When it comes to ensuring operational reliability, many companies struggle to grasp the value of a structured approach like Failure Mode and Effects Analysis (FMEA) and the need for methods that boost operational efficiency.
It’s easy to envision the end goal—smooth operations and flawless performance—without considering the essential steps that lead there. However, without a clear understanding of potential failures and their impacts, businesses may find themselves facing unexpected disruptions that could have been prevented.
Dans cet article, nous examinerons en détail le processus AMDE, en soulignant son importance pour l'identification des modes de défaillance potentiels, l'évaluation des risques, l'élaboration de stratégies de maintenance en hiérarchisant les équipements à entretenir et la mise en œuvre d'actions correctives efficaces pour améliorer la fiabilité opérationnelle dans l'industrie pétrolière et gazière.
AMDE : Qu'est-ce que c'est ?
L'analyse des modes de défaillance et de leurs effets (AMDE) est une méthode systématique conçue pour identifier et évaluer les problèmes potentiels et les modes de défaillance dans les systèmes, les produits ou les processus. En analysant ces risques avant qu'ils ne se transforment en véritables problèmes, l'AMDE améliore la fiabilité globale des conceptions et des opérations.
Le processus implique généralement
- Identifier les modes de défaillance: Reconnaître comment et où les défaillances peuvent se produire.
- Analyse des effets: Évaluer les conséquences de ces défaillances sur le système ou le client.
- Hiérarchisation des risques: Classer les modes de défaillance en fonction de leur gravité, de leur probabilité d'occurrence et de leur détectabilité.
- Élaborer des recommandations pour l'atténuation des risques: Sur la base de l'analyse, l'AMDE propose des mesures spécifiques pour réduire ou prévenir les risques, notamment des modifications de la conception, des améliorations des processus, des initiatives de formation ou des inspections supplémentaires.
Cette méthodologie repose sur une équipe d'experts qui analysent systématiquement le système ou le produit afin d'évaluer la probabilité des différents modes de défaillance et leurs effets. Les informations tirées de cette analyse permettent non seulement d'élaborer des mesures correctives visant à atténuer les défaillances potentielles, mais aussi d'établir des priorités en matière de maintenance, en veillant à ce que les problèmes les plus critiques soient traités en premier.
Qu'est-ce qu'un mode de défaillance ?
But what exactly is a failure mode? A failure mode refers to the specific way a system, component, or process fails to perform its intended function. It describes the various ways in which something can fail, such as through physical damage, loss of functionality, or operational inefficiencies.
For example, in the oil and gas industry, common failure modes might include pipeline leaks due to corrosion, equipment malfunctions, or sensor failures.
Mettons cela en perspective avec un élément dont nous dépendons tous : le système de chauffage de votre maison. Ce système dépend d'un appareil de chauffage pour produire de la chaleur, qui est ensuite distribuée par un réseau de conduits.
Imaginez un peu : en plein hiver, votre chaudière s'arrête soudainement de fonctionner. Pourquoi ? Le filtre à air est peut-être obstrué, le thermostat ne fonctionne pas correctement ou il y a une fuite de gaz. Chacun de ces scénarios représente un mode de défaillance spécifique qui peut empêcher votre système de chauffage de garder votre maison au chaud.
Qu'est-ce que l'analyse des effets ?
Dans le monde de l'AMDE, l'identification des modes de défaillance n'est qu'un début. L'objectif est d'analyser les impacts potentiels (ou effets, le "E" de l'AMDE) des défaillances et de hiérarchiser les actions pour y remédier avant qu'elles ne se traduisent par une maison glaciale ou, pire encore, par une réparation d'urgence coûteuse.
Types d'AMDE
Dans le secteur du pétrole et du gaz, différents types d'analyse des modes de défaillance et de leurs effets (AMDE) sont conçus pour répondre à des besoins opérationnels spécifiques et améliorer la sécurité et la fiabilité. En voici les principaux types :
- AMDE de conception (DFMEA): Elle se concentre sur l'identification des défaillances potentielles lors de la phase de conception d'actifs tels que les plates-formes de forage ou les pipelines.
- AMDE de processus (AMDEF) : Cible les risques associés aux processus de fabrication ou d'exploitation, tels que les méthodes de raffinage ou d'extraction.
- AMDE fonctionnelle (AMDEF) : Elle analyse les fonctions des systèmes critiques pour la sécurité, tels que les soupapes de sûreté, et leurs défaillances, et constitue un outil essentiel pour développer une approche de la maintenance basée sur le risque.
