When it comes to ensuring operational reliability, many companies struggle to grasp the value of a structured approach like Failure Mode and Effects Analysis (FMEA) and the need for methods that boost operational efficiency.
It’s easy to envision the end goal—smooth operations and flawless performance—without considering the essential steps that lead there. However, without a clear understanding of potential failures and their impacts, businesses may find themselves facing unexpected disruptions that could have been prevented.
Neste artigo, vamos explorar o processo FMEA em pormenor, destacando a sua importância na identificação de potenciais modos de falha, na avaliação de riscos, na definição de estratégias de manutenção, dando prioridade ao equipamento para manutenção, e na implementação de acções corretivas eficazes para aumentar a fiabilidade operacional na indústria do petróleo e do gás.
FMEA: O que é?
A análise dos modos e efeitos de falha (FMEA) é um método sistemático concebido para identificar e avaliar potenciais problemas e modos de falha em sistemas, produtos ou processos. Ao analisar estes riscos antes de se transformarem em problemas reais, a FMEA aumenta a fiabilidade global dos projectos e operações
O processo envolve normalmente:
- Identificação de modos de falha: Reconhecer como e onde as falhas podem ocorrer.
- Análise dos efeitos: Avaliar as consequências destas falhas no sistema ou no cliente.
- Priorização de riscos: Classificar os modos de falha com base na gravidade, probabilidade de ocorrência e detetabilidade.
- Desenvolvimento de recomendações para mitigação: Com base na análise, a FMEA sugere passos específicos para reduzir ou prevenir riscos, incluindo modificações na conceção, melhorias no processo, iniciativas de formação ou inspecções adicionais.
Esta metodologia baseia-se numa equipa de especialistas que analisa sistematicamente o sistema ou produto para avaliar a probabilidade de vários modos de falha e os seus efeitos. Os conhecimentos obtidos com esta análise não só informam o desenvolvimento de acções corretivas destinadas a mitigar potenciais falhas, como também ajudam a estabelecer prioridades para a manutenção, garantindo que os problemas mais críticos são tratados em primeiro lugar.
O que é um modo de falha
But what exactly is a failure mode? A failure mode refers to the specific way a system, component, or process fails to perform its intended function. It describes the various ways in which something can fail, such as through physical damage, loss of functionality, or operational inefficiencies.
For example, in the oil and gas industry, common failure modes might include pipeline leaks due to corrosion, equipment malfunctions, or sensor failures.
Vamos pôr isto em perspetiva com algo em que todos confiamos: o sistema de aquecimento da nossa casa. Este sistema depende de um forno para gerar calor, que é depois distribuído através de uma rede de condutas.
Agora, imagine o seguinte: estamos no auge do inverno e o seu forno deixa subitamente de funcionar. Porquê? Talvez o filtro de ar esteja entupido, o termóstato não esteja a funcionar corretamente ou haja uma fuga de gás. Cada um destes cenários representa um modo de falha - eventos específicos que podem levar a que o seu sistema de aquecimento não consiga manter a sua casa quente.
O que é a análise de efeitos
No mundo da FMEA, identificar os modos de falha é apenas o começo. O objetivo é analisar os potenciais impactos (ou efeitos, o "E" em FMEA) das falhas e dar prioridade às acções para as resolver antes que resultem numa casa gelada ou, pior ainda, numa reparação de emergência dispendiosa.
Tipos de FMEA
No sector do petróleo e do gás, existem diferentes tipos de Análise dos Modos de Falha e Efeitos (FMEA) que são adaptados para responder a necessidades operacionais específicas e aumentar a segurança e a fiabilidade. Eis os principais tipos:
- FMEA de projeto (DFMEA): Centra-se na identificação de potenciais falhas na fase de conceção de activos, tais como plataformas de perfuração ou condutas.
- FMEA de processo (PFMEA): Visa os riscos associados a processos de fabrico ou operacionais, tais como métodos de refinação ou extração.
- FMEA funcional (FFMEA): Analisa as funções dos sistemas críticos de segurança, como as válvulas de alívio de pressão, e as suas falhas e é uma ferramenta vital para desenvolver uma abordagem de manutenção baseada no risco.
