potenzielle Korrosionsarten vorhersehen, sei es allgemeine Korrosion, Rillenbildung oder Lochfraß. Wenn zum BeispielLochfraßerwartet wird, können Ingenieure die potenzielle Fehlerlänge auf das 20-fache der Korrosionstiefe schätzen. Diese Beziehung ermöglicht es ihnen, auf der Grundlage dieses Verhältnisses von Länge zu Tiefe eine Linie im Diagramm zur Fehlerbewertung vom Ursprung (0,0) aus zu zeichnen. Der Schnittpunkt dieser Linie mit der Sicherheitskurve zeigt die Korrosionstoleranz (CT) und die minimal zulässige Dicke (MAT) - auf dem nächsten Bild sind CT und MAT für die Rillenkorrosion angegeben.
Wird dagegen von allgemeiner Korrosion ausgegangen, kann ihre Länge mit dem 1.000-fachen der Wanddicke (WT) angegeben werden. Diese Methode führt in der Regel zu einer geringeren Korrosionstoleranz, da Lochfraß zu einem tieferen Materialverlust führen kann als allgemeine Korrosion. Daher ist die genaue Bestimmung der zu erwartenden Korrosionsart entscheidend für die Festlegung angemessener Toleranzen.
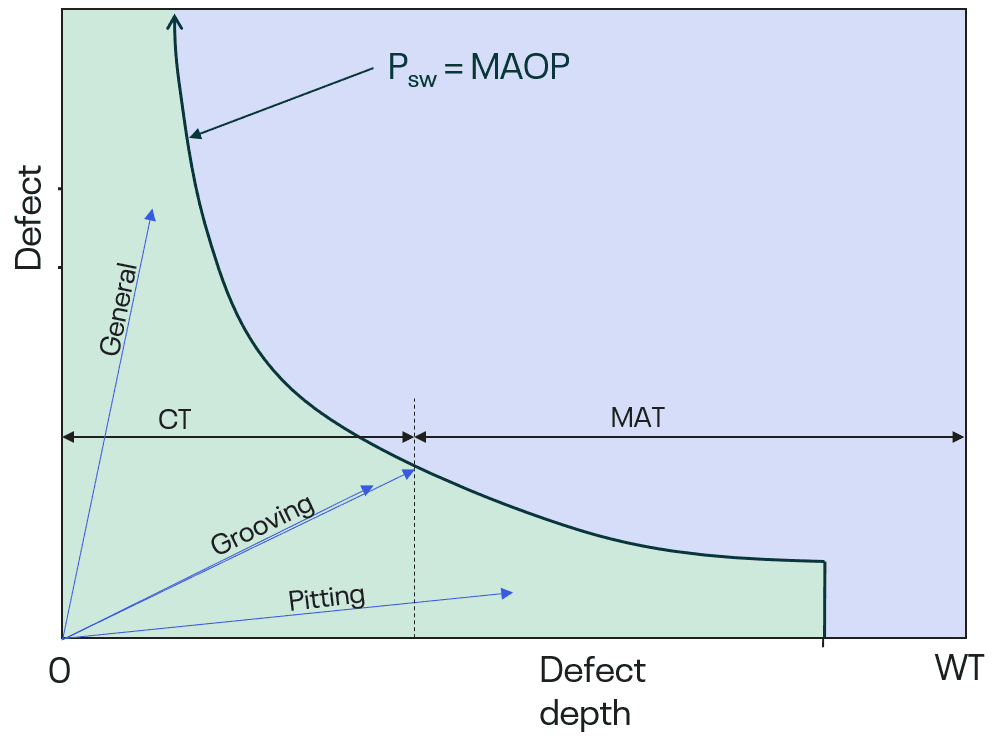
Berechnung der Korrosionstoleranz in Fällen mit Defekten
Bei Vorhandensein von Mängeln wird die Bewertung differenzierter. Die Bediener können auf dem Fehlerbewertungsdiagramm Linien von (0,0) durch jeden Fehler ziehen, um die jeweiligen Toleranzen zu ermitteln. Der Abstand zwischen dem Schnittpunkt dieser Linien mit der Sicherheitskurve und dem Punkt, an dem der Fehler auf die x-Achse trifft, gibt die Korrosionstoleranzen (CT) zum Zeitpunkt der In-Line-Inspektion (ILI) an.
Die Korrosionstoleranz (CT) wird für jeden Fehler berechnet. BeiASME B31G ist diese Bewertung einfach; jeder Fehler wird einer einzigen Berechnung unterzogen.DNV RP-F101verkompliziert die Angelegenheit jedoch durch seinen iterativen Prozess - Defekte können mehrfach bewertet werden, wenn sie sich gegenseitig beeinflussen. Diese Komplexität wird besonders deutlich, wenn man mit großen Datensätzen arbeitet.
