Fitness for Service (FFS) is not just a technical term; it’s a lifeline for the industrial world, particularly in sectors where aging infrastructure poses significant risks. Imagine a bustling oil rig or a sprawling pipeline system where every inch of metal and weld is constantly scrutinized. These assets are the veins of our economy, and ensuring their integrity is crucial for safety and efficiency.
In this blog post, we will embark on a journey to understand the essence of FFS assessments, focusing particularly on pipelines that exhibit defects that result in material loss.
What is Fitness for Service?
At its core, Fitness for Service is a quantitative engineering method designed to evaluate the condition of in-service industrial assets—think pipelines, pressure vessels, and storage tanks. The goal? To determine if these critical components can continue to perform their intended functions safely and effectively.
This process involves meticulously assessing several factors: design specifications, material properties, operating conditions, and any existing flaws or damage. This comprehensive analysis adheres to established industry standards such as API 579-1/ASME FFS-1, BS 7910, DNV RP-F101, and ASME B31G, which outline methodologies for evaluating component fitness throughout their lifecycle.
The Benefits of Fitness for Service Assessments
The advantages of conducting FFS assessments are manifold:
- Extended Asset Life: By identifying the current condition of equipment, organizations can make informed decisions that prolong the operational life of their assets.
- Cost Savings: Accurate assessments minimize unnecessary repairs and replacements, leading to significant savings in maintenance costs.
- Enhanced Safety: Regular evaluations ensure equipment operates safely, reducing the risk of failures that could endanger personnel and the environment.
- Improved Reliability: Maintaining mechanical integrity ensures that critical systems function reliably, which is essential for operational efficiency.
- Optimized Maintenance Planning: Insights from FFS assessments inform maintenance schedules, preventing unplanned downtime.
- Regulatory Compliance: Adhering to industry standards through FFS assessments reduces legal liabilities and enhances operational credibility.
Informed Decision-Making: A structured framework for evaluating asset conditions enables better decisions regarding repairs or continued operation.
Overview of FFS Assessment Levels
The API 579-1/ASME FFS-1 standard outlines three levels of assessment:
- Level 1 Assessments (FFS1): These straightforward evaluations use methods like B31G and DNV RP-F101 to provide quick insights based on minimal data. While cost-effective, they may overlook critical variables.
- Level 2 Assessments (FFS2): More complex analyses come into play here, utilizing original signal data rather than just defect measurements. Level 2 assessments refine the analysis by considering additional parameters when Level 1 indicates potential issues.
- Level 3 Assessments (FFS3): Employing advanced techniques like Finite Element Analysis (FEA), this level offers comprehensive insights into asset conditions by accounting for complex interactions and stress distributions.
The Purpose of FFS Assessment of Pipelines
The primary aim of Fitness for Service assessments is straightforward yet vital: to evaluate whether a component with existing defects is still fit for continued service. For pipelines, this means ensuring that the Safe Working Pressure (PSW) exceeds the Maximum Allowable Operating Pressure (MAOP).
FFS also answers the question of how long it will remain fit for service. The evaluation also includes calculating corrosion tolerance and determining how much corrosion can occur without compromising structural integrity. This evaluation not only safeguards operations but also helps predict how much life remains in a pipeline. With that information and the help of Risk-Based Assessment, we can calculate the date of the next inspection.
Calculating the Safe Working Pressure of a Pipeline
Safe Working Pressure (PSW) is a metric that defines the maximum pressure a pipeline can safely handle during normal operations. PSW must always exceed the Maximum Allowable Operating Pressure (MAOP), representing the highest pressure at which a pipeline can operate without risking failure or damage.
Understanding Hoop Stress and Design Pressure
Now, let’s dive deeper into the mechanics. Picture the internal forces at play when fluids surge through the pipeline. This is where hoop stress comes into play—a silent guardian, wrapping around the pipe and counteracting its natural tendency to burst under pressure.