Le processus AMDE
Le processus d'AMDE suit généralement une série d'étapes :
- Planification et préparation: Constituer une équipe interfonctionnelle ayant des compétences dans divers domaines tels que l'ingénierie, les opérations, la maintenance et la sécurité. Définir le champ d'application de l'AMDE, y compris les systèmes ou processus spécifiques évalués et les objectifs de l'analyse.
- Systématisation: Décomposer le système en ses composants pour faciliter l'analyse détaillée. Cela implique d'identifier les sous-systèmes et leurs interfaces, ce qui est essentiel dans les opérations pétrolières et gazières complexes où les interactions peuvent avoir un impact significatif sur les performances.
- Analyse des fonctions: Identifier les fonctions de chaque composant du système. Dans un contexte pétrolier et gazier, il peut s'agir de fonctions telles que la régulation de la pression, le contrôle du débit ou les mécanismes d'arrêt de sécurité.
- Analyse des défaillances: Déterminer les modes de défaillance potentiels pour chaque fonction identifiée. Cette étape implique un brainstorming pour identifier les défaillances possibles qui pourraient empêcher les composants de remplir les fonctions prévues, telles que les dysfonctionnements des vannes ou les défaillances des capteurs. Recueillir des données sur les modes de défaillance. Il peut être utile de consulter diverses sources, notamment les manuels de maintenance des équipementiers, les diagrammes de processus d'ingénierie, les dossiers et l'historique de maintenance, l'expérience opérationnelle, les rapports d'incidents et les images de l'équipement.
- Analyse des causes : Déterminer les causes de chaque mode de défaillance grâce à une analyse approfondie et à la collecte de données. Cette étape permet de découvrir les facteurs fondamentaux qui déclenchent les défaillances potentielles.
- Analyse des risques: Évaluer chaque mode de défaillance en fonction de ses caractéristiques :
- Gravité :Évaluée de 1 à 10, une note élevée indiquant un risque grave.
- Probabilité :Évaluée de 1 à 10, une note élevée correspond à une plus grande probabilité d'échec.
- Détection :Notée de 1 à 10, une note élevée indiquant une faible capacité de détection.
- Hiérarchisation des risques : Sur la base de la probabilité, de la détection et de la gravité, classer les modes de défaillance afin de déterminer ceux qui nécessitent un examen plus approfondi.
Priorité du risque = Gravité x Occurrence x Détection
- Optimization: Develop action plans to mitigate high-priority risks identified in the previous step. This may involve redesigning components, implementing additional safety measures and inspections, or enhancing maintenance procedures to reduce failure likelihood.
- Documentation: Consigner toutes les constatations, les décisions prises au cours de l'analyse et les enseignements tirés afin de pouvoir s'y référer ultérieurement. Cette documentation doit comprendre un résumé des défaillances à haut risque identifiées et des mesures correctives prises pour y remédier.
Importance de l'AMDE
Considérez l'AMDE comme votre filet de sécurité opérationnel qui non seulement protège vos opérations, mais offre également plusieurs avantages clés :
- Gestion proactive des risques: L'AMDE permet d'anticiper les problèmes avant qu'ils ne surviennent, réduisant ainsi la probabilité d'erreurs coûteuses.
- Hiérarchisation des risques : Il permet aux organisations de hiérarchiser les risques en fonction de leur gravité et de leur probabilité, ce qui facilite une stratégie de maintenance plus ciblée.
- Prise de décision éclairée: L'AMDE fournit une approche structurée pour comprendre l'impact des défaillances, ce qui permet de prendre des décisions éclairées en matière de conception et d'exploitation.
- Conformité réglementaire: De nombreuses industries exigent que l'AMDE soit conforme aux normes de sécurité et de qualité, ce qui la rend essentielle pour réduire les risques juridiques associés à la non-conformité.
- Réduction des coûts: L'AMDE permet d'élaborer une stratégie de maintenance basée sur le risque qui donne la priorité aux équipements critiques, minimisant ainsi les défaillances et les temps d'arrêt coûteux. Le traitement précoce des défaillances potentielles peut réduire de manière significative les coûts associés aux travaux de reprise, aux rappels ou aux réclamations au titre de la garantie.
- Documentation et partage des connaissances : L'AMDE crée un dossier documenté sur les modes de défaillance potentiels et les stratégies d'atténuation, qui peut être utilisé pour des projets futurs.
- Amélioration continue : Les connaissances acquises grâce à l'AMDE contribuent à l'amélioration continue des processus et des systèmes, ce qui favorise une culture d'amélioration continue.
