Пригодность к эксплуатации (FFS) - это не просто технический термин; это спасательный круг для промышленного мира, особенно в тех отраслях, где стареющая инфраструктура представляет собой значительный риск. Представьте себе оживленную нефтяную вышку или разветвленную систему трубопроводов, где каждый сантиметр металла и сварного шва постоянно подвергается тщательному контролю. Эти объекты являются жилами нашей экономики, и обеспечение их целостности имеет решающее значение для безопасности и эффективности.
В этой статье блога мы отправимся в путешествие, чтобы понять суть оценки FFS, уделяя особое внимание трубопроводам, в которых обнаружены дефекты, приводящие к материальным потерям.
Что такое пригодность к службе?
По своей сутиFitness for Service- это количественный инженерный метод, предназначенный для оценки состояния промышленных активов, находящихся в эксплуатации, -трубопроводов, сосудов под давлением и резервуаров для хранения. Цель? Определить, смогут ли эти критически важные компоненты продолжать безопасно и эффективно выполнять свои функции.
Этот процесс включает в себя тщательную оценку нескольких факторов: проектных спецификаций, свойств материалов, условий эксплуатации, а также любых существующих дефектов или повреждений. Этот комплексный анализ соответствует установленным отраслевым стандартам, таким как API 579-1/ASME FFS-1, BS 7910, DNV RP-F101 и ASME B31G, в которых изложены методики оценки пригодности компонентов на протяжении всего их жизненного цикла.
Преимущества оценки пригодности к службе
Преимущества проведения оценки FFS многообразны:
- Продление срока службы активов: Определяя текущее состояние оборудования, организации могут принимать обоснованные решения, продлевающие срок эксплуатации активов.
- Экономия средств: Точные оценки сводят к минимуму ненужные ремонты и замены, что приводит к значительной экономии эксплуатационных расходов.
- Повышенная безопасность: Регулярные оценки обеспечивают безопасную работу оборудования, снижая риск сбоев, которые могут угрожать персоналу и окружающей среде.
- Повышение надежности: Поддержание механической целостности обеспечивает надежное функционирование критически важных систем, что необходимо для повышения эффективности работы.
- Оптимизированное планирование технического обслуживания: Данные, полученные в результате оценки FFS, служат основой для составления графиков технического обслуживания, предотвращая незапланированные простои.
- Соответствие нормативным требованиям: Соблюдение отраслевых стандартов с помощью оценок FFS снижает юридическую ответственность и повышает доверие к операционной деятельности.
Обоснованное принятие решений: Структурированная система оценки состояния активов позволяет принимать более обоснованные решения о ремонте или продолжении эксплуатации.
Обзор уровней оценки FFS
Стандарт API 579-1/ASME FFS-1 предусматривает три уровня оценки:
- Оценки уровня 1 (FFS1): Эти простые оценки используют такие методы, как B31G и DNV RP-F101, для получения быстрых выводов на основе минимальных данных. Несмотря на экономическую эффективность, они могут упустить критические переменные.
- Оценки уровня 2 (FFS2): Здесь проводится более сложный анализ с использованием исходных сигнальных данных, а не только измерений дефектов. Оценки уровня 2 уточняют анализ, рассматривая дополнительные параметры, когда уровень 1 указывает на потенциальные проблемы.
- Оценка уровня 3 (FFS3): Используя передовые методы, такие как анализ методом конечных элементов (FEA), этот уровень предлагает всестороннее понимание состояния активов благодаря учету сложных взаимодействий и распределений напряжений.
Цель оценки трубопроводов с помощью FFS
Основная цель оценки пригодности к эксплуатации проста, но жизненно важна: определить, пригоден ли компонент с имеющимися дефектами для дальнейшей эксплуатации. Для трубопроводов это означает, что безопасное рабочее давление (PSW) должно превышать максимально допустимое рабочее давление (MAOP).
