When it comes to ensuring operational reliability, many companies struggle to grasp the value of a structured approach like Failure Mode and Effects Analysis (FMEA) and the need for methods that boost operational efficiency.
It’s easy to envision the end goal—smooth operations and flawless performance—without considering the essential steps that lead there. However, without a clear understanding of potential failures and their impacts, businesses may find themselves facing unexpected disruptions that could have been prevented.
En este artículo exploraremos en detalle el proceso AMFE, destacando su importancia para identificar posibles modos de fallo, evaluar riesgos, configurar estrategias de mantenimiento priorizando los equipos que requieren mantenimiento y aplicar medidas correctivas eficaces para mejorar la fiabilidad operativa en la industria del petróleo y el gas.
FMEA: ¿Qué es?
El Análisis Modal de Fallos y Efectos (AMFE ) es un método sistemático diseñado para identificar y evaluar posibles problemas y modos de fallo en sistemas, productos o procesos. Al analizar estos riesgos antes de que se conviertan en problemas reales, el AMFE mejora la fiabilidad general de los diseños y las operaciones.
El proceso suele implicar:
- Identificación de los modos de fallo: Reconocer cómo y dónde pueden producirse fallos.
- Analizar los efectos: Evaluar las consecuencias de estos fallos en el sistema o en el cliente.
- Priorización de riesgos: Clasificación de los modos de fallo en función de la gravedad, la probabilidad de ocurrencia y la detectabilidad.
- Elaboración de recomendaciones para mitigar los riesgos: Basándose en el análisis, el AMFE sugiere medidas concretas para reducir o prevenir los riesgos, como modificaciones del diseño, mejoras de los procesos, iniciativas de formación o inspecciones adicionales.
Esta metodología se basa en un equipo de expertos que analizan sistemáticamente el sistema o producto para evaluar la probabilidad de diversos modos de fallo y sus efectos. La información obtenida de este análisis no sólo sirve para elaborar medidas correctivas destinadas a mitigar posibles fallos, sino que también ayuda a establecer prioridades de mantenimiento, garantizando que los problemas más críticos se aborden en primer lugar.
¿Qué es un modo de fallo?
But what exactly is a failure mode? A failure mode refers to the specific way a system, component, or process fails to perform its intended function. It describes the various ways in which something can fail, such as through physical damage, loss of functionality, or operational inefficiencies.
For example, in the oil and gas industry, common failure modes might include pipeline leaks due to corrosion, equipment malfunctions, or sensor failures.
Pongamos esto en perspectiva con algo de lo que todos dependemos: el sistema de calefacción de su casa. Este sistema depende de un horno para generar calor, que luego se distribuye a través de una red de conductos.
Imagínese lo siguiente: estamos en pleno invierno y, de repente, su caldera deja de funcionar. ¿Por qué? Puede que el filtro de aire esté obstruido, que el termostato no funcione correctamente o que haya una fuga de gas. Cada una de estas situaciones representa un modo de fallo específico que puede hacer que su sistema de calefacción deje de mantener caliente su hogar.
Qué es el análisis de efectos
En el mundo del AMFE, identificar los modos de fallo es sólo el principio. El objetivo es analizar los posibles impactos (o efectos, la "E" de FMEA) de los fallos y priorizar las acciones para solucionarlos antes de que den lugar a una casa helada o, peor aún, a una costosa reparación de emergencia.
Tipos de AMFE
En el sector del petróleo y el gas, los distintos tipos de Análisis Modal de Fallos y Efectos (AMFE) se adaptan a las necesidades operativas específicas y mejoran la seguridad y la fiabilidad. He aquí los principales tipos:
- FMEA de diseño (DFMEA): Se centra en identificar posibles fallos en la fase de diseño de activos como plataformas de perforación o tuberías.
- FMEA de procesos (PFMEA): Se centra en los riesgos asociados a los procesos de fabricación u operativos, como los métodos de refinado o extracción.
- FMEA funcional (FFMEA): Analiza las funciones de los sistemas críticos para la seguridad, como las válvulas de alivio de presión, y sus fallos, y es una herramienta vital para desarrollar un enfoque de mantenimiento basado en el riesgo.
El proceso AMFE
El proceso AMFE suele seguir una serie de pasos:
- Planificación y preparación: Forme un equipo interfuncional con experiencia en diversas áreas, como ingeniería, operaciones, mantenimiento y seguridad. Defina el alcance del AMFE, incluidos los sistemas o procesos específicos que se van a evaluar y los objetivos del análisis.