O processo FMEA
O processo FMEA segue normalmente uma série de etapas:
- Planeamento e preparação: Reunir uma equipa multifuncional com experiência em várias áreas, tais como engenharia, operações, manutenção e segurança. Definir o âmbito da FMEA, incluindo os sistemas ou processos específicos a serem avaliados e os objectivos da análise.
- Sistematização: Dividir o sistema nos seus componentes para facilitar a análise detalhada. Isto implica a identificação dos subsistemas e das suas interfaces, o que é fundamental em operações complexas de petróleo e gás, em que as interações podem ter um impacto significativo no desempenho.
- Análise de funções: Identificar as funções de cada componente do sistema. No contexto do petróleo e do gás, isto pode incluir funções como a regulação da pressão, o controlo do fluxo ou os mecanismos de encerramento de segurança.
- Análise de falhas: Determinar os potenciais modos de falha para cada função identificada. Esta etapa envolve um brainstorming para identificar as possíveis falhas que podem impedir que os componentes desempenhem as funções pretendidas, tais como avarias nas válvulas ou falhas nos sensores. Para recolher dados sobre os modos de falha. Pode ser benéfico consultar várias fontes, incluindo manuais de manutenção do OEM, diagramas de processos de engenharia, registos e histórico de manutenção, experiência operacional, relatórios de incidentes e imagens do equipamento.
- Análise de causas: Descubra as causas de cada modo de falha através de uma análise aprofundada e da recolha de dados. Este passo revela os factores de raiz que desencadeiam as potenciais falhas.
- Análise de risco: Avaliar cada modo de falha com base no seu risco:
- Gravidade:Classificada de 1 a 10, sendo que uma pontuação elevada indica um risco grave.
- Probabilidade:Classificada de 1 a 10, em que uma pontuação elevada reflecte uma maior probabilidade de fracasso.
- Deteção:Classificado de 1 a 10, com uma pontuação elevada a indicar uma fraca capacidade de deteção.
- Priorização de riscos: Com base na classificação de probabilidade, deteção e gravidade, classifique os modos de falha para determinar quais requerem uma análise mais aprofundada.
Prioridade do risco = Gravidade x Ocorrência x Deteção
- Optimization: Develop action plans to mitigate high-priority risks identified in the previous step. This may involve redesigning components, implementing additional safety measures and inspections, or enhancing maintenance procedures to reduce failure likelihood.
- Documentação: Registar todas as conclusões, decisões tomadas durante a análise e lições aprendidas para referência futura. Esta documentação deve incluir um resumo das falhas de alto risco identificadas e as medidas corretivas tomadas para as resolver.
Importância da FMEA
Pense na FMEA como a sua rede de segurança operacional que não só protege as suas operações, como também oferece vários benefícios importantes:
- Gestão proactiva do risco: A FMEA ajuda a antecipar os problemas antes que eles surjam, reduzindo a probabilidade de erros dispendiosos.
- Priorização de riscos: Permite que as organizações priorizem os riscos com base em sua gravidade e probabilidade, facilitando uma estratégia de manutenção mais focada.
- Tomada de decisões informada: A FMEA fornece uma abordagem estruturada para compreender os impactos das falhas, o que ajuda a tomar decisões informadas sobre a conceção e o funcionamento.
- Conformidade regulamentar: Muitas indústrias exigem que a FMEA cumpra as normas de segurança e qualidade, o que a torna essencial para reduzir os riscos legais associados à não conformidade.
- Redução de custos: A FMEA ajuda a desenvolver uma estratégia de manutenção baseada no risco que dá prioridade ao equipamento crítico, minimizando as falhas dispendiosas e o tempo de inatividade. A resolução precoce de potenciais falhas pode reduzir significativamente os custos associados a retrabalho, recolhas ou reclamações de garantia.
- Documentação e partilha de conhecimentos: A FMEA cria um registo documentado de potenciais modos de falha e estratégias de mitigação, que pode ser consultado em projectos futuros.
- Melhoria contínua: Os conhecimentos adquiridos através da FMEA contribuem para a melhoria contínua dos processos e sistemas, promovendo uma cultura de melhoria contínua.
Cada risco identificado e cada falha potencial tratada através da mitigação ou eliminação contribui para uma base mais forte para as suas operações. Ao implementar a FMEA, a sua atenção passa de uma mera visão de um desempenho ótimo para a implementação ativa das práticas de hoje que o levarão a alcançar o resultado desejado amanhã.
