Ensuring the integrity of heat exchanger tubes is critical and challenging when it comes to maintaining industrial efficiency. Heat exchangers are vital components in various industries, playing a key role in transferring heat between fluids.
However, inspection becomes a BIG and DIRTY job with bundles containing anywhere from 250 to an overwhelming 5000 tubes. Traditionally, due to concerns over tube conditions and the potential for corrosion in heat exchangers, sites often inspect every single tube. This process is not only laborious but also incredibly time-consuming.
Imagine spending 12 hours just cleaning and inspecting a mere 300 tubes! Moreover, certain corrosion inspection techniques like the Internal Rotary Inspection System (IRIS) necessitate substrate materials to be cleaned meticulously for effective results. Often, this means multiple rounds of washing and inspecting to get accurate data.
Enter Extreme Value Analysis (EVA) – a statistical method revolutionizing how we approach this daunting task. By employing EVA for efficient heat exchanger tube wall thickness calculations, we can confidently reduce the number of tubes inspected without compromising safety or performance.
This not only slashes inspection times significantly but also translates into substantial cost savings. Additionally, EVA helps extend the heat exchanger’s useful life by accurately assessing tube conditions. In this blog, we’ll explore how EVA transforms the heat exchanger inspection process, making it smarter, faster, and more efficient.
Aplicación del análisis de valores extremos (EVA) al cálculo del espesor de la pared del intercambiador de calor
El análisis de valores extremos (EVA) es un potente método estadístico para predecir los valores más extremos de un conjunto de datos. En el contexto de los intercambiadores de calor, el EVA resulta especialmente útil para calcular la pérdida de pared máxima a partir de una muestra de tubos más pequeña y representativa. El proceso comienza con el muestreo, en el que se toman lecturas del espesor de pared de una selección representativa de tubos dentro del intercambiador de calor.
Una vez recogidos los datos, se ajustan a una distribución estadística, normalmente la distribución de Gumbel. Este proceso de ajuste ayuda a comprender el comportamiento de los valores extremos dentro del conjunto de datos. A partir de esta distribución, la pérdida de pared máxima se extrapola a todo el intercambiador de calor, lo que proporciona una visión completa de la degradación potencial.
A partir de aquí, hay que calcular el grosor de la pared de los tubos del intercambiador de calor a lo largo del tiempo. Al comprender cómo cambia el grosor de la pared, es posible predecir la vida útil restante del intercambiador de calor. Esta información es crucial para planificar las inspecciones y garantizar el rendimiento óptimo del equipo.
Pasos del cálculo del espesor de la pared de los tubos del intercambiador de calor
Ahora que ya sabemos cómo puede aplicarse EVA a los cálculos del espesor de las paredes de los tubos de un intercambiador de calor, vamos a estudiar cómo puede aplicarse este proceso en la práctica. Utilizaremos el flujo de trabajo de nuestro software IMS PEI como ejemplo para ilustrarlo. He aquí un desglose paso a paso del proceso:
- Planificar la inspección: Comience por especificar los tubos que deben medirse. Prepare y exporte la documentación necesaria para la inspección.
- Recogida de datos: Realice inspecciones en la muestra de tubos seleccionada. Esto puede implicar técnicas como IRIS, que requieren que el material del sustrato se limpie a un alto nivel para obtener resultados eficaces.
- Defina Estratificación: La estratificación ayuda a gestionar los datos no uniformes mediante la creación de grupos más pequeños y coherentes denominados estratos. Ajustar la estratificación según sea necesario garantiza que los datos de cada estrato sean homogéneos, lo cual es crucial para un análisis preciso.
- Ejecutar el cálculo EVA: El cálculo utiliza la distribución de Gumbel para modelizar los valores extremos en los datos recogidos. Esto permite extrapolar la pérdida de pared máxima en todo el intercambiador de calor. Los modelos tradicionales de velocidad de corrosión se aplican para estimar el espesor de la pared del tubo a lo largo del tiempo. (En este caso, el cálculo EVA se realiza con el software IMS PEI).
- Evalúe los resultados: Realice pruebas de bondad de ajuste para evaluar la calidad de la distribución ajustada. Si los resultados no son satisfactorios, vuelva a la etapa de estratificación para garantizar la homogeneidad de las muestras. Además, evalúe la pérdida de pared prevista y asegúrese de que se comprende bien el comportamiento de la corrosión en el intercambiador de calor.
- Calcular y aprobar la vida útil restante y la próxima fecha de inspección: Basándose en los resultados del EVA, calcule la vida útil restante del intercambiador de calor y determine la próxima fecha de inspección. Esto nos devuelve al paso inicial de planificar la próxima inspección.
La siguiente imagen visualiza este flujo de trabajo, proporcionando una visión clara de todo el proceso.