- Sistematización: Descomponer el sistema en sus componentes para facilitar un análisis detallado. Esto implica identificar los subsistemas y sus interfaces, algo fundamental en operaciones complejas de petróleo y gas en las que las interacciones pueden afectar significativamente al rendimiento.
- Análisis de funciones: Identificar las funciones de cada componente del sistema. En un contexto de petróleo y gas, esto podría incluir funciones como la regulación de la presión, el control del flujo o los mecanismos de parada de seguridad.
- Análisis de fallos: Determinar los posibles modos de fallo para cada función identificada. Este paso implica una lluvia de ideas para identificar los posibles fallos que podrían impedir que los componentes realicen las funciones previstas, como el mal funcionamiento de las válvulas o los fallos de los sensores. Recopilar datos sobre los modos de fallo. Puede ser beneficioso consultar diversas fuentes, como manuales de mantenimiento de fabricantes de equipos originales, diagramas de procesos de ingeniería, registros e historial de mantenimiento, experiencia operativa, informes de incidentes e imágenes del equipo.
- Análisis de causas: Averigüe qué causa cada modo de fallo mediante un análisis en profundidad y la recopilación de datos. Este paso descubre los factores que desencadenan posibles fallos.
- Análisis de riesgos: Evaluar cada modo de fallo en función de su:
- Gravedad:Calificada de 1 a 10, una puntuación alta indica un riesgo grave.
- Probabilidad:Valorada de 1 a 10, donde una puntuación alta refleja una mayor probabilidad de fracaso.
- Detección:Calificada de 1 a 10, una puntuación alta indica una capacidad de detección deficiente.
- Priorización de riesgos: Basándose en la clasificación de probabilidad, detección y gravedad, clasifique los modos de fallo para determinar cuáles requieren un examen más detallado.
Prioridad del riesgo = Gravedad x Ocurrencia x Detección
- Optimization: Develop action plans to mitigate high-priority risks identified in the previous step. This may involve redesigning components, implementing additional safety measures and inspections, or enhancing maintenance procedures to reduce failure likelihood.
- Documentación: Registre todas las conclusiones, decisiones tomadas durante el análisis y lecciones aprendidas para futuras consultas. Esta documentación debe incluir un resumen de los fallos de alto riesgo identificados y las medidas correctivas adoptadas para solucionarlos.
Importancia del AMFE
Piense en el AMFE como una red de seguridad operativa que no sólo protege sus operaciones, sino que también ofrece varias ventajas clave:
- Gestión proactiva de riesgos: El AMFE ayuda a anticiparse a los problemas antes de que surjan, reduciendo la probabilidad de errores costosos.
- Priorización de riesgos: Permite a las organizaciones priorizar los riesgos en función de su gravedad y probabilidad, facilitando una estrategia de mantenimiento más centrada.
- Toma de decisiones informada: El AMFE proporciona un enfoque estructurado para comprender los impactos de los fallos, lo que ayuda a tomar decisiones informadas sobre el diseño y el funcionamiento.
- Cumplimiento de la normativa: Muchas industrias exigen un AMFE para cumplir las normas de seguridad y calidad, por lo que resulta esencial para reducir los riesgos legales asociados al incumplimiento.
- Reducción de costes: El AMFE ayuda a desarrollar una estrategia de mantenimiento basada en el riesgo que prioriza los equipos críticos, minimizando los costosos fallos y los tiempos de inactividad. Abordar los posibles fallos en una fase temprana puede reducir significativamente los costes asociados a repeticiones de trabajos, retiradas de productos o reclamaciones de garantía.
- Documentación e intercambio de conocimientos: El AMFE crea un registro documentado de los posibles modos de fallo y las estrategias de mitigación, que puede servir de referencia para futuros proyectos.
- Mejora continua: La información obtenida del AMFE contribuye a la mejora continua de procesos y sistemas, fomentando una cultura de mejora continua.
Cada riesgo identificado y cada fallo potencial abordado mediante su mitigación o eliminación contribuyen a reforzar los cimientos de sus operaciones. Al implantar el AMFE, su atención pasa de limitarse a prever un rendimiento óptimo a implantar activamente hoy las prácticas que le llevarán a alcanzar ese resultado deseado mañana.