FFS также отвечает на вопрос, как долго он будет оставаться пригодным к эксплуатации. Оценка также включает в себя расчет допустимого уровня коррозии и определение того, насколько сильной может быть коррозия без нарушения целостности конструкции. Такая оценка не только обеспечивает безопасность эксплуатации, но и помогает предсказать, сколько еще осталось жить трубопроводу. С помощью этой информации и метода оценки риска мы можем рассчитать дату следующей инспекции.
Расчет безопасного рабочего давления в трубопроводе
Безопасное рабочее давление (PSW)- это метрика, определяющая максимальное давление, которое трубопровод может безопасно выдерживать при нормальной эксплуатации.PSW всегда должно превышать максимально допустимое рабочее давление (MAOP), представляющее собой максимальное давление, при котором трубопровод может работать без риска разрушения или повреждения.
Понятие о нагрузке на обруч и расчетном давлении
Теперь давайте углубимся в механику. Представьте себе внутренние силы, возникающие при движении жидкостей по трубопроводу. Именно здесь в игру вступаетнапряжение обруча- молчаливый страж, обхватывающий трубу и противодействующий ее естественному стремлению лопнуть под давлением.
Инженеры изучают напряжение в обруче, чтобы определить, какое внутреннее давление может выдержать труба. Это похоже на оценку прочности моста перед тем, как пустить по нему большегрузный транспорт. Формула, лежащая в основе этой оценки, - уравнение Барлоу, которое помогает инженерам рассчитать напряжение обруча на основе внутреннего давления, диаметра трубы и толщины стенки.
σh=P(D-t)/2t
Где:
- σh= напряжение обруча
- P= Внутреннее давление
- D= Диаметр трубы
- t= Толщина стенки трубы
Из напряжения обруча вытекает еще одно важнейшее понятие:расчетное давление. Этот параметр представляет собой максимальное давление, которое трубопровод может безопасно выдержать, с учетом необходимого запаса прочности. Инженеры учитывают такие факторы, как толщина стенки и прочность материала, чтобы гарантировать, что трубопроводы рассчитаны на давление, значительно превышающее то, с которым они столкнутся в реальных условиях. Это упреждающий инжиниринг в его лучшем проявлении - предотвращение потенциальных отказов до их возникновения.
Свойства материалов и механизмы разрушения
Чтобы понять, как ведут себя трубопроводы под нагрузкой, необходимо изучить свойства их материалов и возможные механизмы разрушения. Здесь кривая "напряжение-деформация" иллюстрирует реакцию материалов на приложенные силы.
- Предел текучести (σy)представляет собой максимальное напряжение, которое может выдержать материал, сохраняя свою первоначальную форму после снятия нагрузки.
- Предельная прочность на разрыв (σUTS)указывает на максимальное напряжение, при котором материал начинает разрушаться.
Разрушение обычно происходит между этими порогами, знаменуя переход от упругого поведения, при котором материалы могут снова пружинить, к пластической деформации, при которой происходят необратимые изменения.
Оценка условий отказа
С практической точки зрения, разрушение трубопровода происходит, когда напряжение обруча достигает критического порога, называемогонапряжением потока(σflow). Эта точка означает, что трубопровод больше не может сохранять свою структурную целостность под давлением. Инженеры анализируют эти условия, чтобы определить базовые ожидания для характеристик материала в идеальных условиях.
Когда в дело вступает коррозия, все становится еще сложнее. Инженеры должны оценить все дефекты, которые могут нарушить целостность конструкции.
