When it comes to ensuring operational reliability, many companies struggle to grasp the value of a structured approach like Failure Mode and Effects Analysis (FMEA) and the need for methods that boost operational efficiency.
It’s easy to envision the end goal—smooth operations and flawless performance—without considering the essential steps that lead there. However, without a clear understanding of potential failures and their impacts, businesses may find themselves facing unexpected disruptions that could have been prevented.
In diesem Artikel werden wir den FMEA-Prozess im Detail untersuchen und seine Bedeutung für die Identifizierung potenzieller Fehlermodi, die Bewertung von Risiken, die Gestaltung von Instandhaltungsstrategien durch die Festlegung von Prioritäten für die Instandhaltung und die Umsetzung wirksamer Korrekturmaßnahmen zur Verbesserung der Betriebssicherheit in der Öl- und Gasindustrie hervorheben.
FMEA: Was ist das?
Die Fehlermöglichkeits- und Einflussanalyse (FMEA) ist eine systematische Methode zur Ermittlung und Bewertung potenzieller Probleme und Fehlermöglichkeiten in Systemen, Produkten oder Prozessen. Durch die Analyse dieser Risiken, bevor sie zu echten Problemen werden, verbessert die FMEA die allgemeine Zuverlässigkeit von Konstruktionen und Abläufen
Der Prozess umfasst in der Regel Folgendes:
- Identifizierung von Fehlermodi: Erkennen, wie und wo Fehler auftreten können.
- Analyse der Auswirkungen: Bewertung der Folgen dieser Fehler für das System oder den Kunden.
- Priorisierung von Risiken: Einstufung von Fehlermodi nach Schweregrad, Eintrittswahrscheinlichkeit und Entdeckbarkeit.
- Entwicklung von Empfehlungen zur Risikominderung: Auf der Grundlage der Analyse schlägt die FMEA spezifische Schritte zur Verringerung oder Vermeidung von Risiken vor, z. B. Konstruktionsänderungen, Prozessverbesserungen, Schulungsinitiativen oder zusätzliche Inspektionen.
Diese Methode stützt sich auf ein Expertenteam, das das System oder Produkt systematisch analysiert, um die Wahrscheinlichkeit verschiedener Ausfallarten und deren Auswirkungen zu bewerten. Die aus dieser Analyse gewonnenen Erkenntnisse fließen nicht nur in die Entwicklung von Abhilfemaßnahmen ein, die darauf abzielen, potenzielle Ausfälle zu verringern, sondern helfen auch bei der Festlegung von Prioritäten für die Instandhaltung, um sicherzustellen, dass die kritischsten Probleme zuerst angegangen werden.
Was ist ein Fehlermodus?
But what exactly is a failure mode? A failure mode refers to the specific way a system, component, or process fails to perform its intended function. It describes the various ways in which something can fail, such as through physical damage, loss of functionality, or operational inefficiencies.
For example, in the oil and gas industry, common failure modes might include pipeline leaks due to corrosion, equipment malfunctions, or sensor failures.
Betrachten wir dies einmal anhand einer Sache, auf die wir uns alle verlassen: die Heizungsanlage Ihres Hauses. Dieses System ist auf einen Ofen angewiesen, um Wärme zu erzeugen, die dann durch ein Netz von Kanälen verteilt wird.
Stellen Sie sich Folgendes vor: Es ist mitten im Winter, und Ihr Ofen funktioniert plötzlich nicht mehr. Und warum? Vielleicht ist der Luftfilter verstopft, der Thermostat funktioniert nicht richtig, oder es gibt ein Gasleck. Jedes dieser Szenarien stellt einen Fehlermodus dar - spezifische Ereignisse, die dazu führen können, dass Ihr Heizsystem Ihre Wohnung nicht mehr warm hält.
Was ist Wirkungsanalyse?
In der Welt der FMEA ist die Identifizierung von Fehlerarten nur der Anfang. Ziel ist es, die potenziellen Auswirkungen (oder Effekte, das "E" in FMEA) der Fehler zu analysieren und Maßnahmen zu ihrer Behebung zu priorisieren, bevor sie zu einem eiskalten Haus oder noch schlimmer zu einer kostspieligen Notfallreparatur führen.
