Ensuring the integrity of heat exchanger tubes is critical and challenging when it comes to maintaining industrial efficiency. Heat exchangers are vital components in various industries, playing a key role in transferring heat between fluids.
However, inspection becomes a BIG and DIRTY job with bundles containing anywhere from 250 to an overwhelming 5000 tubes. Traditionally, due to concerns over tube conditions and the potential for corrosion in heat exchangers, sites often inspect every single tube. This process is not only laborious but also incredibly time-consuming.
Imagine spending 12 hours just cleaning and inspecting a mere 300 tubes! Moreover, certain corrosion inspection techniques like the Internal Rotary Inspection System (IRIS) necessitate substrate materials to be cleaned meticulously for effective results. Often, this means multiple rounds of washing and inspecting to get accurate data.
Enter Extreme Value Analysis (EVA) – a statistical method revolutionizing how we approach this daunting task. By employing EVA for efficient heat exchanger tube wall thickness calculations, we can confidently reduce the number of tubes inspected without compromising safety or performance.
This not only slashes inspection times significantly but also translates into substantial cost savings. Additionally, EVA helps extend the heat exchanger’s useful life by accurately assessing tube conditions. In this blog, we’ll explore how EVA transforms the heat exchanger inspection process, making it smarter, faster, and more efficient.
Применение анализа экстремальных значений (EVA) для расчетов толщины стенок теплообменников
Анализ экстремальных значений (EVA) - это мощный статистический метод для прогнозирования наиболее экстремальных значений в наборе данных. В контексте теплообменников EVA особенно полезен для расчета максимальной потери толщины стенки на основе меньшей, репрезентативной выборки трубок. Процесс начинается с отбора проб, когда показания толщины стенок снимаются с репрезентативной выборки трубок в теплообменнике.
После того как данные собраны, они подгоняются под статистическое распределение, обычно это распределение Гумбеля. Этот процесс подгонки помогает понять поведение экстремальных значений в наборе данных. Используя это распределение, максимальные потери на стенках экстраполируются на весь теплообменник, что дает полное представление о потенциальной деградации.
Отсюда следует, что толщина стенок трубок теплообменника должна рассчитываться с течением времени. Понимание того, как изменяется толщина стенок, позволяет спрогнозировать оставшийся срок службы теплообменника. Эта информация крайне важна для планирования проверок и обеспечения оптимальной работы оборудования.
Этапы расчета толщины стенок трубок теплообменника
Теперь, когда мы поняли, как EVA может применяться для расчета толщины стенок труб теплообменников, давайте рассмотрим, как этот процесс может быть реализован на практике. В качестве примера мы используем рабочий процесс из нашего программного обеспечения IMS PEI. Вот пошаговое описание этого процесса:
- Составьте план проверки: Начните с определения труб, которые необходимо измерить. Подготовьте и экспортируйте необходимую документацию для проведения инспекции.
- Соберите данные: Проведите инспекцию отобранной выборки трубок. Для этого могут использоваться такие методы, как IRIS, которые требуют высокой степени очистки материала подложки для получения эффективных результатов.
- Дайте определение стратификации: Стратификация помогает управлять неоднородными данными путем создания более мелких, последовательных групп, называемых стратами. Корректировка стратификации по мере необходимости обеспечивает однородность данных в каждой страте, что очень важно для точного анализа.
- Запустите расчет EVA: В расчете используется распределение Гумбеля для моделирования экстремальных значений в собранных данных. Это позволяет экстраполировать максимальную потерю стенки на весь теплообменник. Для оценки толщины стенок труб с течением времени применяются традиционные модели скорости коррозии. (В данном случае расчет EVA выполняется с помощью программного обеспечения IMS PEI).
- Оцените результаты: Проведите тесты на правильность подгонки, чтобы оценить качество подогнанного распределения. Если результаты неудовлетворительны, вернитесь к этапу стратификации, чтобы обеспечить однородность образцов. Кроме того, оцените прогнозируемые потери на стенках и убедитесь, что поведение коррозии в теплообменнике хорошо изучено.
- Рассчитайте и утвердите оставшийся срок службы и дату следующей проверки: На основе результатов EVA рассчитайте оставшийся срок службы теплообменника и определите дату следующей проверки. Это возвращает нас к начальному этапу планирования следующей проверки.
Следующее изображение визуализирует этот рабочий процесс, давая наглядное представление обо всем процессе.
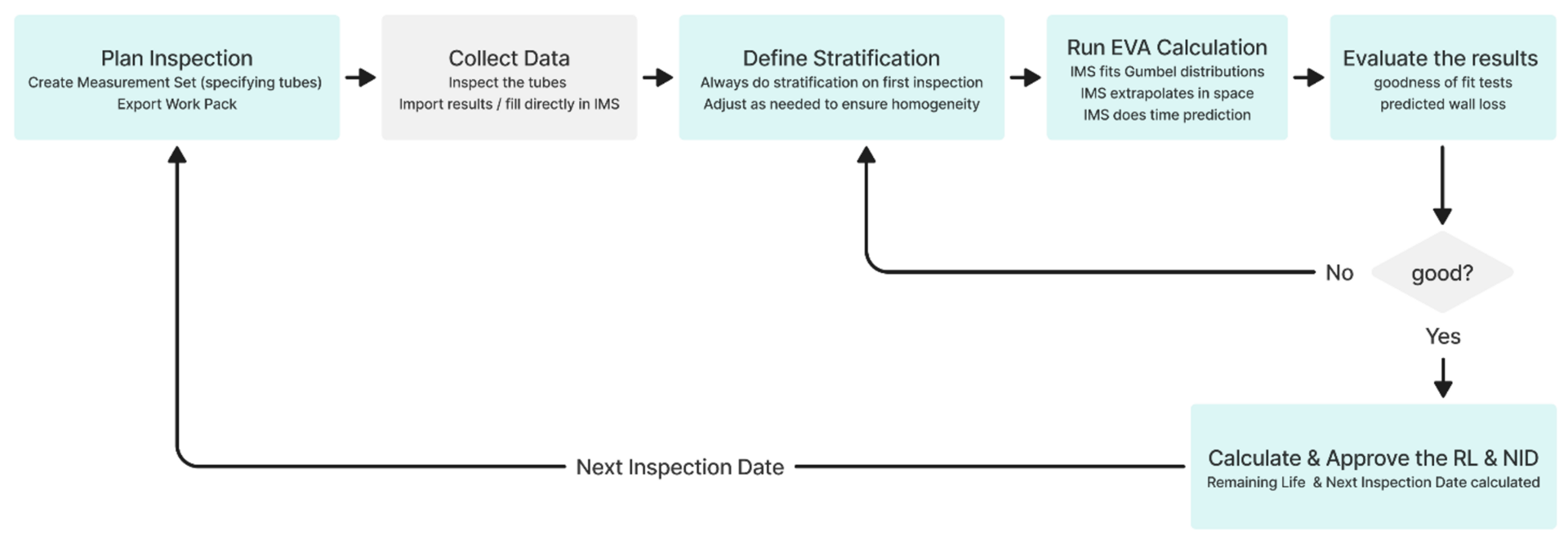
Обеспечение точных расчетов толщины стенок трубок: Передовые методы проверки теплообменников
При сборе данных о толщине стенок труб необходимо обеспечить высокое качество и репрезентативность образца. Высококачественные проверки, например, выполняемые с помощью системы внутреннего ротационного контроля (IRIS), настоятельно рекомендуются, поскольку они позволяют получить точные и надежные данные. Однако даже при менее качественном контроле результаты, как правило, консервативны и могут быть использованы.