Например, если наш трубопровод имеет дефект, характеризующийся определенной длиной (L) и глубиной (d), мы можем рассчитать площадь дефекта как:
A0= L x t
Где:
- A0= площадь дефекта
- t = Толщина стенки трубы
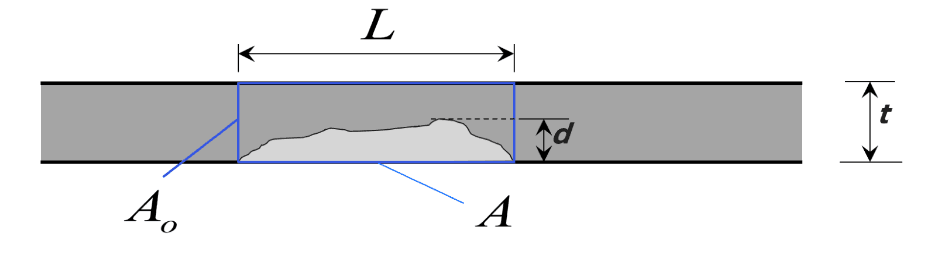
Чтобы определить давление разрушения корродированной трубы, мы начинаем с давления разрушения неповрежденной трубы и применяем коэффициент, известный каккоэффициент остаточной прочности (RSF), который учитывает влияние коррозии:
RSF = (1 - A / A0) / 1 - (A / A0 x 1 / M)
Где:
- A = Площадь, подверженная коррозии
- M = коэффициент раздутия учитывает влияние внутреннего давления на структурную целостность трубы с дефектами.
Давление разрушения (Pfailure) корродированного трубопровода может быть выражено как давление разрушения неповрежденной трубы, умноженное на коэффициент остаточной прочности (RSF) из-за коррозии:
Pfailure = 2tσflow / (D - t) x RSF
Или
Pfailure = 2tσflow / (D - t) x ((1 - A / A0) / 1 - (A / A0 x 1 / M))
Это уравнение служит универсальным методом расчета безопасного рабочего давления для различных кодов оценки трубопроводов и FFS.
Где:
- σflow= напряжение течения (напряжение, при котором происходит разрушение)
- D = Диаметр трубы
Оценивая степень коррозии и ее влияние на допустимое давление, они определяют, какое давление может безопасно выдержать корродированная труба, обеспечивая точную оценку даже в не самых лучших условиях.
Установление безопасных границ: Безопасное рабочее давление
Безопасное рабочее давление (PSW)является важнейшим ориентиром для эксплуатационных ограничений. Его можно рассчитать по следующей формуле:
PSW = f x 2tσflow / (D - t) x RSF
или
PSW = f x 2tσflow / (D - t) x ((1 - A / A0) / 1 - (A / A0 x 1 / M))
Где:
f = расчетный коэффициент или коэффициент безопасности, учитывающий неопределенность свойств материала и условий эксплуатации.
Фактор ремонта: Навигация по ERF
После того как мы установили безопасное рабочее давление, мы рассчитываемоценочный коэффициент ремонта (ERF), основываясь на результатах проверки. ERF определяется как:
ERF = MAOP xPSW
Этот фактор помогает определить необходимость корректирующих действий:
- Если ERF меньше 1, это означает, что MAOP ниже безопасного рабочего давления, что позволяет безопасно продолжать работы.
- И наоборот, если ERF превышает 1, это сигнализирует о необходимости немедленных действий, например, ремонта или корректировки эксплуатационных ограничений.
Например, если инспекция выявляет ERF 0,8 в определенный момент времени, но последующие оценки показывают увеличение более 1, это говорит о необходимости оперативного вмешательства для обеспечения безопасности.
Метод оценки дефектов
Для оценки пригодности трубопровода к эксплуатации мы должны оценить дефекты, чтобы определить допустимый уровень коррозии. Затем мы можем рассчитать оставшийся срок службы трубы и дату следующей инспекции. В этой области доминируют два основных метода:ASME B31GиDNV RP-F101.
Стандарт ASME B31Gбыл первым, в котором решалась задача расчета безопасного рабочего давления при наличии дефектов. Он включает в себя оригинальный стандарт, определяющий напряжение текучести как 1,1-кратное значение заданного минимального предела текучести (SMYS), и модифицированную версию, в которой это значение уточняется до SMYS плюс дополнительные 69 МПа (около 10 KSI) для большей точности.
