Num blogue recente, abordámos o tema da otimização da atribuição de recursos ao implementar a Manutenção Centrada na Fiabilidade (RCM) para ajudar a desenvolver um plano de inspeção e manutenção eficaz. Abordámos a origem da RCM e as Sete Perguntas da RCM. No post de hoje, aprofundamos os fundamentos da RCM e falamos sobre as Sete Perguntas da Manutenção Centrada em Confiabilidade (RCM).
Mudança de perspetiva sobre a manutenção
À medida que o mundo se industrializava, primeiro lentamente e depois rapidamente, no início do século XX, a produção de bens tornou-se cada vez mais dependente da maquinaria. Isto deveu-se a muitos factores, incluindo os avanços na tecnologia de fabrico e a escassez de mão de obra durante a Segunda Guerra Mundial.
Manutenção reactiva
As instalações industriais tornaram-se mais mecanizadas e os programas de manutenção aumentaram de importância devido à necessidade de assegurar que as interrupções de fabrico fossem minimizadas devido a falhas de equipamento. Inicialmente, os programas de manutenção centravam-se em abordagens reactivas para reparar a maquinaria depois de esta ter falhado.
Manutenção proactiva
Com o tempo, a produção industrial tornou-se mais eficiente através de abordagens como a entrega just-in-time. Estas abordagens inovadoras tiveram a vantagem de reduzir os inventários e permitir cadeias de abastecimento mais eficientes, mas também significaram que mesmo uma falha relativamente pequena numa parte do processo de produção poderia ter um impacto significativo na produção industrial.
Em resposta a estes novos desafios, os programas de manutenção industrial voltaram-se para uma abordagem de manutenção mais proactiva, baseada na convicção de que quanto mais tempo o equipamento estivesse em serviço, maior seria a probabilidade de falhar. Os programas de manutenção baseavam-se em manutenção e revisões baseadas no tempo. Esta abordagem predominou durante as décadas de 1960 e 1970.
Novas teorias do insucesso
A nova investigação em engenharia industrial nas décadas de 1960 e 1970 mostrou que a anterior compreensão da falha do equipamento não estava completa. Compreendia-se agora que diferentes tipos de equipamento tinham diferentes modos de falha e que uma abordagem de manutenção de tamanho único resultava em capital desperdiçado e tempo de inatividade desnecessário.
As sete questões da manutenção centrada na fiabilidade
Durante a década de 1970, a indústria aeroespacial americana começou a analisar mais atentamente os seus programas de manutenção e desenvolveu processos para substituir a anterior manutenção baseada no tempo dos componentes dos aviões. A United Airlines, com o apoio do Departamento de Defesa dos EUA, escreveu um dos primeiros manuais sobre esta nova abordagem, conhecida como Manutenção Centrada na Fiabilidade.
Esta abordagem foi codificada na Norma SAE JA1011 e, mais tarde, na IEC 60300. Na sua essência, a Manutenção Centrada na Fiabilidade gira em torno de sete questões-chave que ajudam a identificar e implementar tarefas de manutenção eficazes. Abaixo, aprofundamos essas sete questões com um exemplo específico.
1. Quais são as funções e as normas de desempenho associadas do ativo?
O primeiro passo na RCM é compreender as funções do ativo e os padrões de desempenho associados a essas funções. Isto implica definir o que é suposto o ativo fazer e os critérios para determinar se o está a fazer bem. Por exemplo, a função de uma bomba de fluido numa fábrica de produtos químicos pode ser a de transportar o produto de uma parte da fábrica para outra a uma determinada velocidade. O padrão de desempenho pode ser a capacidade de transportar um volume específico de fluido por hora sem falhas.
2. De que forma pode falhar no cumprimento das suas funções?
O passo seguinte é identificar as diferentes formas em que o ativo pode deixar de cumprir as suas funções. Isto pode incluir uma falha completa, uma falha parcial ou um desempenho degradado. Por exemplo, a bomba pode falhar completamente (deixa de funcionar), parcialmente (funciona de forma intermitente) ou o seu desempenho pode degradar-se (abrandar).
