When it comes to ensuring operational reliability, many companies struggle to grasp the value of a structured approach like Failure Mode and Effects Analysis (FMEA) and the need for methods that boost operational efficiency.
It’s easy to envision the end goal—smooth operations and flawless performance—without considering the essential steps that lead there. However, without a clear understanding of potential failures and their impacts, businesses may find themselves facing unexpected disruptions that could have been prevented.
在本文中,我们将详细探讨 FMEA 流程,强调其在以下方面的重要性:识别潜在故障模式、评估风险、通过确定设备维护的优先级来制定维护策略,以及实施有效的纠正措施以提高油气行业的运行可靠性。
FMEA:它是什么?
失效模式和影响分析 (FMEA)是一种系统方法,旨在识别和评估系统、产品或流程中的潜在问题和失效模式。通过在这些风险变成实际问题之前对其进行分析,FMEA 提高了设计和运行的整体可靠性
这一过程通常包括
- 识别故障模式:识别故障可能发生的方式和地点。
- 分析影响:评估这些故障对系统或客户造成的后果。
- 确定风险的优先次序:根据严重性、发生可能性和可探测性对故障模式进行排序。
- 制定降低风险的建议:根据分析结果,FMEA 提出减少或预防风险的具体步骤,包括修改设计、改进流程、开展培训或进行额外检查。
这种方法依靠专家团队对系统或产品进行系统分析,以评估各种故障模式的可能性及其影响。从分析中获得的洞察力不仅有助于制定旨在减少潜在故障的纠正措施,还有助于确定维护工作的优先次序,确保首先解决最关键的问题。
什么是故障模式
But what exactly is a failure mode? A failure mode refers to the specific way a system, component, or process fails to perform its intended function. It describes the various ways in which something can fail, such as through physical damage, loss of functionality, or operational inefficiencies.
For example, in the oil and gas industry, common failure modes might include pipeline leaks due to corrosion, equipment malfunctions, or sensor failures.
让我们从一个我们都依赖的东西--家庭供暖系统--的角度来看待这个问题。该系统依靠火炉产生暖气,然后通过管道网络将暖气输送出去。
现在,请想象一下:正值严冬,您的炉子却突然停止了工作。为什么会这样?也许是空气过滤器堵塞了,也许是恒温器工作不正常,也许是燃气泄漏了。上述每种情况都代表了一种故障模式,都有可能导致供暖系统无法为您的家庭提供温暖。
什么是效果分析
在 FMEA 的世界里,确定故障模式只是一个开始。我们的目标是分析故障的潜在影响(或效果,即 FMEA 中的 "E"),并在故障导致房屋冰冷或更糟糕的是导致昂贵的紧急维修之前,优先采取应对措施。
FMEA 的类型
在石油和天然气领域,不同类型的故障模式和影响分析(FMEA)可满足特定的运营需求,并提高安全性和可靠性。以下是主要类型:
- 设计 FMEA(DFMEA):侧重于识别钻机或管道等资产在设计阶段可能出现的故障。
- 流程 FMEA(PFMEA):针对与生产或操作流程(如精炼或提取方法)相关的风险。
- 功能性 FMEA(FFMEA):分析泄压阀等安全关键系统的功能及其故障,是制定基于风险的维护方法的重要工具。
FMEA 流程
FMEA 流程通常遵循一系列步骤:
- 规划和准备:组建一个跨职能团队,该团队应具备工程、运营、维护和安全等不同领域的专业知识。确定 FMEA 的范围,包括要评估的具体系统或流程以及分析目标。
- 系统化:将系统分解为各个组成部分,以便于进行详细分析。这包括识别子系统及其接口,这在复杂的石油和天然气运营中至关重要,因为交互作用会对性能产生重大影响。
- 功能分析:确定系统中每个组件的功能。在石油和天然气领域,这可能包括压力调节、流量控制或安全关闭机制等功能。
- 故障分析:确定每个已识别功能的潜在故障模式。这一步需要集思广益,找出可能导致部件无法执行预期功能的故障,如阀门故障或传感器故障。收集有关故障模式的数据。可以参考各种资料,包括原始设备制造商的维护手册、工程流程图、维护记录和历史、操作经验、事故报告和设备图像。
- 原因分析: 通过深入分析和数据收集,找出导致每种故障模式的原因。这一步骤揭示了引发潜在故障的根本因素。
- 风险分析:根据每种故障模式,对其进行评估:
- 严重性:评分从 1 到 10,高分表示风险严重。
- 概率:评分从 1 到 10,分数越高,失败的可能性越大。
- 探测能力:评分从 1 到 10,高分表示检测能力差。
- 确定风险优先级:根据概率、检测和严重性评级,对故障模式进行排序,以确定哪些需要进一步检查。
风险优先级 = 严重性 x 发生率 x 检测率
- Optimization: Develop action plans to mitigate high-priority risks identified in the previous step. This may involve redesigning components, implementing additional safety measures and inspections, or enhancing maintenance procedures to reduce failure likelihood.