С другой стороны,DNV RP-F101, введенный в 2010 году, фокусируется на пределе прочности при растяжении (UTS), прогнозируя разрушение при 0,9-кратном UTS. Этот стандарт упрощает форму дефектов, рассматривая их как прямоугольные, в то время как ASME B31G первоначально рассматривал дефекты как параболические, но позже допустил произвольную форму.
Другим важным аспектом являетсякоэффициент выпуклости, который измеряет, как дефекты деформируются под давлением. Маленькие дефекты уменьшают его значение, а большие - увеличивают.
Для визуализации безопасного рабочего давления в обоих стандартах используетсядиаграмма оценки отказов (FAD), которая переводит уравнение безопасного рабочего давления (PSW = f x 2tσflow / (D - t) x ((1 - A / A0) / 1 - (A / A0 x 1 / M)) в графический формат, отображающий длину дефекта против глубины. Точки под кривой обозначают безопасные условия, а точки над кривой - потенциальные риски разрушения.
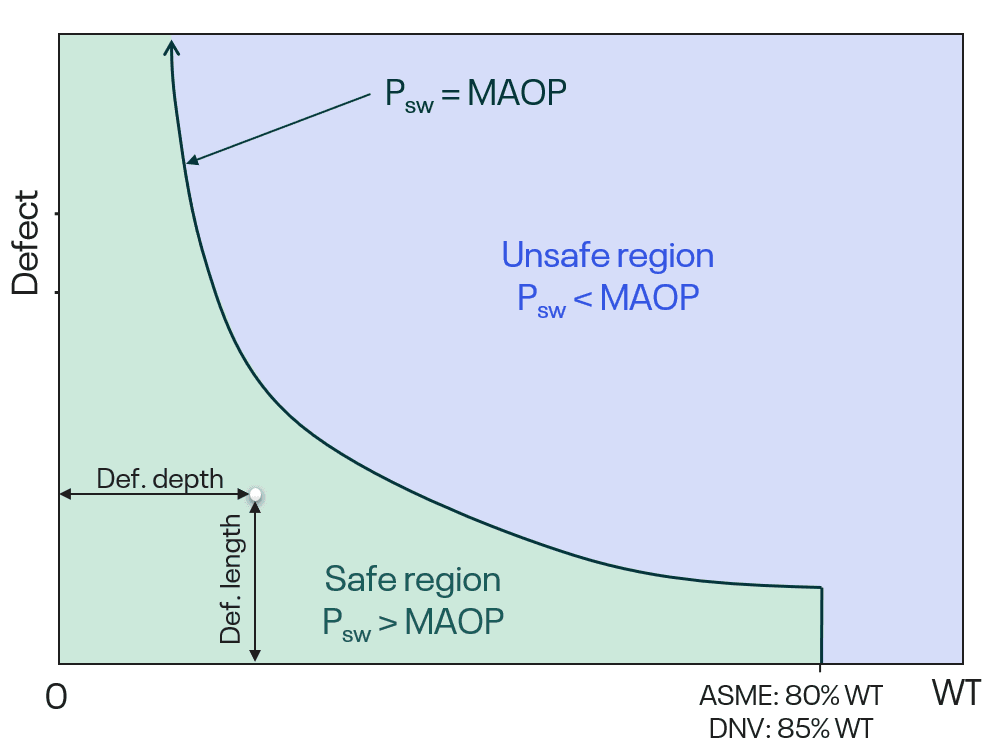
При оценке дефектов из отчетов о внутритрубной инспекции (ILI) необходимо учитывать максимально допустимую глубину - 80 % толщины стенки (WT) по ASME и 85 % по DNV. Превышение этих пороговых значений делает дефекты небезопасными.
Правила взаимодействия с дефектами
В мире трубопроводов дефекты редко бывают одиночными. Они часто группируются вместе, создавая сложную паутину потенциальных слабых мест. ASME B31G оценивает дефекты по отдельности, но признает, что близко расположенные дефекты могут взаимодействовать как один более крупный дефект, если они находятся в пределах трехкратного превышения номинальной толщины стенки (3t). Такое взаимодействие может существенно нарушить целостность конструкции.