Engineers study hoop stress to gauge how much internal pressure a pipe can withstand. It’s like assessing the strength of a bridge before allowing heavy traffic to cross. The formula behind this assessment is Barlow’s Equation, which helps engineers calculate hoop stress based on internal pressure, pipe diameter, and wall thickness.
σh=P(D−t)/2t
Where:
- σh = Hoop stress
- P = Internal pressure
- D = Diameter of the pipe
- t = Wall thickness of the pipe
From hoop stress flows another critical concept: design pressure. This parameter represents the maximum pressure that a pipeline can safely handle, incorporating necessary safety margins. Engineers consider factors like wall thickness and material strength to ensure that pipelines are designed to endure pressures well above what they will face in real-world conditions. It is proactive engineering at its finest—preventing potential failures before they occur.
Material Properties and Failure Mechanisms
To truly grasp how pipelines behave under stress, we must explore their material properties and potential failure mechanisms. Here, the stress-strain curve illustrates how materials respond to applied forces.
- Yield Strength (σy) represents the maximum stress that a material can tolerate while still returning to its original shape after the load is removed.
- Ultimate Tensile Strength (σUTS) indicates the maximum stress before a material begins to fail.
Failure typically occurs between these thresholds, marking a transition from elastic behavior—where materials can spring back—to plastic deformation, where permanent changes take place.
Assessing Failure Conditions
In practical terms, pipeline failure occurs when hoop stress reaches a critical threshold called flow stress (σflow). This point signifies that the pipeline can no longer maintain its structural integrity under pressure. Engineers analyze these conditions to establish baseline expectations for material performance under ideal circumstances.
When corrosion enters the picture, things get trickier. Engineers must assess any defects that could compromise structural integrity.
For example, if our pipeline has a defect characterized by a certain length (L) and depth (d), we can calculate the area of the defect as:
A0 = L x t
Where:
- A0 = Area of the defect
- t = Wall thickness of the pipe
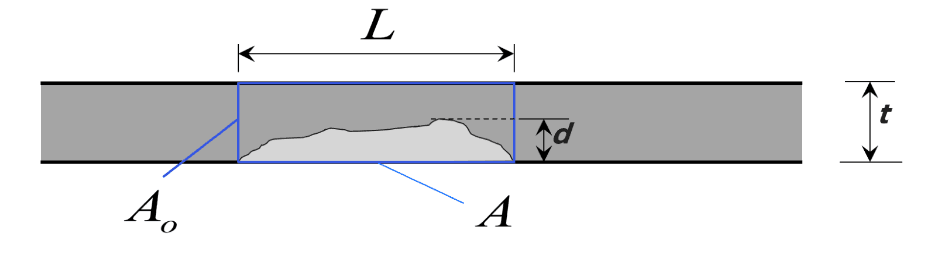
To determine the failure pressure of the corroded pipe, we start with the failure pressure of an undamaged pipe and apply a factor known as the Remaining Strength Factor (RSF), which accounts for the impact of corrosion:
RSF = (1 – A / A0) / 1 – (A / A0 x 1 / M)
Where:
- A = Area affected by corrosion
- M = Bulging factor accounts for the effects of internal pressure on the structural integrity of a pipe with defects.
The failure pressure (Pfailure) of a corroded pipeline can then be expressed as the Failure pressure of undamaged pipe times Remaining Strength Factor (RSF) due to corrosion:
Pfailure = 2tσflow / (D – t) x RSF
Or
Pfailure = 2tσflow / (D – t) x ((1 – A / A0) / 1 – (A / A0 x 1 / M))
This equation serves as a universal method for calculating safe working pressures across various pipeline and FFS assessment codes.
Where:
- σflow = Flow stress (the stress at which failure occurs)
- D = Diameter of the pipe
By evaluating corrosion extent and its impact on pressure tolerance, they determine how much pressure a corroded pipe can safely handle—ensuring accurate evaluations even in less-than-ideal conditions.