Arten von FMEA
Im Öl- und Gassektor gibt es verschiedene Arten von Fehler- und Einflussanalysen (FMEA), die auf spezifische betriebliche Anforderungen zugeschnitten sind und die Sicherheit und Zuverlässigkeit verbessern. Hier sind die wichtigsten Arten:
- Konstruktions-FMEA (DFMEA): Konzentriert sich auf die Identifizierung potenzieller Fehler in der Konstruktionsphase von Anlagen wie Bohrinseln oder Pipelines.
- Prozess-FMEA (PFMEA): Zielt auf Risiken im Zusammenhang mit Herstellungs- oder Betriebsprozessen ab, wie z. B. Raffinations- oder Extraktionsverfahren.
- Funktionale FMEA (FFMEA): Analysiert die Funktionen sicherheitskritischer Systeme, wie z. B. Überdruckventile, und deren Ausfälle und ist ein wichtiges Instrument zur Entwicklung eines risikobasierten Instandhaltungskonzepts.
Der FMEA-Prozess
Der FMEA-Prozess besteht in der Regel aus einer Reihe von Schritten:
- Planung und Vorbereitung: Stellen Sie ein funktionsübergreifendes Team mit Fachwissen in verschiedenen Bereichen wie Technik, Betrieb, Wartung und Sicherheit zusammen. Definieren Sie den Umfang der FMEA, einschließlich der spezifischen Systeme oder Prozesse, die bewertet werden, und die Ziele der Analyse.
- Systematisierung: Zerlegen Sie das System in seine Komponenten, um eine detaillierte Analyse zu ermöglichen. Dies beinhaltet die Identifizierung von Subsystemen und deren Schnittstellen, was bei komplexen Öl- und Gasbetrieben, bei denen sich Wechselwirkungen erheblich auf die Leistung auswirken können, von entscheidender Bedeutung ist.
- Funktionsanalyse: Identifizieren Sie die Funktionen der einzelnen Komponenten innerhalb des Systems. In einem Öl- und Gaskontext könnte dies Funktionen wie Druckregelung, Durchflusskontrolle oder Sicherheitsabschaltmechanismen umfassen.
- Versagensanalyse: Bestimmen Sie potenzielle Fehlermöglichkeiten für jede identifizierte Funktion. Dieser Schritt beinhaltet ein Brainstorming, um die möglichen Fehler zu identifizieren, die verhindern könnten, dass die Komponenten ihre beabsichtigten Funktionen erfüllen, wie z. B. Fehlfunktionen von Ventilen oder Sensorausfälle. Sammeln von Daten über Fehlermöglichkeiten. Es kann von Vorteil sein, verschiedene Quellen zu konsultieren, darunter OEM-Wartungshandbücher, technische Prozessdiagramme, Wartungsaufzeichnungen und -historie, Betriebserfahrungen, Berichte über Zwischenfälle und Bilder der Anlage.
- Ursachenanalyse: Ermitteln Sie die Ursachen der einzelnen Fehlerarten durch eingehende Analyse und Datenerfassung. Dieser Schritt deckt die grundlegenden Faktoren auf, die potenzielle Ausfälle auslösen.
- Risikoanalyse: Bewerten Sie jeden Fehlermodus auf der Grundlage seiner:
- Schweregrad:Bewertet von 1 bis 10, wobei ein hoher Wert ein hohes Risiko anzeigt.
- Wahrscheinlichkeit:Bewertet von 1 bis 10, wobei eine hohe Punktzahl eine größere Wahrscheinlichkeit des Scheiterns widerspiegelt.
- Erkennung:Bewertet von 1 bis 10, wobei eine hohe Punktzahl auf eine schlechte Erkennungsleistung hinweist.
- Risikopriorisierung: Auf der Grundlage der Wahrscheinlichkeits-, Entdeckungs- und Schweregradeinstufung eine Rangfolge der Fehlermodi aufstellen, um festzustellen, welche eine weitere Untersuchung erfordern.
Risikopriorität = Schweregrad x Auftreten x Entdeckung
- Optimization: Develop action plans to mitigate high-priority risks identified in the previous step. This may involve redesigning components, implementing additional safety measures and inspections, or enhancing maintenance procedures to reduce failure likelihood.