Образец должен представлять весь теплообменник и быть однородным, чтобы точно отражать состояние оборудования. На рисунке ниже показан типичный репрезентативный образец (слева) в сравнении с нерепрезентативным образцом (справа), который не имеет достаточного распространения.
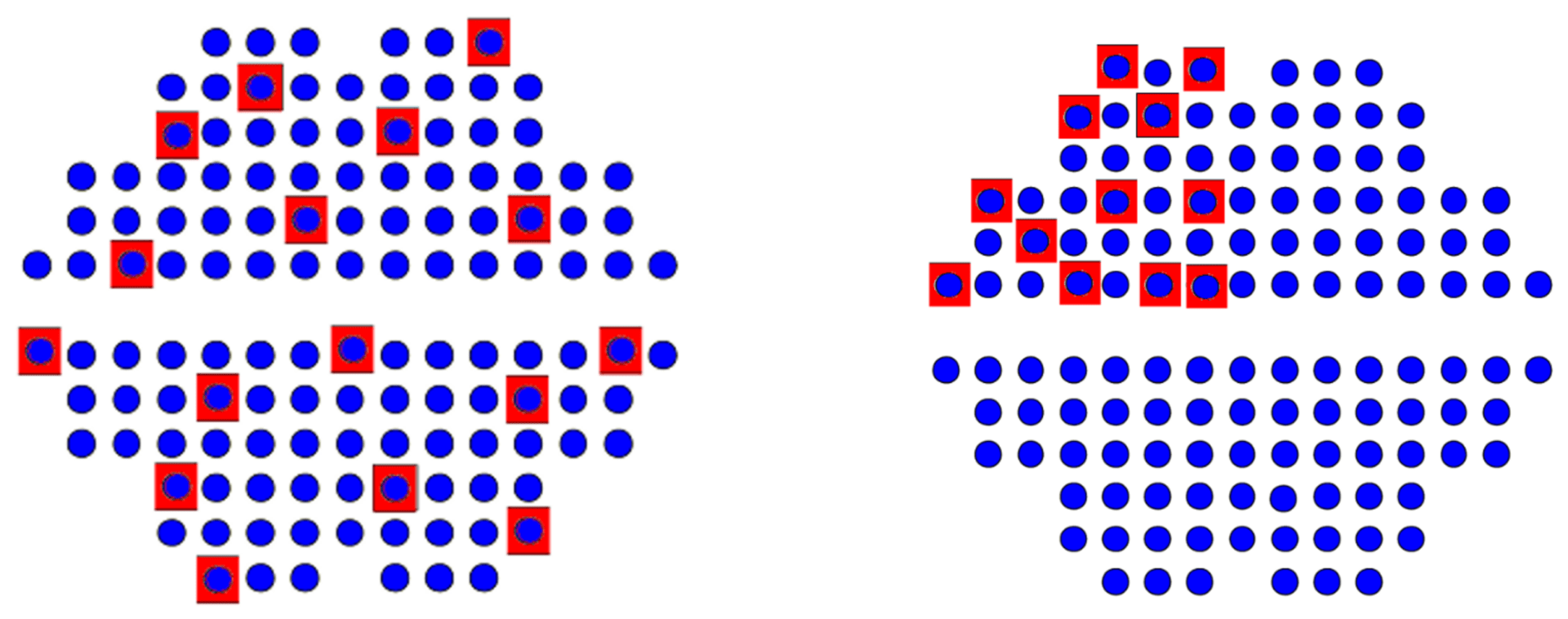
Homogeneous data shows no significant variations or localized areas with higher or lower corrosion rates. When the data is non-homogeneous, stratification is needed. This involves dividing the data into smaller, more uniform groups or strata.
For example, the inlet and outlet sides of the heat exchanger might be separate strata since temperature differences affect corrosion rates. It’s recommended to sample 20-25% of the tubes per stratum, as sampling more could result in overly optimistic estimates. For the first inspection, when establishing a baseline, inspecting up to 100% may be necessary. By following these guidelines, you’ll ensure that your tube wall thickness readings are accurate and reliable.
Оценка пригодности статистической модели: Сочетание статистических и графических методов
После подгонки распределения, например, Гумбеля, к данным необходимо оценить правильность подгонки, используя как статистические, так и графические методы. Статистические методы включают проверку гипотез, например тест Колмогорова-Смирнова, который оценивает общее качество подгонки, и тест Андерсона-Дарлинга, который подчеркивает хвосты распределения. Эти тесты дают количественную оценку того, насколько хорошо распределение Гумбеля отражает данные.
In addition to statistical methods, graphical methods should be used to better understand the fit. These include probability plots, exceedance probability plots, and quantile plots.