Establishing Safe Boundaries: Safe Working Pressure
The Safe Working Pressure (PSW) emerges from these assessments as an essential guideline for operational limits. It can be calculated using the following formula:
PSW = f x 2tσflow / (D – t) x RSF
or
PSW = f x 2tσflow / (D – t) x ((1 – A / A0) / 1 – (A / A0 x 1 / M))
Where:
f = Design factor or safety factor, which accounts for uncertainties in material properties and operating conditions.
The Repair Factor: Navigating ERF
Once we have established safe working pressure, we calculate an Estimated Repair Factor (ERF) based on inspection findings. ERF is defined as:
ERF = MAOP x PSW
This factor helps determine whether corrective actions are necessary:
- If ERF is less than 1, it indicates that MAOP is below safe working pressure—allowing operations to continue safely.
- Conversely, if ERF exceeds 1, it signals that immediate action is required, e.g., repairs or adjustments to operational limits.
For instance, if an inspection reveals an ERF of 0.8 at one point in time but later assessments show an increase beyond 1, it highlights the need for prompt intervention to ensure safety.
Defect Assessment Method
To assess the pipeline’s Fitness for Service, we must evaluate the defects to determine the corrosion tolerance. With this we can then calculate the pipe’s remaining life and next inspection date. Two primary methods dominate this field: ASME B31G and DNV RP-F101.
ASME B31G was the first to tackle the challenge of calculating safe working pressure in the presence of defects. It includes the original standard, which defines flow stress as 1.1 times the specified minimum yield strength (SMYS), and a modified version that refines this to SMYS plus an additional 69 MPa (about 10 KSI) for greater accuracy.
On the other hand, DNV RP-F101, introduced in 2010, focuses on ultimate tensile strength (UTS), predicting failure at 0.9 times UTS. This standard simplifies defect shapes, treating them as rectangular, while ASME B31G originally approximated defects as parabolic but later allowed for arbitrary shapes.
Another critical aspect is the bulging factor, which measures how defects deform under pressure. Smaller defects diminish its significance, while larger ones amplify it.
To visualize safe working pressures, both standards use the Failure Assessment Diagram (FAD), which translates the Safe Working Pressure equation (PSW = f x 2tσflow / (D – t) x ((1 – A / A0) / 1 – (A / A0 x 1 / M))) into a graphical format plotting defect length against depth. Points below the curve indicate safe conditions, while those above signal potential failure risks.
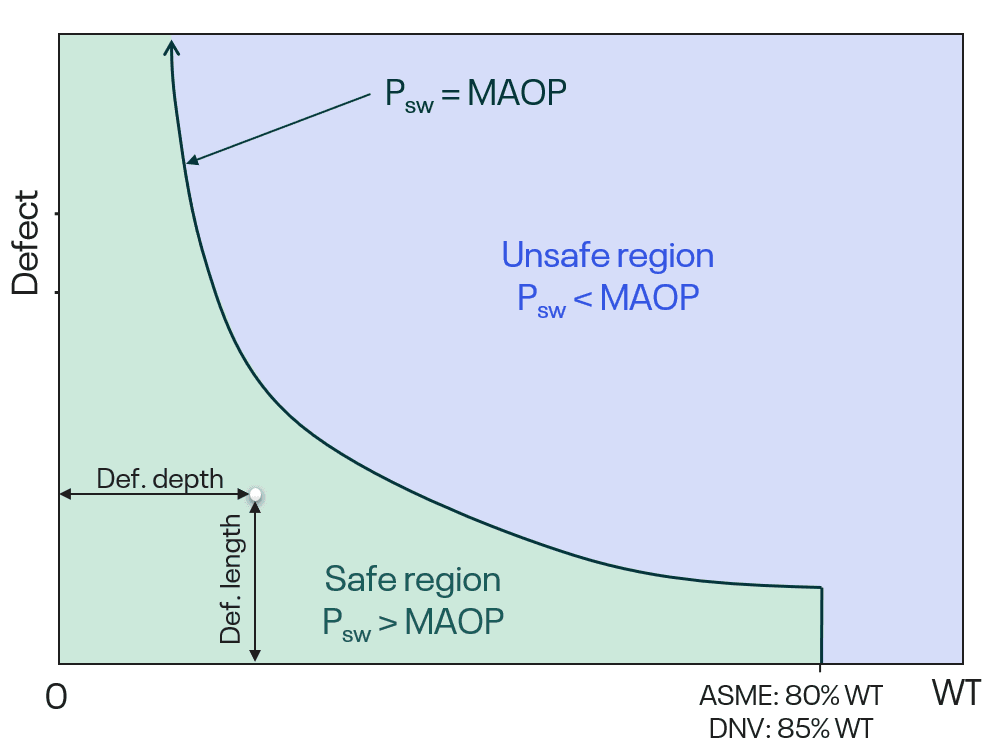
