Dans un récent blog, nous avons abordé le sujet de l'optimisation de l'allocation des ressources lors de la mise en œuvre de la maintenance axée sur la fiabilité (RCM) pour aider à élaborer un plan d'inspection et de maintenance efficace. Nous avons évoqué l'origine de la RCM et les sept questions qu'elle soulève. Dans l'article d'aujourd'hui, nous approfondissons les principes fondamentaux de la RCM et abordons les sept questions de la maintenance axée sur la fiabilité (RCM).
Changer les perspectives sur la maintenance
Alors que le monde s'est industrialisé, d'abord lentement, puis rapidement, au début du XXe siècle, la production de biens est devenue de plus en plus dépendante des machines. Cette évolution est due à de nombreux facteurs, dont les progrès de la technologie de fabrication et les pénuries de main-d'œuvre pendant la Seconde Guerre mondiale.
Maintenance réactive
Les installations industrielles sont devenues plus mécanisées et les programmes de maintenance ont pris de l'importance en raison de la nécessité de réduire au minimum les interruptions de production dues aux pannes d'équipement. Dans un premier temps, les programmes de maintenance se sont concentrés sur des approches réactives visant à réparer les machines après qu'elles soient tombées en panne.
Maintenance proactive
Avec le temps, la production industrielle est devenue plus efficace grâce à des approches telles que la livraison juste à temps. Ces approches innovantes ont eu l'avantage de réduire les stocks et de permettre des chaînes d'approvisionnement plus efficaces, mais elles ont également signifié que même une défaillance relativement faible dans une partie du processus de production pouvait avoir un impact significatif sur la production industrielle.
En réponse à ces nouveaux défis, les programmes de maintenance industrielle se sont tournés vers une approche de maintenance plus proactive, basée sur la conviction que plus l'équipement est en service longtemps, plus il est susceptible de tomber en panne. Les programmes de maintenance s'appuyaient sur une maintenance et des révisions basées sur le temps. Cette approche a dominé les années 1960 et 1970.
Nouvelles théories de l'échec
De nouvelles recherches en génie industriel menées dans les années 1960 et 1970 ont montré que la compréhension antérieure des défaillances des équipements n'était pas complète. On comprenait désormais que les différents types d'équipements avaient des modes de défaillance différents et qu'une approche unique de la maintenance entraînait un gaspillage de capital et des temps d'arrêt inutiles.
Les sept questions de la maintenance centrée sur la fiabilité
Au cours des années 1970, l'industrie aérospatiale américaine a commencé à examiner de plus près ses programmes de maintenance et a mis au point des processus pour remplacer la maintenance des composants d'avion basée sur le temps. United Airlines, avec le soutien du ministère américain de la défense, a rédigé l'un des premiers manuels sur cette nouvelle approche, connue sous le nom de "Reliability Centered Maintenance" (maintenance axée sur la fiabilité).
Cette approche a été codifiée dans la norme SAE JA1011, puis dans la norme IEC 60300. La maintenance axée sur la fiabilité s'articule autour de sept questions clés qui permettent d'identifier et de mettre en œuvre des tâches de maintenance efficaces. Ci-dessous, nous approfondissons ces sept questions à l'aide d'un exemple spécifique.
1. Quelles sont les fonctions et les normes de performance associées au bien ?
La première étape du RCM consiste à comprendre les fonctions de l'actif et les normes de performance associées à ces fonctions. Il s'agit de définir ce que l'actif est censé faire et les critères permettant de déterminer s'il le fait bien. Par exemple, la fonction d'une pompe à fluide dans une usine chimique peut être de transporter le produit d'une partie de l'usine à une autre à un certain rythme. La norme de performance pourrait être la capacité à transporter un volume spécifique de fluide par heure sans défaillance.
2. De quelle manière peut-il ne pas remplir ses fonctions ?
L'étape suivante consiste à identifier les différentes façons dont l'actif peut ne pas remplir ses fonctions. Il peut s'agir d'une panne complète, d'une panne partielle ou d'une dégradation des performances. Par exemple, la pompe peut tomber en panne totale (arrêt de fonctionnement), partielle (fonctionnement intermittent) ou ses performances peuvent se dégrader (ralentissement).
3. Quelles sont les causes de chaque défaillance fonctionnelle ?
Il est essentiel d'identifier les causes de chaque défaillance fonctionnelle. Celles-ci peuvent être dues à l'usure, à une mauvaise utilisation, aux conditions environnementales ou à des défauts de conception. Dans notre exemple de pompe, les causes peuvent être des roues ou des roulements usés, des différences de hauteur de charge excessives, l'exposition à des températures extrêmes ou un défaut de conception qui rend la pompe sujette à des pannes fréquentes.
