In einem kürzlich erschienenen Blog haben wir uns mit der Optimierung der Ressourcenzuweisung bei der Umsetzung der zuverlässigkeitsorientierten Instandhaltung (RCM) befasst, um die Entwicklung eines effektiven Inspektions- und Wartungsplans zu unterstützen. Wir sprachen über den Ursprung von RCM und die sieben Fragen des RCM. Im heutigen Beitrag gehen wir tiefer in die Grundlagen des RCM ein und sprechen über die Sieben Fragen der zuverlässigkeitsorientierten Instandhaltung (RCM).
Veränderte Perspektiven der Instandhaltung
Mit der zunächst langsamen, dann schnellen Industrialisierung der Welt zu Beginn des 20. Jahrhunderts wurde die Produktion von Gütern zunehmend von Maschinen abhängig. Dies war auf viele Faktoren zurückzuführen, u. a. auf Fortschritte in der Fertigungstechnologie und den Arbeitskräftemangel während des Zweiten Weltkriegs.
Reaktive Wartung
Die Industrieanlagen wurden zunehmend mechanisiert, und die Bedeutung von Wartungsprogrammen nahm zu, da sichergestellt werden musste, dass Produktionsunterbrechungen aufgrund von Maschinenausfällen auf ein Minimum reduziert wurden. Zunächst konzentrierten sich die Wartungsprogramme auf reaktive Ansätze zur Reparatur von Maschinen, nachdem diese ausgefallen waren.
Proaktive Wartung
Mit der Zeit wurde die industrielle Produktion durch Ansätze wie die Just-in-time-Lieferung effizienter. Diese innovativen Ansätze hatten den Vorteil, dass sie die Lagerbestände verringerten und effizientere Lieferketten ermöglichten, aber sie bedeuteten auch, dass selbst ein relativ kleiner Fehler in einem Teil des Produktionsprozesses die industrielle Produktion erheblich beeinträchtigen konnte.
Als Reaktion auf diese neuen Herausforderungen wandten sich die industriellen Wartungsprogramme einem proaktiveren Wartungsansatz zu, der auf der Überzeugung beruhte, dass die Wahrscheinlichkeit eines Ausfalls umso größer ist, je länger die Anlagen in Betrieb sind. Die Wartungsprogramme stützten sich auf zeitbasierte Wartung und Überholung. Dieser Ansatz dominierte in den 1960er und 1970er Jahren.
Neue Theorien des Scheiterns
Neue Forschungen im Bereich der Industrietechnik in den 1960er und 1970er Jahren zeigten, dass das frühere Verständnis von Geräteausfällen nicht vollständig war. Man verstand nun, dass verschiedene Anlagentypen unterschiedliche Ausfallarten haben und dass ein einheitlicher Ansatz für die Instandhaltung zu Kapitalverschwendung und unnötigen Ausfallzeiten führt.
Die sieben Fragen der zuverlässigkeitsorientierten Instandhaltung
In den 1970er Jahren begann die US-amerikanische Luft- und Raumfahrtindustrie, ihre Wartungsprogramme genauer unter die Lupe zu nehmen, und entwickelte Verfahren, um die bisherige zeitbasierte Wartung von Flugzeugkomponenten zu ersetzen. United Airlines schrieb mit Unterstützung des US-Verteidigungsministeriums eines der ersten Lehrbücher über diesen neuen Ansatz, der als "Reliability Centered Maintenance" bekannt wurde.
Dieser Ansatz wurde in der SAE-Norm JA1011 und später in der IEC 60300 kodifiziert. Im Kern dreht sich die zuverlässigkeitsorientierte Instandhaltung um sieben Schlüsselfragen, die bei der Identifizierung und Umsetzung effektiver Instandhaltungsaufgaben helfen. Im Folgenden werden diese sieben Fragen anhand eines konkreten Beispiels vertieft.
1. Was sind die Funktionen und die damit verbundenen Leistungsstandards der Anlage?
Der erste Schritt im RCM besteht darin, die Funktionen der Anlage und die mit diesen Funktionen verbundenen Leistungsstandards zu verstehen. Dazu gehört, dass man definiert, was die Anlage tun soll, und die Kriterien dafür festlegt, ob sie diese Aufgabe gut erfüllt. Die Funktion einer Flüssigkeitspumpe in einer chemischen Anlage könnte beispielsweise darin bestehen, das Produkt mit einer bestimmten Geschwindigkeit von einem Teil der Anlage zu einem anderen zu transportieren. Der Leistungsstandard könnte die Fähigkeit sein, ein bestimmtes Flüssigkeitsvolumen pro Stunde ohne Ausfall zu befördern.
2. Auf welche Weise kann sie ihre Funktionen nicht erfüllen?
Der nächste Schritt besteht darin, die verschiedenen Möglichkeiten zu ermitteln, wie die Anlage ihre Funktionen nicht erfüllen kann. Dies kann ein kompletter Ausfall, ein Teilausfall oder eine verminderte Leistung sein. Die Pumpe könnte beispielsweise vollständig ausfallen (nicht mehr funktionieren), teilweise ausfallen (mit Unterbrechungen arbeiten) oder in ihrer Leistung nachlassen (langsamer werden).