For example, the quantile plot shown below compares theoretical quantiles to sample quantiles. A quantile divides a dataset into equal-sized intervals (e.g., the median is the 50th quantile, meaning half the data points are below it). If the fit is good, the points in the quantile plot will align along a straight line. The plot includes a line of perfect fit (blue) and confidence bands (green) to highlight deviations.
If most points (red) lie close to the line and within the bands, it indicates the theoretical distribution fits well.
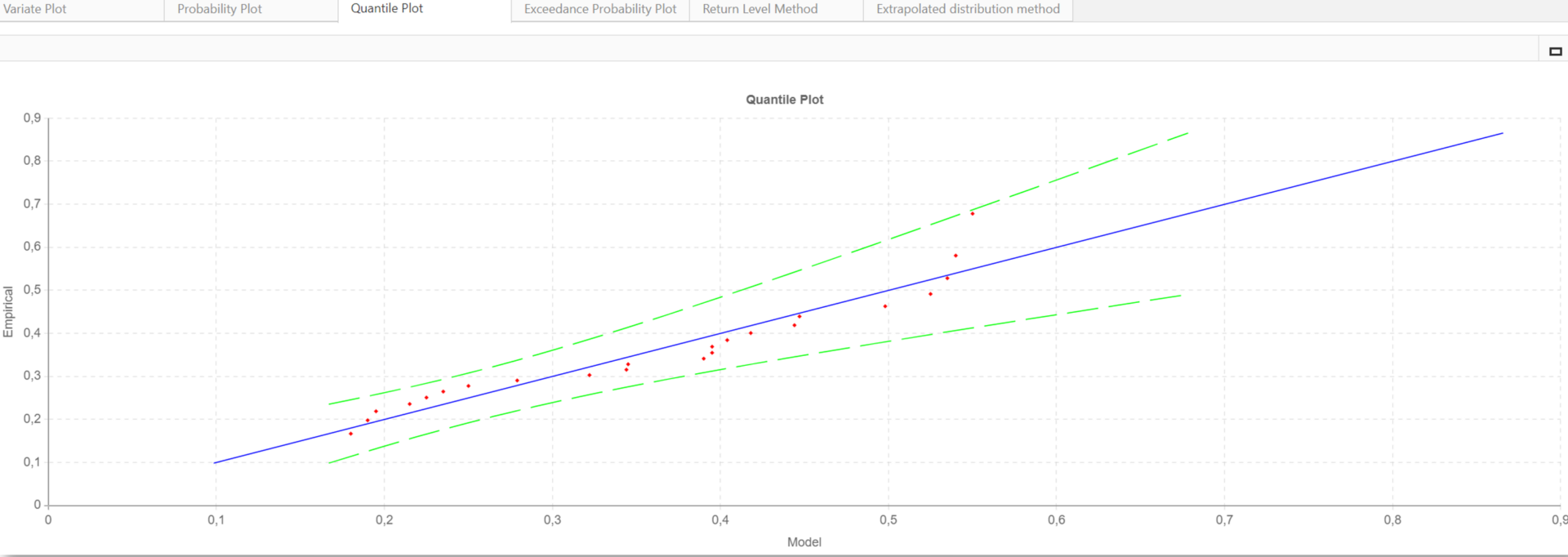
Эти визуальные инструменты помогают выявить расхождения или закономерности, которые могут быть не очевидны только с помощью статистических тестов. Очень важно не полагаться только на статистические методы. Анализ графических методов перед тем, как делать выводы, обеспечивает более надежную оценку соответствия. Кроме того, всегда следует оценивать прогнозируемые потери стенки и убедиться, что поведение коррозии хорошо изучено.
Расчет толщины стенок трубки для всего теплообменника
Цель состоит в том, чтобы статистически определить максимальные потери на стенках всего теплообменника. Для этого можно использовать два метода: Уровень возврата и Экстраполированное распределение. Эти методы помогают определить наиболее вероятную максимальную потерю стенки (экстремальное значение) и ее доверительные границы (ДГ). Давайте рассмотрим визуальное представление, которое поможет нам понять распределение значений потерь на стенках и соответствующие доверительные интервалы.
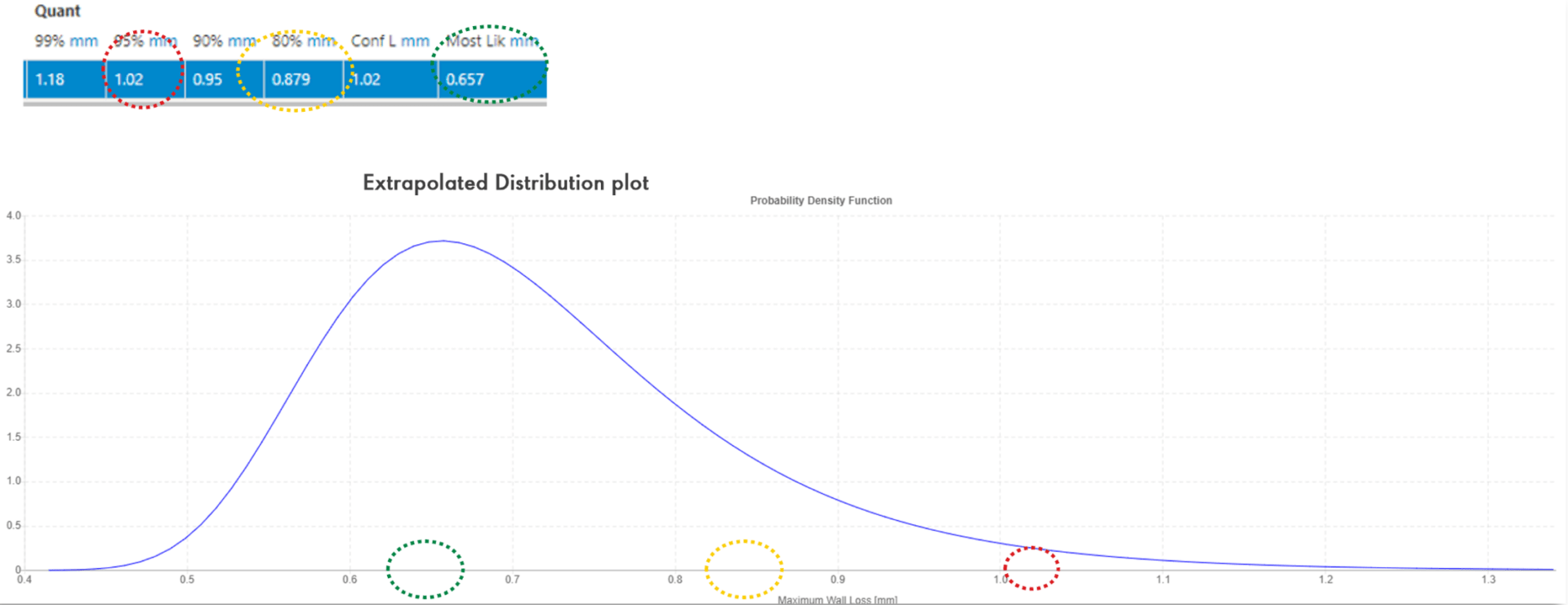
The image above shows an Extrapolated Distribution plot featuring a probability density function curve. The curve peaks at the most likely maximum wall loss value (highlighted by the green circle). It tapers off at both ends, illustrating the distribution of potential maximum wall loss values.
