When it comes to ensuring operational reliability, many companies struggle to grasp the value of a structured approach like Failure Mode and Effects Analysis (FMEA) and the need for methods that boost operational efficiency.
It’s easy to envision the end goal—smooth operations and flawless performance—without considering the essential steps that lead there. However, without a clear understanding of potential failures and their impacts, businesses may find themselves facing unexpected disruptions that could have been prevented.
В этой статье мы подробно рассмотрим процесс FMEA, подчеркнув его важность для выявления потенциальных режимов отказов, оценки рисков, формирования стратегии технического обслуживания путем определения приоритетов оборудования для технического обслуживания и реализации эффективных корректирующих действий для повышения эксплуатационной надежности в нефтегазовой отрасли.
FMEA: что это такое?
Анализ режимов и последствий отказов (FMEA) - это систематический метод, предназначенный для выявления и оценки потенциальных проблем и режимов отказов в системах, продуктах или процессах. Анализируя эти риски до того, как они превратятся в реальные проблемы, FMEA повышает общую надежность конструкций и операций.
Обычно этот процесс включает в себя:
- Идентификация режимов отказов: Распознавание того, как и где могут происходить сбои.
- Анализ последствий: Оценка последствий этих сбоев для системы или клиента.
- Определение приоритетов рисков: Ранжирование режимов отказа по степени серьезности, вероятности возникновения и возможности обнаружения.
- Разработка рекомендаций по снижению рисков: На основе анализа FMEA предлагает конкретные шаги по снижению или предотвращению рисков, включая модификацию конструкции, усовершенствование процесса, инициативы по обучению или дополнительные проверки.
Эта методология опирается на команду экспертов, которые систематически анализируют систему или изделие для оценки вероятности возникновения различных режимов отказа и их последствий. Полученные в результате анализа выводы не только служат основой для разработки корректирующих действий, направленных на смягчение последствий потенциальных отказов, но и помогают определить приоритеты технического обслуживания, гарантируя, что наиболее важные вопросы будут решаться в первую очередь.
Что такое режим отказа
But what exactly is a failure mode? A failure mode refers to the specific way a system, component, or process fails to perform its intended function. It describes the various ways in which something can fail, such as through physical damage, loss of functionality, or operational inefficiencies.
For example, in the oil and gas industry, common failure modes might include pipeline leaks due to corrosion, equipment malfunctions, or sensor failures.
Давайте рассмотрим это на примере того, на что мы все полагаемся: вашей домашней системы отопления. Эта система зависит от печи, генерирующей тепло, которое затем распределяется по сети воздуховодов.
Представьте себе: на дворе зима, а ваша печь внезапно перестала работать. Почему? Возможно, засорился воздушный фильтр, неправильно работает термостат или произошла утечка газа. Каждый из этих сценариев представляет собой определенный режим отказа, который может привести к тому, что ваша система отопления не сможет поддерживать тепло в вашем доме.
Что такое анализ эффектов
В мире FMEA определение режимов отказов - это только начало. Цель состоит в том, чтобы проанализировать потенциальные последствия (или эффекты, "E" в FMEA) отказов и определить приоритетность действий по их устранению, прежде чем они приведут к замерзанию дома или, что еще хуже, к дорогостоящему аварийному ремонту.
Типы FMEA
В нефтегазовом секторе для решения конкретных производственных задач и повышения безопасности и надежности применяются различные виды анализа режимов и последствий отказов (FMEA). Вот основные типы:
- Проектирование FMEA (DFMEA): Направлен на выявление потенциальных отказов на этапе проектирования таких объектов, как буровые установки или трубопроводы.
- FMEA процесса (PFMEA): Нацелен на риски, связанные с производственными или операционными процессами, такими как методы рафинирования или экстракции.
- Функциональный FMEA (FFMEA): Анализирует функции критически важных для безопасности систем, таких как предохранительные клапаны, и их отказы, и является важнейшим инструментом для разработки подхода к техническому обслуживанию, основанного на оценке рисков.
Процесс FMEA
Процесс FMEA обычно состоит из нескольких этапов:
- Планирование и подготовка: Соберите межфункциональную команду с опытом работы в различных областях, таких как проектирование, эксплуатация, техническое обслуживание и безопасность. Определите область применения FMEA, включая конкретные системы или процессы, которые будут оцениваться, и цели анализа.