- 记录:记录所有发现、分析过程中做出的决定以及吸取的经验教训,供今后参考。该文件应包括已发现的高风险故障以及为解决这些故障而采取的纠正措施的摘要。
FMEA 的重要性
将 FMEA 视为您的运营安全网,它不仅能保障您的运营,还能带来几大好处:
- 前瞻性风险管理:FMEA 有助于在问题出现之前对其进行预测,从而降低发生代价高昂的错误的可能性。
- 风险优先排序: 它使企业能够根据风险的严重性和可能性来确定风险的优先级,从而制定更有针对性的维护策略。
- 知情决策:FMEA 提供了一种了解故障影响的结构化方法,有助于做出明智的设计和运营决策。
- 遵守法规:许多行业都要求 FMEA 符合安全和质量标准,因此它对于降低与不合规相关的法律风险至关重要。
- 降低成本:FMEA 有助于制定基于风险的维护战略,确定关键设备的优先次序,最大限度地减少代价高昂的故障和停机时间。及早解决潜在故障可大大降低与返工、召回或保修索赔相关的成本。
- 文档和知识共享:FMEA 为潜在的故障模式和缓解策略创建了文档记录,可供未来项目参考。
- 持续改进:从 FMEA 中获得的见解有助于不断改进流程和系统,培养一种持续改进的文化。
通过减轻或消除所发现的每一个风险和潜在故障,都有助于为您的运营奠定更坚实的基础。通过实施 FMEA,您的工作重心将从仅仅设想最佳绩效转变为积极实施今天的实践,从而实现明天的预期成果。
安全仪表系统 (SIS) 中的 FMEA
Operational safety relies heavily on Safety Instrumented Systems (SIS), where Safety Instrumented Functions (SIFs) perform key safety actions to reduce risks, such as shutting down a process or isolating equipment during hazardous situations.
FMEA dives deep into the components of Safety Instrumented Functions (SIFs). By conducting FMEA, you can uncover how each part—like sensors, logic solvers, and final elements—might fail and what those failures could mean for safety. For instance, if a safety valve is part of a SIF, FMEA helps identify how failure modes like valve sticking or sensor inaccuracies could impact its ability to perform its safety function.
The FMEA process for this device begins by generating a list of potentially dangerous failures. If they occur, these failures will defeat the safety mission of the device when there is a demand from the process. Specialists then do a study to estimate the contribution of each identified failure mode to the overall number of dangerous failures.
As some dangerous failures are more common than others, this contribution or weight factor (in %) is included. It is important to note that the total weight factors of all dangerous failures of the device under study cannot exceed 100%.
从 FMEA 研究中收集的信息可用于将设备确定的危险故障模式与设备定期测试所用的验证测试程序进行比较。这项检查旨在确定设备 FMEA 中确定的危险故障会在任何验证测试程序步骤中出现。
例如,如果确定通过正确应用验证测试程序可以检测出 8 种已识别的危险故障模式中的 7 种,而这 7 种模式合计占 FMEA 中已识别的所有危险故障的 90%,那么我们就可以得出结论,即 测试覆盖因子 (TCF)即 设备的验证测试程序的测试覆盖因子 (TCF) 为 90%。
FMEA 在 PFD 计算中的作用
在计算设备的按需故障概率 (PFD) 时,λd 是一个重要的组成部分,因为它反映了在工艺对设备提出要求之前,如果不及时发现可能导致安全事故的危险故障的数量。TCF 有助于确定有多少λd故障可以在验证测试期间检测到,因此是整个设备 PFD 计算中的一个重要因素。
另一个关键要素是任务时间(MT)。它表示安全仪表功能(SIF)在不进行大修或更换的情况下必须有效运行的时间。与制造商规定的设备何时需要更换不同,任务时间是根据每个 SIF 组件的具体需求量身定制的。
Why does this matter? Because with imperfect proof testing (i.e., where the TFC is less than 100%) Mission Time plays a vital role in managing risks associated with dangerous failures.
A well-defined Mission Time helps us gauge how long we can expect our SIF to function safely before risks accumulate.