Quantile values, such as the 95th quantile at 1.02mm (marked by the red circle), indicate confidence bounds. This means 95% of the expected maximum wall losses are below 1.02mm, while 80% of the expected maximum wall losses are below 0.879mm (indicated by the yellow circle)
Конкретный пример: Анализ экстремальных значений для подогревателя сырой нефти с тремя теплообменниками
В нашем примере речь идет об осмотре подогревателя сырой нефти с тремя действующими составами. Эти теплообменники проработали 25 лет, отработав свой расчетный срок, и заказчик хотел продлить их срок службы еще как минимум на десять лет. Ранее для оценки состояния трубок через определенные промежутки времени проводились визуальные осмотры с помощью бороскопа, но они давали только качественные данные без измерения толщины стенок. Заказчику необходимо было определить необходимость замены.
За год до окончания срока службы, во время плановой остановки, теплообменники были осмотрены с использованием репрезентативных образцов. Это позволило оценить максимальную потерю стенок и решить, безопасно ли продолжать эксплуатацию еще десять лет.
All three heat exchangers had similar results, and we’ll concentrate on one of them. The heat exchanger bundle consists of 120 carbon steel tubes, 23 of which were inspected. Knowledge from previous borescope inspections helped identify the best tubes to examine. The renewal thickness was set at 1.1 mm, with a nominal wall thickness of 2.4 mm.
The inspection took place on October 1, 2023.
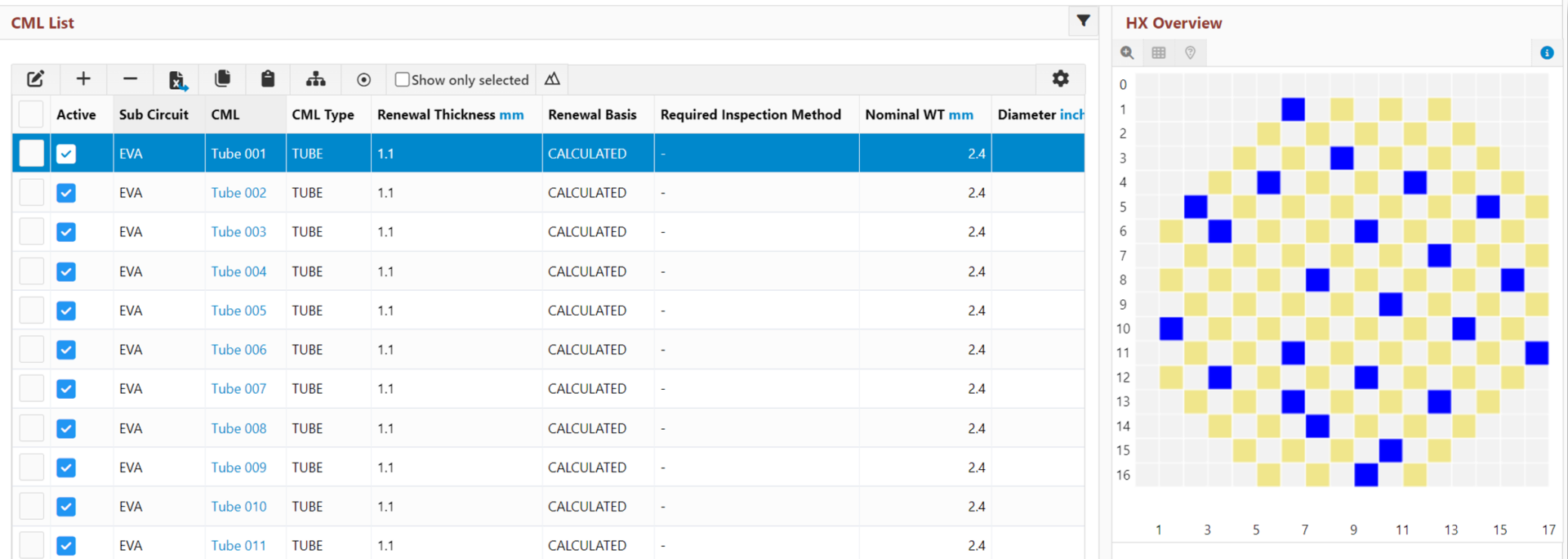
Для этого теплообменника было достаточно одной однородной стратификации. Значительных колебаний или локализованных участков с более высокой или низкой скоростью коррозии не наблюдалось; значения находились в узком диапазоне, как показано на гистограмме ниже. Это подтверждает, что собранные данные отражают весь теплообменник и позволяют получить достоверную информацию о его состоянии.