4. Que se passe-t-il lorsque chaque défaillance se produit ?
Comprendre les conséquences de chaque défaillance permet de hiérarchiser les tâches de maintenance. L'impact peut aller de perturbations mineures à des pannes de système majeures. La défaillance d'une pompe peut entraîner un ralentissement de la production ou, dans des cas extrêmes, l'arrêt de toute la chaîne de production.
5. En quoi chaque échec est-il important ?
Chaque défaillance a une importance particulière. Certaines défaillances peuvent avoir des conséquences sur la sécurité, d'autres peuvent avoir un impact sur la production et d'autres encore peuvent entraîner des coûts de maintenance plus élevés. La défaillance de notre pompe est importante car elle a un impact direct sur l'efficacité de la production. Une défaillance peut entraîner une augmentation des coûts opérationnels, des temps d'arrêt ou un gaspillage de produit.
6. Que peut-on faire pour prévoir ou prévenir chaque défaillance ?
Des stratégies de maintenance prédictive et préventive peuvent être employées pour gérer chaque défaillance. Il peut s'agir d'inspections régulières, de contrôle de l'état, de remplacement de composants ou de reconception de certaines parties du système. Pour la pompe, la surveillance des vibrations et de la température, les inspections régulières et le remplacement en temps voulu des pièces usées peuvent aider à prévoir et à prévenir les défaillances.
7. Que faire si une tâche proactive appropriée ne peut être trouvée ?
S'il est impossible de trouver une tâche proactive appropriée, une approche réactive peut s'avérer nécessaire. Il peut s'agir de faire fonctionner l'actif jusqu'à la panne, puis de le réparer ou de le remplacer. Dans le cas de notre pompe, si les tâches proactives ne sont pas réalisables ou rentables, les options peuvent consister à faire fonctionner la pompe jusqu'à sa défaillance, puis à la réparer ou à la remplacer, ou à disposer d'une pompe de secours prête à l'emploi.
L'ICR, c'est plus que sept questions
Les sept questions du RCM constituent la base de la maintenance centrée sur la fiabilité (RCM). Toutefois, pour mettre en œuvre efficacement le RCM dans une organisation, il est essentiel de comprendre d'autres outils et concepts. Voici quelques principes fondamentaux et meilleures pratiques pour la mise en œuvre de la GRC :
- Identifier les points de défaillance : Il s'agit de comprendre la fonction et les modes de défaillance des actifs, ainsi que leurs conséquences.
- Choisir la bonne stratégie de maintenance : Utilisation d'outils tels que les arbres logiques de décision, la matrice des risques et l'analyse coûts-avantages pour choisir la stratégie de maintenance la plus appropriée pour chaque actif.
- Mise en œuvre et suivi du plan de maintenance : Définir les tâches de maintenance, les intervalles, les ressources et les indicateurs de performance pour chaque bien, et collecter/analyser les données sur l'état des biens et les taux de défaillance.
- Exploiter la technologie et les données : Le logiciel RCM peut rationaliser le processus RCM en organisant les données, en effectuant des analyses et en suivant les indicateurs de performance et de fiabilité.
En outre, il est important de définir les limites du système, d'identifier les besoins en ressources et d'impliquer et de former les parties prenantes pour une mise en œuvre réussie de la GRC. En comprenant ces concepts et en utilisant les bons outils, les organisations peuvent réduire les coûts, améliorer la sécurité et accroître la satisfaction des clients en mettant en œuvre la GRC de manière efficace.
Présentation de l'IMS RCM
IMS RCM est le logiciel de maintenance centrée sur la fiabilité (Reliability Centered Maintenance) deenosco, basé sur le cloud. Il aide à prévenir les défaillances non planifiées en améliorant la disponibilité des actifs par le biais de la maintenance. Vous n'avez pas besoin d'avoir un plan de maintenance coûteux pour assurer la sécurité de votre personnel et la haute disponibilité de vos actifs. Avec IMS RCM, vous optimiserez vos tâches de maintenance afin d'opérer de la manière la plus sûre et la plus économique possible.
Améliorez la disponibilité de vos actifs grâce à la maintenance.
Nous présentons ci-dessous quelques-unes des principales caractéristiques d'IMS RCM. Explorez les nombreuses façons dont notre logiciel RCM peut vous aider à prendre le contrôle de vos opérations.