- Систематизация: Разбиение системы на компоненты для облегчения детального анализа. Это включает в себя определение подсистем и их интерфейсов, что очень важно в сложных нефтегазовых операциях, где взаимодействие может существенно повлиять на производительность.
- Функциональный анализ: Определите функции каждого компонента в системе. В контексте нефтегазовой отрасли это может включать такие функции, как регулирование давления, контроль расхода или механизмы аварийного отключения.
- Анализ отказов: Определите потенциальные режимы отказов для каждой выявленной функции. Этот шаг включает в себя мозговой штурм для определения возможных отказов, которые могут помешать компонентам выполнять свои функции, например, неисправность клапана или отказ датчика. Сбор данных о режимах отказов. Полезно обратиться к различным источникам, включая руководства по техническому обслуживанию производителей оборудования, технологические схемы, записи и историю технического обслуживания, опыт эксплуатации, отчеты об инцидентах и изображения оборудования.
- Анализ причин: Выясните причину каждого вида отказа с помощью глубокого анализа и сбора данных. Этот шаг позволяет выявить коренные факторы, провоцирующие потенциальные отказы.
- Анализ рисков: Оцените каждый вид отказа на основе его:
- Серьезность:Оценивается от 1 до 10, высокий балл означает серьезный риск.
- Вероятность:Оценивается от 1 до 10, где высокий балл отражает большую вероятность неудачи.
- Обнаружение:Оценка от 1 до 10, высокий балл указывает на низкую способность к обнаружению.
- Приоритезация рисков: На основе оценки вероятности, обнаружения и серьезности проранжируйте режимы отказа, чтобы определить, какие из них требуют дальнейшего изучения.
Приоритет риска = Тяжесть х Возникновение х Обнаружение
- Optimization: Develop action plans to mitigate high-priority risks identified in the previous step. This may involve redesigning components, implementing additional safety measures and inspections, or enhancing maintenance procedures to reduce failure likelihood.
- Документация: Зафиксируйте все выводы, решения, принятые в ходе анализа, и извлеченные уроки для последующего использования. Эта документация должна включать краткое описание выявленных отказов с высоким риском и корректирующих действий, предпринятых для их устранения.
Важность FMEA
Считайте, что FMEA - это ваша операционная сеть безопасности, которая не только защищает ваши операции, но и предлагает несколько ключевых преимуществ:
- Проактивное управление рисками: FMEA помогает предвидеть проблемы до их возникновения, снижая вероятность дорогостоящих ошибок.
- Приоритизация рисков: Позволяет организациям определять приоритетность рисков в зависимости от их серьезности и вероятности, что способствует выработке более целенаправленной стратегии обслуживания.
- Обоснованное принятие решений: FMEA обеспечивает структурированный подход к пониманию последствий отказа, что помогает принимать обоснованные проектные и эксплуатационные решения.
- Соответствие нормативным требованиям: Многие отрасли требуют проведения FMEA для соблюдения стандартов безопасности и качества, что делает его необходимым для снижения юридических рисков, связанных с несоблюдением требований.
- Снижение затрат: FMEA помогает разработать стратегию технического обслуживания, основанную на оценке рисков, которая определяет приоритеты критически важного оборудования, сводя к минимуму дорогостоящие отказы и простои. Устранение потенциальных неисправностей на ранней стадии может значительно снизить затраты, связанные с доработкой, отзывами или гарантийными претензиями.
- Документация и обмен знаниями: FMEA создает документированную запись потенциальных режимов отказов и стратегий их устранения, на которую можно ссылаться в будущих проектах.
- Непрерывное совершенствование: Полученные в ходе FMEA знания способствуют постоянному совершенствованию процессов и систем, способствуя развитию культуры непрерывного совершенствования.
Каждый выявленный риск и каждый потенциальный сбой, устраненный путем смягчения или устранения, способствуют укреплению фундамента вашей деятельности. Внедряя FMEA, вы переходите от простого представления об оптимальной производительности к активному внедрению сегодняшних методов, которые приведут вас к достижению желаемого результата завтра.
