En un blog reciente, abordamos el tema de la Optimización de la Asignación de Recursos al implantar el Mantenimiento Centrado en la Fiabilidad (RCM) para ayudar a desarrollar un plan eficaz de inspección y mantenimiento. Tocamos el origen del RCM y las Siete Preguntas del RCM. En el post de hoy, profundizamos en los fundamentos del RCM y hablamos de las Siete Preguntas del Mantenimiento Centrado en la Confiabilidad (RCM).
Cambiar las perspectivas del mantenimiento
A medida que el mundo se industrializaba, primero lentamente y después con rapidez, a principios del siglo XX, la producción de bienes dependía cada vez más de la maquinaria. Esto se debió a muchos factores, como los avances en la tecnología de fabricación y la escasez de mano de obra durante la Segunda Guerra Mundial.
Mantenimiento reactivo
Las instalaciones industriales se mecanizaron cada vez más y los programas de mantenimiento adquirieron mayor importancia debido a la necesidad de garantizar que las interrupciones de la fabricación se redujeran al mínimo por fallos de los equipos. Al principio, los programas de mantenimiento se centraban en enfoques reactivos para reparar la maquinaria después de que hubiera fallado.
Mantenimiento proactivo
Con el tiempo, la producción industrial se hizo más eficiente a través de enfoques como la entrega justo a tiempo. Estos enfoques innovadores tenían la ventaja de reducir los inventarios y permitir cadenas de suministro más eficientes, pero también significaba que incluso un fallo relativamente pequeño en una parte del proceso de producción podía afectar significativamente a la producción industrial.
En respuesta a estos nuevos retos, los programas de mantenimiento industrial adoptaron un enfoque de mantenimiento más proactivo basado en la creencia de que cuanto más tiempo estuvieran en servicio los equipos, más probabilidades tendrían de fallar. Los programas de mantenimiento se basaban en el mantenimiento basado en el tiempo y las revisiones. Este enfoque dominó durante las décadas de 1960 y 1970.
Nuevas teorías del fracaso
Los nuevos estudios de ingeniería industrial de los años sesenta y setenta demostraron que los conocimientos previos sobre los fallos de los equipos no eran completos. Ahora se comprendía que los distintos tipos de equipos tenían diferentes modos de fallo y que un enfoque único del mantenimiento provocaba un despilfarro de capital y tiempos de inactividad innecesarios.
Las siete preguntas del mantenimiento centrado en la fiabilidad
En la década de 1970, la industria aeroespacial estadounidense empezó a estudiar más detenidamente sus programas de mantenimiento y desarrolló procesos para sustituir el anterior mantenimiento de los componentes de los aviones basado en el tiempo. United Airlines, con el apoyo del Departamento de Defensa de EE.UU., escribió uno de los primeros libros de texto sobre este novedoso enfoque, conocido como mantenimiento centrado en la fiabilidad.
Este enfoque se codificó en la norma SAE JA1011 y, posteriormente, en la IEC 60300. En esencia, el mantenimiento centrado en la fiabilidad gira en torno a siete preguntas clave que ayudan a identificar y aplicar tareas de mantenimiento eficaces. A continuación, profundizamos en estas siete preguntas con un ejemplo concreto.
1. ¿Cuáles son las funciones y las normas de rendimiento asociadas del activo?
El primer paso de la GCR es comprender las funciones del activo y las normas de rendimiento asociadas a dichas funciones. Esto implica definir lo que se supone que debe hacer el activo y los criterios para determinar si lo está haciendo bien. Por ejemplo, la función de una bomba de fluidos en una planta química podría ser transportar el producto de una parte de la planta a otra a una velocidad determinada. La norma de rendimiento podría ser la capacidad de transportar un volumen específico de fluido por hora sin fallos.
2. ¿De qué manera puede incumplir sus funciones?
El siguiente paso consiste en identificar las distintas formas en que el activo puede dejar de cumplir sus funciones. Esto puede incluir un fallo completo, un fallo parcial o una degradación del rendimiento. Por ejemplo, la bomba podría fallar completamente (deja de funcionar), parcialmente (funciona de forma intermitente) o su rendimiento podría degradarse (se ralentiza).
3. ¿Cuáles son las causas de cada fallo funcional?