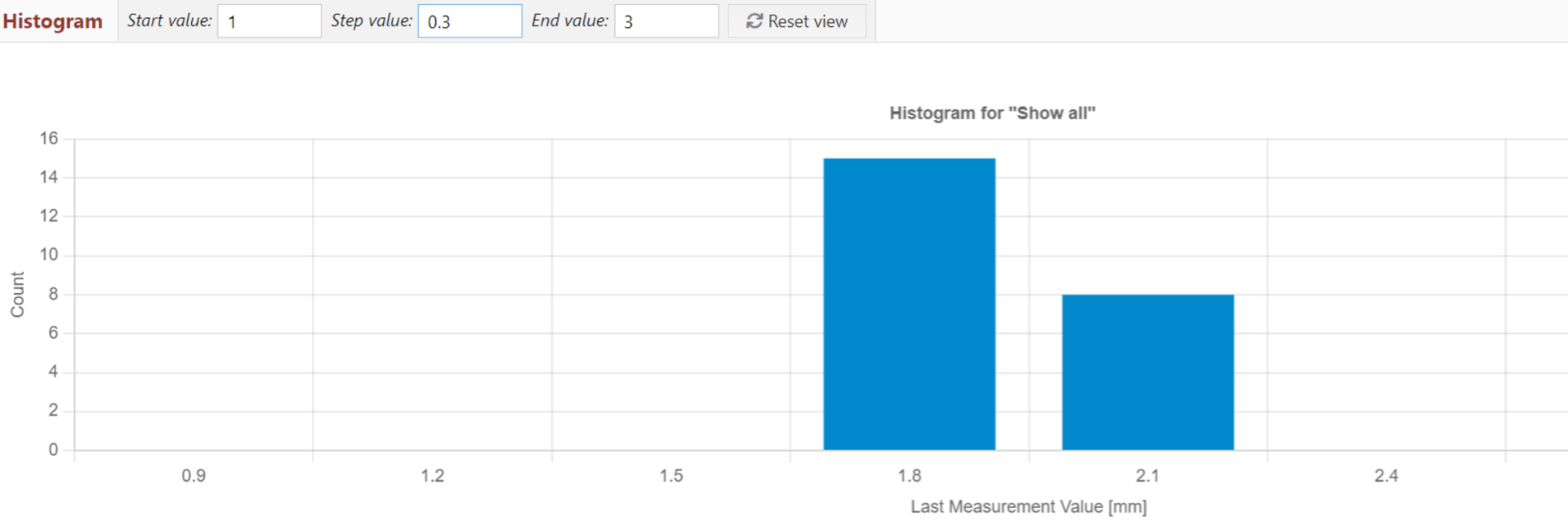
Оценка пригодности полученной статистической модели
Статистические тесты и графические методы показали хорошее соответствие данных. Тесты Колмогорова-Смирнова (p-KS) и Андерсона-Дарлинга (p-AD) показали p-значения больше 0,5, что подтверждает качество подгонки (см. результаты ниже).
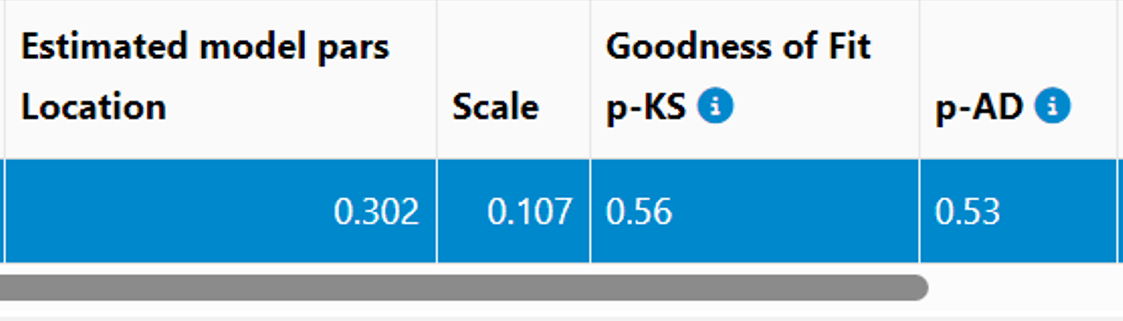
Графики также показали, что теоретическое распределение хорошо согласуется с данными выборки, обеспечивая уверенность в анализе и подтверждая хорошее соответствие. Ниже вы можете увидеть это на графиках вероятностей.
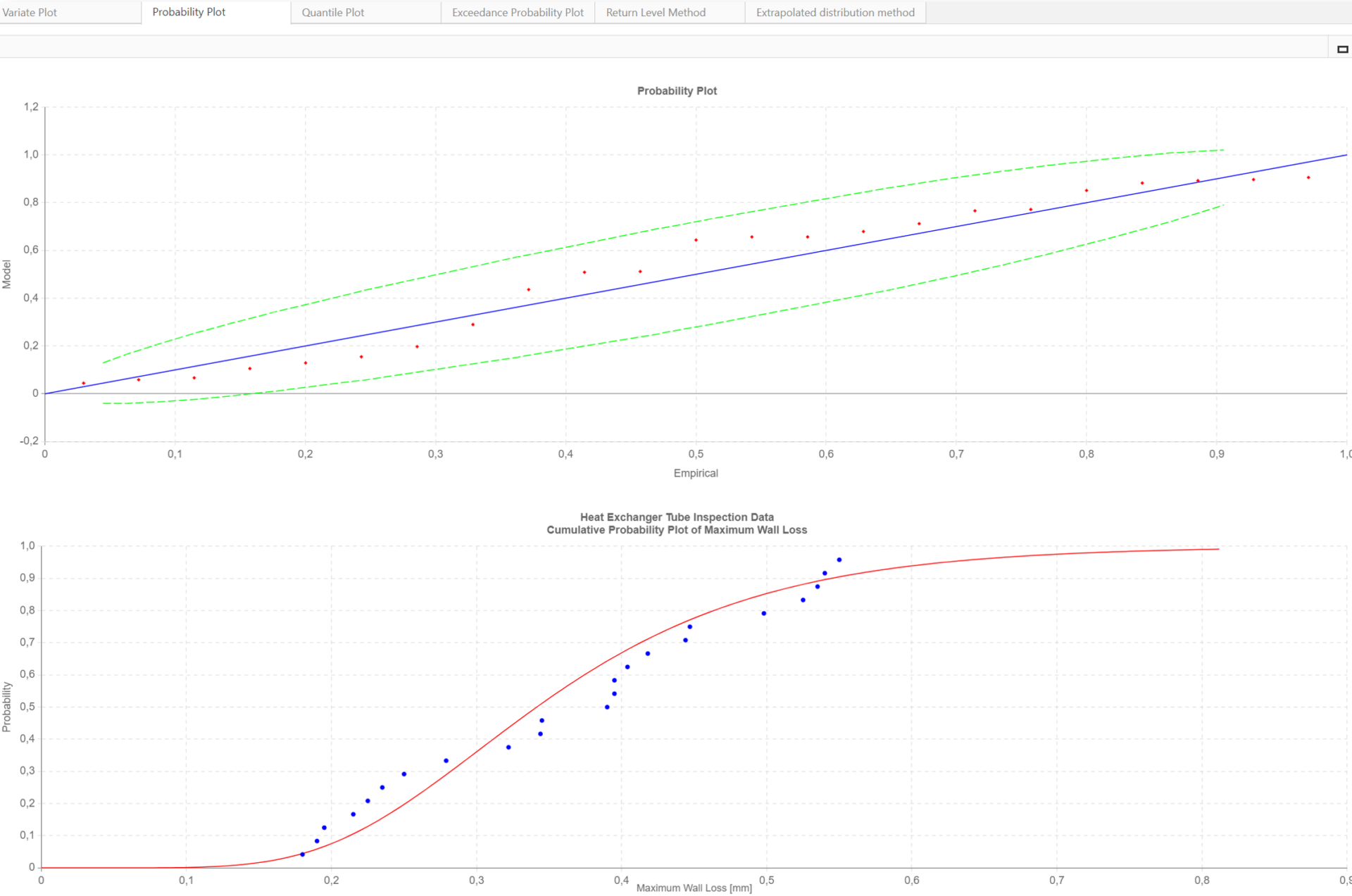
Расчет толщины стенок трубки для всего теплообменника
Next, the Return Level Method was used to extrapolate the data in space to calculate the maximum wall loss for the entire heat exchanger. The most likely maximum wall loss was 0.816 mm (indicated in red). At the 99% confidence bound, the