Fitness for Service (FFS) não é apenas um termo técnico; é uma tábua de salvação para o mundo industrial, particularmente em sectores onde o envelhecimento das infra-estruturas representa riscos significativos. Imagine uma plataforma petrolífera em plena atividade ou um sistema de condutas em expansão, onde cada centímetro de metal e solda é constantemente examinado. Estes activos são as veias da nossa economia, e garantir a sua integridade é crucial para a segurança e eficiência.
Nesta publicação do blogue, vamos embarcar numa viagem para compreender a essência das avaliações FFS, concentrando-nos particularmente nas condutas que apresentam defeitos que resultam em perdas de material.
O que é a aptidão para o serviço?
Na sua essência, aAdequação ao Serviçoé um métodode engenharia quantitativo concebido para avaliar o estado dos activos industriais em serviço - pense emcondutas, recipientes sob pressão e tanques de armazenamento. O objetivo? Determinar se estes componentes críticos podem continuar a desempenhar as funções pretendidas de forma segura e eficaz.
Este processo envolve uma avaliação meticulosa de vários factores: especificações de conceção, propriedades dos materiais, condições de funcionamento e quaisquer falhas ou danos existentes. Esta análise abrangente segue as normas estabelecidas pela indústria, tais como API 579-1/ASME FFS-1, BS 7910, DNV RP-F101 e ASME B31G, que definem metodologias para avaliar a adequação dos componentes ao longo do seu ciclo de vida.
As vantagens das avaliações de aptidão para o serviço
As vantagens da realização de avaliações FFS são múltiplas:
- Aumento da vida útil dos activos: Ao identificar o estado atual do equipamento, as organizações podem tomar decisões informadas que prolongam a vida operacional dos seus activos.
- Poupança de custos: Avaliações exactas minimizam reparações e substituições desnecessárias, levando a poupanças significativas nos custos de manutenção.
- Segurança reforçada: As avaliações regulares garantem que o equipamento funciona em segurança, reduzindo o risco de falhas que podem pôr em perigo o pessoal e o ambiente.
- Fiabilidade melhorada: A manutenção da integridade mecânica garante que os sistemas críticos funcionam de forma fiável, o que é essencial para a eficiência operacional.
- Planeamento de manutenção optimizado: As informações das avaliações FFS informam os planos de manutenção, evitando períodos de inatividade não planeados.
- Conformidade regulamentar: O cumprimento das normas do sector através de avaliações FFS reduz as responsabilidades legais e aumenta a credibilidade operacional.
Tomada de decisões informada: Um quadro estruturado para avaliar as condições dos activos permite tomar melhores decisões relativamente a reparações ou à continuação do funcionamento.
Visão geral dos níveis de avaliação FFS
A norma API 579-1/ASME FFS-1 define três níveis de avaliação:
- Avaliações de Nível 1 (FFS1): Estas avaliações diretas utilizam métodos como o B31G e o DNV RP-F101 para fornecer uma visão rápida com base em dados mínimos. Embora sejam económicas, podem ignorar variáveis críticas.
- Avaliações de nível 2 (FFS2): Aqui entram em ação análises mais complexas, utilizando dados de sinais originais em vez de apenas medições de defeitos. As avaliações de nível 2 refinam a análise, considerando parâmetros adicionais quando o nível 1 indica potenciais problemas.
- Avaliações de nível 3 (FFS3): Empregando técnicas avançadas como a Análise de Elementos Finitos (FEA), este nível oferece uma visão abrangente das condições dos activos, tendo em conta as interações complexas e as distribuições de tensões.
O objetivo da avaliação FFS das condutas
O principal objetivo das avaliações de aptidão para serviço é simples, mas vital: avaliar se um componente com defeitos existentes ainda está apto para continuar em serviço. No caso das condutas, isto significa garantir que a pressão de trabalho segura (PSW) excede a pressão máxima de funcionamento permitida (MAOP).