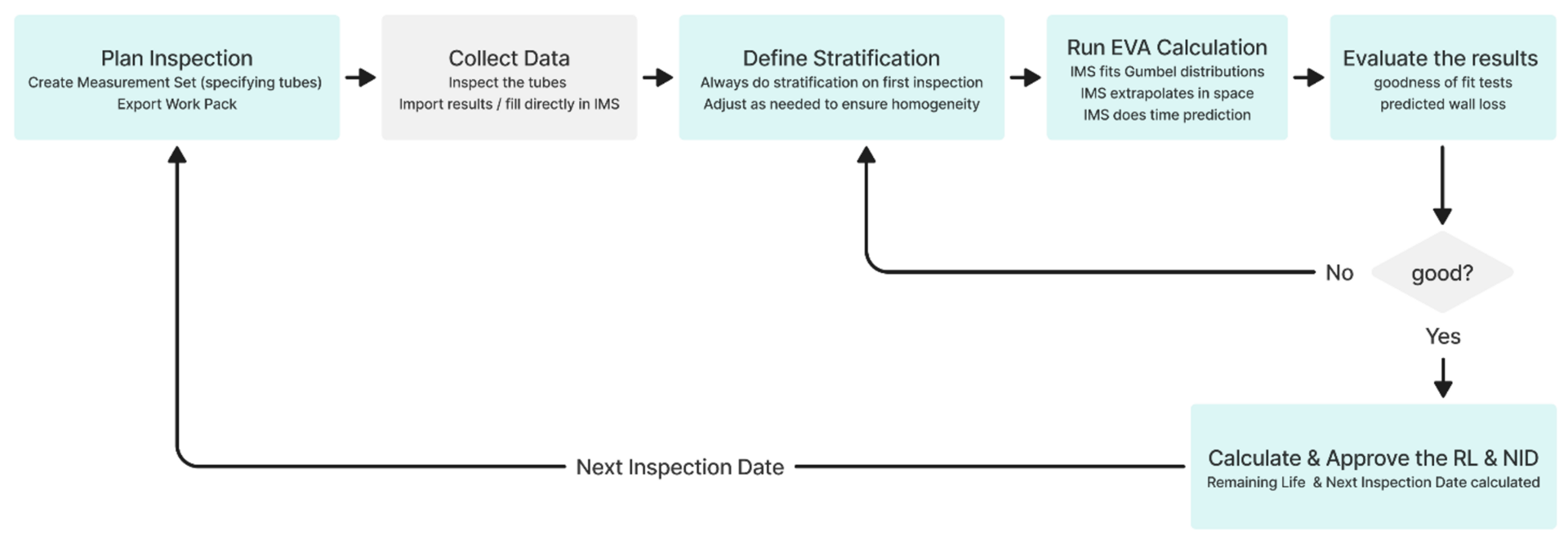
Cálculos precisos del espesor de pared de los tubos: Buenas prácticas para las inspecciones de intercambiadores de calor
A la hora de recopilar datos sobre el espesor de las paredes de los tubos, es esencial asegurarse de que la muestra sea representativa y de alta calidad. Las inspecciones de alta calidad, como las realizadas con el Sistema de Inspección Rotativa Interna (IRIS), son muy recomendables, ya que proporcionan datos precisos y fiables. Sin embargo, incluso con inspecciones de menor calidad, los resultados tienden a ser conservadores y pueden seguir utilizándose.
La muestra debe representar la totalidad del intercambiador de calor y ser homogénea para reflejar con precisión el estado del equipo. La imagen siguiente muestra una muestra representativa típica (izquierda) comparada con una muestra no representativa (derecha), que carece de la suficiente dispersión.
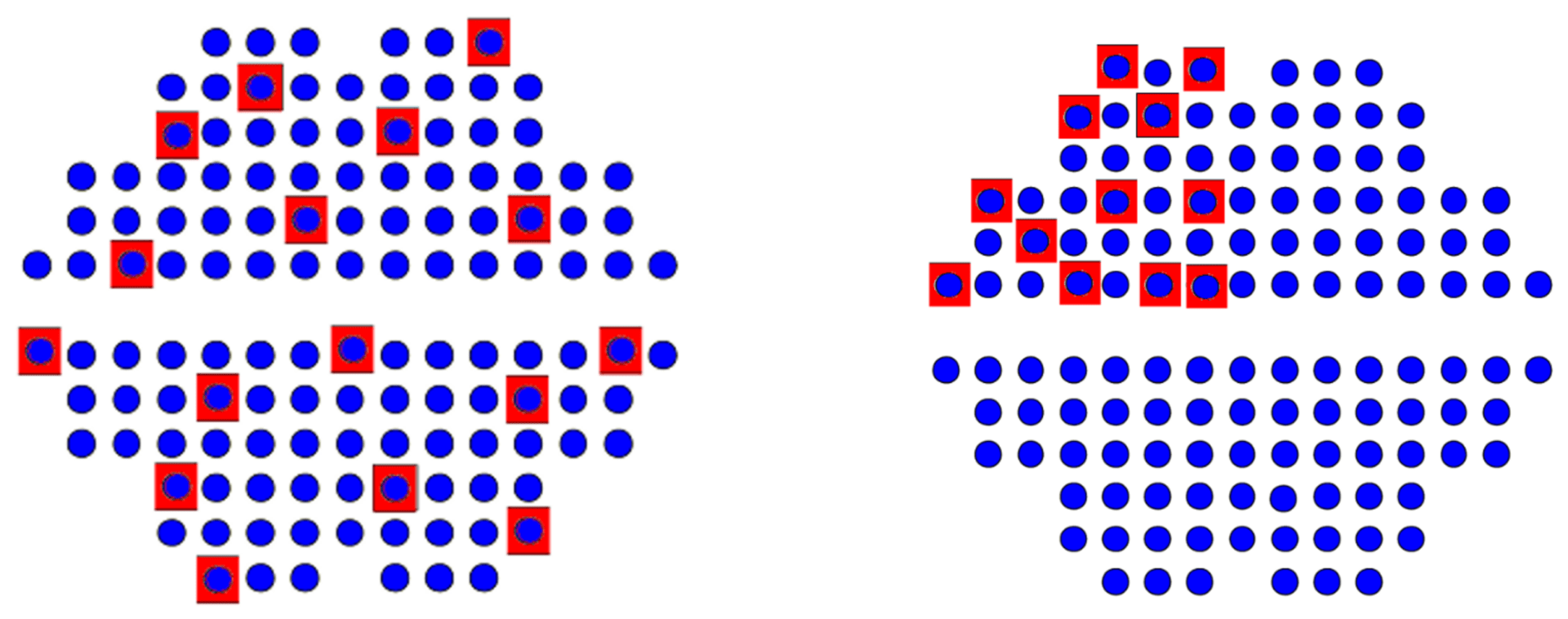
Homogeneous data shows no significant variations or localized areas with higher or lower corrosion rates. When the data is non-homogeneous, stratification is needed. This involves dividing the data into smaller, more uniform groups or strata.
For example, the inlet and outlet sides of the heat exchanger might be separate strata since temperature differences affect corrosion rates. It’s recommended to sample 20-25% of the tubes per stratum, as sampling more could result in overly optimistic estimates. For the first inspection, when establishing a baseline, inspecting up to 100% may be necessary. By following these guidelines, you’ll ensure that your tube wall thickness readings are accurate and reliable.
Evaluación del ajuste del modelo estadístico: Combinación de métodos estadísticos y gráficos
Después de ajustar la distribución, por ejemplo, Gumbel, a los datos, es esencial evaluar la bondad del ajuste utilizando métodos estadísticos y gráficos. Los métodos estadísticos incluyen pruebas de hipótesis como la prueba de Kolmogorov-Smirnov, que evalúa la calidad general del ajuste, y la prueba de Anderson-Darling, que hace hincapié en las colas de la distribución. Estas pruebas proporcionan una medida cuantitativa de lo bien que la distribución de Gumbel representa los datos.