When evaluating defects from In-Line Inspection (ILI) reports, it’s essential to consider maximum allowable depths—80% of Wall Thickness (WT) for ASME and 85% for DNV. Exceeding these thresholds renders defects unsafe.
Defect Interaction Rules
In the world of pipelines, defects rarely stand alone. They often cluster together, creating a complex web of potential weaknesses. ASME B31G assesses the defects individually but acknowledges that closely spaced defects can interact as a single larger defect if they are within three times the nominal wall thickness (3t). This interaction can significantly compromise structural integrity.
In contrast, DNV RP-F101 evaluates each defect individually and considers combinations of adjacent interacting defects. Defects are deemed to interact if their axial distance is less than a specific threshold based on pipe diameter and wall thickness. This criterion helps identify which defects may influence each other.
The DNV RP-F101 method involves a structured three-step process:
- Sectioning the Pipeline: The pipeline is divided circumferentially into sections based on the formula √(D/t), where D is the diameter and t is the wall thickness. This division allows for a structured approach to analyzing defects.
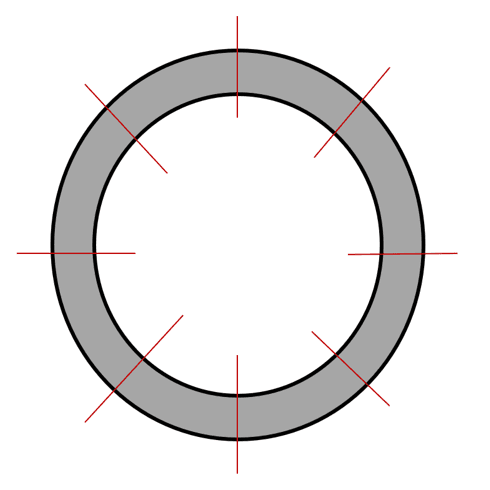
- Projecting Defects: For each projection line corresponding to these sections, defects from neighboring sections are mapped onto the lines. For example, if a defect is located in the first section, it will be projected onto both the first and second lines. If there are defects in the second section, they will be mapped onto the second and third lines. In DNV RP-F101 2010, overlapping internal and external defects interact, too. The resulting depth for the combination is di=d1+d2.
- Calculating Safe Working Pressure: The Psw is calculated for all possible combinations of these interacting defects. The lowest Psw among these calculations becomes the Safe Working Pressure for the corroded pipe.
In the 2010 version of DNV RP-F101, overlapping defects were treated as a single defect with a combined length from the start of the first defect to the end of the last defect in the cluster, using the depth of the deepest defect within that cluster. However, in the 2015 update, overlapping defects are not boxed into one single defect; instead, their individual contributions are considered separately when calculating safe working pressure.
Understanding Corrosion Tolerance
As we delve deeper into pipeline integrity assessments, we encounter the concept of corrosion tolerance—the maximum allowable corrosion that a pipeline can sustain while still being deemed fit for service. This concept is intertwined with the limit state, defining when a pipeline becomes unsafe to operate.