O FFS também responde à questão de saber durante quanto tempo se manterá apto para o serviço. A avaliação também inclui o cálculo da tolerância à corrosão e a determinação da quantidade de corrosão que pode ocorrer sem comprometer a integridade estrutural. Esta avaliação não só salvaguarda as operações, como também ajuda a prever a vida útil restante de uma conduta. Com essa informação e a ajuda da Avaliação Baseada no Risco, podemos calcular a data da próxima inspeção.
Cálculo da pressão de trabalho segura de uma conduta
A pressão de trabalho segura (PSW)é uma métrica que define a pressão máxima que uma conduta pode suportar em segurança durante as operações normais.A PSW deve sempre exceder a Pressão Operacional Máxima Permitida (MAOP), que representa a pressão mais elevada a que uma conduta pode funcionar sem risco de falha ou danos.
Compreender a tensão de arco e a pressão de projeto
Agora, vamos mergulhar mais fundo na mecânica. Imagine as forças internas em jogo quando os fluidos passam pela tubagem. É aqui quea tensão do aroentra em ação - um guardião silencioso, que envolve o tubo e contraria a sua tendência natural para rebentar sob pressão.
Os engenheiros estudam a tensão do aro para avaliar a pressão interna que um tubo pode suportar. É como avaliar a resistência de uma ponte antes de permitir a passagem de tráfego pesado. A fórmula por detrás desta avaliação é a Equação de Barlow, que ajuda os engenheiros a calcular a tensão do anel com base na pressão interna, no diâmetro do tubo e na espessura da parede.
σh=P(D-t)/2t
Onde:
- σh= Tensão do arco
- P= Pressão interna
- D= Diâmetro do tubo
- t= Espessura da parede do tubo
Da tensão do anel decorre outro conceito crítico:a pressão de projeto. Este parâmetro representa a pressão máxima que uma tubagem pode suportar em segurança, incorporando as margens de segurança necessárias. Os engenheiros consideram factores como a espessura da parede e a resistência do material para garantir que as condutas são concebidas para suportar pressões muito superiores às que enfrentarão em condições reais. É a engenharia proactiva no seu melhor - prevenindo potenciais falhas antes que elas ocorram.
Propriedades dos materiais e mecanismos de falha
Para compreender verdadeiramente como as condutas se comportam sob tensão, temos de explorar as suas propriedades materiais e potenciais mecanismos de falha. Aqui, a curva tensão-deformação ilustra a forma como os materiais respondem às forças aplicadas.
- Resistência ao escoamento (σy)representa a tensão máxima que um material pode tolerar enquanto regressa à sua forma original depois de a carga ser removida.
- Resistência à tração final (σUTS)indica a tensão máxima antes de um material começar a falhar.
A falha ocorre tipicamente entre estes limiares, marcando uma transição do comportamento elástico - onde os materiais podem voltar a saltar - para a deformação plástica, onde ocorrem alterações permanentes.
Avaliação das condições de falha
Em termos práticos, a falha da tubagem ocorre quando a tensão do anel atinge um limiar crítico denominadotensão de fluxo(σflow). Este ponto significa que a tubagem já não consegue manter a sua integridade estrutural sob pressão. Os engenheiros analisam estas condições para estabelecer expectativas de base para o desempenho do material em circunstâncias ideais.
Quando a corrosão entra em cena, as coisas tornam-se mais complicadas. Os engenheiros têm de avaliar quaisquer defeitos que possam comprometer a integridade estrutural.