In addition to statistical methods, graphical methods should be used to better understand the fit. These include probability plots, exceedance probability plots, and quantile plots.
For example, the quantile plot shown below compares theoretical quantiles to sample quantiles. A quantile divides a dataset into equal-sized intervals (e.g., the median is the 50th quantile, meaning half the data points are below it). If the fit is good, the points in the quantile plot will align along a straight line. The plot includes a line of perfect fit (blue) and confidence bands (green) to highlight deviations.
If most points (red) lie close to the line and within the bands, it indicates the theoretical distribution fits well.
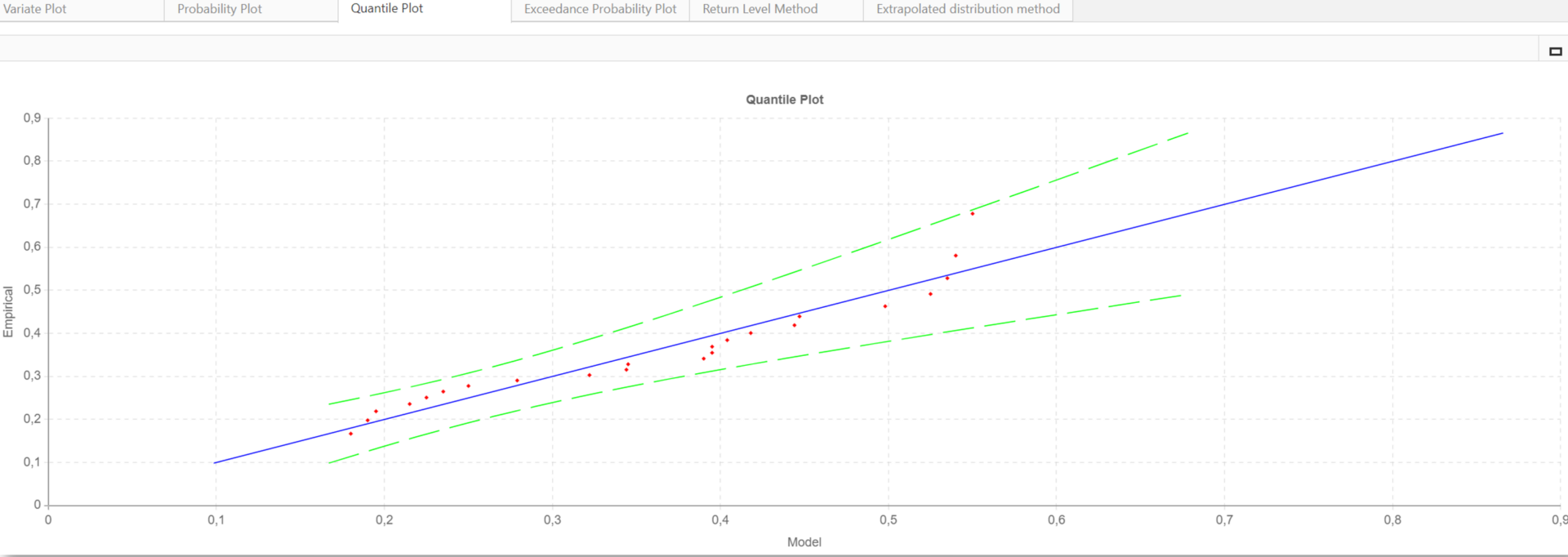
Estas herramientas visuales ayudan a identificar discrepancias o patrones que pueden no ser evidentes sólo mediante pruebas estadísticas. Es fundamental no confiar únicamente en los métodos estadísticos. Revisar los métodos gráficos antes de sacar conclusiones garantiza una evaluación de ajuste más sólida. Además, siempre se debe evaluar la pérdida de pared prevista y asegurarse de que se comprende bien el comportamiento de la corrosión.
Cálculo del espesor de la pared de los tubos de todo el intercambiador de calor
El objetivo es deducir estadísticamente la pérdida de pared máxima de todo el intercambiador de calor. Para ello pueden utilizarse dos métodos: Nivel de retorno y Distribución extrapolada. Estos métodos ayudan a determinar la pérdida de pared máxima más probable (valor extremo) y sus límites de confianza (CB). Veamos ahora una representación visual que nos ayudará a comprender la distribución de los valores de pérdida de pared y los intervalos de confianza asociados.
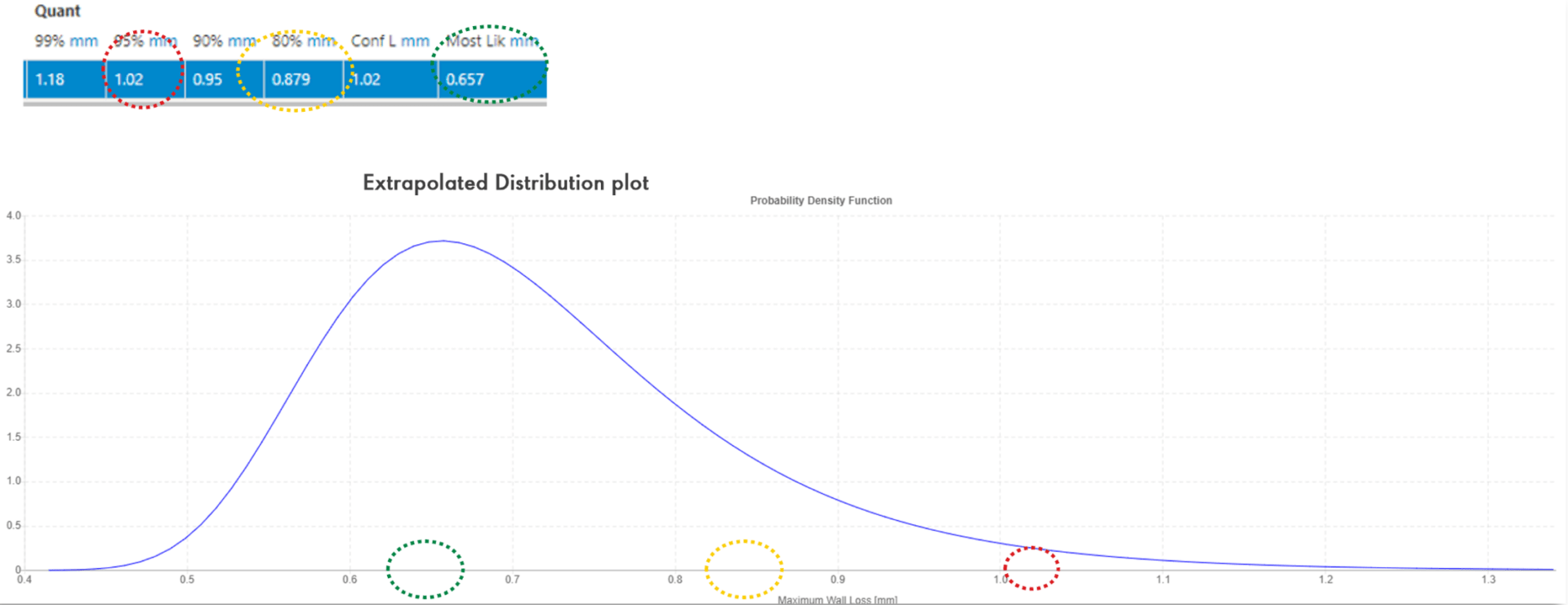
The image above shows an Extrapolated Distribution plot featuring a probability density function curve. The curve peaks at the most likely maximum wall loss value (highlighted by the green circle). It tapers off at both ends, illustrating the distribution of potential maximum wall loss values.