В отличие от этого, DNV RP-F101 оценивает каждый дефект в отдельности и рассматривает комбинации соседних взаимодействующих дефектов. Дефекты считаются взаимодействующими, если их осевое расстояние меньше определенного порога, основанного на диаметре трубы и толщине стенки. Этот критерий помогает определить, какие дефекты могут влиять друг на друга.
Метод DNV RP-F101 включает в себя структурированный трехэтапный процесс:
- Деление трубопровода на секции: Трубопровод делится по окружности на секции по формуле √(D/t), гдеD- диаметр, аt- толщина стенки. Такое деление позволяет использовать структурированный подход к анализу дефектов.
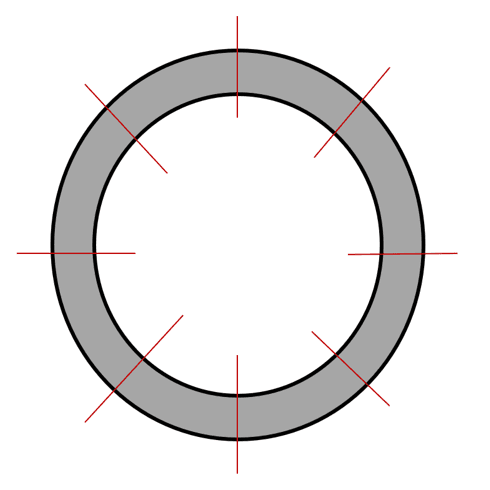
- Проецирование дефектов: Для каждой линии проекции, соответствующей данным секциям, дефекты из соседних секций проецируются на эти линии. Например, если дефект находится в первой секции, он будет спроецирован на первую и вторую линии. Если дефекты есть во второй секции, они будут отображены на вторую и третью линии. В DNV RP-F101 2010 перекрывающиеся внутренние и внешние дефекты также взаимодействуют. Результирующая глубина для комбинации равна di=d1+d2.
- Расчет безопасного рабочего давления: Psw рассчитывается для всех возможных комбинаций этих взаимодействующих дефектов. Наименьшее значение Psw из этих расчетов становится безопасным рабочим давлением для корродированной трубы.
В версии DNV RP-F101 2010 года перекрывающиеся дефекты рассматривались как один дефект с суммарной длиной от начала первого дефекта до конца последнего дефекта в кластере, используя глубину самого глубокого дефекта в этом кластере. Однако в обновленном варианте 2015 года перекрывающиеся дефекты не объединяются в один дефект; вместо этого их индивидуальный вклад рассматривается отдельно при расчете безопасного рабочего давления.
Понимание коррозионной устойчивости
Углубляясь в оценку целостности трубопроводов, мы сталкиваемся с понятиемдопустимой коррозии -максимально допустимой коррозии, которую может выдержать трубопровод, оставаясь пригодным к эксплуатации. Эта концепция переплетается спредельным состоянием, определяющим, когда трубопровод становится небезопасным для эксплуатации.
Расчет допустимой коррозии в случаях без дефектов
Если трубопровод не имеет дефектов, операторы должны предугадать возможные виды коррозии - общую коррозию, канавки или точечную коррозию. Например, если ожидаетсяточечная коррозия, инженеры могут оценить длину потенциального дефекта как 20-кратную глубину коррозии. Это соотношение позволяет им построить линию на диаграмме оценки отказов из начала координат (0,0), основываясь на этом соотношении длины и глубины. Пересечение этой линии с кривой безопасности определяет допуск на коррозию (CT) и минимально допустимую толщину (MAT) - на следующем изображении CT и MAT указаны для бороздчатой коррозии.
В отличие от этого, если предполагается общая коррозия, ее длина может быть представлена как 1000-кратная толщина стенки (WT). Этот метод обычно дает меньший допуск на коррозию, поскольку точечная коррозия может привести к более глубокой потере материала, чем общая коррозия. Поэтому точное определение ожидаемого типа коррозии имеет решающее значение для определения соответствующих допусков.