FMEA в контрольно-измерительных системах безопасности (SIS)
Operational safety relies heavily on Safety Instrumented Systems (SIS), where Safety Instrumented Functions (SIFs) perform key safety actions to reduce risks, such as shutting down a process or isolating equipment during hazardous situations.
FMEA dives deep into the components of Safety Instrumented Functions (SIFs). By conducting FMEA, you can uncover how each part—like sensors, logic solvers, and final elements—might fail and what those failures could mean for safety. For instance, if a safety valve is part of a SIF, FMEA helps identify how failure modes like valve sticking or sensor inaccuracies could impact its ability to perform its safety function.
The FMEA process for this device begins by generating a list of potentially dangerous failures. If they occur, these failures will defeat the safety mission of the device when there is a demand from the process. Specialists then do a study to estimate the contribution of each identified failure mode to the overall number of dangerous failures.
As some dangerous failures are more common than others, this contribution or weight factor (in %) is included. It is important to note that the total weight factors of all dangerous failures of the device under study cannot exceed 100%.
Информация, полученная в ходе исследования FMEA, может быть использована для сравнения опасных режимов отказа, выявленных для устройства, с процедурой доказательных испытаний, используемой для периодического тестирования устройства. Это исследование позволяет определить, какие опасные отказы, выявленные в FMEA устройства, будут обнаружены на любом из этапов процедуры испытаний.
Например, если установлено, что 7 из 8 идентифицированных опасных режимов отказа могут быть обнаружены при правильном применении процедуры доказательных испытаний, и эти 7 режимов в совокупности составляют 90% всех опасных отказов, идентифицированных в FMEA, мы можем сделать вывод, что Коэффициент охвата испытаний (TCF) процедуры испытания устройства составляет 90%.
Роль FMEA в расчетах PFD
При расчете вероятности отказа по требованию (PFD) устройства, λd является критически важным компонентом, поскольку он отражает количество опасных отказов, которые могут привести к инцидентам безопасности, если не будут обнаружены до того, как на устройство поступит требование от технологического процесса. TCF помогает определить, сколько таких отказов λd может быть обнаружено в ходе испытаний на стойкость, и поэтому является важным фактором при расчете общего PFD устройства.
Еще одним важным компонентом является время выполнения миссии (MT). Оно представляет собой период, в течение которого функция прибора безопасности (SIF) должна эффективно работать без капитального ремонта или замены. В отличие от срока службы, определяемого производителями как время, когда оборудование нуждается в замене, срок службы зависит от конкретных потребностей каждого компонента SIF.
Why does this matter? Because with imperfect proof testing (i.e., where the TFC is less than 100%) Mission Time plays a vital role in managing risks associated with dangerous failures.
A well-defined Mission Time helps us gauge how long we can expect our SIF to function safely before risks accumulate.