- Accès exclusif à une bibliothèque de stratégies de fiabilité créée avec Shell
- Formulaires dynamiques
- Gérer l'optimisation de l'entretien des équipements
- Indice d'efficacité de la maintenance
- Modification et report
- ... et bien plus encore
Demander une démonstration
Vous êtes prêt à en savoir plus sur IMS RCM ? Remplissez le formulaire ci-dessous pour en savoir plus.
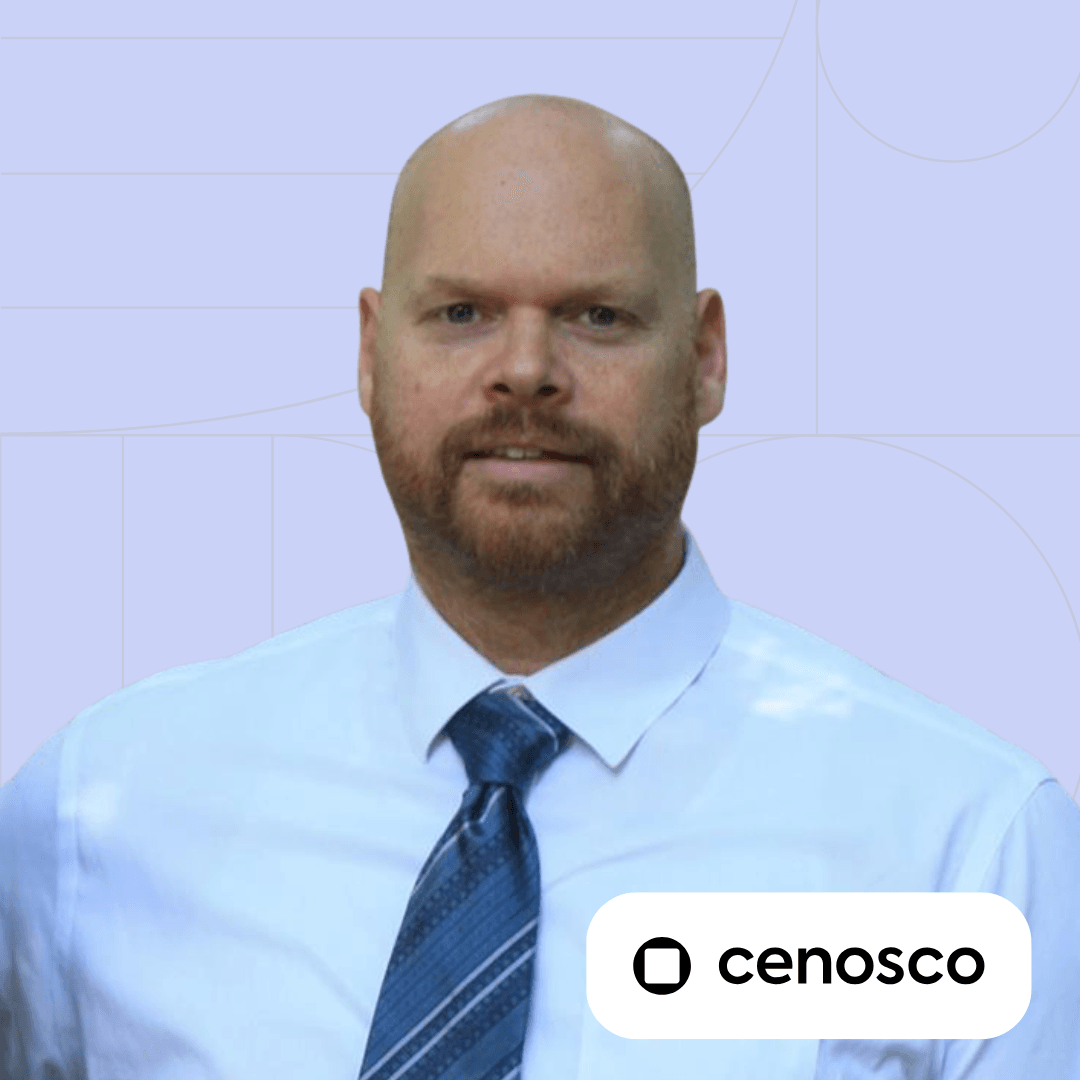
Tomislav Renić Technical Writer
Tomislav is an experienced engineer and technical communicator with over 20 years in complex systems, modeling, and project management. As a Technical Writer at Cenosco, he translates engineering concepts into clear, user-friendly documentation for software in the oil, gas, and refining industries.