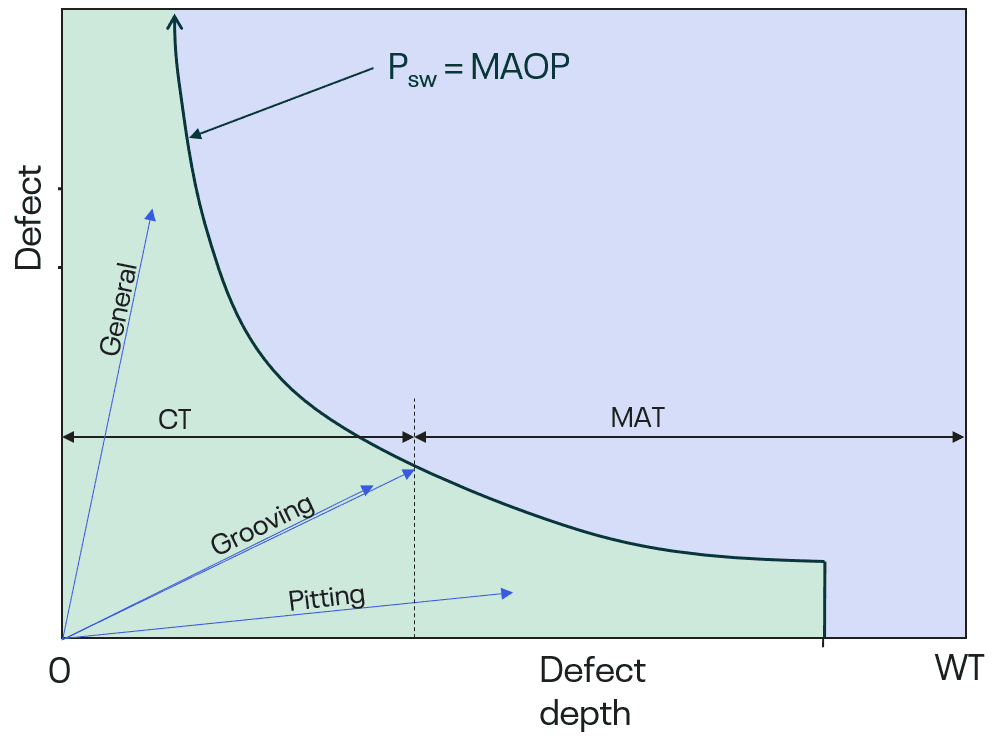
Расчет допустимой коррозии в случаях с дефектами
При наличии дефектов оценка становится более тонкой. Операторы могут провести линии на диаграмме оценки отказов от (0,0) через каждый дефект, чтобы определить их соответствующие допуски. Расстояние между местом пересечения этих линий с кривой безопасности и местом пересечения дефекта с осью x указывает на допуски коррозии (CT) на момент проведения инспекции на линии (ILI).
Коррозионный допуск (КД) рассчитывается для каждого дефекта. В стандартеASME B31G эта оценка проста: каждый дефект подвергается однократному расчету. ОднакоDNV RP-F101усложняет ситуацию своим итеративным процессом - дефекты могут быть оценены несколько раз, если они взаимодействуют. Эта сложность становится особенно очевидной при работе с большими массивами данных.
Взаимосвязь дефектов
Когда два дефекта находятся достаточно близко, чтобы взаимодействовать, они имеют общий коррозионный допуск (КД) из-за их совместного воздействия на целостность трубопровода. Это взаимодействие должно быть тщательно оценено, чтобы убедиться, что расчеты безопасного рабочего давления (Psw) остаются верными и что трубопровод продолжает безопасно эксплуатироваться.
Определение срока службы трубопровода и дальнейшие шаги по его проверке
Как уже упоминалось в начале статьи, оценка пригодности к эксплуатации не только определяет, пригоден ли трубопровод к эксплуатации, но и оценивает, как долго он может продолжать безопасно функционировать. Рассчитав допустимую коррозию (CT) с помощью кривой оценки отказов, мы можем оценить оставшийся срок службы трубопровода и рассчитать, когда необходимо провести его очередное обследование.