Quantile values, such as the 95th quantile at 1.02mm (marked by the red circle), indicate confidence bounds. This means 95% of the expected maximum wall losses are below 1.02mm, while 80% of the expected maximum wall losses are below 0.879mm (indicated by the yellow circle)
Estudio de caso: Análisis de valores extremos de un precalentador de crudo con tres intercambiadores de calor
Nuestro estudio de caso se centra en la inspección de un precalentador de crudo con tres trenes en funcionamiento. Estos intercambiadores de calor llevan funcionando 25 años, alcanzando su vida útil de diseño, y el cliente quería prolongar su vida útil al menos diez años más. Anteriormente, se realizaban inspecciones visuales con boroscopio a intervalos fijos para evaluar el estado de los tubos, pero éstas sólo proporcionaban datos cualitativos sin medir el grosor de las paredes. El cliente necesitaba determinar si era necesario sustituirlos.
Un año antes del final de su vida útil, durante una parada programada, se inspeccionaron los intercambiadores de calor utilizando muestras representativas. Esto permitió estimar la pérdida máxima de pared y ayudó a decidir si era seguro seguir funcionando otros diez años.
All three heat exchangers had similar results, and we’ll concentrate on one of them. The heat exchanger bundle consists of 120 carbon steel tubes, 23 of which were inspected. Knowledge from previous borescope inspections helped identify the best tubes to examine. The renewal thickness was set at 1.1 mm, with a nominal wall thickness of 2.4 mm.
The inspection took place on October 1, 2023.
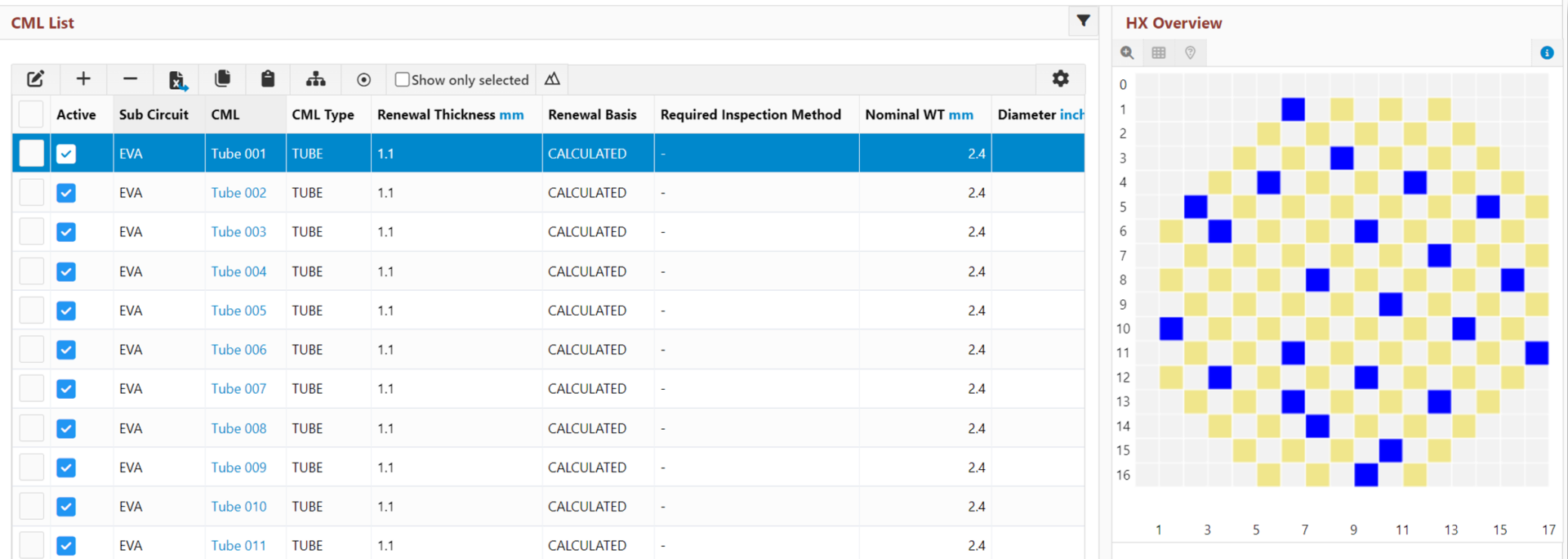
Una única estratificación homogénea fue suficiente para este intercambiador de calor. No hubo variaciones significativas ni zonas localizadas con índices de corrosión más altos o más bajos; los valores se situaron dentro de un estrecho margen, como se muestra en el histograma siguiente. Esto confirma que los datos recogidos representaban la totalidad del intercambiador de calor, proporcionando información fiable sobre su estado.