This is illustrated in the below figure (Mission Time 20 years):
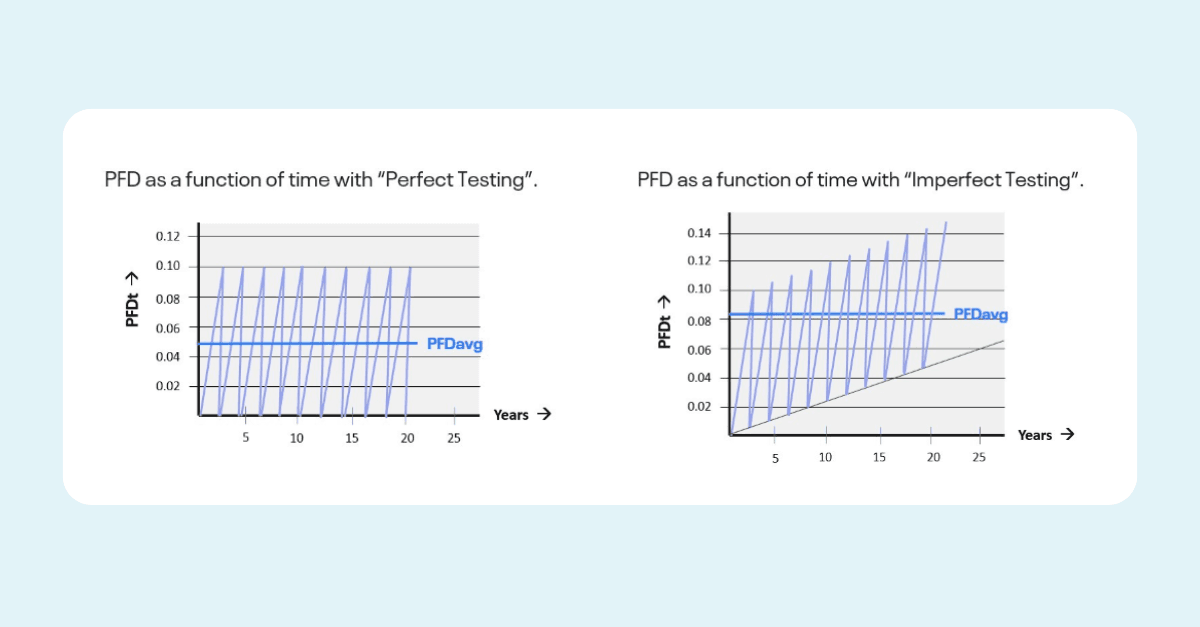
Включение MT в расчеты PFD дает представление об эффективности мер безопасности, определяя интервалы технического обслуживания и испытаний. Взаимосвязь между TCF и PFD подчеркивает их важность для обеспечения надежности SIF.
Более высокий TCF (близкий к 100%) указывает на то, что обнаруживается больше опасных отказов, что снижает эффективную λd и способствуя снижению PFD. Эта взаимосвязь подчеркивает важность TCF и λd при оценке надежности и безопасности SIF в критически важных приложениях.
PFD отражает вероятность того, что функция безопасности откажет в нужный момент, и зависит от того, насколько хорошо испытания могут выявить опасные отказы. Формула для расчета среднего PFD, включающего TCF, выглядит следующим образом:

В этом уравнении:
- TCF представляет собой эффективность пробных испытаний в выявлении опасных неисправностей, варьирующуюся от 0% до 100%.
- (1 - TCF)указывает на долю опасных отказов, которые остаются необнаруженными в ходе этих испытаний.
- λdэто частота опасных отказов, которые могут привести к отказу по требованию.
- Tiэто интервал между проверками доказательств.
- MTобозначает время миссии SIF.
Каждый раз, когда проводится пробное тестирование, оно выявляет лишь часть опасных неисправностей, как указывает TCF. Это означает, что даже при эффективном тестировании некоторые неисправности могут остаться необнаруженными, что со временем усугубляет риск. Таким образом, понимание того, как TCF влияет на PFD, является жизненно важным; более высокий TCF ведет к более низкому PFD, что свидетельствует о более эффективном снижении риска.
И наоборот, если TCF низкий, вероятность необнаруженных отказов возрастает, что требует более частых пробных испытаний для поддержания целостности системы безопасности. Таким образом, оптимизация TCF с помощью строгих протоколов испытаний не только улучшает обнаружение неисправностей, но и играет важную роль в обеспечении того, чтобы PFD оставался в допустимых пределах для соответствия стандартам безопасности.
Повышение эксплуатационной надежности с помощью FMEA и IMS от Cenosco
Как мы уже видели, FMEA помогает повысить эксплуатационную надежность. Выявляя потенциальные режимы отказов и оценивая их последствия, он позволяет компаниям проактивно управлять рисками и повышать эффективность своих активов.
FMEA - это универсальная и эффективная методология, которая интегрируется в другие процессы, например, в контрольно-измерительные системы безопасности. Благодаря тщательной оценке критических компонентов безопасности FMEA позволяет своевременно разрабатывать стратегии снижения рисков и принимать решения о периодичности испытаний, обеспечивая надежность и эффективность систем безопасности.
Такой подход не только укрепляет протоколы безопасности, но и оптимизирует распределение ресурсов, что в конечном итоге приводит к повышению надежности работы в нефтегазовой отрасли. Если вы ищете способ повысить надежность технологических процессов на вашем предприятии, наша система управления целостностью (IMS) может вам помочь. Заполните форму ниже и запросите демонстрацию!