Das Zusammenspiel von Defekten
Wenn zwei Defekte nahe genug beieinander liegen, um sich gegenseitig zu beeinflussen, haben sie aufgrund ihrer kombinierten Auswirkungen auf die Integrität der Pipeline eine gemeinsame Korrosionstoleranz (CT). Diese Wechselwirkung muss sorgfältig bewertet werden, um sicherzustellen, dass die Berechnungen des sicheren Betriebsdrucks (Psw) gültig bleiben und die Pipeline weiterhin sicher betrieben werden kann.
Bestimmung der Lebensdauer von Rohrleitungen und nächste Schritte zur Inspektion
Wie bereits zu Beginn dieses Artikels erwähnt, wird bei der Bewertung der Gebrauchstauglichkeit nicht nur festgestellt, ob eine Pipeline für den Betrieb geeignet ist, sondern auch abgeschätzt, wie lange sie noch sicher funktionieren kann. Sobald wir unsere Korrosionstoleranz (CT) mit Hilfe der Ausfallbewertungskurve berechnet haben, können wir die verbleibende Lebensdauer der Pipeline abschätzen und berechnen, wann die Pipeline erneut inspiziert werden muss.
- Um die verbleibende Lebensdauer zu ermitteln, wird die Korrosionstoleranz (CT) durch die Korrosionsrate (CR) geteilt. Wenn eine Rohrleitung zum Beispiel eine Korrosionstoleranz von 2 mm und eine Korrosionsrate von 0,1 mm pro Jahr hat, sieht die Berechnung wie folgt aus:
Verbleibende Lebensdauer = CT / CR = 2 mm / 0,1 mm Jahr = 20 Jahre
Das bedeutet, dass die Pipeline unter den derzeitigen Bedingungen weitere 20 Jahre sicher betrieben werden kann, bevor sie ihre Korrosionsgrenze erreicht.
- Um zu bestimmen, wann die nächste Inspektion stattfinden soll, benötigen wir den Intervallfaktor (IF), der aus einerrisikobasierten Bewertung (RBA) abgeleitet wird, bei der die Kritikalität und die möglichen Folgen von Fehlern bewertet werden. Die Formel zur Berechnung des nächsten Inspektionsintervalls lautet:
Nächstes Inspektionsintervall = verbleibende Lebensdauer × IF
Wenn wir in unserem vorherigen Beispiel von einem internen Faktor von 0,3 ausgehen, würde die Berechnung folgendermaßen aussehen:
Nächstes Inspektionsintervall = 20 Jahre × 0,3 = 6 Jahre
Dies bedeutet, dass die Pipeline in 6 Jahren erneut inspiziert werden sollte, um sicherzustellen, dass sie für den Betrieb geeignet bleibt.
Bewertung der Gebrauchstauglichkeit von Pipelines mit IMS PLSS
Im Pipeline-Management sind Bewertungen der Gebrauchstauglichkeit (Fitness for Service, FFS) von entscheidender Bedeutung, um die Sicherheit und den weiteren Betrieb alternder Infrastrukturen zu gewährleisten. Diese Bewertungen bestimmen nicht nur, ob eine Pipeline in Betrieb bleiben kann, sondern geben auch Aufschluss über ihre verbleibende Lebensdauer.
Die Datenanalyse wird zum Herzstück dieses Prozesses und hilft den Betreibern, die Leistung vorherzusagen und Inspektionen auf der Grundlage der berechneten Restlebensdauer zu planen. Das IMS - Pipeline and Subsea Systems (PLSS) von Cenoco ermöglicht Betreibern die Bewertung der Eignung von Pipelines und bietet Einblicke in die verbleibende Lebensdauer. Mithilfe von Methoden wie ASME B31G und DNV RP-F101 können Betreiber Defekte genau bewerten und Korrosionstoleranzen berechnen. Die Analyse der Beziehung zwischen Defekten, Ringspannung und sicherem Betriebsdruck unterstützt ein proaktives Pipeline-Management.
PLSS ermöglicht den Benutzern die Bewertung von ILI-Daten durch das Fitness-for-Service-Modul, das den sicheren Betriebsdruck und den geschätzten Reparaturfaktor für jeden Defekt anzeigt. Die Stärke des Moduls liegt in der Berechnung der Korrosionstoleranz für einzelne oder gruppierte Defekte, wobei Materialqualität, Defektgröße und -tiefe berücksichtigt werden. Das Modul zur risikobasierten Bewertung berechnet die verbleibende Lebensdauer der Pipeline und das Datum der nächsten Inspektion, mit der Option, Inspektionsergebnisse in der Zustandshistorie zu planen und zu protokollieren. Das System unterstützt die Bewertung der Gebrauchstauglichkeit von Pipelines, Fließleitungen und Verbindungsstücken aus Kohlenstoffstahl und korrosionsbeständigen Legierungen.