3. Was sind die Ursachen der einzelnen Funktionsstörungen?
Es ist wichtig, die Ursachen für jeden Funktionsausfall zu ermitteln. Diese können auf Verschleiß, unsachgemäßen Gebrauch, Umweltbedingungen oder Konstruktionsfehler zurückzuführen sein. In unserem Pumpenbeispiel könnten die Ursachen verschlissene Laufräder oder Lager, zu große Förderhöhenunterschiede, extreme Temperaturen oder ein Konstruktionsfehler sein, der zu häufigen Ausfällen führt.
4. Was passiert, wenn ein Fehler auftritt?
Das Wissen um die Folgen eines jeden Fehlers hilft bei der Priorisierung von Wartungsaufgaben. Die Auswirkungen können von kleineren Störungen bis hin zu größeren Systemausfällen reichen. Wenn unsere Pumpe ausfällt, kann dies zu einer Verlangsamung der Produktion oder im Extremfall zum Stillstand der gesamten Produktionslinie führen.
5. Inwiefern ist jedes Scheitern von Bedeutung?
Jeder Ausfall ist auf seine eigene Weise von Bedeutung. Einige Störungen können Auswirkungen auf die Sicherheit haben, andere können die Produktion beeinträchtigen und wieder andere können zu höheren Wartungskosten führen. Der Ausfall unserer Pumpe ist wichtig, weil er sich direkt auf die Produktionseffizienz auswirkt. Ein Ausfall könnte zu erhöhten Betriebskosten, Ausfallzeiten oder Produktverschwendung führen.
6. Was kann getan werden, um jedes Versagen vorherzusagen oder zu verhindern?
Vorausschauende und präventive Wartungsstrategien können eingesetzt werden, um jeden Ausfall zu bewältigen. Dies könnte regelmäßige Inspektionen, Zustandsüberwachung, den Austausch von Komponenten oder die Umgestaltung von Teilen des Systems beinhalten. Bei der Pumpe könnten die Überwachung von Schwingungen und Temperaturen, regelmäßige Inspektionen und der rechtzeitige Austausch verschlissener Teile dazu beitragen, Ausfälle vorherzusagen und zu verhindern.
7. Was ist zu tun, wenn keine geeignete proaktive Aufgabe gefunden werden kann?
Wenn keine geeignete proaktive Maßnahme gefunden werden kann, ist möglicherweise ein reaktiver Ansatz erforderlich. Dazu könnte gehören, die Anlage bis zum Ausfall zu betreiben und sie dann zu reparieren oder zu ersetzen. Wenn proaktive Maßnahmen im Falle unserer Pumpe nicht durchführbar oder kosteneffizient sind, könnten die Optionen darin bestehen, die Pumpe bis zum Ausfall laufen zu lassen und sie dann zu reparieren oder zu ersetzen oder eine Reservepumpe bereitzuhalten.
RCM ist mehr als nur sieben Fragen
Die Sieben Fragen des RCM bilden die Grundlage der zuverlässigkeitsorientierten Instandhaltung (RCM). Um RCM in einem Unternehmen effektiv umzusetzen, ist es jedoch unerlässlich, zusätzliche Werkzeuge und Konzepte zu verstehen. Einige wichtige Grundlagen und Best Practices für die Implementierung von RCM sind:
- Identifizierung von Fehlerquellen: Dazu gehört das Verständnis der Funktion und der Fehlermöglichkeiten von Anlagen und deren Folgen.
- Auswahl der richtigen Instandhaltungsstrategie: Einsatz von Werkzeugen wie Entscheidungslogikbäumen, Risikomatrix und Kosten-Nutzen-Analyse zur Auswahl der am besten geeigneten Instandhaltungsstrategie für jede Anlage.
- Umsetzung und Überwachung des Wartungsplans: Festlegung von Wartungsaufgaben, -intervallen, -ressourcen und Leistungsindikatoren für jede Anlage und Sammlung/Analyse von Daten über den Zustand der Anlage und die Ausfallraten.
- Nutzung von Technologie und Daten: RCM-Software kann den RCM-Prozess durch die Organisation von Daten, die Durchführung von Analysen und die Verfolgung von Leistungs- und Zuverlässigkeitsindikatoren rationalisieren.
Darüber hinaus ist es für eine erfolgreiche RCM-Implementierung wichtig, die Systemgrenzen zu definieren, den Ressourcenbedarf zu ermitteln und die Beteiligten einzubinden und zu schulen. Wenn Unternehmen diese Konzepte verstehen und die richtigen Werkzeuge einsetzen, können sie durch eine effektive RCM-Implementierung Kosten senken, die Sicherheit verbessern und die Kundenzufriedenheit steigern.
Treffen Sie IMS RCM
IMS RCM ist die Cloud-basierte Software von Cenosco für die zuverlässigkeitsorientierte Instandhaltung. Sie hilft, ungeplante Ausfälle zu vermeiden, indem sie die Verfügbarkeit von Anlagen durch Wartung verbessert. Sie brauchen keinen teuren Wartungsplan, um die Sicherheit Ihrer Mitarbeiter und eine hohe Anlagenverfügbarkeit zu gewährleisten. Mit IMS RCM optimieren Sie Ihre Wartungsaufgaben, damit Sie so sicher und budgetfreundlich wie möglich arbeiten können.