maximum wall loss was 1.059 mm (indicated in yellow), and at the 80% confidence bound, it was 0.937 mm (indicated in green). The graphs below illustrate these findings.
The upper graph shows the return level curve with the 99% confidence bound, while the lower graph shows the curve with the 80% confidence bound. As you can see, higher confidence bounds lead to more conservative estimates, showing greater wall loss, indicating a thinner remaining tube wall thickness and a shorter useful life for heat exchangers.

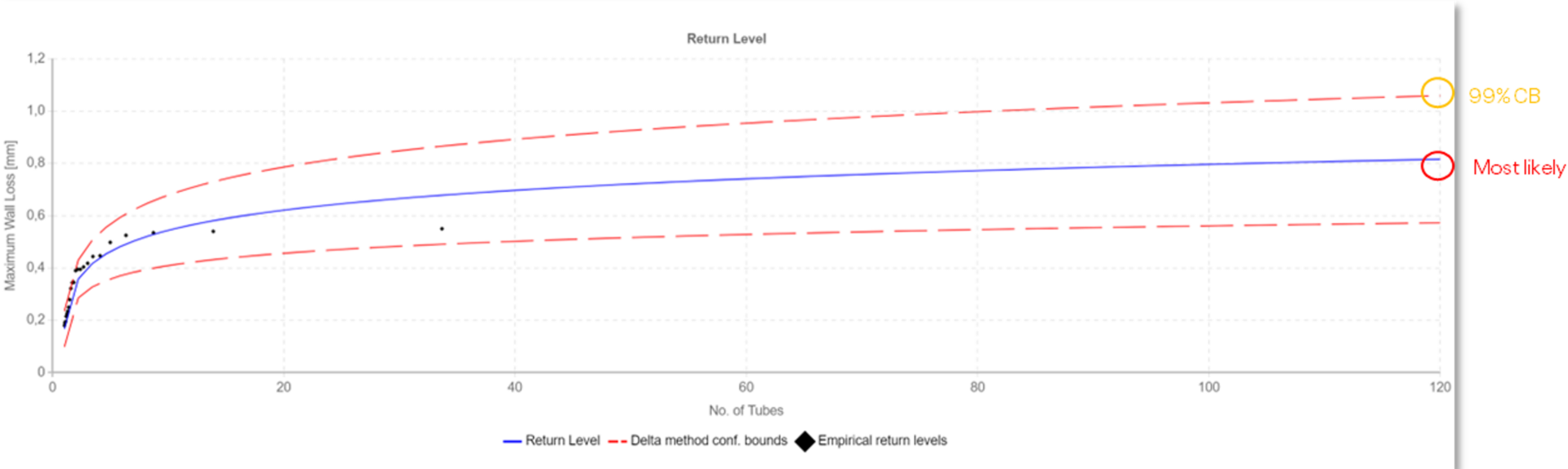
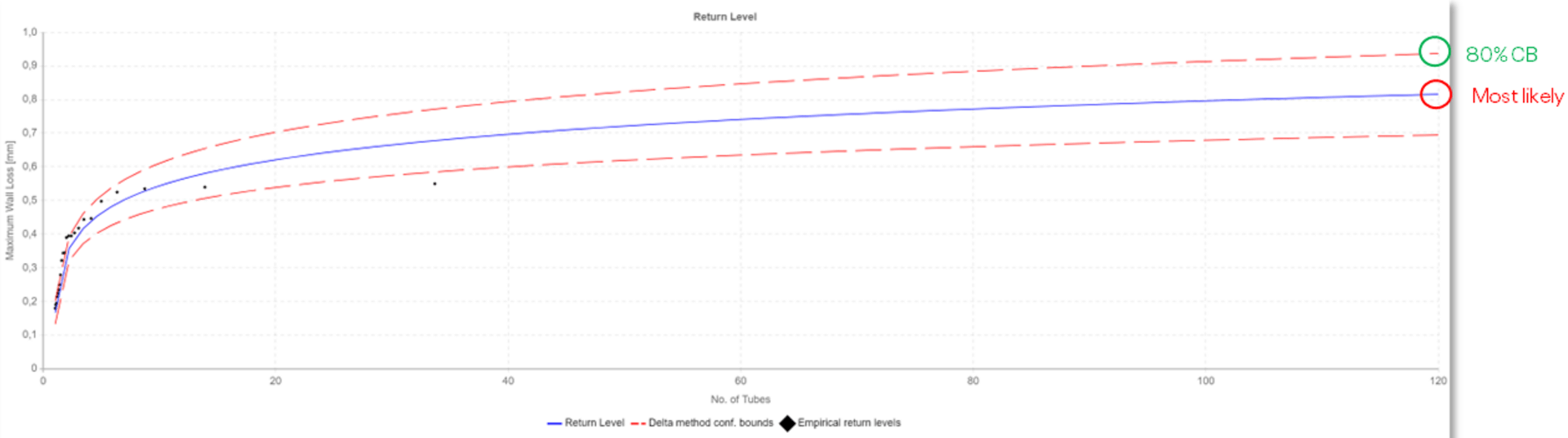
Расчет срока службы теплообменника и даты следующей проверки
Минимальная оставшаяся толщина стенки трубки и скорость коррозии теплообменника были рассчитаны для различных доверительных границ. Эти расчеты позволили определить срок службы теплообменника, максимальный интервал между проверками и дату следующей проверки.