PLSS befasst sich mit den häufigsten Defekten von in Betrieb befindlichen Pipelines, insbesondere mit volumetrischer Korrosion, die zu einem Kunststoffkollaps führen kann. Es konzentriert sich auf wesentliche und dennoch einfache Bewertungen der Stufe 1, wie ASME B31G und DNV RP-F101 Teil B. Dieser rationalisierte Ansatz ermöglicht es den Betreibern, wirtschaftlichen Überlegungen Vorrang zu geben. Eine detailliertere Bewertung außerhalb von PLSS wird für hochkritische Pipelines oder Pipelines, die strengen Vorschriften unterliegen, empfohlen.
Zusammenfassend lässt sich sagen, dass PLSS für die Bewältigung bekannter, kontrollierter Bedingungen mit volumetrischen Korrosionsdefekten unter Umfangsdruckbelastung sehr effektiv ist.
Möchten Sie mehr über IMS erfahren?
Fordern Sie unten eine Demo an, um sich einen Eindruck von den Möglichkeiten zu verschaffen!
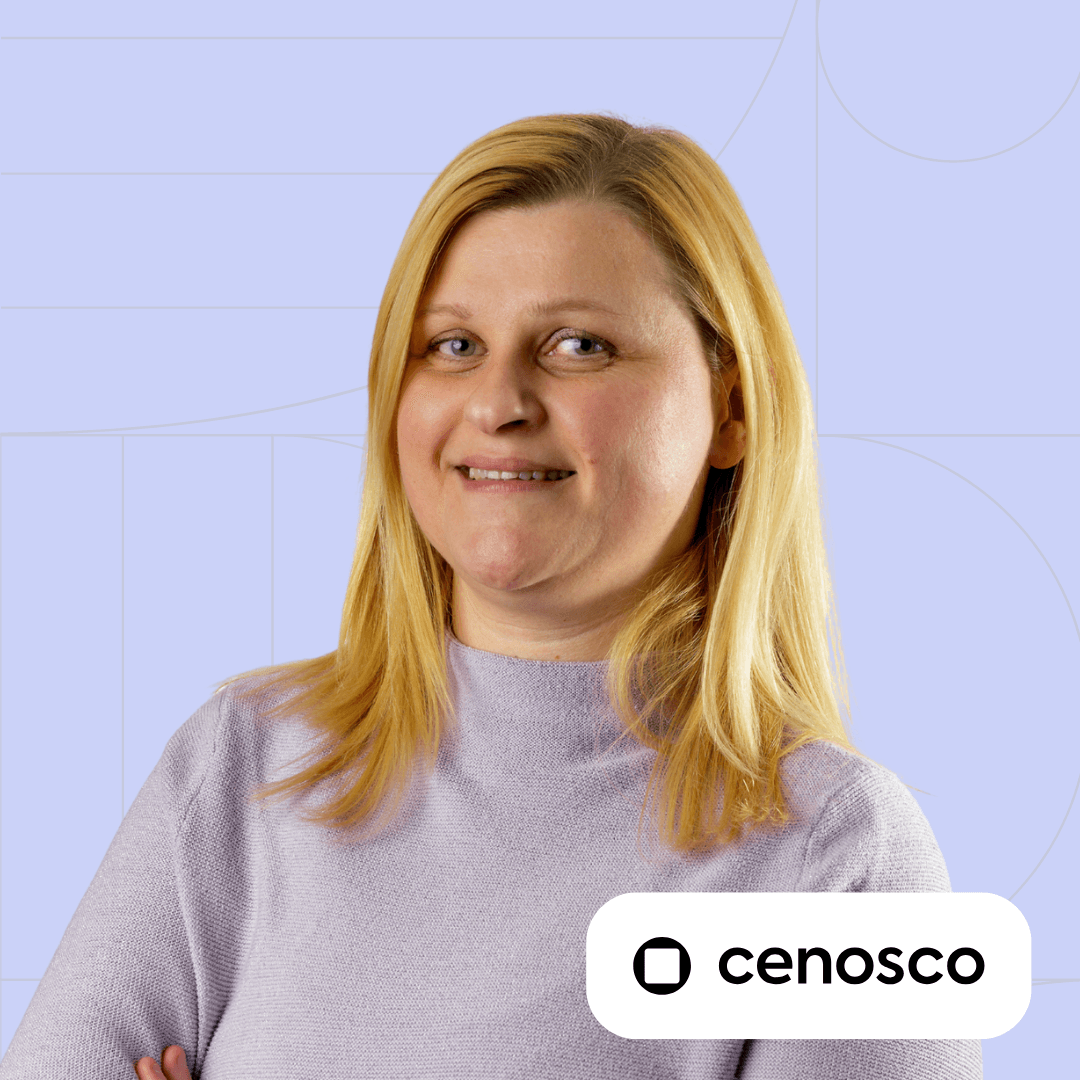
Denis Tkalec Technical writer
Denis Tkalec is a technical writer at Cenosco, specializing in asset integrity management software since 2022. With a background in education and six years in marketing, she turns complex topics into clear, user-friendly content. Inspired by Camus’s belief that “a writer keeps civilization from destroying itself,” she brings precision and care to every manual.