FMEA em sistemas instrumentados de segurança (SIS)
Operational safety relies heavily on Safety Instrumented Systems (SIS), where Safety Instrumented Functions (SIFs) perform key safety actions to reduce risks, such as shutting down a process or isolating equipment during hazardous situations.
FMEA dives deep into the components of Safety Instrumented Functions (SIFs). By conducting FMEA, you can uncover how each part—like sensors, logic solvers, and final elements—might fail and what those failures could mean for safety. For instance, if a safety valve is part of a SIF, FMEA helps identify how failure modes like valve sticking or sensor inaccuracies could impact its ability to perform its safety function.
The FMEA process for this device begins by generating a list of potentially dangerous failures. If they occur, these failures will defeat the safety mission of the device when there is a demand from the process. Specialists then do a study to estimate the contribution of each identified failure mode to the overall number of dangerous failures.
As some dangerous failures are more common than others, this contribution or weight factor (in %) is included. It is important to note that the total weight factors of all dangerous failures of the device under study cannot exceed 100%.
As informações recolhidas no estudo FMEA podem ser utilizadas para comparar os modos de falha perigosa identificados para o dispositivo com o Procedimento de Ensaio de Prova utilizado para os ensaios periódicos do dispositivo. Esta análise procura determinar quais as falhas perigosas identificadas na FMEA do dispositivo que serão detectadas em qualquer uma das etapas dos procedimentos de ensaio de prova.
Por exemplo, se for determinado que 7 dos 8 modos de falha perigosa identificados podem ser detectados através da aplicação adequada do procedimento de ensaio de prova, e estes 7 modos representam coletivamente 90% de todas as falhas perigosas identificadas na FMEA, podemos concluir que o Fator de cobertura do ensaio (TCF) do procedimento de ensaio de prova do dispositivo é de 90%.
O papel da FMEA nos cálculos do PFD
Ao calcular a probabilidade de falha a pedido (PFD) de um dispositivo, λd é um componente crítico, uma vez que reflecte o número de falhas perigosas que podem potencialmente conduzir a incidentes de segurança se não forem detectadas antes de ocorrer uma solicitação do dispositivo por parte do processo. O TCF ajuda a determinar quantas destas falhas λd podem ser detectadas durante os ensaios de prova e é, portanto, um fator importante no cálculo global do PFD do dispositivo.
Outro componente crítico é o Tempo de Missão (TM). Representa o período durante o qual uma Função Instrumentada de Segurança (SIF) deve funcionar efetivamente sem grandes revisões ou substituições. Ao contrário da Vida Útil - definida pelos fabricantes para quando o equipamento precisa de ser substituído - o MT é adaptado às necessidades específicas de cada componente SIF.
Why does this matter? Because with imperfect proof testing (i.e., where the TFC is less than 100%) Mission Time plays a vital role in managing risks associated with dangerous failures.
A well-defined Mission Time helps us gauge how long we can expect our SIF to function safely before risks accumulate.