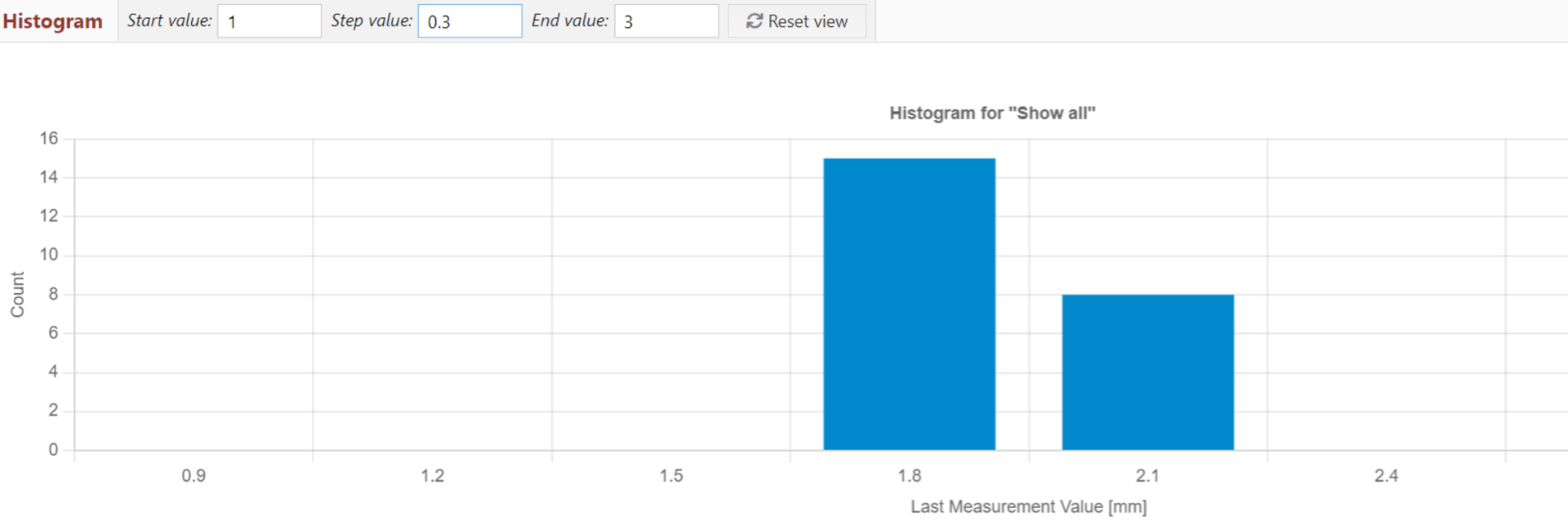
Evaluación del ajuste del modelo estadístico obtenido
Las pruebas estadísticas y los métodos gráficos indicaron un buen ajuste de los datos. Tanto la prueba de Kolmogorov-Smirnov (p-KS) como la de Anderson-Darling (p-AD) mostraron valores p superiores a 0,5, lo que confirma la calidad del ajuste (véanse los resultados a continuación).
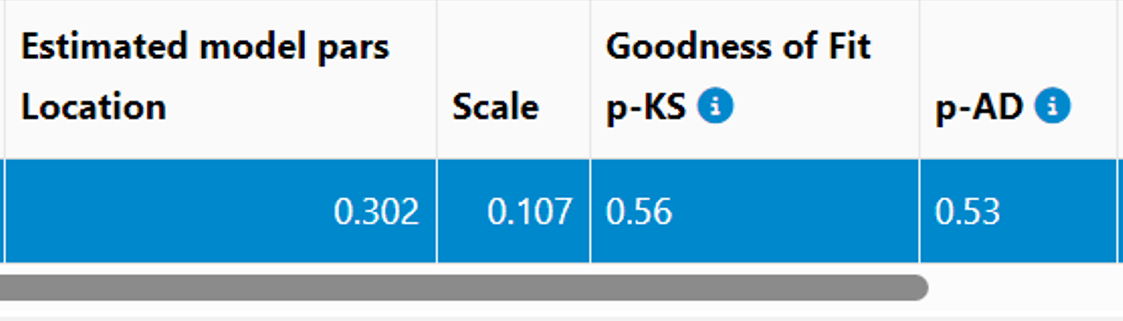
Los gráficos también mostraban que la distribución teórica se ajustaba bien a los datos de la muestra, lo que daba confianza en el análisis y confirmaba un buen ajuste. A continuación se muestran los gráficos de probabilidad.
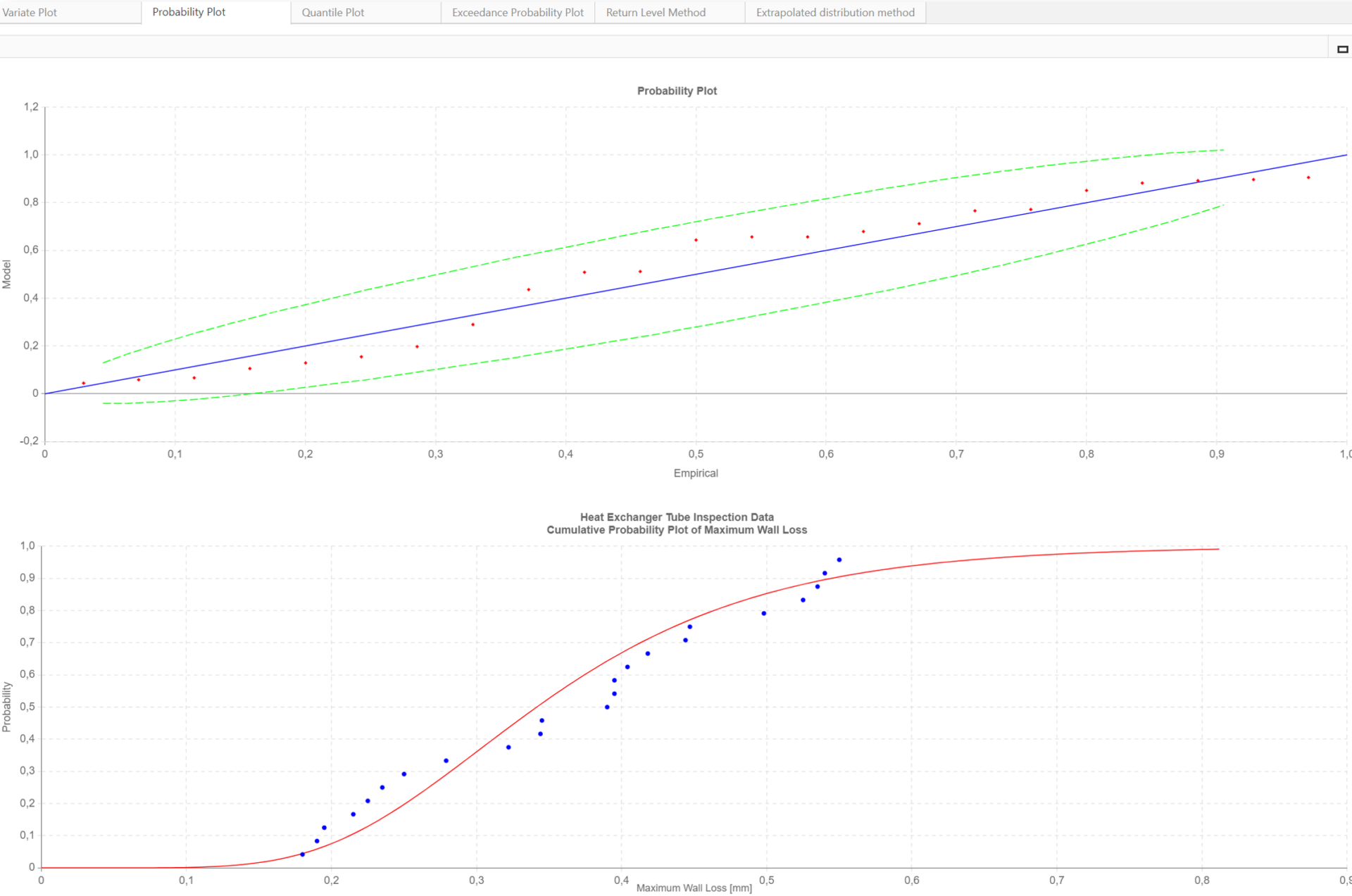
Cálculo del espesor de la pared de los tubos de todo el intercambiador de calor
Next, the Return Level Method was used to extrapolate the data in space to calculate the maximum wall loss for the entire heat exchanger. The most likely maximum wall loss was 0.816 mm (indicated in red). At the 99% confidence