Identificar las causas de cada fallo funcional es crucial. Pueden deberse a desgaste, uso inadecuado, condiciones ambientales o defectos de diseño. En el ejemplo de nuestra bomba, las causas podrían ser el desgaste de impulsores o cojinetes, diferencias de altura excesivas, exposición a temperaturas extremas o un defecto de diseño que la haga susceptible de averías frecuentes.
4. ¿Qué ocurre cuando se produce cada fallo?
Comprender las consecuencias de cada fallo ayuda a priorizar las tareas de mantenimiento. Las repercusiones pueden ir desde pequeñas interrupciones hasta importantes averías del sistema. Si nuestra bomba falla, puede provocar una ralentización de la producción o, en casos extremos, detener toda la línea de producción.
5. ¿Qué importancia tiene cada fracaso?
Cada fallo tiene una importancia única. Algunos fallos pueden tener implicaciones de seguridad, otros pueden afectar a la producción y algunos pueden suponer mayores costes de mantenimiento. El fallo de nuestra bomba es importante porque afecta directamente a la eficacia de la producción. Un fallo puede provocar un aumento de los costes operativos, tiempo de inactividad o pérdida de producto.
6. ¿Qué se puede hacer para predecir o prevenir cada fallo?
Se pueden emplear estrategias de mantenimiento predictivo y preventivo para gestionar cada fallo. Esto podría implicar inspecciones periódicas, control del estado, sustitución de componentes o rediseño de partes del sistema. En el caso de la bomba, el control de las vibraciones y la temperatura, las inspecciones periódicas y la sustitución a tiempo de las piezas desgastadas pueden ayudar a predecir y evitar averías.
7. ¿Qué debe hacerse si no se encuentra una tarea proactiva adecuada?
Si no se encuentra una tarea proactiva adecuada, puede ser necesario un enfoque reactivo. Esto podría implicar hacer funcionar el activo hasta que falle y luego repararlo o sustituirlo. En el caso de nuestra bomba, si las tareas proactivas no son factibles o rentables, las opciones podrían ser hacerla funcionar hasta que falle y luego repararla o sustituirla, o tener una bomba de reserva lista para el servicio.
RCM es más que siete preguntas
Las Siete Preguntas de RCM constituyen la base del Mantenimiento Centrado en la Fiabilidad (RCM). Sin embargo, para implantar eficazmente el RCM en una organización, es esencial comprender herramientas y conceptos adicionales. Algunos fundamentos clave y mejores prácticas para implementar el RCM incluyen:
- Identificación de los puntos de fallo: Se trata de comprender el funcionamiento y los modos de fallo de los activos, así como sus consecuencias.
- Selección de la estrategia de mantenimiento adecuada: Utilización de herramientas como árboles lógicos de decisión, matriz de riesgos y análisis coste-beneficio para elegir la estrategia de mantenimiento más adecuada para cada activo.
- Ejecución y supervisión del plan de mantenimiento: Definición de tareas de mantenimiento, intervalos, recursos e indicadores de rendimiento para cada activo, y recogida/análisis de datos sobre el estado de los activos y los índices de avería.
- Aprovechar la tecnología y los datos: El software de RCM puede agilizar el proceso de RCM mediante la organización de datos, la realización de análisis y el seguimiento de los indicadores de rendimiento y fiabilidad.
Además, es importante definir los límites del sistema, identificar las necesidades de recursos e implicar y formar a las partes interesadas para implantar con éxito la RCM. Comprendiendo estos conceptos y utilizando las herramientas adecuadas, las organizaciones pueden reducir costes, mejorar la seguridad y aumentar la satisfacción del cliente implantando eficazmente la RCM.
Conozca IMS RCM
IMS RCM es el software basado en la nube de mantenimiento centrado en la fiabilidad de Cenosco. Ayuda a prevenir fallos imprevistos mejorando la disponibilidad de los activos mediante el mantenimiento. No necesita tener un costoso plan de mantenimiento para garantizar la seguridad de su personal y una alta disponibilidad de los activos. Con IMS RCM, optimizará sus tareas de mantenimiento para que pueda operar de la forma más segura y económica posible.
Mejore la disponibilidad de sus activos mediante el mantenimiento.
A continuación presentamos algunas de las características clave de IMS RCM. Explore las muchas formas en que nuestro software RCM puede ayudarle a obtener el control de sus operaciones.