Calculating Corrosion Tolerance in Cases Without Defects
When a pipeline is free of defects, operators must anticipate potential corrosion types—be it general corrosion, grooving, or pitting. For instance, if pitting corrosion is expected, engineers might estimate potential defect lengths as 20 times the depth of the corrosion. This relationship allows them to plot a line on the Failure Assessment diagram from the origin (0,0) based on this length-to-depth ratio. The intersection of this line with safety curve reveals the Corrosion Tolerance (CT) and Minimum Allowable Thickness (MAT) —on the next image the CT and MAT are indicated for grooving corrosion.
In contrast, if general corrosion is assumed, its length might be represented as 1,000 times the Wall Thickness (WT). This method typically yields lower corrosion tolerance since pitting can lead to deeper material loss than general corrosion. Therefore, accurately identifying the expected type of corrosion is crucial for determining appropriate tolerances.
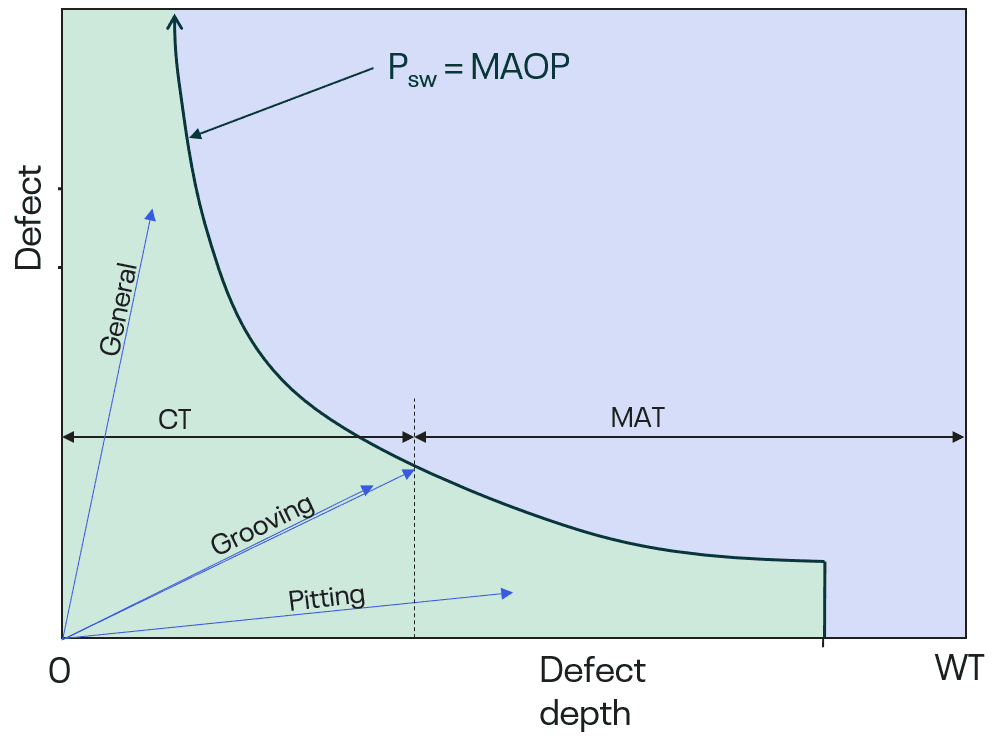
Calculating Corrosion Tolerance in Cases with Defects
When defects are present, the assessment becomes more nuanced. Operators can draw lines on the Failure Assessment Diagram from (0,0) through each defect to ascertain their respective tolerances. The distance between where these lines intersect with the safety curve and where the defect meets the x-axis indicates the Corrosion Tolerances (CT) at the time of the In-Line Inspection (ILI) run.