Chaque risque identifié et chaque défaillance potentielle traitée par l'atténuation ou l'élimination contribuent à renforcer les bases de vos opérations. En mettant en œuvre l'AMDE, vous passez de la simple vision d'une performance optimale à la mise en œuvre active des pratiques d'aujourd'hui qui vous permettront d'atteindre le résultat souhaité demain.
AMDE dans les systèmes instrumentés de sécurité (SIS)
Operational safety relies heavily on Safety Instrumented Systems (SIS), where Safety Instrumented Functions (SIFs) perform key safety actions to reduce risks, such as shutting down a process or isolating equipment during hazardous situations.
FMEA dives deep into the components of Safety Instrumented Functions (SIFs). By conducting FMEA, you can uncover how each part—like sensors, logic solvers, and final elements—might fail and what those failures could mean for safety. For instance, if a safety valve is part of a SIF, FMEA helps identify how failure modes like valve sticking or sensor inaccuracies could impact its ability to perform its safety function.
The FMEA process for this device begins by generating a list of potentially dangerous failures. If they occur, these failures will defeat the safety mission of the device when there is a demand from the process. Specialists then do a study to estimate the contribution of each identified failure mode to the overall number of dangerous failures.
As some dangerous failures are more common than others, this contribution or weight factor (in %) is included. It is important to note that the total weight factors of all dangerous failures of the device under study cannot exceed 100%.
Les informations recueillies dans le cadre de l'AMDE peuvent être utilisées pour comparer les modes de défaillance dangereux identifiés pour le dispositif avec la procédure de test d'épreuve utilisée pour les essais périodiques du dispositif. Cet examen vise à déterminer quelles défaillances dangereuses identifiées dans l'AMDE du dispositif seront détectées dans l'une ou l'autre des étapes de la procédure d'essai.
Par exemple, s'il est établi que 7 des 8 modes de défaillance dangereux identifiés peuvent être détectés en appliquant correctement la procédure de test d'épreuve, et que ces 7 modes représentent collectivement 90 % de toutes les défaillances dangereuses identifiées dans l'AMDE, nous pouvons conclure que le facteur de couverture des tests (TCF) de la procédure d'épreuve du dispositif est de 90 %.
Rôle de l'AMDE dans le calcul des VFI
Lors du calcul de la probabilité de défaillance à la demande (PFD) d'un dispositif, λd est un élément critique, car il reflète le nombre de défaillances dangereuses qui pourraient potentiellement conduire à des incidents de sécurité si elles ne sont pas détectées avant que le dispositif ne soit sollicité par le processus. Le TCF aide à déterminer combien de ces défaillances λ d peuvent être détectées pendant les essais de validation et constitue donc un facteur important dans le calcul de la DFP globale du dispositif.
La durée de la mission (MT) est un autre élément essentiel. Elle représente la période pendant laquelle une fonction instrumentée de sécurité (FIS) doit fonctionner efficacement sans nécessiter de révisions ou de remplacements majeurs. Contrairement à la durée de vie utile, définie par les fabricants pour déterminer le moment où l'équipement doit être remplacé, la durée de mission est adaptée aux besoins spécifiques de chaque composant de la fonction instrumentée de sécurité.
Why does this matter? Because with imperfect proof testing (i.e., where the TFC is less than 100%) Mission Time plays a vital role in managing risks associated with dangerous failures.
A well-defined Mission Time helps us gauge how long we can expect our SIF to function safely before risks accumulate.