AMFE en sistemas instrumentados de seguridad (SIS)
Operational safety relies heavily on Safety Instrumented Systems (SIS), where Safety Instrumented Functions (SIFs) perform key safety actions to reduce risks, such as shutting down a process or isolating equipment during hazardous situations.
FMEA dives deep into the components of Safety Instrumented Functions (SIFs). By conducting FMEA, you can uncover how each part—like sensors, logic solvers, and final elements—might fail and what those failures could mean for safety. For instance, if a safety valve is part of a SIF, FMEA helps identify how failure modes like valve sticking or sensor inaccuracies could impact its ability to perform its safety function.
The FMEA process for this device begins by generating a list of potentially dangerous failures. If they occur, these failures will defeat the safety mission of the device when there is a demand from the process. Specialists then do a study to estimate the contribution of each identified failure mode to the overall number of dangerous failures.
As some dangerous failures are more common than others, this contribution or weight factor (in %) is included. It is important to note that the total weight factors of all dangerous failures of the device under study cannot exceed 100%.
La información obtenida del estudio FMEA puede utilizarse para comparar los modos de fallo peligrosos identificados para el dispositivo con el Procedimiento de Prueba de Ensayo utilizado para las pruebas periódicas del dispositivo. Este examen busca determinar qué fallos peligrosos identificados en el AMFE del dispositivo se detectarán en cualquiera de los pasos del Procedimiento de Pruebas de Ensayo.
Por ejemplo, si se determina que 7 de los 8 modos de fallo peligrosos identificados pueden detectarse aplicando correctamente el Procedimiento de Prueba de Ensayo, y estos 7 modos representan colectivamente el 90% de todos los fallos peligrosos identificados en el AMFE, podemos concluir que el Factor de cobertura de la prueba (TCF) del procedimiento de prueba del dispositivo es del 90%.
Papel del AMFE en el cálculo de la DFP
Al calcular la Probabilidad de Fallo a Demanda (PFD) de un dispositivo, λd es un componente crítico, ya que refleja el número de fallos peligrosos que podrían provocar incidentes de seguridad si no se detectan antes de que se produzca una demanda del proceso sobre el dispositivo. El TCF ayuda a determinar cuántos de estos fallos λd pueden detectarse durante las pruebas de comprobación y, por tanto, es un factor importante en el cálculo global de la PFD del dispositivo.
Otro componente crítico es el Tiempo de Misión (TM). Representa el periodo durante el cual una función instrumentada de seguridad (SIF) debe funcionar eficazmente sin revisiones o sustituciones importantes. A diferencia de la vida útil, definida por los fabricantes para determinar cuándo es necesario sustituir los equipos, el tiempo de misión se adapta a las necesidades específicas de cada componente de la función instrumentada de seguridad.
Why does this matter? Because with imperfect proof testing (i.e., where the TFC is less than 100%) Mission Time plays a vital role in managing risks associated with dangerous failures.
A well-defined Mission Time helps us gauge how long we can expect our SIF to function safely before risks accumulate.