Por exemplo, se a nossa conduta tiver um defeito caracterizado por um determinado comprimento (L) e profundidade (d), podemos calcular a área do defeito como:
A0= L x t
Onde:
- A0= Área do defeito
- t = Espessura da parede do tubo
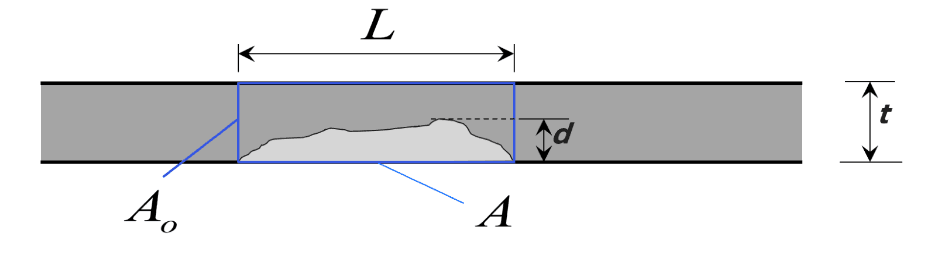
Para determinar a pressão de rutura do tubo corroído, começamos com a pressão de rutura de um tubo não danificado e aplicamos um fator conhecido comoFator de Resistência Remanescente (RSF), que tem em conta o impacto da corrosão:
RSF = (1 - A / A0) / 1 - (A / A0 x 1 / M)
Onde:
- A = Área afetada pela corrosão
- M = O fator de abaulamento tem em conta os efeitos da pressão interna na integridade estrutural de um tubo com defeitos.
A pressão de rutura (Pfailure) de uma tubagem corroída pode então ser expressa como a pressão de rutura da tubagem não danificada vezes o Fator de Resistência Remanescente (RSF) devido à corrosão:
Pfailure = 2tσflow / (D - t) x RSF
Ou
Pfailure = 2tσflow / (D - t) x ((1 - A / A0) / 1 - (A / A0 x 1 / M))
Esta equação serve como um método universal para calcular as pressões de trabalho seguras em vários códigos de avaliação de condutas e FFS.
Onde:
- σflow= Tensão de escoamento (a tensão em que ocorre a rotura)
- D = Diâmetro do tubo
Ao avaliar a extensão da corrosão e o seu impacto na tolerância à pressão, determinam a pressão que um tubo corroído pode suportar em segurança - assegurando avaliações exactas mesmo em condições menos que ideais.
Estabelecer limites seguros: Pressão de trabalho segura
Apressão de trabalho segura (PSW)emerge destas avaliações como uma diretriz essencial para os limites operacionais. Pode ser calculada utilizando a seguinte fórmula:
PSW = f x 2tσfluxo / (D - t) x RSF
ou
PSW = f x 2tσflow / (D - t) x ((1 - A / A0) / 1 - (A / A0 x 1 / M))
Onde:
f = Fator de projeto ou fator de segurança, que tem em conta as incertezas das propriedades dos materiais e das condições de funcionamento.
O fator de reparação: Navegando pelo ERF
Depois de estabelecermos a pressão de trabalho segura, calculamos umFator de Reparação Estimado (ERF)com base nos resultados da inspeção. O FRE é definido como:
FER = MAOP xPSW
Este fator ajuda a determinar se são necessárias medidas corretivas:
- Se o ERF for inferior a 1, indica que a MAOP é inferior à pressão de trabalho segura - permitindo que as operações continuem em segurança.
- Inversamente, se o ERF exceder 1, indica que é necessária uma ação imediata, por exemplo, reparações ou ajustamentos dos limites operacionais.
Por exemplo, se uma inspeção revelar um FER de 0,8 num determinado momento, mas as avaliações posteriores revelarem um aumento para além de 1, isso evidencia a necessidade de uma intervenção imediata para garantir a segurança.
Método de avaliação de defeitos
Para avaliar a aptidão da tubagem para o serviço, temos de avaliar os defeitos para determinar a tolerância à corrosão. Com isto, podemos então calcular a vida útil restante da tubagem e a data da próxima inspeção. Dois métodos principais dominam este campo:ASME B31GeDNV RP-F101.
A ASME B31Gfoi a primeira a enfrentar o desafio de calcular a pressão de trabalho segura na presença de defeitos. Inclui a norma original, que define a tensão de escoamento como 1,1 vezes a tensão de cedência mínima especificada (SMYS), e uma versão modificada que a refina para SMYS mais 69 MPa adicionais (cerca de 10 KSI) para maior precisão.
Por outro lado, aDNV RP-F101, introduzida em 2010, centra-se na resistência à tração final (UTS), prevendo a falha a 0,9 vezes a UTS. Esta norma simplifica as formas dos defeitos, tratando-os como rectangulares, enquanto a ASME B31G originalmente aproximava os defeitos como parabólicos, mas mais tarde permitiu formas arbitrárias.
