When it comes to ensuring operational reliability, many companies struggle to grasp the value of a structured approach like Failure Mode and Effects Analysis (FMEA) and the need for methods that boost operational efficiency.
It’s easy to envision the end goal—smooth operations and flawless performance—without considering the essential steps that lead there. However, without a clear understanding of potential failures and their impacts, businesses may find themselves facing unexpected disruptions that could have been prevented.
In this article we will explore the FMEA process in detail, highlighting its importance in identifying potential failure modes, assessing risks, shaping maintenance strategies by prioritizing equipment for maintenance, and implementing effective corrective actions to enhance operational reliability in the oil and gas industry.
FMEA: What is it?
Failure Mode and Effects Analysis (FMEA) is a systematic method designed to identify and evaluate potential problems and failure modes in systems, products, or processes. By analyzing these risks before they turn into real issues, FMEA enhances the overall reliability of designs and operations
The process typically involves:
- Identifying Failure Modes: Recognizing how and where failures might occur.
- Analyzing Effects: Assessing the consequences of these failures on the system or customer.
- Prioritizing Risks: Ranking failure modes based on severity, occurrence likelihood, and detectability.
- Developing recommendations for mitigation: Based on the analysis, FMEA suggests specific steps to reduce or prevent risks, including design modifications, process enhancements, training initiatives, or extra inspections.
This methodology relies on a team of experts who systematically analyze the system or product to assess the likelihood of various failure modes and their effects. The insights gained from this analysis not only inform the development of corrective actions aimed at mitigating potential failures but also help establish priorities for maintenance, ensuring that the most critical issues are addressed first.
What is a Failure Mode
But what exactly is a failure mode? A failure mode refers to the specific way a system, component, or process fails to perform its intended function. It describes the various ways in which something can fail, such as through physical damage, loss of functionality, or operational inefficiencies.
For example, in the oil and gas industry, common failure modes might include pipeline leaks due to corrosion, equipment malfunctions, or sensor failures.
Let’s put this into perspective with something we all rely on: your home heating system. This system depends on a furnace to generate warmth, which is then distributed through a network of ducts.
Now, picture this: it’s the dead of winter, and your furnace suddenly stops working. Why? Perhaps the air filter is clogged, the thermostat isn’t functioning properly, or there’s a gas leak. Each of these scenarios represents a failure mode—specific events that can lead to your heating system failing to keep your home warm.
What is Effect Analysis
In the world of FMEA, identifying failure modes is just the beginning. The goal is to analyze potential impacts (or effects, the “E” in FMEA) of the failures and prioritize actions to address them before they result in a freezing cold house or even worse, a costly emergency repair.
Types of FMEA
In the oil and gas sector, distinct types of Failure Modes and Effects Analysis (FMEA) are tailored to address specific operational needs and enhance safety and reliability. Here are the main types:
- Design FMEA (DFMEA): Focuses on identifying potential failures in the design phase of assets such as drilling rigs or pipelines.
- Process FMEA (PFMEA): Targets risks associated with manufacturing or operational processes, such as refining or extraction methods.
- Functional FMEA (FFMEA): Analyzes the functions of safety-critical systems, such as pressure relief valves, and their failures and is a vital tool to develop a risk-based maintenance approach.
The FMEA Process
The FMEA process typically follows a series of steps:
- Planning & Preparation: Assemble a cross-functional team with expertise in various areas such as engineering, operations, maintenance, and safety. Define the scope of the FMEA, including the specific systems or processes being evaluated and the objectives of the analysis.
- Systemization: Break down the system into its components to facilitate detailed analysis. This involves identifying subsystems and their interfaces, which is critical in complex oil and gas operations where interactions can significantly impact performance.
- Function Analysis: Identify the functions of each component within the system. In an oil and gas context, this could include functions such as pressure regulation, flow control, or safety shutdown mechanisms.
- Failure Analysis: Determine potential failure modes for each function identified. This step involves brainstorming to identify the possible failures that could prevent components from performing their intended functions, such as valve malfunctions or sensor failures. To gather data on failure modes. It can be beneficial to consult various sources, including OEM maintenance manuals, engineering process diagrams, maintenance records and history, operational experience, incident reports, and images of the equipment.
- Cause Analysis: Find out what causes each failure mode through in-depth analysis and data collection. This step uncovers the root factors triggering potential failures.
- Risk Analysis: Evaluate each failure mode based on its:
- Severity: Rated from 1 to 10, with a high score indicating severe risk.