- Dokumentation: Halten Sie alle Ergebnisse, die während der Analyse getroffenen Entscheidungen und die daraus gezogenen Lehren für spätere Zwecke fest. Diese Dokumentation sollte eine Zusammenfassung der festgestellten risikoreichen Fehler und der zu ihrer Behebung ergriffenen Maßnahmen enthalten.
Bedeutung der FMEA
Betrachten Sie die FMEA als Ihr betriebliches Sicherheitsnetz, das nicht nur Ihre Abläufe schützt, sondern auch mehrere wichtige Vorteile bietet:
- Proaktives Risikomanagement: Die FMEA hilft dabei, Probleme zu erkennen, bevor sie entstehen, und verringert so die Wahrscheinlichkeit kostspieliger Fehler.
- Priorisierung von Risiken: Es ermöglicht Unternehmen, Risiken auf der Grundlage ihrer Schwere und Wahrscheinlichkeit zu priorisieren, was eine gezieltere Wartungsstrategie erleichtert.
- Informierte Entscheidungsfindung: Die FMEA bietet einen strukturierten Ansatz zum Verständnis der Auswirkungen von Fehlern, der es ermöglicht, fundierte Konstruktions- und Betriebsentscheidungen zu treffen.
- Einhaltung gesetzlicher Vorschriften: In vielen Branchen ist eine FMEA erforderlich, um Sicherheits- und Qualitätsstandards zu erfüllen, was sie zu einem unverzichtbaren Instrument macht, um rechtliche Risiken im Zusammenhang mit der Nichteinhaltung von Vorschriften zu verringern.
- Kostenreduzierung: Die FMEA hilft bei der Entwicklung einer risikobasierten Instandhaltungsstrategie, die kritischen Anlagen Priorität einräumt und kostspielige Ausfälle und Stillstandszeiten minimiert. Die frühzeitige Behebung potenzieller Ausfälle kann die Kosten für Nacharbeiten, Rückrufe oder Garantieansprüche erheblich senken.
- Dokumentation und Wissensaustausch: Die FMEA schafft eine dokumentierte Aufzeichnung potenzieller Fehlermöglichkeiten und Abhilfestrategien, auf die bei künftigen Projekten zurückgegriffen werden kann.
- Kontinuierliche Verbesserung: Die aus der FMEA gewonnenen Erkenntnisse tragen zur kontinuierlichen Verbesserung von Prozessen und Systemen bei und fördern so eine Kultur der ständigen Verbesserung.
Jedes identifizierte Risiko und jeder potenzielle Fehler, der durch Abschwächung oder Beseitigung behoben wird, trägt zu einer stärkeren Grundlage für Ihren Betrieb bei. Durch die Umsetzung der FMEA verlagert sich Ihr Fokus von der bloßen Vorstellung einer optimalen Leistung auf die aktive Umsetzung der Praktiken von heute, die Sie dazu bringen werden, das gewünschte Ergebnis morgen zu erreichen.
FMEA in sicherheitsinstrumentierten Systemen (SIS)
Operational safety relies heavily on Safety Instrumented Systems (SIS), where Safety Instrumented Functions (SIFs) perform key safety actions to reduce risks, such as shutting down a process or isolating equipment during hazardous situations.
FMEA dives deep into the components of Safety Instrumented Functions (SIFs). By conducting FMEA, you can uncover how each part—like sensors, logic solvers, and final elements—might fail and what those failures could mean for safety. For instance, if a safety valve is part of a SIF, FMEA helps identify how failure modes like valve sticking or sensor inaccuracies could impact its ability to perform its safety function.
The FMEA process for this device begins by generating a list of potentially dangerous failures. If they occur, these failures will defeat the safety mission of the device when there is a demand from the process. Specialists then do a study to estimate the contribution of each identified failure mode to the overall number of dangerous failures.
As some dangerous failures are more common than others, this contribution or weight factor (in %) is included. It is important to note that the total weight factors of all dangerous failures of the device under study cannot exceed 100%.
Die aus der FMEA-Studie gewonnenen Informationen können zum Vergleich der für das Gerät ermittelten gefährlichen Ausfallarten mit dem für die regelmäßige Prüfung des Geräts verwendeten Prüfverfahren verwendet werden. Bei dieser Prüfung wird ermittelt, welche der in der FMEA für das Gerät identifizierten gefährlichen Ausfälle in einem der Schritte des Prüfverfahrens erfasst werden.