- Чтобы определить оставшийся срок службы, нужно разделить Допуск на коррозию (CT) на Скорость коррозии (CR). Например, если допуск на коррозию трубопровода составляет 2 мм, а скорость коррозии - 0,1 мм в год, расчет будет выглядеть следующим образом:
Остаточный срок службы = CT / CR = 2 мм / 0,1 мм в год = 20 лет
Это означает, что при существующих условиях трубопровод может безопасно работать еще 20 лет, прежде чем достигнет предела коррозии.
- Чтобы определить, когда следует провести следующую проверку, нам нужен коэффициент интервала (IF), полученный в результатеоценки риска (RBA), которая оценивает критичность и потенциальные последствия отказов. Формула для расчета интервала следующей проверки выглядит следующим образом:
Интервал следующего осмотра = Оставшийся срок службы × IF
Используя наш предыдущий пример, если мы примем внутренний коэффициент 0,3, расчет будет следующим:
Интервал следующего осмотра = 20 лет × 0,3 = 6 лет
Это говорит о том, что трубопровод следует снова проверить через 6 лет, чтобы убедиться, что он по-прежнему пригоден к эксплуатации.
Оценка пригодности трубопроводов к эксплуатации с помощью IMS PLSS
При управлении трубопроводами оценка пригодности к эксплуатации (FFS) необходима для обеспечения безопасности и непрерывной работы стареющей инфраструктуры. Эти оценки не только определяют, может ли трубопровод оставаться в эксплуатации, но и дают представление о его оставшемся сроке службы.
Анализ данных становится сердцем этого процесса, помогая операторам прогнозировать работу и составлять график проверок на основе рассчитанного остаточного срока службы. Система IMS - Трубопроводные и подводные системы (PLSS) компании Cenoco позволяет операторам оценивать пригодность трубопроводов, предлагая информацию об оставшемся сроке службы. Используя такие методики, как ASME B31G и DNV RP-F101, операторы могут точно оценить дефекты и рассчитать допуски на коррозию. Анализ взаимосвязи между дефектами, напряжением в обруче и безопасным рабочим давлением способствует проактивному управлению трубопроводом.
PLSS позволяет пользователям оценивать данные ILI с помощью модуля Fitness for Service, показывая безопасное рабочее давление и оценочный коэффициент ремонта для каждого дефекта. Его сильной стороной является расчет допустимой коррозии для отдельных или сгруппированных дефектов с учетом марки материала, размера и глубины дефекта. Модуль оценки риска рассчитывает остаточный срок службы трубопровода и дату следующего осмотра с возможностью планирования и регистрации результатов осмотра в истории состояния. Эта система поддерживает оценку пригодности к эксплуатации трубопроводов, поточных линий и перемычек из углеродистой стали и коррозионностойких сплавов.
PLSS рассматривает наиболее распространенные дефекты трубопроводов в процессе эксплуатации, в частности объемную коррозию, которая может привести к пластическому разрушению. Основное внимание уделяется важным, но простым оценкам уровня 1, таким как ASME B31G и DNV RP-F101 Part B. Такой упрощенный подход позволяет операторам уделять первоочередное внимание экономическим соображениям. Более подробная оценка за пределами PLSS рекомендуется для особо ответственных трубопроводов или трубопроводов, на которые распространяются строгие нормы.
В заключение следует отметить, что PLSS очень эффективна для управления известными, контролируемыми условиями, включающими объемные коррозионные дефекты под нагрузкой обручного давления.
Хотите узнать больше о IMS?
Запросите демонстрацию ниже, чтобы воочию увидеть его возможности!