Outro aspeto crítico é ofator de abaulamento, que mede a forma como os defeitos se deformam sob pressão. Os defeitos mais pequenos diminuem a sua importância, enquanto os maiores a amplificam.
Para visualizar as pressões de trabalho seguras, ambas as normas utilizam oDiagrama de Avaliação de Falhas (FAD), que traduz a equação da Pressão de Trabalho Segura (PSW = f x 2tσflow / (D - t) x ((1 - A / A0) / 1 - (A / A0 x 1 / M)) num formato gráfico que representa o comprimento do defeito em função da profundidade. Os pontos abaixo da curva indicam condições seguras, enquanto os pontos acima indicam potenciais riscos de falha.
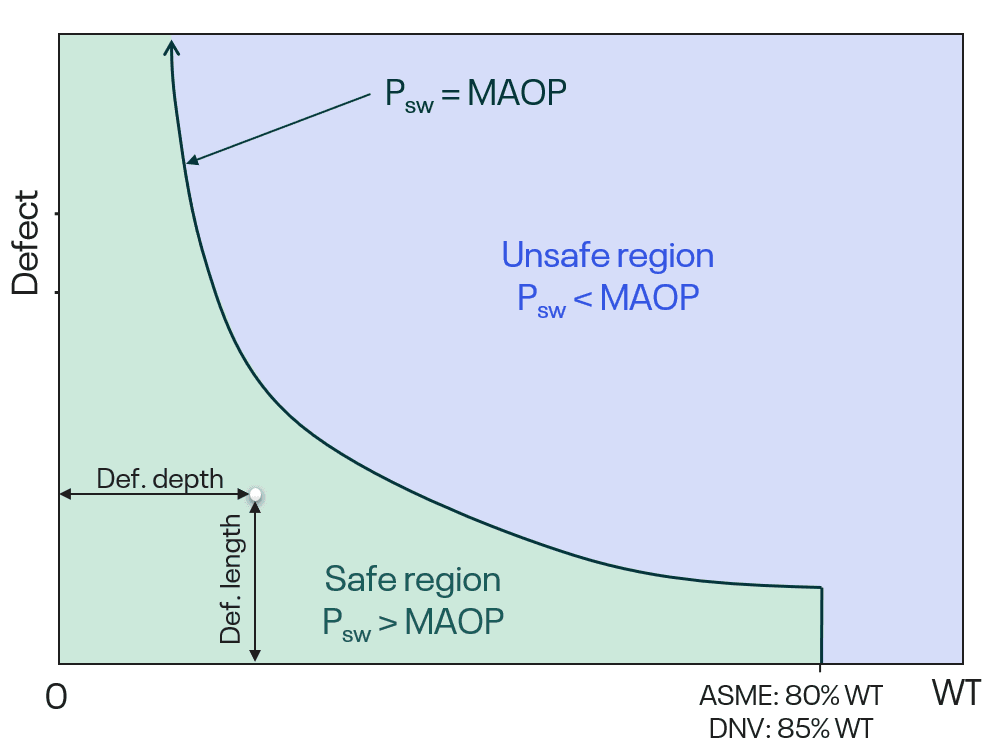
Ao avaliar os defeitos dos relatórios de Inspeção em Linha (ILI), é essencial considerar as profundidades máximas permitidas - 80% da Espessura da Parede (WT) para ASME e 85% para DNV. Exceder estes limites torna os defeitos inseguros.
Regras de interação de defeitos
No mundo dos pipelines, os defeitos raramente estão isolados. Muitas vezes, eles se agrupam, criando uma rede complexa de potenciais pontos fracos. A norma ASME B31G avalia os defeitos individualmente, mas reconhece que os defeitos espaçados podem interagir como um único defeito maior se estiverem dentro de um intervalo de três vezes a espessura nominal da parede (3t). Esta interação pode comprometer significativamente a integridade estrutural.