3. Quais são as causas de cada falha funcional?
É fundamental identificar as causas de cada falha funcional. Estas podem ser devidas a desgaste, utilização incorrecta, condições ambientais ou falhas de conceção. No nosso exemplo da bomba, as causas podem incluir impulsores ou rolamentos gastos, diferenças excessivas de cabeça, exposição a temperaturas extremas ou uma falha de conceção que a torne suscetível a avarias frequentes.
4. O que acontece quando cada falha ocorre?
Compreender as consequências de cada falha ajuda a dar prioridade às tarefas de manutenção. O impacto pode variar desde pequenas interrupções até grandes avarias no sistema. Se a nossa bomba falhar, isso pode levar a um abrandamento da produção ou, em casos extremos, à paragem de toda a linha de produção.
5. De que forma é que cada fracasso é importante?
Cada falha é importante de uma forma única. Algumas falhas podem ter implicações de segurança, outras podem afetar a produção e outras podem levar a custos de manutenção mais elevados. A avaria da nossa bomba é importante porque tem um impacto direto na eficiência da produção. A falha pode levar a um aumento dos custos operacionais, tempo de inatividade ou desperdício de produto.
6. O que pode ser feito para prever ou evitar cada falha?
Podem ser utilizadas estratégias de manutenção preditiva e preventiva para gerir cada falha. Isto pode envolver inspecções regulares, monitorização do estado, substituição de componentes ou redesenho de partes do sistema. No caso da bomba, a monitorização da vibração e da temperatura, as inspecções regulares e a substituição atempada de peças gastas podem ajudar a prever e a evitar avarias.
7. O que deve ser feito se não for possível encontrar uma tarefa proactiva adequada?
Se não for possível encontrar uma tarefa proactiva adequada, poderá ser necessária uma abordagem reactiva. Isto pode implicar o funcionamento do ativo até à falha e depois a sua reparação ou substituição. No caso da nossa bomba, se as tarefas pró-activas não forem viáveis ou rentáveis, as opções podem ser funcionar até à falha e depois reparar ou substituir a bomba ou ter uma bomba de reserva pronta a funcionar.
RCM é mais do que apenas sete perguntas
As Sete Perguntas da RCM constituem a base da Manutenção Centrada na Fiabilidade (RCM). No entanto, para implementar eficazmente a RCM numa organização, é essencial compreender ferramentas e conceitos adicionais. Alguns dos principais fundamentos e melhores práticas para a implementação da RCM incluem:
- Identificação de pontos de falha: Trata-se de compreender a função e os modos de falha dos activos, bem como as suas consequências.
- Seleção da estratégia de manutenção correcta: Utilizar ferramentas como árvores lógicas de decisão, matriz de risco e análise custo-benefício para escolher a estratégia de manutenção mais adequada para cada ativo.
- Implementar e monitorizar o plano de manutenção: Definir tarefas de manutenção, intervalos, recursos e indicadores de desempenho para cada ativo, e recolher/analisar dados sobre o estado dos activos e as taxas de falha.
- Aproveitamento da tecnologia e dos dados: O software RCM pode simplificar o processo RCM, organizando dados, efectuando análises e acompanhando indicadores de desempenho e fiabilidade.
Para além disso, é importante definir os limites do sistema, identificar os requisitos de recursos e envolver e formar as partes interessadas para uma implementação bem sucedida da RCM. Ao compreender estes conceitos e utilizar as ferramentas correctas, as organizações podem reduzir custos, melhorar a segurança e aumentar a satisfação do cliente através da implementação eficaz da RCM.
Conheça a IMS RCM
O IMS RCM é o software baseado na nuvem de Manutenção Centrada na Fiabilidade da Cenosco. Ajuda a evitar falhas não planeadas, melhorando a disponibilidade dos activos através da manutenção. Não precisa de ter um plano de manutenção dispendioso para garantir a segurança dos seus colaboradores e uma elevada disponibilidade dos activos. Com o IMS RCM, irá otimizar as suas tarefas de manutenção para que possa operar da forma mais segura e económica possível.
Melhore a disponibilidade dos seus activos através da manutenção.
Abaixo apresentamos algumas das principais características do IMS RCM. Explore as muitas formas em que o nosso software RCM pode ajudá-lo a ganhar o controlo das suas operações.
- Acesso exclusivo a uma biblioteca de estratégias de fiabilidade criada com a Shell
- Formulários dinâmicos
- Gerir a otimização dos cuidados com o equipamento
- Índice de eficiência da manutenção
- Modificação e diferimento
- ... muito mais
Pedir uma demonstração
Pronto para saber mais sobre o IMS RCM? Preencha o formulário abaixo para saber mais.