bound, the maximum wall loss was 1.059 mm (indicated in yellow), and at the 80% confidence bound, it was 0.937 mm (indicated in green). The graphs below illustrate these findings.
The upper graph shows the return level curve with the 99% confidence bound, while the lower graph shows the curve with the 80% confidence bound. As you can see, higher confidence bounds lead to more conservative estimates, showing greater wall loss, indicating a thinner remaining tube wall thickness and a shorter useful life for heat exchangers.

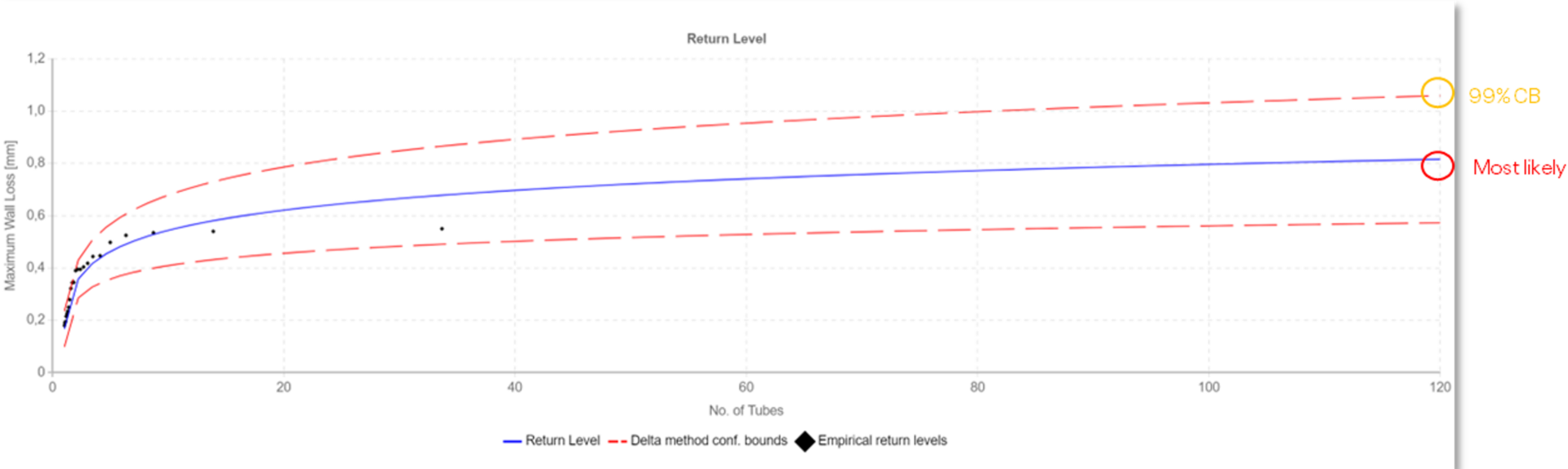
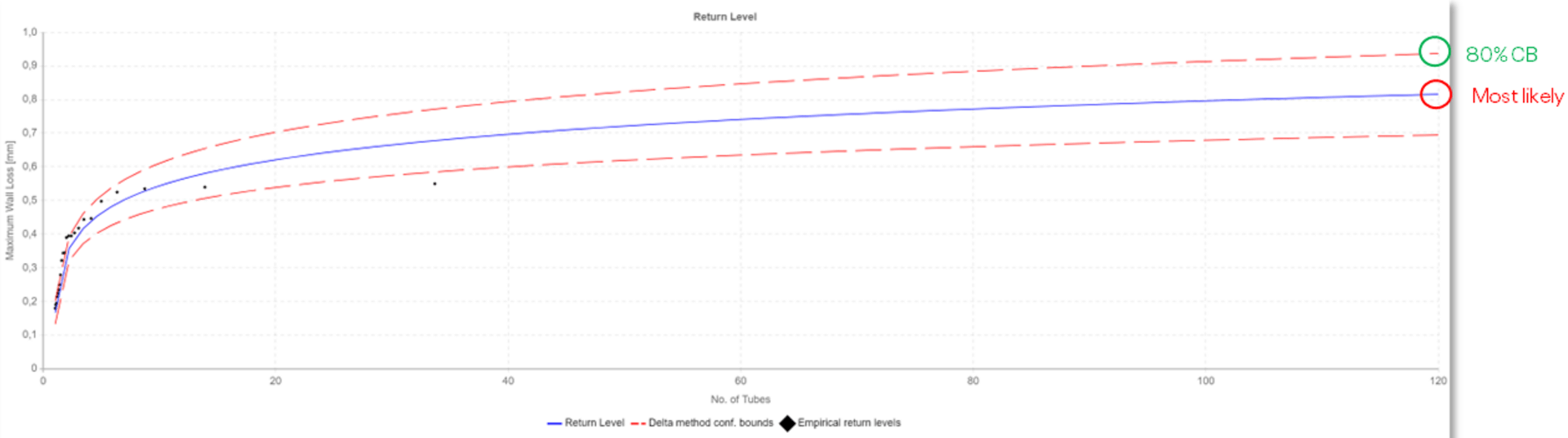
Cálculo de la vida útil del intercambiador de calor y próxima fecha de inspección
Se calcularon el grosor mínimo restante de la pared del tubo y los índices de corrosión del intercambiador de calor para distintos límites de confianza. Estos cálculos permitieron determinar la vida útil del intercambiador de calor, el intervalo máximo de inspección y la próxima fecha de inspección.