This is illustrated in the below figure (Mission Time 20 years):
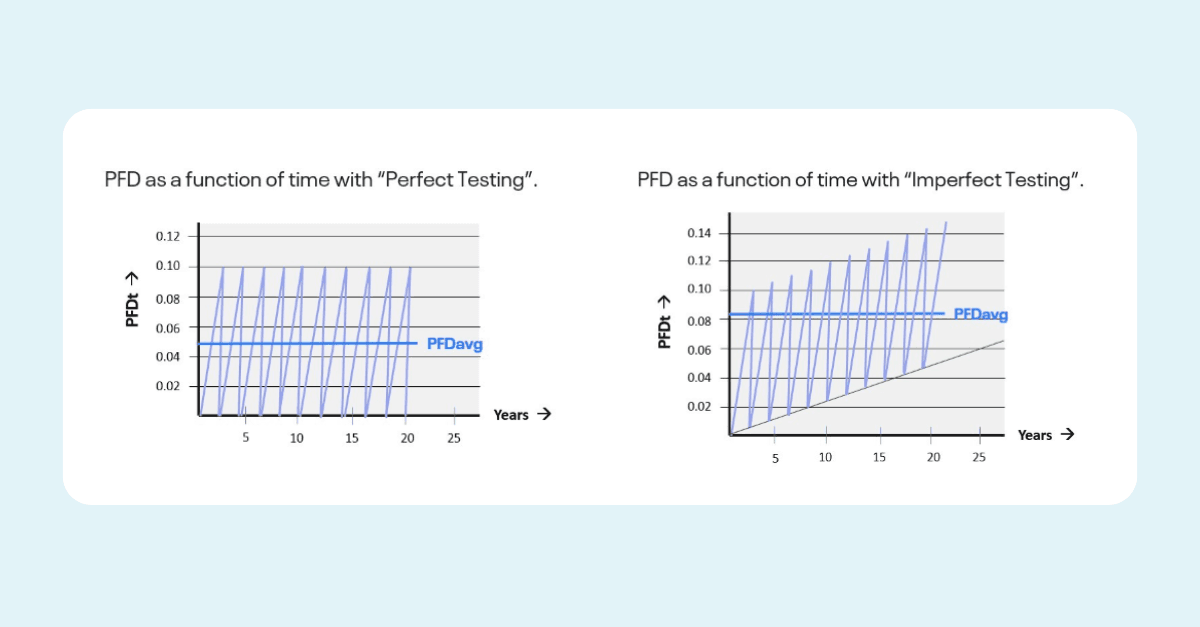
L'intégration de la MT dans les calculs de la DFP permet de mieux comprendre l'efficacité des mesures de sécurité et d'orienter les intervalles de maintenance et d'essai. L'interaction entre le TCF et la PFD met en évidence leur importance pour garantir la fiabilité des installations de production d'énergie.
Un TCF plus élevé (proche de 100 %) indique que davantage de défaillances dangereuses sont détectées, ce qui réduit le λd et contribue à réduire la DFP. Cette relation souligne l'importance du TCF et du λd dans l'évaluation de la fiabilité et de la sécurité des FIS dans les applications critiques pour la sécurité.
La DFP reflète la probabilité qu'une fonction de sécurité tombe en panne en cas de besoin, et elle est influencée par la capacité des essais à détecter les défaillances dangereuses. La formule de calcul de la DFP moyenne intégrant le TCF est la suivante :

Dans cette équation :
- Le TCF représente l'efficacité des tests de preuve dans l'identification des fautes dangereuses, allant de 0% à 100%.
- (1 - TCF)indique la part des défaillances dangereuses qui ne sont pas détectées par ces tests.
- λdest le taux de défaillances dangereuses susceptibles d'entraîner une défaillance sur demande.
- Tiest l'intervalle entre les tests de preuve.
- MTindique la durée de la mission du FIS.
Chaque fois qu'un test d'épreuve est effectué, il n'identifie qu'une fraction des défauts dangereux, comme l'indique le TCF. Cela signifie que même avec des tests efficaces, certaines défaillances peuvent ne pas être détectées, ce qui aggrave le risque au fil du temps. Il est donc essentiel de comprendre l'influence du TCF sur la DFP ; un TCF élevé conduit à une DFP plus faible, ce qui indique une atténuation plus efficace des risques.
Inversement, si le TCF est faible, la probabilité de défaillances non détectées augmente, ce qui nécessite des tests de preuve plus fréquents pour maintenir l'intégrité de la sécurité. Ainsi, l'optimisation du TCF grâce à des protocoles d'essai rigoureux permet non seulement d'améliorer la détection des défaillances, mais joue également un rôle essentiel en garantissant que la DFP reste dans des limites acceptables pour le respect des normes de sécurité.
Renforcer la fiabilité opérationnelle grâce à l'AMDE et à l'IMS de Cenosco
Comme nous l'avons vu, l'AMDE contribue à améliorer la fiabilité opérationnelle. En identifiant les modes de défaillance potentiels et en évaluant leurs impacts, elle permet aux entreprises de gérer les risques de manière proactive et d'améliorer l'efficacité de leurs actifs.
L'AMDE est une méthodologie polyvalente et efficace qui s'intègre dans d'autres processus, tels que ceux des systèmes instrumentés de sécurité. Grâce à une évaluation approfondie des composants de sécurité critiques, l'AMDE permet de mettre en place des stratégies d'atténuation des risques en temps opportun et d'éclairer les décisions concernant les intervalles de test, garantissant ainsi la fiabilité et l'efficacité des systèmes de sécurité.