Corrosion Tolerance (CT) is calculated for every defect. With ASME B31G, this assessment is straightforward; each defect undergoes a single calculation. However, DNV RP-F101 complicates matters with its iterative process—defects may be assessed multiple times if they interact. This complexity becomes particularly evident when dealing with large datasets.
The Interplay of Defects
When two defects are close enough to interact, they share a common Corrosion Tolerance (CT) due to their combined effects on pipeline integrity. This interaction must be carefully assessed to ensure that Safe Working Pressure (Psw) calculations remain valid and that the pipeline continues to operate safely.
Determining Pipeline Service Life and Next Steps for Inspection
As mentioned at the beginning of this article, a Fitness for Service assessment not only determines whether a pipeline is suitable for operation but also estimates how long it can continue to function safely. Once we calculate our Corrosion Tolerance (CT) with the help of the Failure Assessment Curve, we can then estimate the remaining life of the pipeline and calculate when to inspect the pipeline again.
- To find the remaining life, we divide the Corrosion Tolerance (CT) by the Corrosion Rate (CR). For instance, if a pipeline has a Corrosion Tolerance of 2 mm and a Corrosion Rate of 0.1 mm per year, the calculation will look like this:
Remaining Life = CT / CR = 2 mm / 0.1 mm year = 20 years
This means that under current conditions, the pipeline can operate safely for an additional 20 years before reaching its corrosion limit.
- To determine when the next inspection should occur, we need the Interval Factor (IF) derived from a Risk-Based Assessment (RBA), which evaluates the criticality and potential consequences of failures. The formula for calculating the next inspection interval is:
Next Inspection Interval = Remaining Life × IF
Using our previous example, if we assume an internal factor of 0.3, the calculation would be:
Next Inspection Interval = 20 years × 0.3 = 6 years
This indicates that the pipeline should be inspected again in 6 years to ensure it remains fit for service.
Assessing Pipeline’s Fitness for Service with IMS PLSS
In pipeline management, Fitness for Service (FFS) assessments are essential for ensuring the safety and continued operation of aging infrastructure. These evaluations not only determine if a pipeline can remain in service but also provide insights into its remaining lifespan.
Data analysis emerges as the heartbeat of this process, helping operators predict performance and schedule inspections based on calculated remaining life. Cenoco’s IMS – Pipeline and Subsea Systems (PLSS) enables operators to assess pipeline fitness, offering insights into the remaining lifespan. Using methodologies like ASME B31G and DNV RP-F101, operators can accurately evaluate defects and calculate corrosion tolerances. Analyzing the relationship between defects, hoop stress, and Safe Working Pressures supports proactive pipeline management.
PLSS allows users to assess ILI data through the Fitness for Service module, showing the Safe Working Pressure and Estimated Repair Factor for each defect. Its strength lies in calculating Corrosion Tolerance for individual or grouped defects, factoring in material grade, defect size, and depth. The Risk-Based Assessment module calculates the pipeline’s Remaining Life and next inspection date, with the option to schedule and log inspection findings in the Condition History. This system supports Fitness for Service assessments for pipelines, flowlines, and jumpers made from carbon steel and corrosion-resistant alloys.
PLSS addresses the most common in-service pipeline defects, specifically volumetric corrosion that can lead to plastic collapse. It focuses on essential yet straightforward Level 1 assessments, such as ASME B31G and DNV RP-F101 Part B. This streamlined approach allows operators to prioritize economic considerations. A more detailed evaluation outside of PLSS is recommended for highly critical pipelines or pipelines subject to strict regulations.
In conclusion, PLSS is highly effective for managing known, controlled conditions involving volumetric corrosion defects under hoop pressure loading.
Want to learn more about IMS?
Request a demo below to get a first-hand look at its capabilities!