- Probability: Rated from 1 to 10, where a high score reflects a greater likelihood of failure.
- Detection: Rated from 1 to 10, with a high score indicating poor detection capability.
- Risk Prioritization: Based on the probability, detection, and severity rating, rank failure modes to determine which ones require further examination.
Risk Priority = Severity x Occurrence x Detection
- Optimization: Develop action plans to mitigate high-priority risks identified in the previous step. This may involve redesigning components, implementing additional safety measures and inspections, or enhancing maintenance procedures to reduce failure likelihood.
- Documentation: Record all findings, decisions made during the analysis, and lessons learned for future reference. This documentation should include a summary of identified high-risk failures and the corrective actions taken to address them.
Importance of FMEA
Think of FMEA as your operational safety net that not only safeguards your operations but also offers several key benefits:
- Proactive Risk Management: FMEA helps anticipate problems before they arise, reducing the likelihood of costly errors.
- Risk Prioritization: It allows organizations to prioritize risks based on their severity and likelihood, facilitating a more focused maintenance strategy.
- Informed Decision-Making: FMEA provides a structured approach to understanding failure impacts, which aids in making informed design and operational decisions.
- Regulatory Compliance: Many industries require FMEA to meet safety and quality standards, making it essential for reducing legal risks associated with non-compliance.
- Cost Reduction: FMEA helps develop a risk-based maintenance strategy that prioritizes critical equipment, minimizing costly failures and downtime. Addressing potential failures early can significantly lower costs associated with rework, recalls, or warranty claims.
- Documentation and Knowledge Sharing: FMEA creates a documented record of potential failure modes and mitigation strategies, which can be referenced for future projects.
- Continuous Improvement: The insights gained from FMEA contribute to ongoing improvements in processes and systems, fostering a culture of continuous enhancement.
Each risk identified and every potential failure addressed through mitigation or elimination contributes to a stronger foundation for your operations. By implementing FMEA, your focus transitions from simply merely envisioning optimal performance to actively implementing the practices today that will lead you to achieve that desired outcome tomorrow.
FMEA in Safety Instrumented System (SIS)
Operational safety relies heavily on Safety Instrumented Systems (SIS), where Safety Instrumented Functions (SIFs) perform key safety actions to reduce risks, such as shutting down a process or isolating equipment during hazardous situations.
FMEA dives deep into the components of Safety Instrumented Functions (SIFs). By conducting FMEA, you can uncover how each part—like sensors, logic solvers, and final elements—might fail and what those failures could mean for safety. For instance, if a safety valve is part of a SIF, FMEA helps identify how failure modes like valve sticking or sensor inaccuracies could impact its ability to perform its safety function.
The FMEA process for this device begins by generating a list of potentially dangerous failures. If they occur, these failures will defeat the safety mission of the device when there is a demand from the process. Specialists then do a study to estimate the contribution of each identified failure mode to the overall number of dangerous failures.
As some dangerous failures are more common than others, this contribution or weight factor (in %) is included. It is important to note that the total weight factors of all dangerous failures of the device under study cannot exceed 100%.
The information gathered from the FMEA study can be used to compare the dangerous failure modes identified for the device against the Proof Test Procedure used for periodic testing of the device. This examination looks to determine which dangerous failures identified in the FMEA of the device will be caught in any of the Proof Test Procedures’ steps.
For instance, if it is determined that 7 out of 8 identified dangerous failure modes can be detected by properly applying the Proof Test Procedure, and these 7 modes collectively account for 90% of all dangerous failures identified in the FMEA, we can conclude that the Test Coverage Factor (TCF) of the device’s Proof Test Procedure is 90%.
FMEA’s Role in PFD Calculations
When calculating the Probability of Failure on Demand (PFD) of a device, λd is a critical component, as it reflects the number of dangerous failures that could potentially lead to safety incidents if not caught before a demand on the device occurs from the process. The TCF helps determine how many of these λd failures can be detected during proof testing and is therefore an important factor in the overall device PFD calculation.
Another critical component is Mission Time (MT). It represents the period during which a Safety Instrumented Function (SIF) must operate effectively without major overhauls or replacements. Unlike Useful Life—defined by manufacturers for when equipment needs replacing—MT is tailored to the specific needs of each SIF component.
Why does this matter? Because with imperfect proof testing (i.e., where the TFC is less than 100%) Mission Time plays a vital role in managing risks associated with dangerous failures.
A well-defined Mission Time helps us gauge how long we can expect our SIF to function safely before risks accumulate.