This is illustrated in the below figure (Mission Time 20 years):
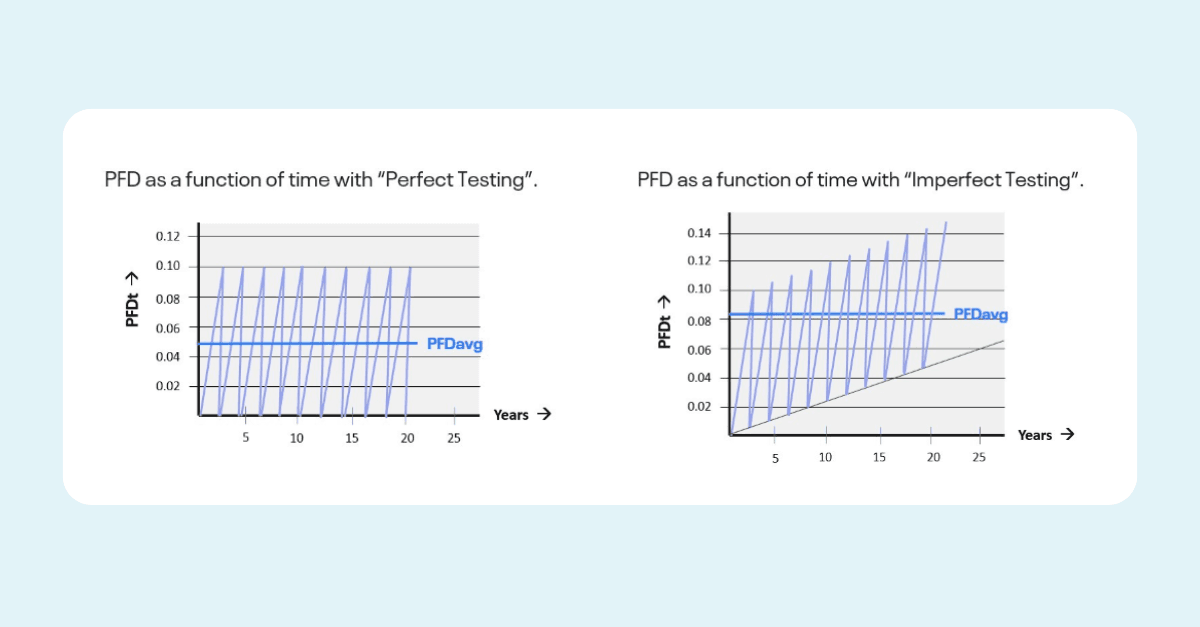
将 MT 纳入 PFD 计算可深入了解安全措施的有效性,为维护和测试间隔提供指导。TCF 和 PFD 之间的相互作用凸显了它们在确保 SIF 可靠性方面的重要性。
TCF 越高(接近 100% ),表明检测到的危险故障越多,从而降低了有效 λd 从而减少有效 λ d,降低 PFD。这种关系强调了 TCF 和λd在评估安全关键型应用中 SIF 的可靠性和安全性方面的重要性。
PFD 反映了安全功能在需要时失效的可能性,它受测试检测危险故障的程度影响。包含 TCF 的平均 PFD 计算公式如下:

在这个等式中
- TCF 表示验证测试在识别危险故障方面的有效性,从 0% 到 100% 不等。
- (1 - TCF)表示这些测试仍未检测到的危险故障比例。
- λd是可能导致按需故障的危险故障率。
- Ti是证明测试之间的间隔时间。
- MT表示 SIF 的任务时间。
如 TCF 所示,每次验证测试只能发现一小部分危险故障。这意味着,即使进行了有效的测试,一些故障仍可能未被发现,从而使风险随着时间的推移而加剧。因此,了解 TCF 如何影响 PFD 至关重要;TCF 越高,PFD 越低,表明风险缓解越有效。
反之,如果 TCF 较低,未检测到故障的可能性就会增加,因此需要更频繁地进行验证测试,以保持安全完整性。因此,通过严格的测试协议优化 TCF 不仅能提高故障检测能力,还能在确保 PFD 保持在符合安全标准的可接受范围内发挥关键作用。
利用 FMEA 和 Cenosco 的 IMS 提高运行可靠性
正如我们所见,FMEA 有助于提高运行可靠性。通过识别潜在的故障模式并评估其影响,它使企业能够主动管理风险并提高资产效率。
FMEA 是一种多用途的有效方法,可集成到其他流程中,如安全仪表系统中的流程。通过对关键安全组件进行全面评估,FMEA 可以及时制定风险缓解策略,并为测试间隔的决策提供信息,从而确保安全系统保持可靠和有效。
这种方法不仅加强了安全协议,还优化了资源配置,最终使石油和天然气行业的运营更具弹性。如果您正在寻找一种方法来提高您工厂的工艺可靠性,我们的完整性管理系统(IMS)可以为您提供帮助。请填写下表并申请演示!
