Cathodic protection management refers to the systematic and strategic approach taken to protect metal structures and equipment from corrosion.
Corrosion is a natural process that can cause deterioration and damage to metallic assets, such as pipelines, storage tanks, bridges, offshore platforms, and other infrastructure.
Cathodic protection is an electrochemical technique used to mitigate corrosion and extend the lifespan of metal structures.
It involves the application of direct current (DC) to the metal surface, which alters the electrochemical reactions that cause corrosion.
Index
The Types of Cathodic Protection
Key Aspects of Cathodic Protection Management
Cathodic Protection Management in the Oil & Gas and Chemical Processing Industries
FAQ: Frequently Asked Questions
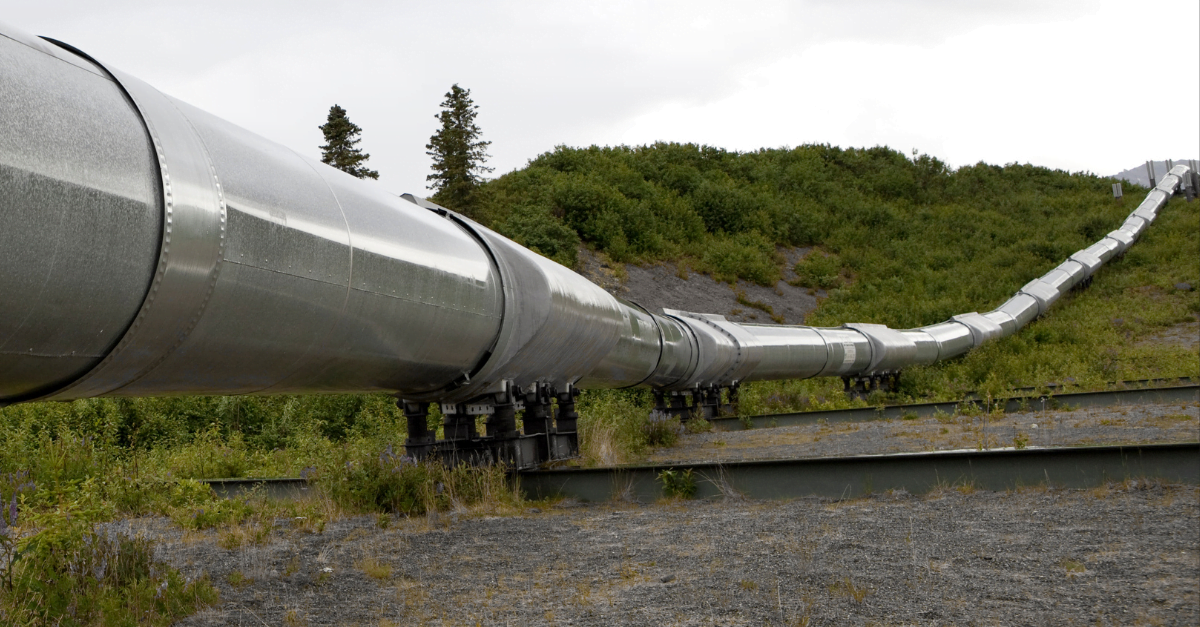
The Types of
Cathodic Protection
Galvanic (Sacrificial) Cathodic Protection:
In this method, a more reactive metal is connected to the structure to be protected, creating a galvanic cell. This sacrificial metal corrodes instead of the protected structure, effectively sacrificing itself to prevent corrosion damage.
Impressed Current Cathodic Protection:
With impressed current cathodic protection, an external power source (rectifier) is used to provide the required direct current to the structure. This way, the structure remains protected, and no metal is sacrificed.
By conducting regular maintenance and inspections according to the checklist, businesses can optimize equipment performance, resulting in improved efficiency, reduced energy consumption, and enhanced productivity.
Key Aspects of Cathodic Protection Management
Cathodic protection management plays a vital role in preventing corrosion-related failures, reducing maintenance costs, and enhancing the safety and integrity of metal structures, particularly in harsh environments or corrosive conditions.
Design and Installation
Thorough analysis and planning are essential for the effective implementation of cathodic protection. This includes determining the type of protection required, selecting appropriate materials, and designing the system layout.
Regular Inspection and Maintenance
Scheduled inspections are critical to ensuring the cathodic protection system is functioning correctly.
Maintenance activities may involve replacing sacrificial anodes (in galvanic systems), checking electrical connections, and verifying system integrity.
Monitoring and Control
Cathodic protection systems should be continuously monitored to detect issues or deviations from the desired protection levels. Remote monitoring equipment can be used to track performance over time.
Compliance and Regulatory Standards
For industries like oil and gas, water distribution, and marine structures, there are often regulatory requirements that mandate the use of cathodic protection systems.
Proper management ensures compliance with these standards.
Corrosion Risk Assessment
Periodic corrosion risk assessments are conducted to evaluate the effectiveness of the cathodic protection system and determine if any adjustments or upgrades are necessary.
Documentation and Reporting
Maintaining detailed records of all aspects of the cathodic protection system, including design plans, inspection reports, and maintenance records, is crucial for accountability and decision-making.
What is the purpose of Cathodic Protection Management?
The purpose of Cathodic Protection Management is to prevent corrosion and extend the life of metal structures and equipment. By applying direct current to the metal surface, cathodic protection systems alter the electrochemical reactions that cause corrosion, effectively protecting the structures from damage.
Which industries benefit from Cathodic Protection Management?
Cathodic Protection Management is essential for various industries, including oil and gas, water distribution, transportation (pipelines, bridges), marine and offshore structures, storage tanks, and industrial facilities. These industries often have valuable metal assets exposed to corrosive environments, making cathodic protection crucial for their integrity and longevity.
How long does a Cathodic Protection System last, and does it require ongoing maintenance?
The longevity of a cathodic protection system depends on various factors, including the type of system, the environment it operates in, and the quality of installation. Galvanic systems typically last 10-20 years, while impressed current systems can last even longer. Ongoing maintenance is crucial to ensure the system’s continued effectiveness. Regular inspections, anode replacements (in galvanic systems), and rectifier monitoring are essential to maintain optimal performance.
Contact Us
Learn more about the leading
Asset Integrity Management Software