This is illustrated in the below figure (Mission Time 20 years):
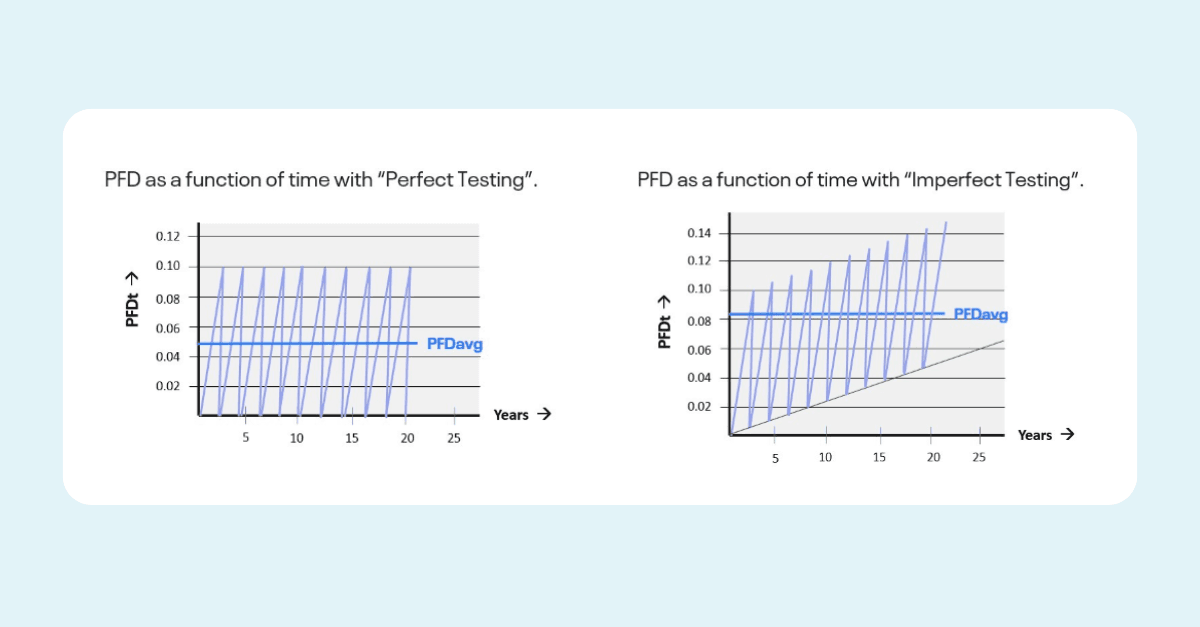
Incorporating MT into PFD calculations provides insights into safety measure effectiveness, guiding maintenance and testing intervals. The interplay between TCF and PFD highlights their importance in ensuring SIF reliability.
A higher TCF (close to 100%) indicates that more dangerous failures are detected, thereby reducing the effective λd and contributing to a lower PFD. This relationship emphasizes the importance of both TCF and λd in assessing the reliability and safety of SIFs in safety-critical applications.
The PFD reflects the likelihood that a safety function will fail when needed, and it is influenced by how well testing can detect dangerous failures. The formula for calculating average PFD incorporating TCF is as follows:

In this equation:
- TCF represents the effectiveness of proof tests in identifying dangerous faults, ranging from 0% to 100%.
- (1 – TCF) indicates the portion of dangerous failures that remain undetected by these tests.
- λd is the rate of dangerous failures that could lead to a failure on demand.
- Ti is the interval between proof tests.
- MT denotes the Mission Time of the SIF.
Every time a proof test is conducted, it identifies only a fraction of dangerous faults, as TCF indicates. This means that even with effective testing, some failures may go undetected, compounding the risk over time. As a result, understanding how TCF influences PFD is vital; a higher TCF leads to a lower PFD, indicating more effective risk mitigation.
Conversely, if TCF is low, the likelihood of undetected failures rises, necessitating more frequent proof tests to maintain safety integrity. Thus, optimizing TCF through rigorous testing protocols not only enhances fault detection but also plays a critical role in ensuring that PFD remains within acceptable limits for compliance with safety standards.
Strengthen Operational Reliability with FMEA and Cenosco’s IMS
As we have seen, FMEA helps enhance operational reliability. By identifying potential failure modes and assessing their impacts, it enables companies to proactively manage risks and improve the efficiency of their assets.
FMEA is a versatile and effective methodology that is integrated into other processes, such as those found in Safety Instrumented Systems. Through thorough evaluation of critical safety components, FMEA enables timely risk mitigation strategies and informs decisions regarding testing intervals, ensuring that safety systems remain reliable and effective.