Request a Demo
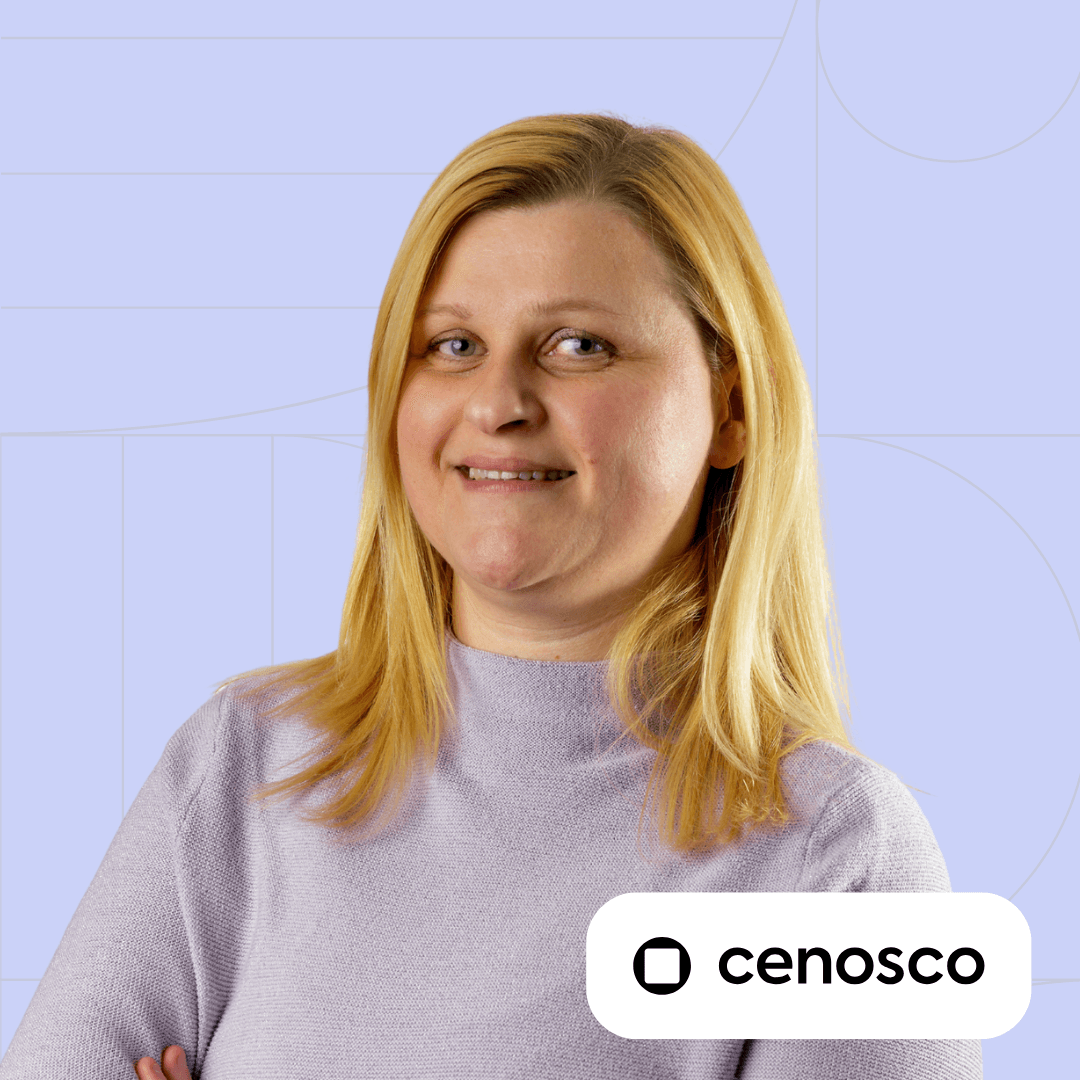
Denis Tkalec Technical writer
Denis Tkalec is a technical writer at Cenosco, specializing in asset integrity management software since 2022. With a background in education and six years in marketing, she turns complex topics into clear, user-friendly content. Inspired by Camus’s belief that “a writer keeps civilization from destroying itself,” she brings precision and care to every manual.