Las imágenes siguientes presentan un desglose detallado de los resultados. En primer lugar, las dos tablas muestran el espesor de pared mínimo restante del intercambiador de calor y los índices de corrosión con distintos niveles de confianza (95%, 90% y 80%).
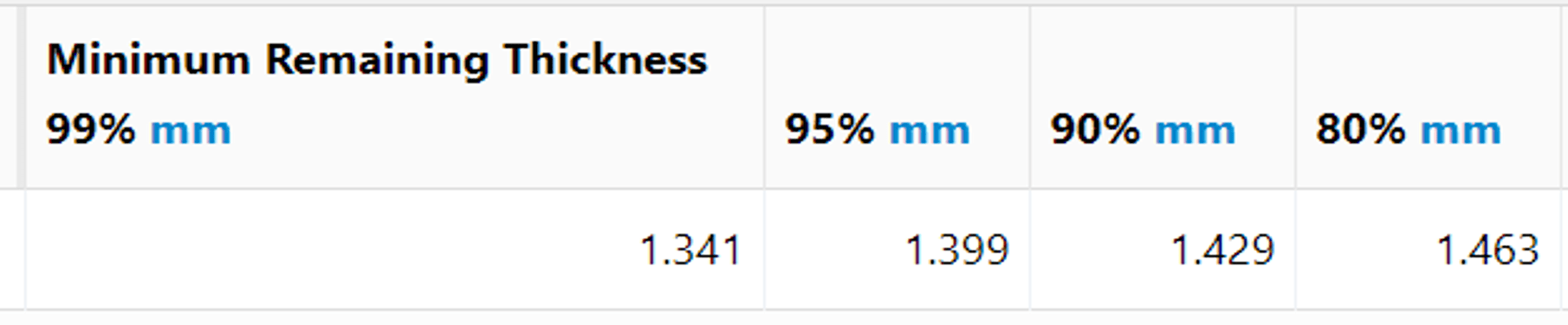

The calculation summary then shows the heat exchanger’s useful life (Remnant Life), corrosion rate (Rate), and next inspection date (Next Insp Date) at the 80% confidence level. It’s important to note that the corrosion engineer determines the choice of confidence bound. Typically, using a representative sample and conducting multiple inspections over time increases confidence in the results, allowing for the use of lower confidence bounds.
In this case study, the information gathered from previous borescope inspections gave the engineers enough confidence in the new results to select the 80% confidence bound.
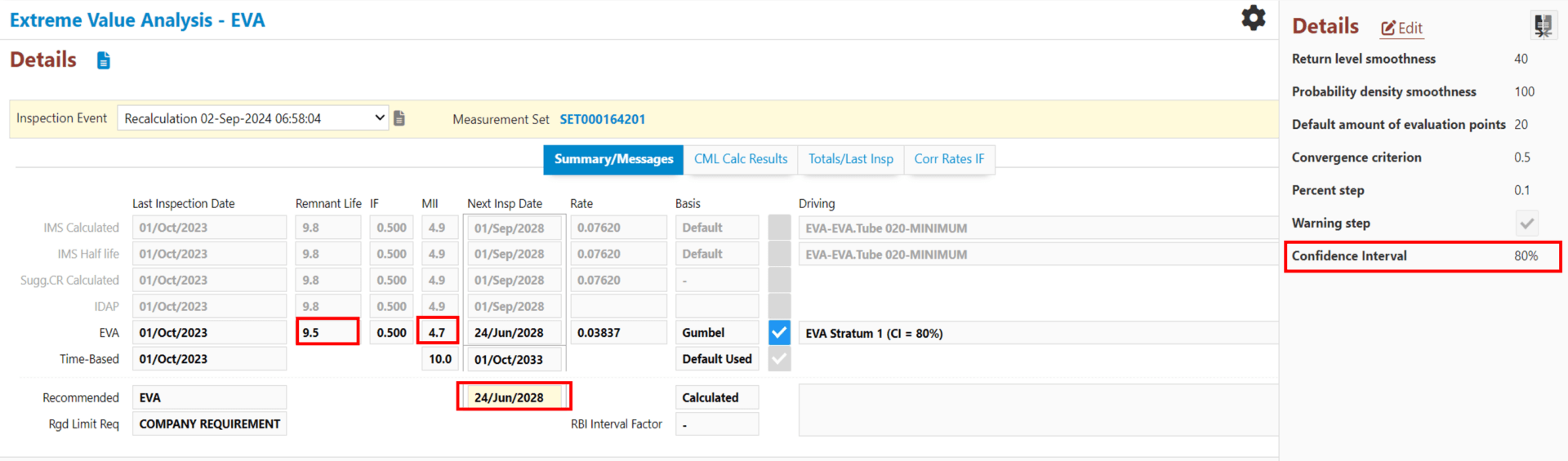
Con una vida útil del intercambiador estimada en 9,5 años (cercana a la extensión deseada de diez años), la aplicación del concepto de vida media estándar en la industria estableció el intervalo máximo de inspección (MII) en 4,7 años, con la próxima inspección programada para el 24 de junio de 2028. A continuación se muestra el cálculo (con un límite de confianza del 80%):
Vida remanente = (Espesor mínimo remanente - Espesor de renovación) / Tasa de corrosión=(1,1463mm -1,1mm) / 0,038mm/año = 9,5años
Próxima fecha de inspección = última fecha de inspección + vida residual ∗ SI = 1 de octubre de 2023+9,5*0,5 = 24 de junio de 2028
Estos resultados dieron a los ingenieros confianza en el estado del intercambiador de calor. En lugar de optar por una sustitución completa, se sintieron tranquilos sobre las medidas necesarias para mantenerlo operativo otros diez años. Si la vida útil estimada hubiera sido más corta, podrían haber considerado otras opciones, como el uso de inhibidores de corrosión para ralentizar la corrosión en el intercambiador de calor. Sin embargo, ahora sabían que no era necesario tomar ninguna medida antes de la próxima inspección.