This approach not only strengthens safety protocols but also optimizes resource allocation, ultimately leading to more resilient operations in the oil and gas industry. If you are looking for a way to enhance process reliability at your facility, our Integrity Management System (IMS) can help. Fill out the form below and request a demo!
Request a Demo
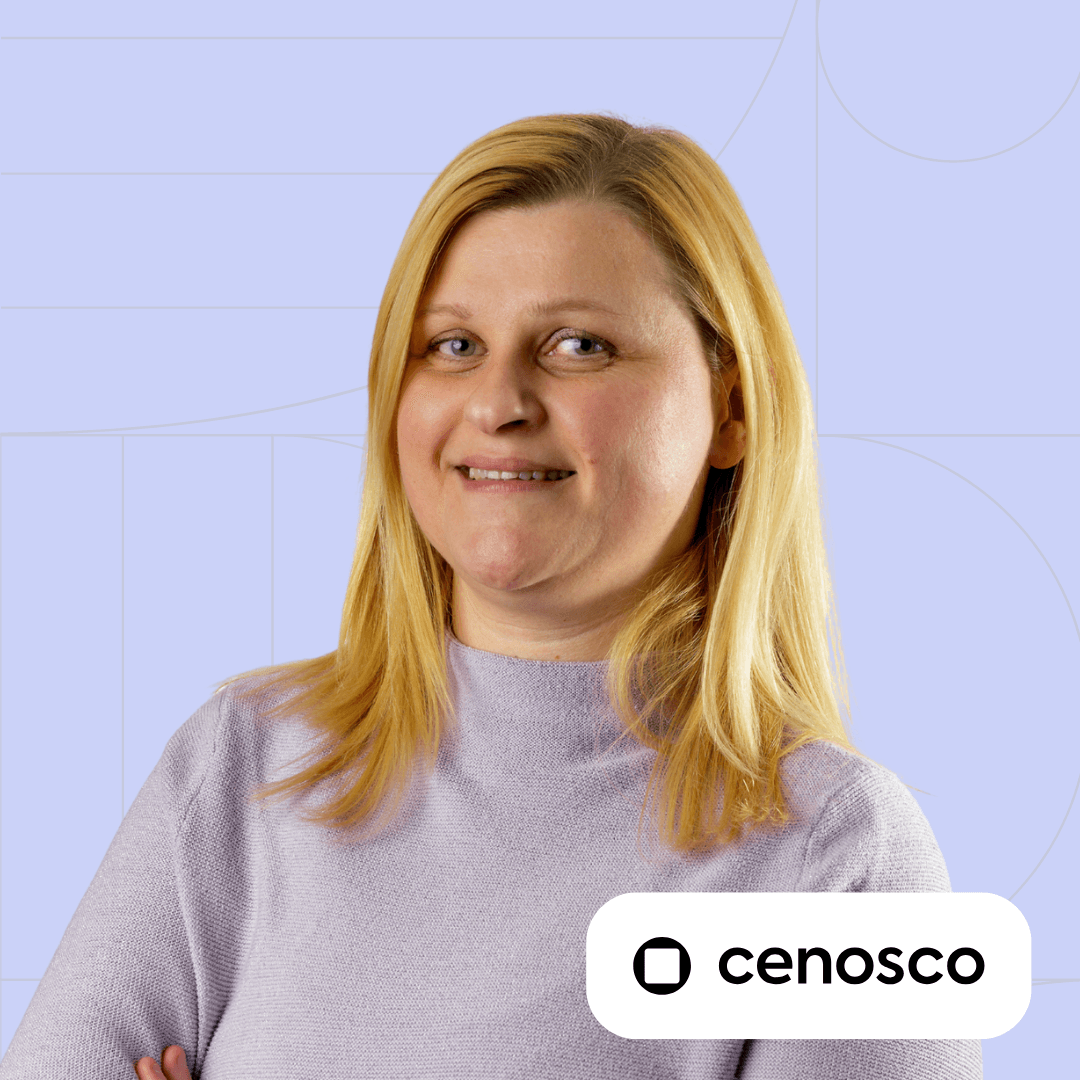
Denis Tkalec Technical writer
Denis Tkalec is a technical writer at Cenosco, specializing in asset integrity management software since 2022. With a background in education and six years in marketing, she turns complex topics into clear, user-friendly content. Inspired by Camus’s belief that “a writer keeps civilization from destroying itself,” she brings precision and care to every manual.