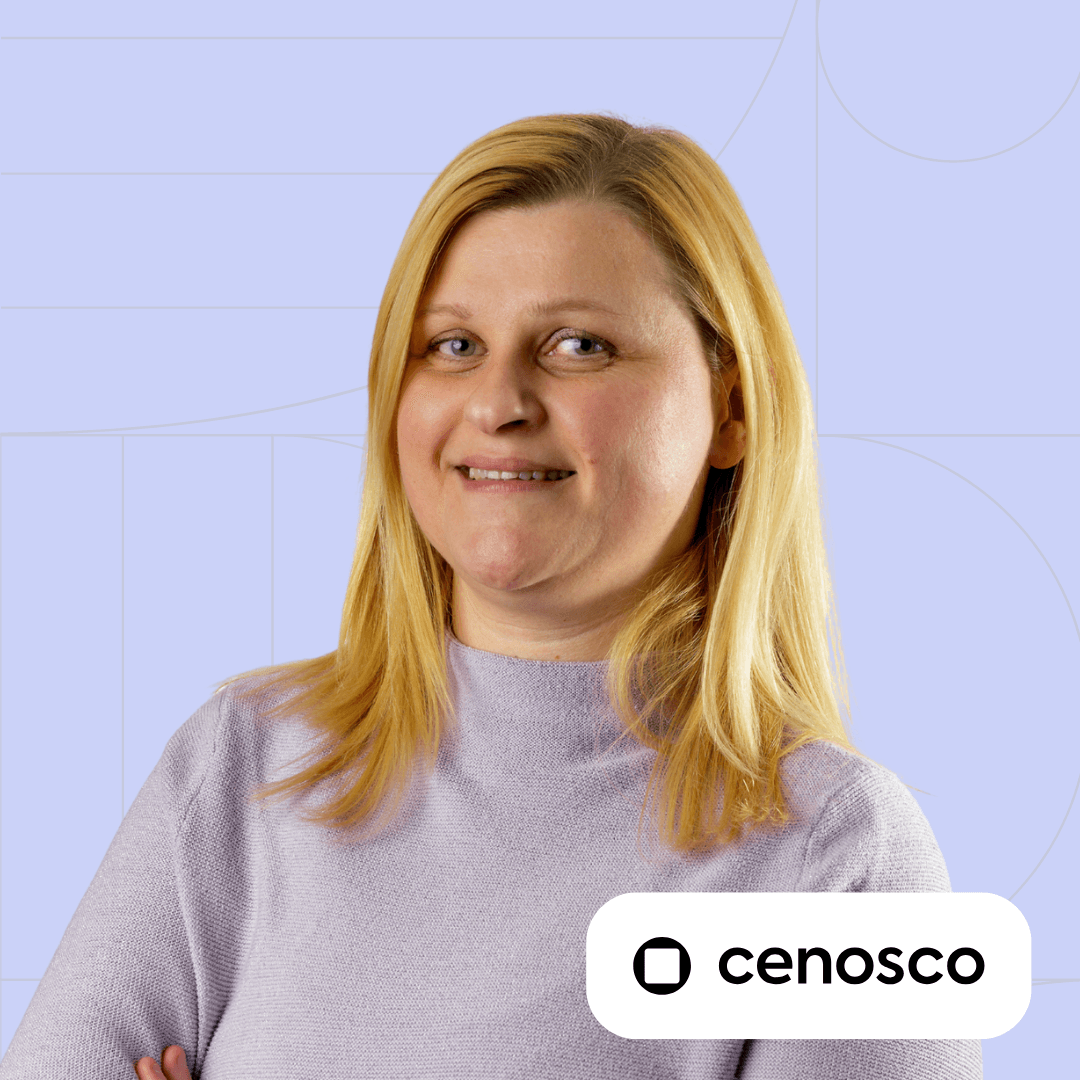
Denis Tkalec Technical writer
Denis Tkalec is a technical writer at Cenosco, specializing in asset integrity management software since 2022. With a background in education and six years in marketing, she turns complex topics into clear, user-friendly content. Inspired by Camus’s belief that “a writer keeps civilization from destroying itself,” she brings precision and care to every manual.