- Acceso exclusivo a una biblioteca de estrategias de fiabilidad creada con Shell
- Formularios dinámicos
- Gestionar la optimización del cuidado de los equipos
- Índice de eficacia del mantenimiento
- Cambio y aplazamiento
- ... mucho más
Solicitar una demostración
¿Está preparado para obtener más información sobre IMS RCM? Rellene el siguiente formulario para obtener más información.
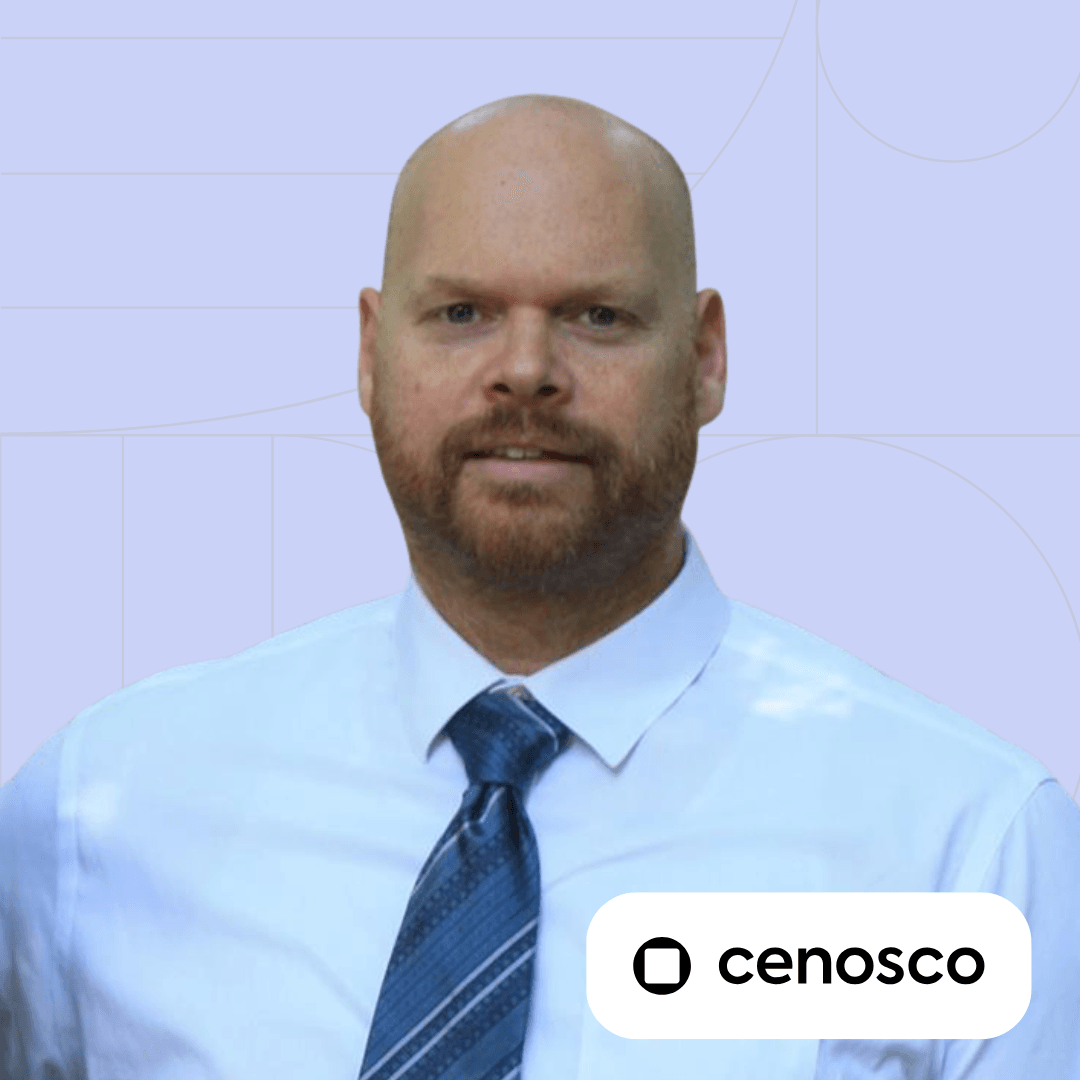
Tomislav Renić Technical Writer
Tomislav is an experienced engineer and technical communicator with over 20 years in complex systems, modeling, and project management. As a Technical Writer at Cenosco, he translates engineering concepts into clear, user-friendly documentation for software in the oil, gas, and refining industries.