This is illustrated in the below figure (Mission Time 20 years):
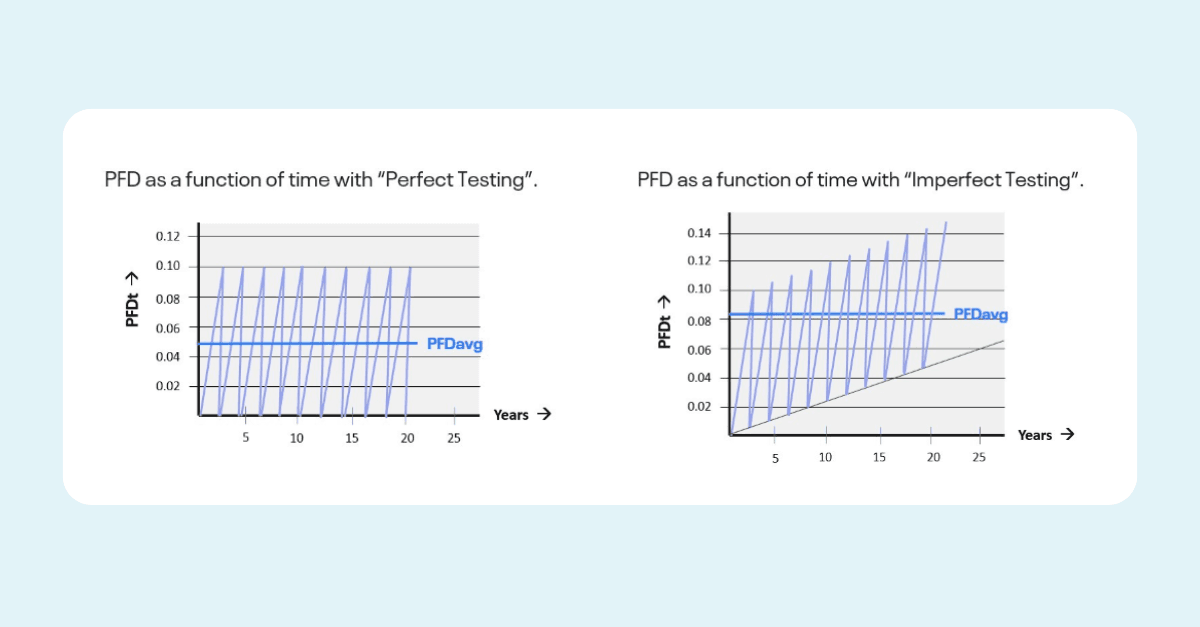
La incorporación de la MT a los cálculos de la PFD proporciona información sobre la eficacia de las medidas de seguridad y orienta los intervalos de mantenimiento y comprobación. La interacción entre TCF y PFD pone de relieve su importancia para garantizar la fiabilidad de los SIF.
Un TCF más alto (cercano al 100%) indica que se detectan más fallos peligrosos, con lo que se reduce la λefectiva d y contribuyendo a una menor PFD. Esta relación subraya la importancia tanto del TCF como de λd a la hora de evaluar la fiabilidad y seguridad de los SIF en aplicaciones críticas para la seguridad.
La PFD refleja la probabilidad de que una función de seguridad falle cuando sea necesario, y está influida por la capacidad de las pruebas para detectar fallos peligrosos. La fórmula para calcular la PFD media incorporando el TCF es la siguiente:

En esta ecuación:
- El TCF representa la eficacia de las pruebas de detección de fallos peligrosos, y oscila entre el 0% y el 100%.
- (1 - TCF)indica la proporción de fallos peligrosos que no son detectados por estas pruebas.
- λdes la tasa de fallos peligrosos que podrían provocar un fallo en la demanda.
- Ties el intervalo entre pruebas.
- MTindica el tiempo de misión de la SIF.
Cada vez que se realiza una prueba, sólo identifica una fracción de los fallos peligrosos, como indica el TCF. Esto significa que, incluso con pruebas eficaces, algunos fallos pueden pasar desapercibidos, lo que agrava el riesgo con el tiempo. En consecuencia, es vital comprender cómo influye el TCF en la PFD; un TCF más alto conduce a una PFD más baja, lo que indica una mitigación más eficaz del riesgo.
Por el contrario, si el TCF es bajo, aumenta la probabilidad de que se produzcan fallos no detectados, lo que hace necesario realizar pruebas más frecuentes para mantener la integridad de la seguridad. Así pues, la optimización de la TCF mediante protocolos de prueba rigurosos no sólo mejora la detección de fallos, sino que también desempeña un papel fundamental a la hora de garantizar que la PFD se mantiene dentro de los límites aceptables para el cumplimiento de las normas de seguridad.
Refuerce la fiabilidad operativa con FMEA e IMS de Cenosco
Como hemos visto, el AMFE ayuda a mejorar la fiabilidad operativa. Al identificar posibles modos de fallo y evaluar sus repercusiones, permite a las empresas gestionar los riesgos de forma proactiva y mejorar la eficiencia de sus activos.
El AMFE es una metodología versátil y eficaz que se integra en otros procesos, como los de los sistemas instrumentados de seguridad. Mediante una evaluación exhaustiva de los componentes de seguridad críticos, el AMFE permite aplicar estrategias oportunas de reducción de riesgos e informa las decisiones relativas a los intervalos de prueba, garantizando que los sistemas de seguridad sigan siendo fiables y eficaces.
Este enfoque no sólo refuerza los protocolos de seguridad, sino que también optimiza la asignación de recursos, lo que en última instancia conduce a operaciones más resistentes en la industria del petróleo y el gas. Si está buscando una forma de mejorar la fiabilidad de los procesos en sus instalaciones, nuestro sistema de gestión de la integridad (IMS ) puede ayudarle. Rellene el siguiente formulario y solicite una demostración.