This is illustrated in the below figure (Mission Time 20 years):
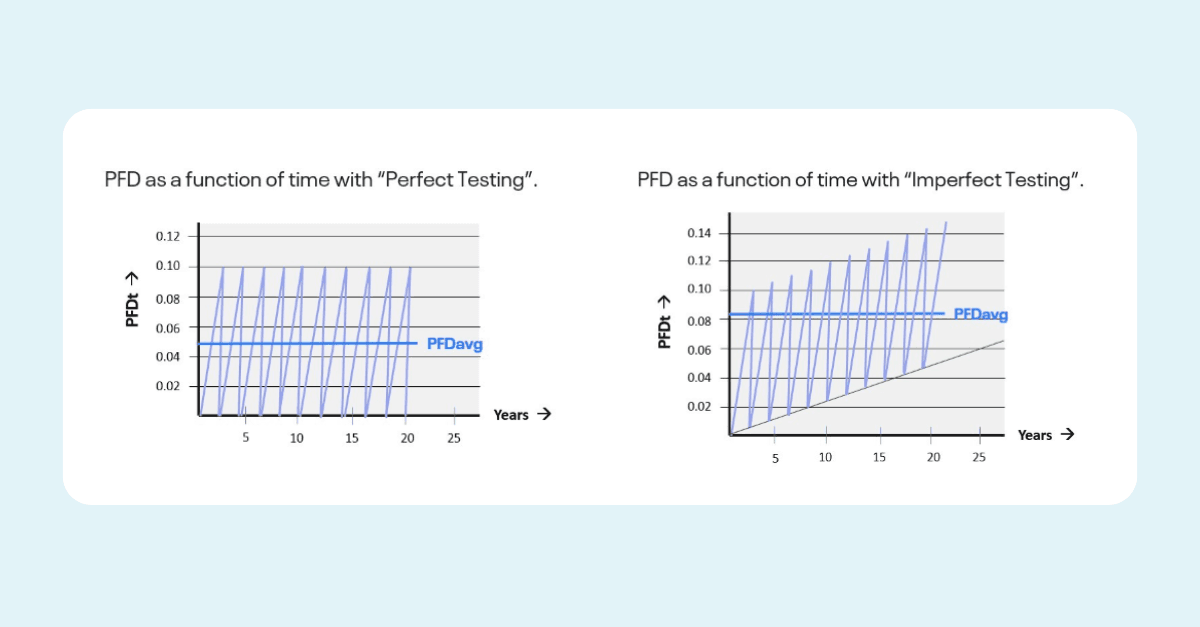
A incorporação da MT nos cálculos do PFD fornece informações sobre a eficácia das medidas de segurança, orientando os intervalos de manutenção e ensaio. A interação entre o TCF e o PFD realça a sua importância para garantir a fiabilidade do SIF.
Um TCF mais elevado (próximo de 100%) indica que são detectadas mais falhas perigosas, reduzindo assim o λd efetivo e contribuindo para um PFD mais baixo. Esta relação realça a importância tanto do TCF como do λd na avaliação da fiabilidade e segurança dos SIF em aplicações críticas para a segurança.
O PFD reflecte a probabilidade de uma função de segurança falhar quando necessário e é influenciado pela capacidade dos ensaios para detetar falhas perigosas. A fórmula para calcular o PFD médio incorporando o TCF é a seguinte

Nesta equação:
- O TCF representa a eficácia dos testes de prova na identificação de falhas perigosas, variando de 0% a 100%.
- (1 - TCF)indica a percentagem de falhas perigosas que não são detectadas por estes ensaios.
- λdé a taxa de falhas perigosas que podem levar a uma falha a pedido.
- Tié o intervalo entre os testes de prova.
- MTrepresenta o tempo de missão do SIF.
Sempre que um teste de prova é realizado, identifica apenas uma fração das falhas perigosas, como indica o TCF. Isto significa que, mesmo com testes eficazes, algumas falhas podem não ser detectadas, agravando o risco ao longo do tempo. Como resultado, é vital compreender como o TCF influencia o PFD; um TCF mais elevado leva a um PFD mais baixo, indicando uma mitigação de risco mais eficaz.
Por outro lado, se o TCF for baixo, a probabilidade de falhas não detectadas aumenta, necessitando de testes de prova mais frequentes para manter a integridade da segurança. Assim, a otimização do TCF através de protocolos de ensaio rigorosos não só melhora a deteção de falhas, como também desempenha um papel fundamental na garantia de que o PFD se mantém dentro dos limites aceitáveis para o cumprimento das normas de segurança.
Reforçar a fiabilidade operacional com a FMEA e o IMS da Cenosco
Como vimos, a FMEA ajuda a aumentar a fiabilidade operacional. Ao identificar potenciais modos de falha e avaliar os seus impactos, permite às empresas gerir proactivamente os riscos e melhorar a eficiência dos seus activos.
A FMEA é uma metodologia versátil e eficaz que é integrada noutros processos, tais como os encontrados nos Sistemas Instrumentados de Segurança. Através de uma avaliação exaustiva dos componentes críticos de segurança, a FMEA permite estratégias atempadas de redução de riscos e informa as decisões relativas aos intervalos de teste, garantindo que os sistemas de segurança permanecem fiáveis e eficazes.
Esta abordagem não só reforça os protocolos de segurança, como também optimiza a atribuição de recursos, conduzindo, em última análise, a operações mais resistentes na indústria do petróleo e do gás. Se procura uma forma de aumentar a fiabilidade dos processos nas suas instalações, o nosso Sistema de Gestão da Integridade (IMS) pode ajudar. Preencha o formulário abaixo e solicite uma demonstração!