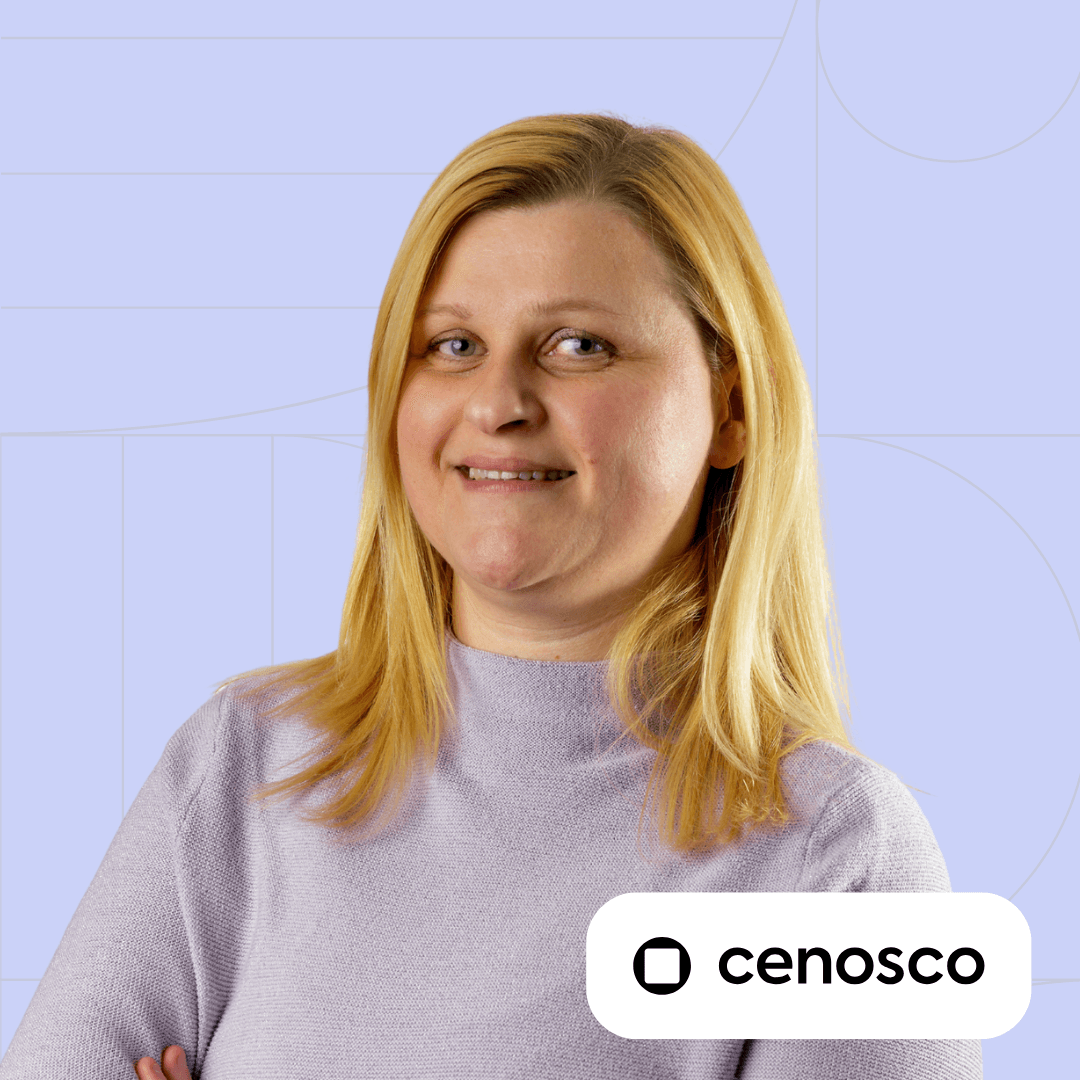
Denis Tkalec Technical writer
Denis Tkalec is a technical writer at Cenosco, specializing in asset integrity management software since 2022. With a background in education and six years in marketing, she turns complex topics into clear, user-friendly content. Inspired by Camus’s belief that “a writer keeps civilization from destroying itself,” she brings precision and care to every manual.