Cette approche permet non seulement de renforcer les protocoles de sécurité, mais aussi d'optimiser l'affectation des ressources, ce qui se traduit en fin de compte par des opérations plus résilientes dans l'industrie pétrolière et gazière. Si vous cherchez un moyen d'améliorer la fiabilité des processus dans votre installation, notre système de gestion de l'intégrité (IMS) peut vous aider. Remplissez le formulaire ci-dessous et demandez une démonstration !
Request a Demo
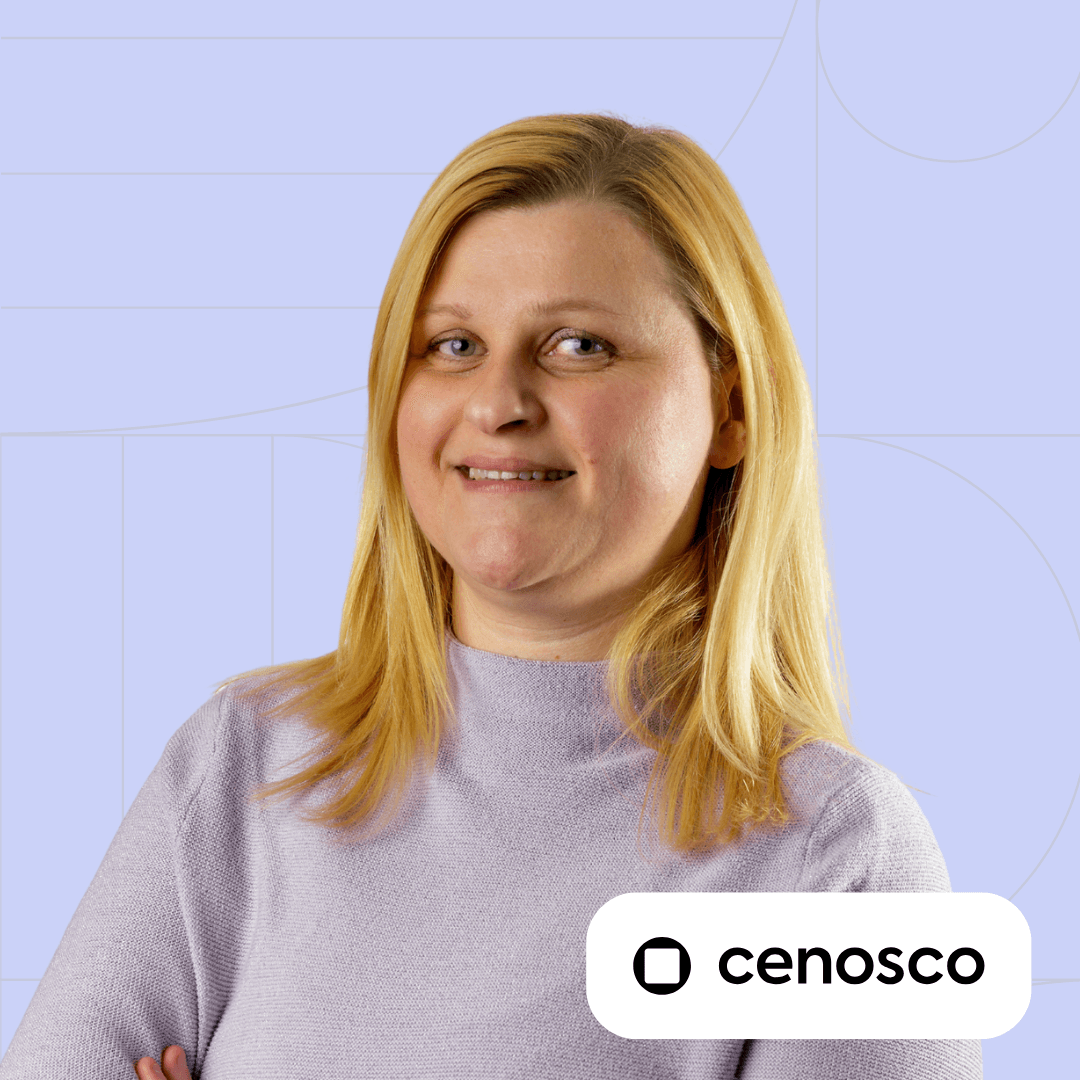
Denis Tkalec Technical writer
Denis Tkalec is a technical writer at Cenosco, specializing in asset integrity management software since 2022. With a background in education and six years in marketing, she turns complex topics into clear, user-friendly content. Inspired by Camus’s belief that “a writer keeps civilization from destroying itself,” she brings precision and care to every manual.