Request a Demo
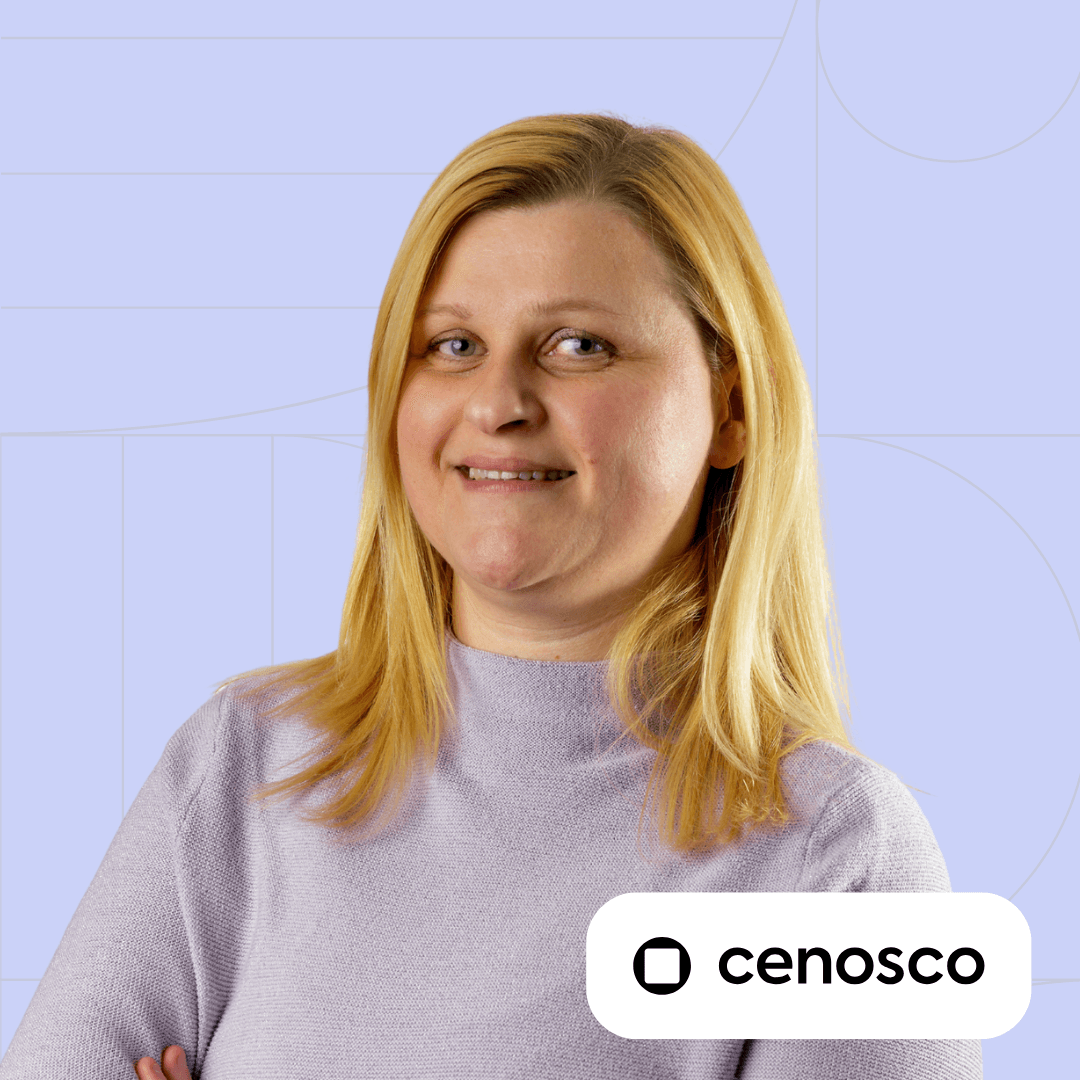
Denis Tkalec Technical writer
Denis Tkalec is a technical writer at Cenosco, specializing in asset integrity management software since 2022. With a background in education and six years in marketing, she turns complex topics into clear, user-friendly content. Inspired by Camus’s belief that “a writer keeps civilization from destroying itself,” she brings precision and care to every manual.