Wenn z.B. festgestellt wird, dass 7 von 8 identifizierten gefährlichen Fehlermodi durch die korrekte Anwendung des Nachweisverfahrens entdeckt werden können und diese 7 Modi zusammen 90% aller in der FMEA identifizierten gefährlichen Fehler ausmachen, können wir schließen, dass der Testabdeckungsfaktor (TCF) des Proof-Test-Verfahrens des Geräts 90 % beträgt.
Die Rolle der FMEA bei PFD-Berechnungen
Bei der Berechnung der Ausfallwahrscheinlichkeit (Probability of Failure on Demand, PFD) eines Geräts ist λd eine kritische Komponente, da sie die Anzahl der gefährlichen Ausfälle widerspiegelt, die möglicherweise zu Sicherheitsvorfällen führen könnten, wenn sie nicht erkannt werden, bevor eine Anforderung an das Gerät durch den Prozess erfolgt. Die TCF trägt dazu bei, zu bestimmen, wie viele dieser λd-Ausfälle bei Proof-Tests entdeckt werden können, und ist daher ein wichtiger Faktor bei der Berechnung der PFD des Geräts insgesamt.
Eine weitere kritische Komponente ist die Einsatzzeit (MT). Sie stellt den Zeitraum dar , in dem eine sicherheitsbezogene Funktion (Safety Instrumented Function, SIF) ohne größere Überholungen oder Ersetzungen effektiv arbeiten muss. Im Gegensatz zur Nutzungsdauer, die von den Herstellern festgelegt wird, wann ein Gerät ersetzt werden muss, ist die MT auf die spezifischen Anforderungen jeder SIF-Komponente zugeschnitten.
Why does this matter? Because with imperfect proof testing (i.e., where the TFC is less than 100%) Mission Time plays a vital role in managing risks associated with dangerous failures.
A well-defined Mission Time helps us gauge how long we can expect our SIF to function safely before risks accumulate.
This is illustrated in the below figure (Mission Time 20 years):
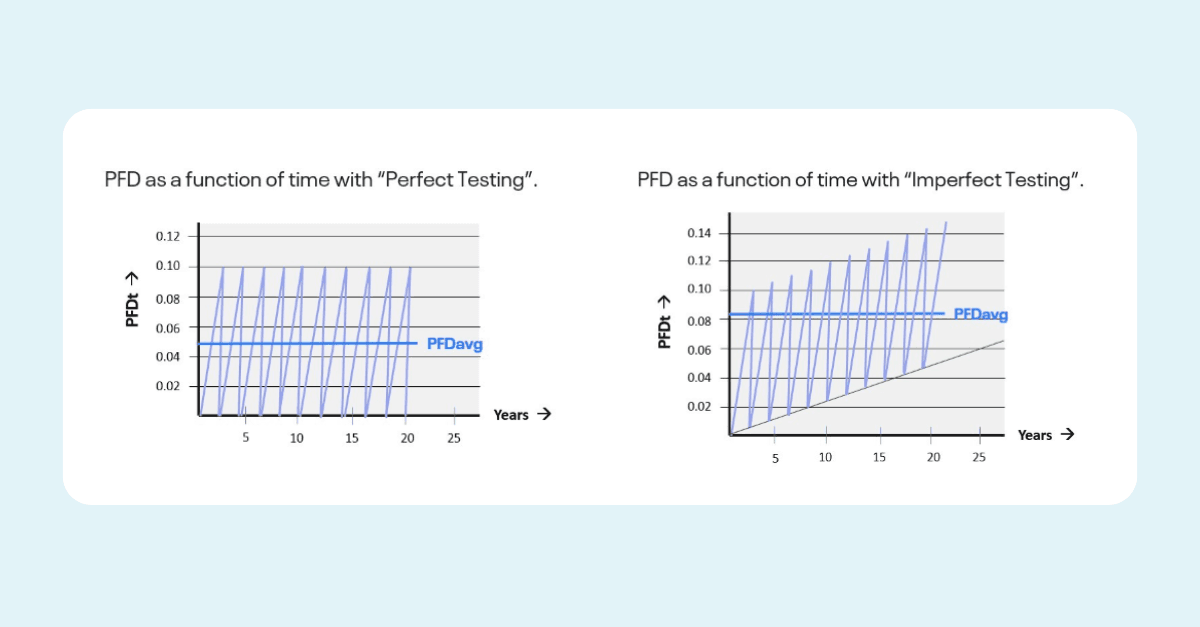
Die Einbeziehung von MT in die PFD-Berechnungen gibt Aufschluss über die Wirksamkeit von Sicherheitsmaßnahmen und dient als Richtschnur für Wartungs- und Prüfintervalle. Das Zusammenspiel von TCF und PFD unterstreicht deren Bedeutung für die Gewährleistung der Zuverlässigkeit von SIFs.