Request a Demo
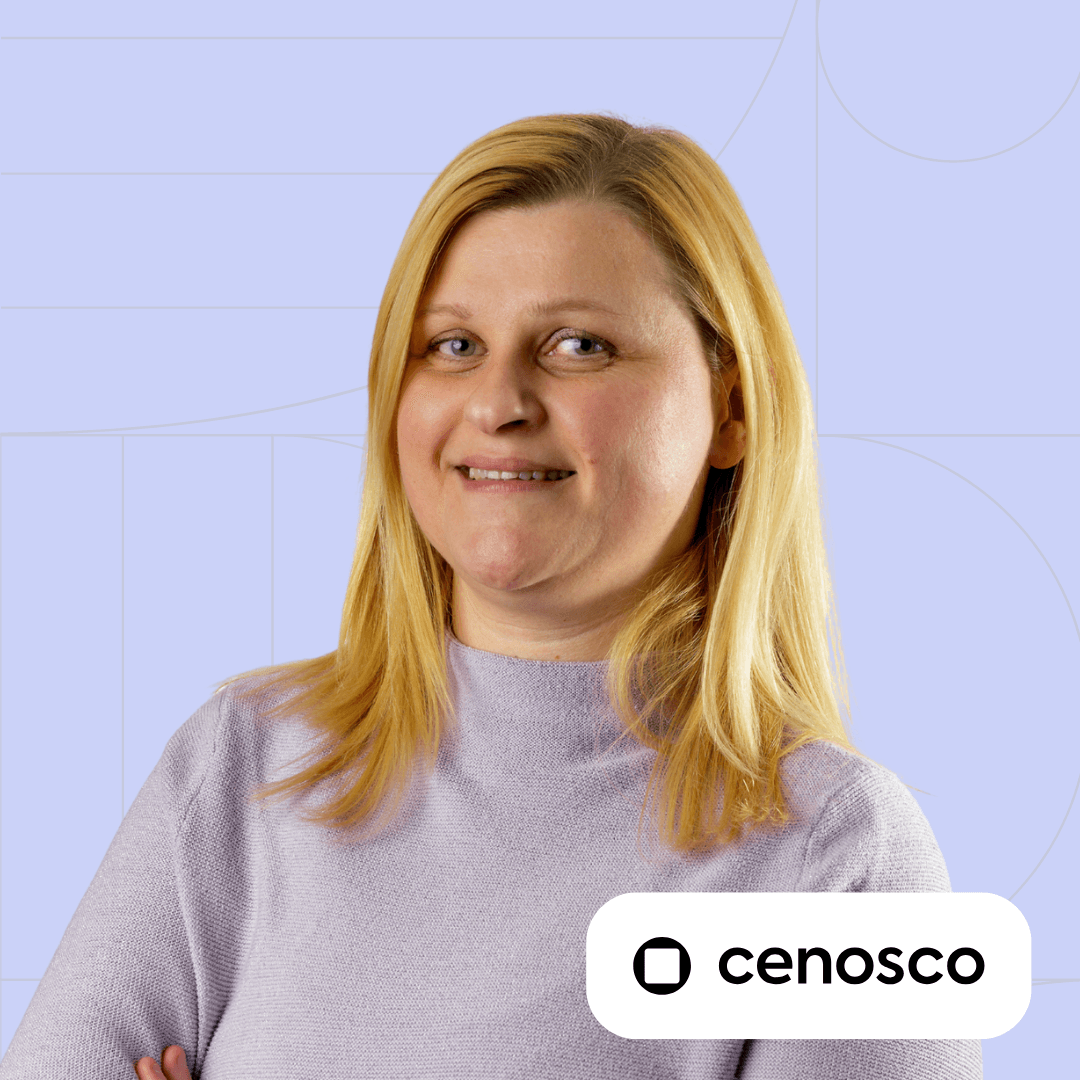
Denis Tkalec Technical writer
Denis Tkalec is a technical writer at Cenosco, specializing in asset integrity management software since 2022. With a background in education and six years in marketing, she turns complex topics into clear, user-friendly content. Inspired by Camus’s belief that “a writer keeps civilization from destroying itself,” she brings precision and care to every manual.