Request a Demo
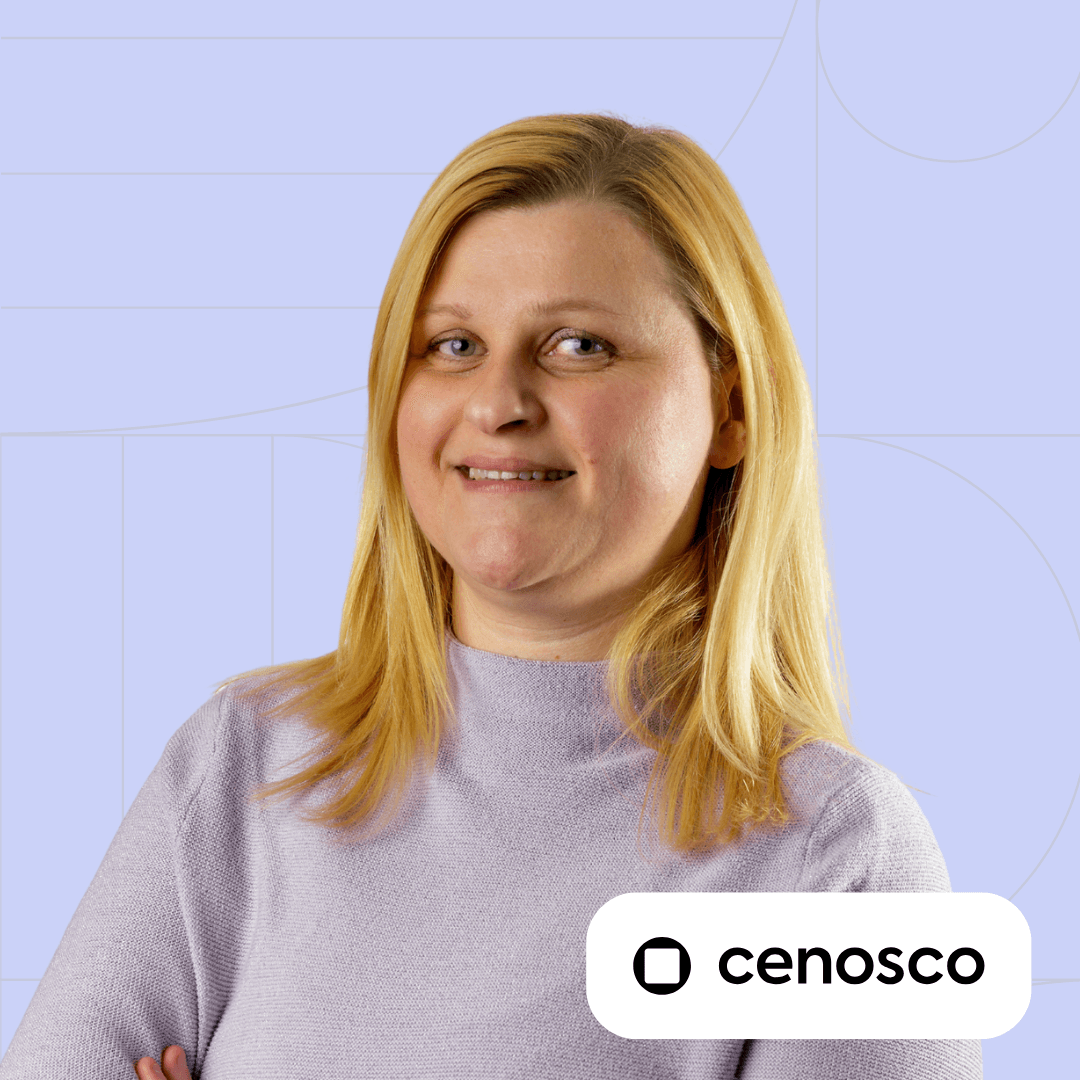
Denis Tkalec Technical writer
Denis Tkalec is a technical writer at Cenosco, specializing in asset integrity management software since 2022. With a background in education and six years in marketing, she turns complex topics into clear, user-friendly content. Inspired by Camus’s belief that “a writer keeps civilization from destroying itself,” she brings precision and care to every manual.