На изображениях ниже представлено подробное описание результатов. Во-первых, в двух таблицах показаны минимальная остаточная толщина стенок теплообменника и скорость коррозии при различных уровнях достоверности (95 %, 90 % и 80 %).
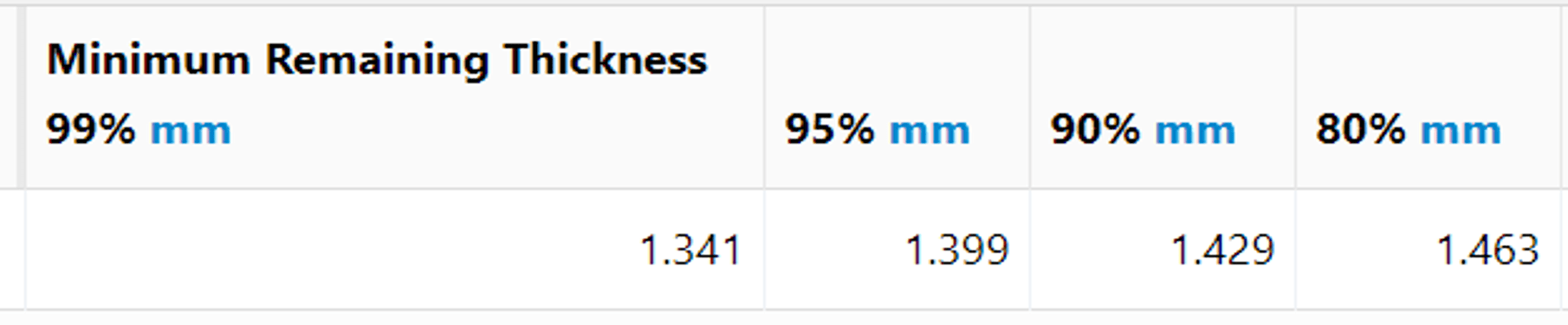

The calculation summary then shows the heat exchanger’s useful life (Remnant Life), corrosion rate (Rate), and next inspection date (Next Insp Date) at the 80% confidence level. It’s important to note that the corrosion engineer determines the choice of confidence bound. Typically, using a representative sample and conducting multiple inspections over time increases confidence in the results, allowing for the use of lower confidence bounds.
In this case study, the information gathered from previous borescope inspections gave the engineers enough confidence in the new results to select the 80% confidence bound.
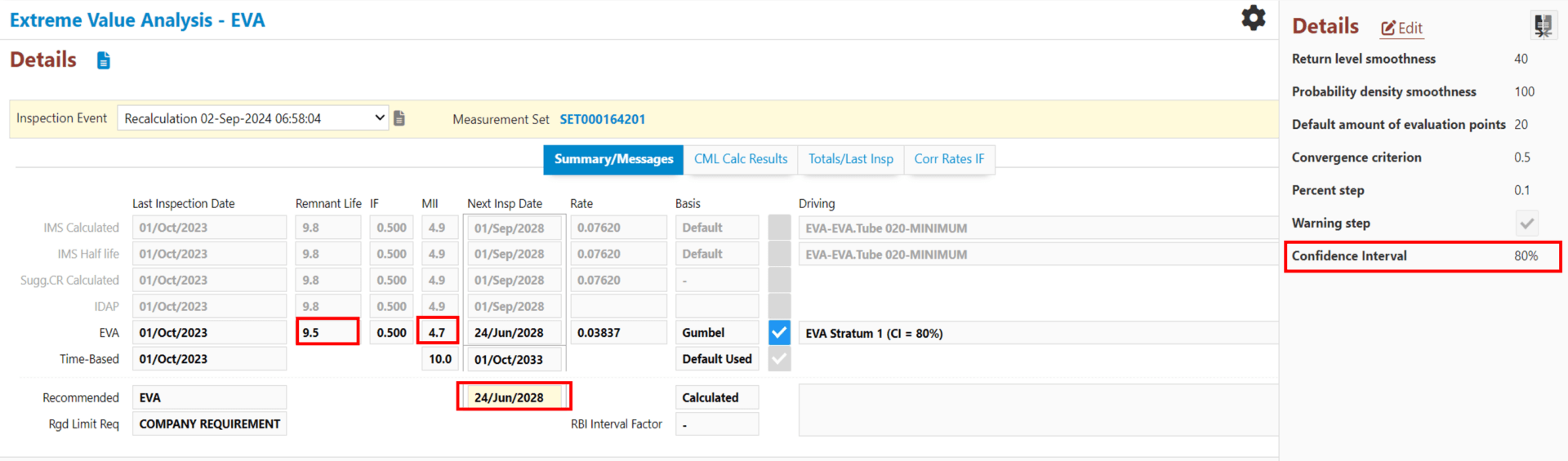
Поскольку срок службы теплообменника оценивается в 9,5 лет (близко к желаемому десятилетнему продлению), применение стандартной для отрасли концепции полураспада установило максимальный интервал между проверками (MII) в 4,7 года, а следующая проверка запланирована на 24 июня 2028 года. Ниже приведен расчет (при доверительной вероятности 80%):
Остаточный срок службы = (Минимальная остаточная толщина - Толщина обновления) / Скорость коррозии = (1,1463 мм -1,1 мм) / 0,038 мм/год = 9,5 лет
Дата следующей проверки = Дата последней проверки + остаточный срок службы ∗ ЕСЛИ = 1 октября 2023 года + 9,5*0,5 = 24 июня 2028 года
Эти результаты дали инженерам уверенность в состоянии теплообменника. Вместо того чтобы решиться на полную замену, они были уверены в том, что предпримут необходимые меры, чтобы сохранить его работоспособность еще на десять лет. Если бы предполагаемый срок службы был короче, они могли бы рассмотреть дополнительные варианты, например, использование ингибиторов коррозии для замедления коррозии в теплообменнике. Однако теперь они знали, что до следующей инспекции никаких действий предпринимать не нужно.