Em contraste, a DNV RP-F101 avalia cada defeito individualmente e considera combinações de defeitos adjacentes que interagem. Considera-se que os defeitos interagem se a sua distância axial for inferior a um limiar específico baseado no diâmetro do tubo e na espessura da parede. Este critério ajuda a identificar quais defeitos podem influenciar uns aos outros.
O método DNV RP-F101 envolve um processo estruturado em três etapas:
- Seccionamento da tubagem: A tubagem é dividida circunferencialmente em secções com base na fórmula√(D/t), em queDé o diâmetro eté a espessura da parede. Esta divisão permite uma abordagem estruturada para analisar defeitos.
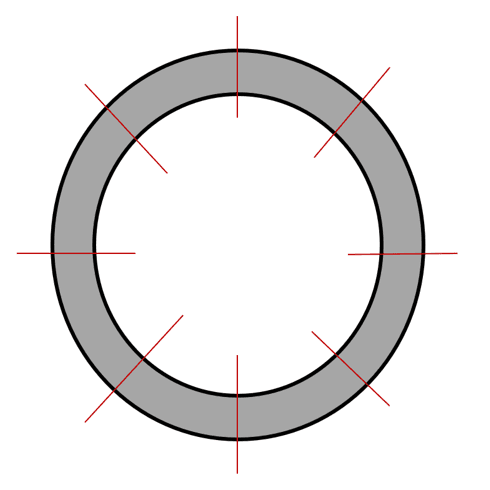
- Projeção de defeitos: Para cada linha de projeção correspondente a estas secções, os defeitos das secções vizinhas são mapeados para as linhas. Por exemplo, se um defeito estiver localizado na primeira secção, será projetado na primeira e na segunda linhas. Se existirem defeitos na segunda secção, estes serão projectados na segunda e terceira linhas. Na DNV RP-F101 2010, os defeitos internos e externos sobrepostos também interagem. A profundidade resultante para a combinação é di=d1+d2.
- Cálculo da pressão de trabalho segura: A Psw é calculada para todas as combinações possíveis destes defeitos em interação. A Psw mais baixa entre estes cálculos torna-se a pressão de trabalho segura para o tubo corroído.
Na versão de 2010 da DNV RP-F101, os defeitos sobrepostos eram tratados como um único defeito com um comprimento combinado desde o início do primeiro defeito até ao fim do último defeito no grupo, utilizando a profundidade do defeito mais profundo dentro desse grupo. No entanto, na atualização de 2015, os defeitos sobrepostos não são encaixotados num único defeito; em vez disso, as suas contribuições individuais são consideradas separadamente no cálculo da pressão de trabalho segura.
Compreender a tolerância à corrosão
À medida que nos aprofundamos nas avaliações de integridade das condutas, deparamo-nos com o conceito detolerância à corrosão - acorrosão máxima permitida que uma conduta pode suportar enquanto continua a ser considerada apta para o serviço. Este conceito está interligado com oestado limite, definindo quando uma tubagem se torna insegura para operar.
Cálculo da tolerância à corrosão em casos sem defeitos
Quando uma tubagem não tem defeitos, os operadores devem antecipar os potenciais tipos de corrosão - seja corrosão geral, ranhuras ou corrosão por picadas. Por exemplo, se for esperadacorrosão por pite, os engenheiros podem estimar o comprimento dos defeitos potenciais como 20 vezes a profundidade da corrosão. Esta relação permite-lhes traçar uma linha no diagrama de Avaliação de Falhas a partir da origem (0,0) com base neste rácio comprimento/profundidade. A intersecção desta linha com a curva de segurança revela a Tolerância de Corrosão (CT) e a Espessura Mínima Admissível (MAT) - na imagem seguinte, a CT e a MAT são indicadas para a corrosão em sulcos.
Em contraste, se for assumida a corrosão geral, o seu comprimento pode ser representado como 1.000 vezes a espessura da parede (WT). Este método produz normalmente uma tolerância de corrosão mais baixa, uma vez que a corrosão por picadas pode levar a uma perda de material mais profunda do que a corrosão geral. Por conseguinte, a identificação exacta do tipo de corrosão esperado é crucial para determinar as tolerâncias adequadas.