Verbessern Sie die Verfügbarkeit Ihrer Anlagen durch Instandhaltung.
Im Folgenden stellen wir Ihnen einige der wichtigsten Funktionen von IMS RCM vor. Entdecken Sie die vielen Möglichkeiten, wie unsere RCM-Software Ihnen helfen kann, die Kontrolle über Ihren Betrieb zu gewinnen.
- Exklusiver Zugang zu einer mit Shell erstellten Bibliothek für Zuverlässigkeitsstrategien
- Dynamische Formulare
- Optimierung der Gerätepflege verwalten
- Effizienzindex für die Instandhaltung
- Änderung und Aufschub
- ... so viel mehr
Demo anfordern
Möchten Sie mehr über IMS RCM erfahren? Füllen Sie das untenstehende Formular aus, um mehr zu erfahren.
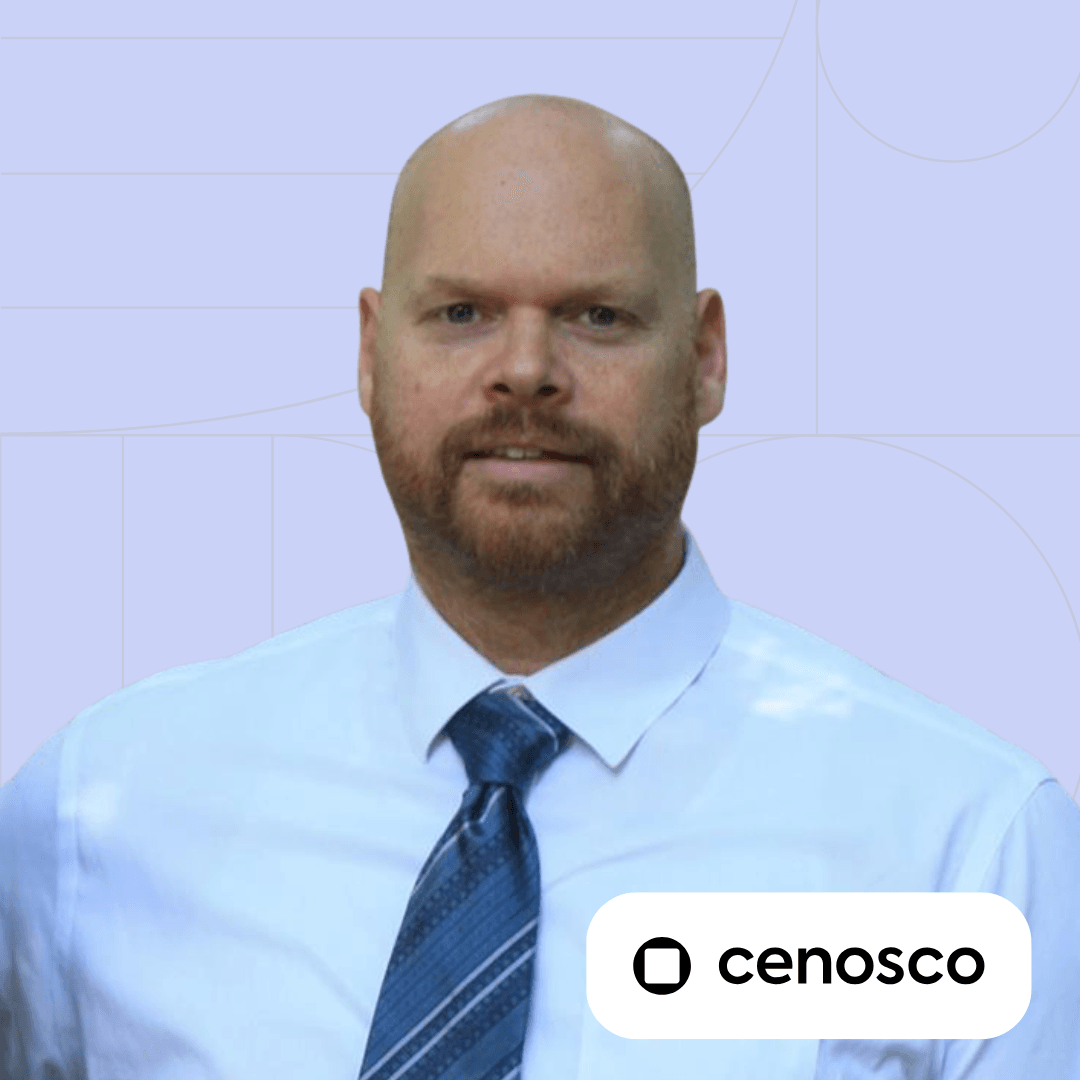
Tomislav Renić Technical Writer
Tomislav is an experienced engineer and technical communicator with over 20 years in complex systems, modeling, and project management. As a Technical Writer at Cenosco, he translates engineering concepts into clear, user-friendly documentation for software in the oil, gas, and refining industries.