Результаты тематического исследования: Сокращение продолжительности инспекции и времени выполнения работ
The benefits of using this heat exchanger tube wall thickness calculation approach were significant. By conducting inspections on a representative sample, engineers reduced overall inspection time and preparation activities by at least 40%, streamlining the entire process.
Due to the heat exchangers being part of the critical path, the turnaround time was also shortened by 12%, allowing production to restart sooner than expected. Additionally, a deeper understanding of risks and threats led to an estimated 85% cost savings by avoiding expensive maintenance actions like repairs and replacements. These advantages highlight how EVA makes the heat exchanger inspection process smarter, faster, and more efficient.
Заключение: EVA обеспечивает эффективные и уверенные проверки
In summary, EVA provides significant time and cost savings for inspections and tube cleaning while ensuring they are performed at the right intervals. By using a representative sample and conducting multiple inspections over time, the conservatism in models can be minimized.
This makes EVA a reliable framework for efficient heat exchanger inspections. For added assurance, IMS PEI allows for independent assessment of tube degradation risks, which can be combined with EVA to determine the optimal time for the next inspection.
Пожалуйста, заполните форму ниже, чтобы увидеть EVA и IMS PEI в действии.
Хотите узнать больше о IMS?
Запросите демонстрацию ниже, чтобы воочию увидеть его возможности!
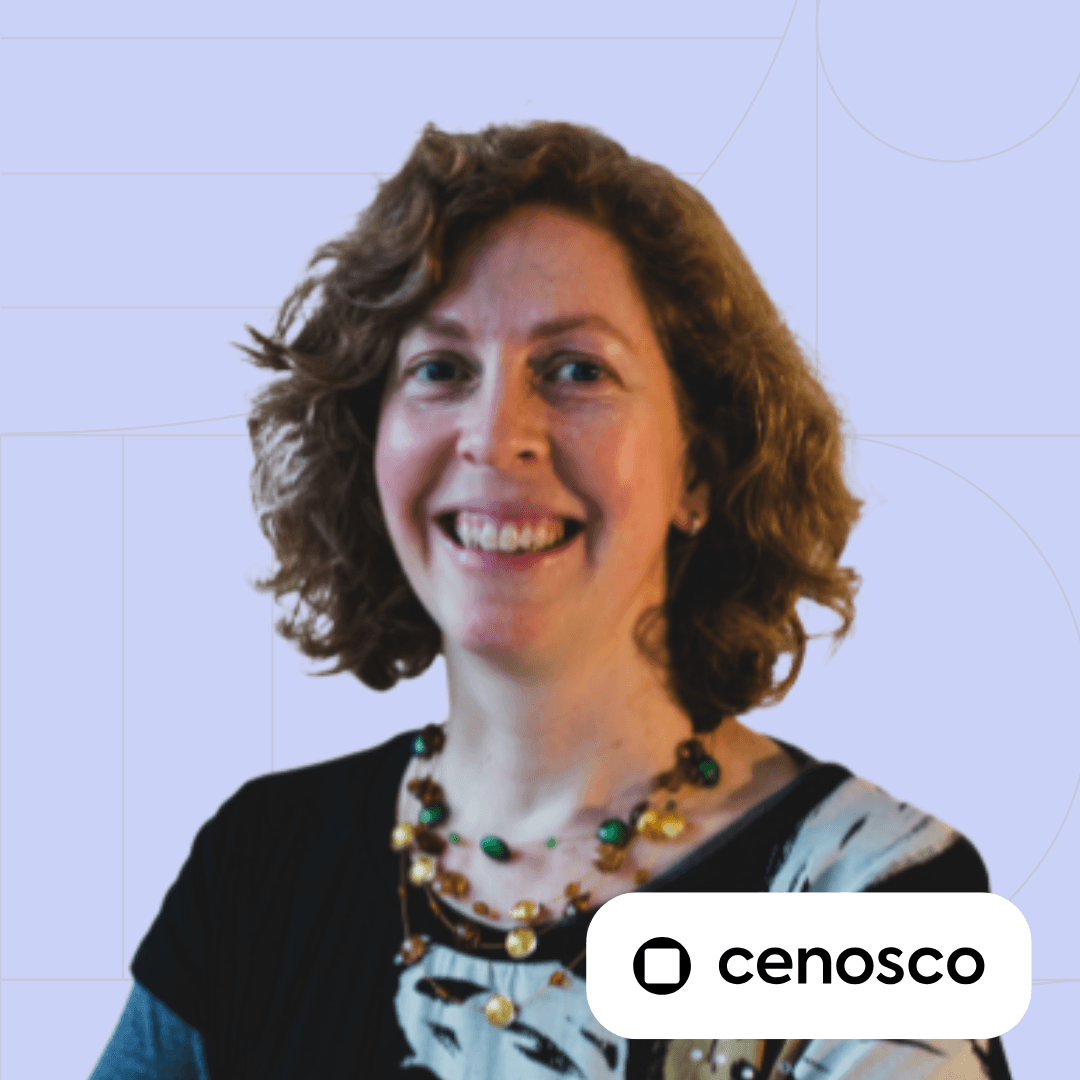
Elsa Tolsma-de Klerk Technical Writer
Elsa is an engineer with a passion for sharing knowledge. She holds a Master’s in Electronic Engineering and spent over a decade at Sasol as an Advanced Process Control Engineer, where she gained hands-on experience in optimization, control systems, and writing technical documentation. Since 2019, she’s been a Technical Writer at Cenosco, now leading the IMS knowledge base and training Academy team.