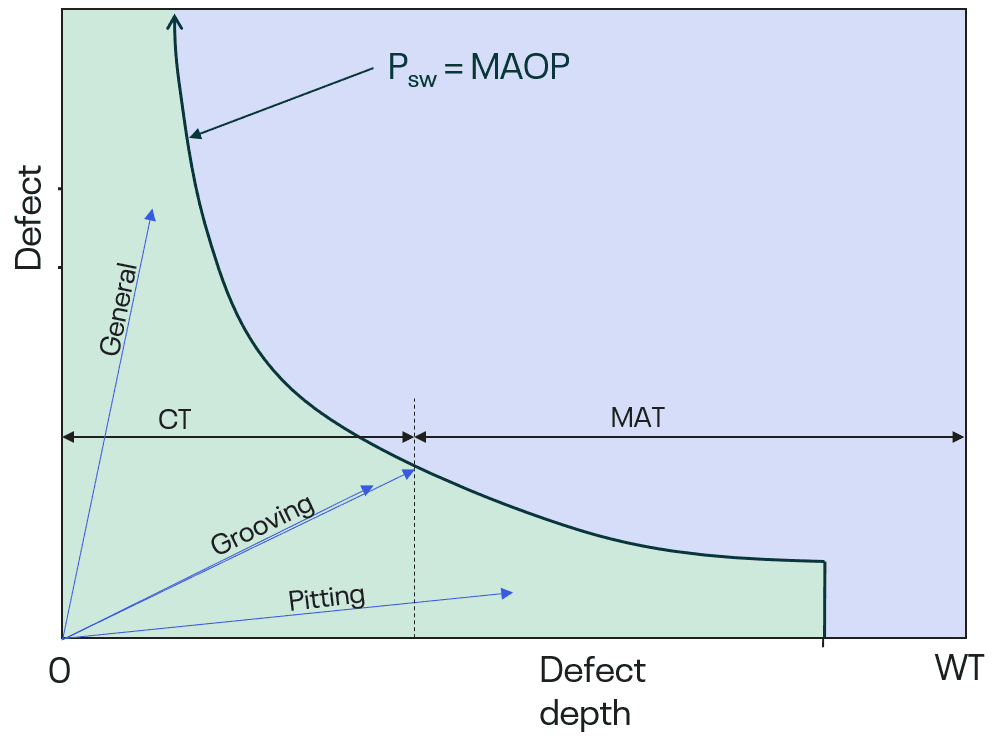
Cálculo da tolerância à corrosão em casos com defeitos
Quando os defeitos estão presentes, a avaliação torna-se mais matizada. Os operadores podem desenhar linhas no Diagrama de Avaliação de Falhas a partir de (0,0) através de cada defeito para determinar as respectivas tolerâncias. A distância entre a intersecção destas linhas com a curva de segurança e a intersecção do defeito com o eixo x indica as Tolerâncias de Corrosão (CT) no momento da execução da Inspeção em Linha (ILI).
A Tolerância à Corrosão (CT) é calculada para cada defeito. Com aASME B31G, esta avaliação é simples; cada defeito é submetido a um único cálculo. No entanto,a norma DNV RP-F101complica as coisas com o seu processo iterativo - os defeitos podem ser avaliados várias vezes se interagirem. Esta complexidade torna-se particularmente evidente quando se lida com grandes conjuntos de dados.
A interação dos defeitos
Quando dois defeitos estão suficientemente próximos para interagir, partilham uma Tolerância à Corrosão (CT) comum devido aos seus efeitos combinados na integridade da tubagem. Esta interação deve ser cuidadosamente avaliada para garantir que os cálculos da Pressão de Trabalho Segura (Psw) permanecem válidos e que a conduta continua a funcionar em segurança.