Ein höherer TCF (nahe 100 %) bedeutet, dass mehr gefährliche Ausfälle erkannt werden, wodurch der effektive λd und trägt zu einer niedrigeren PFD bei. Diese Beziehung unterstreicht die Bedeutung sowohl von TCF als auch von λd bei der Bewertung der Zuverlässigkeit und Sicherheit von SIFs in sicherheitskritischen Anwendungen.
Die PFD spiegelt die Wahrscheinlichkeit wider, dass eine Sicherheitsfunktion ausfällt, wenn sie benötigt wird, und sie wird davon beeinflusst, wie gut Tests gefährliche Ausfälle erkennen können. Die Formel zur Berechnung der durchschnittlichen PFD unter Einbeziehung der TCF lautet wie folgt:

In dieser Gleichung:
- Der TCF steht für die Wirksamkeit von Proof-Tests bei der Erkennung gefährlicher Fehler und reicht von 0 % bis 100 %.
- (1 - TCF)gibt den Anteil der gefährlichen Ausfälle an, die durch diese Tests unentdeckt bleiben.
- λdist die Rate der gefährlichen Ausfälle, die zu einem Ausfall auf Abruf führen könnten.
- Tiist das Intervall zwischen den Probetests.
- MTsteht für die Einsatzzeit des SIF.
Jedes Mal, wenn ein Proof-Test durchgeführt wird, wird nur ein Bruchteil der gefährlichen Fehler erkannt, wie die TCF angibt. Das bedeutet, dass selbst bei einer effektiven Prüfung einige Fehler unentdeckt bleiben können, wodurch sich das Risiko mit der Zeit erhöht. Daher ist es wichtig zu verstehen, wie die TCF die PFD beeinflusst; eine höhere TCF führt zu einer niedrigeren PFD, was auf eine effektivere Risikominderung hinweist.
Umgekehrt steigt bei einem niedrigen TCF die Wahrscheinlichkeit unentdeckter Ausfälle, so dass häufigere Proof-Tests zur Aufrechterhaltung der Sicherheitsintegrität erforderlich werden. Die Optimierung der TCF durch strenge Prüfprotokolle verbessert also nicht nur die Fehlererkennung, sondern spielt auch eine entscheidende Rolle bei der Gewährleistung, dass die PFD innerhalb akzeptabler Grenzen für die Einhaltung der Sicherheitsstandards bleibt.
Stärkung der Betriebssicherheit mit FMEA und Cenoscos IMS
Wie wir gesehen haben, trägt die FMEA zur Verbesserung der Betriebssicherheit bei. Durch die Identifizierung potenzieller Fehlermöglichkeiten und die Bewertung ihrer Auswirkungen können Unternehmen proaktiv mit Risiken umgehen und die Effizienz ihrer Anlagen verbessern.
Die FMEA ist eine vielseitige und wirksame Methodik, die in andere Prozesse integriert werden kann, z. B. in sicherheitsgerichtete Systeme. Durch die gründliche Bewertung kritischer Sicherheitskomponenten ermöglicht die FMEA rechtzeitige Strategien zur Risikominderung und liefert Informationen für Entscheidungen bezüglich der Prüfintervalle, wodurch gewährleistet wird, dass Sicherheitssysteme zuverlässig und effektiv bleiben.
Dieser Ansatz stärkt nicht nur die Sicherheitsprotokolle, sondern optimiert auch die Ressourcenzuweisung, was letztlich zu einem stabileren Betrieb in der Öl- und Gasindustrie führt. Wenn Sie nach einer Möglichkeit suchen, die Prozesssicherheit in Ihrer Anlage zu verbessern, kann Ihnen unser Integritätsmanagementsystem (IMS) helfen. Füllen Sie das untenstehende Formular aus und fordern Sie eine Demo an!