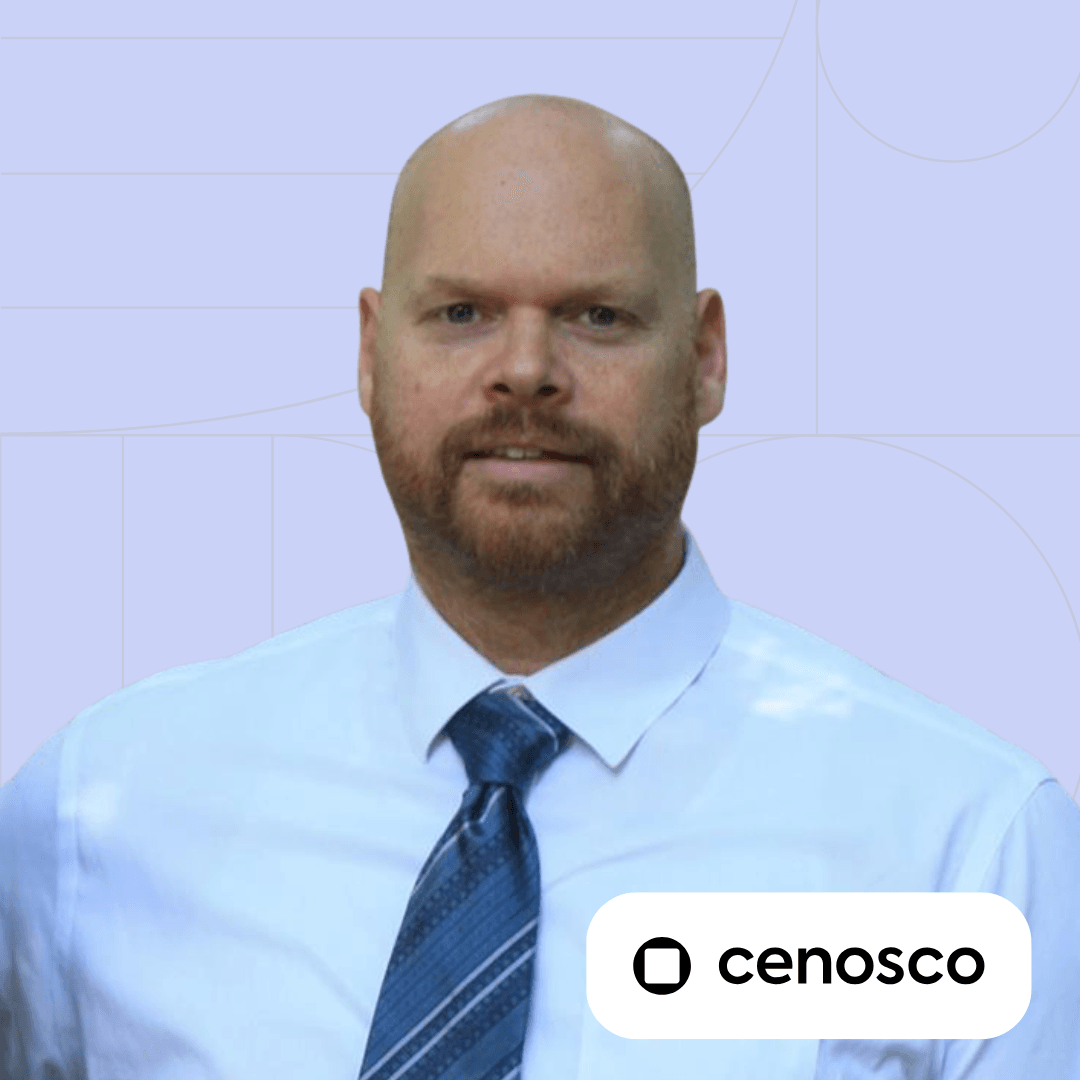
Tomislav Renić Technical Writer
Tomislav is an experienced engineer and technical communicator with over 20 years in complex systems, modeling, and project management. As a Technical Writer at Cenosco, he translates engineering concepts into clear, user-friendly documentation for software in the oil, gas, and refining industries.