Determinar a vida útil da tubagem e os próximos passos para a inspeção
Tal como mencionado no início deste artigo, uma avaliação da aptidão para o serviço não só determina se uma conduta é adequada para o funcionamento, mas também estima durante quanto tempo pode continuar a funcionar em segurança. Depois de calcularmos a nossa Tolerância à Corrosão (CT) com a ajuda da Curva de Avaliação de Falhas, podemos então estimar a vida útil restante da conduta e calcular quando inspecionar novamente a conduta.
- Para encontrar a vida útil restante, dividimos a Tolerância à Corrosão (CT) pela Taxa de Corrosão (CR). Por exemplo, se uma tubagem tiver uma Tolerância à corrosão de 2 mm e uma Taxa de corrosão de 0,1 mm por ano, o cálculo será o seguinte:
Vida útil restante = CT / CR = 2 mm / 0,1 mm ano = 20 anos
Isto significa que, nas condições actuais, a conduta pode funcionar em segurança durante mais 20 anos antes de atingir o seu limite de corrosão.
- Para determinar quando deve ocorrer a próxima inspeção, precisamos do Fator de Intervalo (IF) derivado de umaAvaliação Baseada no Risco (RBA), que avalia a criticidade e as potenciais consequências das falhas. A fórmula para calcular o intervalo da próxima inspeção é a seguinte
Intervalo da próxima inspeção = Vida restante × IF
Utilizando o nosso exemplo anterior, se assumirmos um fator interno de 0,3, o cálculo seria o seguinte:
Próximo intervalo de inspeção = 20 anos × 0,3 = 6 anos
Isto indica que a conduta deve ser inspeccionada novamente dentro de 6 anos para garantir que continua a estar apta para o serviço.
Avaliação da aptidão do pipeline para o serviço com o IMS PLSS
Na gestão de condutas, as avaliações de aptidão para serviço (FFS) são essenciais para garantir a segurança e o funcionamento contínuo de infra-estruturas envelhecidas. Estas avaliações não só determinam se uma conduta pode permanecer em serviço, como também fornecem informações sobre o seu tempo de vida útil restante.
A análise de dados surge como o coração deste processo, ajudando os operadores a prever o desempenho e a programar as inspecções com base no cálculo da vida útil restante. O IMS - Pipeline and Subsea Systems (PLSS) da Cenoco permite que os operadores avaliem a adequação da tubulação, oferecendo informações sobre a vida útil restante. Usando metodologias como ASME B31G e DNV RP-F101, os operadores podem avaliar com precisão os defeitos e calcular as tolerâncias de corrosão. A análise da relação entre defeitos, tensão de aro e pressões de trabalho seguras suporta uma gestão proactiva das condutas.
O PLSS permite aos utilizadores avaliar os dados ILI através do módulo Fitness for Service, mostrando a pressão de trabalho segura e o fator de reparação estimado para cada defeito. A sua força reside no cálculo da Tolerância de Corrosão para defeitos individuais ou agrupados, tendo em conta o grau do material, o tamanho do defeito e a profundidade. O módulo de Avaliação Baseada no Risco calcula a Vida Restante da tubagem e a data da próxima inspeção, com a opção de agendar e registar os resultados da inspeção no Histórico de Condição. Este sistema suporta avaliações de Adequação ao Serviço para tubagens, linhas de fluxo e jumpers feitos de aço carbono e ligas resistentes à corrosão.
O PLSS aborda os defeitos mais comuns das condutas em serviço, especificamente a corrosão volumétrica que pode levar ao colapso plástico. Concentra-se em avaliações de Nível 1 essenciais, mas simples, como a ASME B31G e a DNV RP-F101 Parte B. Esta abordagem simplificada permite que os operadores dêem prioridade a considerações económicas. Uma avaliação mais pormenorizada fora do PLSS é recomendada para condutas altamente críticas ou condutas sujeitas a regulamentos rigorosos.
Em conclusão, o PLSS é altamente eficaz para gerir condições conhecidas e controladas que envolvem defeitos de corrosão volumétrica sob carga de pressão circular.
Quer saber mais sobre a IMS?
Solicite uma demonstração abaixo para obter uma visão em primeira mão das suas capacidades!