Conclusiones del estudio de caso: Reducción de la duración de la inspección y del tiempo de respuesta
The benefits of using this heat exchanger tube wall thickness calculation approach were significant. By conducting inspections on a representative sample, engineers reduced overall inspection time and preparation activities by at least 40%, streamlining the entire process.
Due to the heat exchangers being part of the critical path, the turnaround time was also shortened by 12%, allowing production to restart sooner than expected. Additionally, a deeper understanding of risks and threats led to an estimated 85% cost savings by avoiding expensive maintenance actions like repairs and replacements. These advantages highlight how EVA makes the heat exchanger inspection process smarter, faster, and more efficient.
Conclusiones: EVA garantiza inspecciones eficaces y seguras
In summary, EVA provides significant time and cost savings for inspections and tube cleaning while ensuring they are performed at the right intervals. By using a representative sample and conducting multiple inspections over time, the conservatism in models can be minimized.
This makes EVA a reliable framework for efficient heat exchanger inspections. For added assurance, IMS PEI allows for independent assessment of tube degradation risks, which can be combined with EVA to determine the optimal time for the next inspection.
Rellene el siguiente formulario para ver EVA e IMS PEI en acción.
¿Quiere saber más sobre IMS?
Solicite una demostración a continuación para conocer de primera mano sus posibilidades.
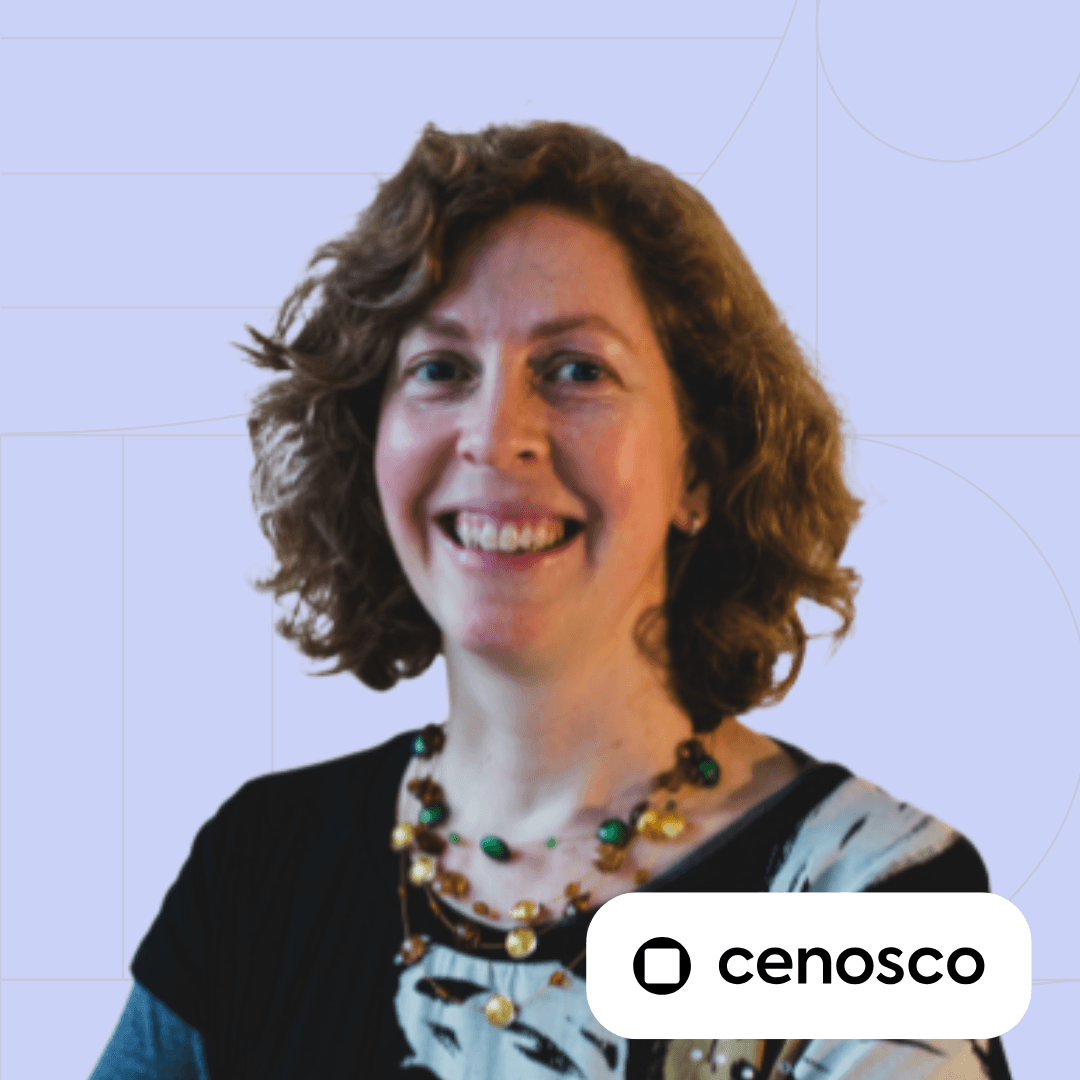
Elsa Tolsma-de Klerk Technical Writer
Elsa is an engineer with a passion for sharing knowledge. She holds a Master’s in Electronic Engineering and spent over a decade at Sasol as an Advanced Process Control Engineer, where she gained hands-on experience in optimization, control systems, and writing technical documentation. Since 2019, she’s been a Technical Writer at Cenosco, now leading the IMS knowledge base and training Academy team.