Request a Demo
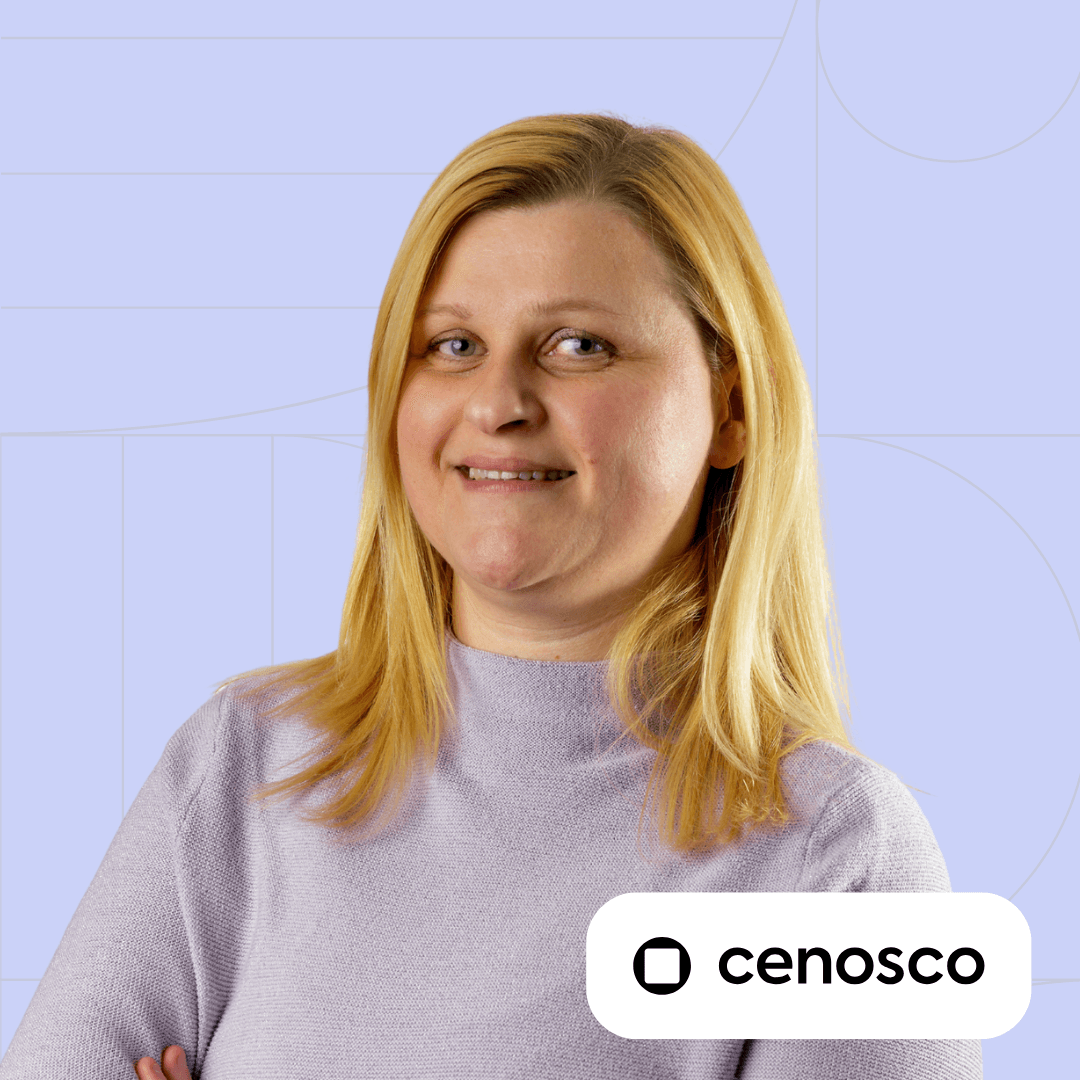
Denis Tkalec Technical writer
Denis Tkalec is a technical writer at Cenosco, specializing in asset integrity management software since 2022. With a background in education and six years in marketing, she turns complex topics into clear, user-friendly content. Inspired by Camus’s belief that “a writer keeps civilization from destroying itself,” she brings precision and care to every manual.