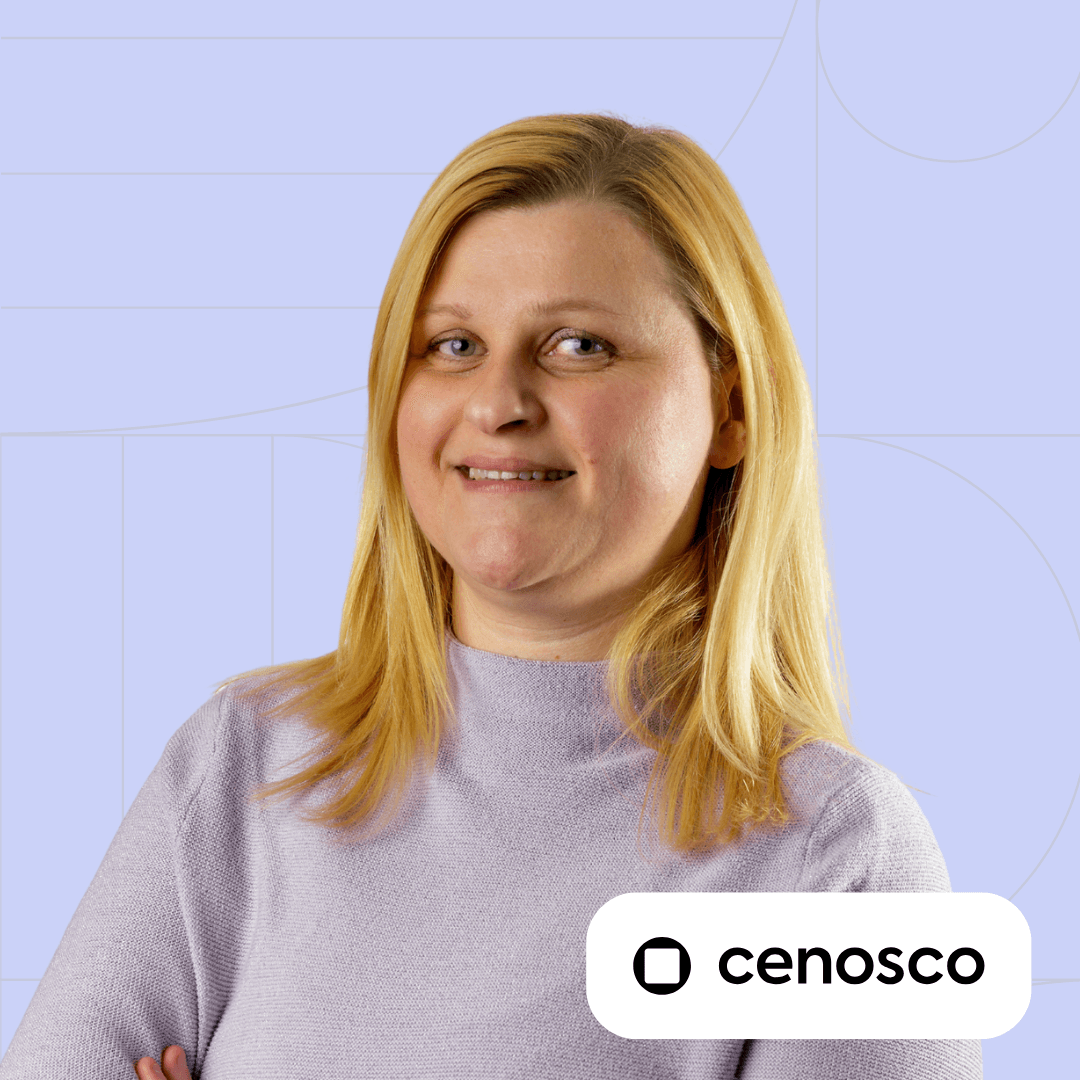
Denis Tkalec Technical writer
Denis Tkalec is a technical writer at Cenosco, specializing in asset integrity management software since 2022. With a background in education and six years in marketing, she turns complex topics into clear, user-friendly content. Inspired by Camus’s belief that “a writer keeps civilization from destroying itself,” she brings precision and care to every manual.