Having access to real-time information impacts the success of field operations. It can mean the difference between achieving targets or facing obstacles. When real-time data is missing, decision-making is delayed, slowing down problem-solving. This delay is often due to field workers struggling with connectivity to their team, internet, and databases.
Embracing the rising “Connected Worker” trend, many companies are adopting advanced technology to integrate their workforce. By implementing digital tools like mobile apps, cloud computing, IoT devices, and AI (Artificial Intelligence) algorithms, organizations enable their field operators to transition into fully integrated and connected workers seamlessly.
Enter our innovative IMS4Field technology – designed to provide field crews with tools to improve their daily tasks and connectivity. It has already demonstrated remarkable results. For instance, at a European refinery owned by a major energy company, after implementing IMS4Field technology, productivity during inspections increased by 50%. Read along as we discuss how CENOSCO’s IMS4Field enhances field operations.
What is a Connected Worker?
A connected worker is an employee who uses advanced technology through a Connected Worker Platform to enhance their work environment significantly. This type of worker is an essential component of modern industries.
What is a Connected Worker Platform?
Connected Worker Platforms are digital tools that improve the experience of field employees in various industries. By integrating with mobile devices, they provide seamless communication, collaboration, guidance, and support for field operators. These platforms offer tools to manage workflows, schedule tasks, and monitor employee performance, allowing businesses to move beyond traditional methods of operation.
What is IMS4Field?
IMS4Field is a component of the IMS (Integrity Management System) Suite that embodies the evolution of connected worker platforms. It is a mobile tool that improves worker’s connectivity, ideal for bringing to the field on a tablet or iPad. It allows you to check work orders and input findings data directly. This digital solution optimizes task execution, inspections, maintenance, and instrumentation-proof tests. It also facilitates efficient data collection, task tracking, and seamless integration with the IMS Suite. Ultimately, it boosts productivity and ensures asset integrity within organizations.
The real game-changer lies in the powerful IMS4Field Dynamic Forms Checklists, which sync with the IMS Suite in real-time. With these customizable checklists, you no longer have to convert notes to digital format or enter duplicate information manually. Dynamic Forms ensures your data is always up-to-date and easily accessible across the organization.
Benefits of IMS4Field
- IMS4Field’s offline feature allows you to work on your checklists anywhere, anytime, without interruptions. It makes it easy to carry out inspections, maintenance tasks, and proof tests with ease, ensuring consistent and efficient workflow even in remote locations.
- We understand how important it is to keep your data secure. That’s why IMS4Field allows you to easily grant access to trusted users and manage their permissions securely through IMS. You can rest assured that your sensitive information is kept confidential and under your control.
- IMS4Field offers a feature that enhances the quality of your digital checklists by allowing you to add supporting documents like photos and videos. By uploading additional content, you can provide in-depth context and capture essential information to ensure a comprehensive understanding of each task.
- Accessing relevant information for your field tasks has never been easier. Our intelligent interface ensures you see only what’s important for your work without any distractions or clutter. This lets you focus on what you need to do, reducing the likelihood of overdue tasks.
IMS4Field vs IMS
You are probably wondering why we need a dedicated s4Field application when IMS is already a versatile and powerful app that can be accessed on tablets or mobile devices. The answer lies in the specialized focus and efficiency that IMS4Field brings to the table.
Originally designed for engineers, IMS’s primary purpose was not centered around fieldwork. While IMS offers a diverse array of functionality, like a Swiss army knife, there are instances where a specialized tool with a singular purpose proves more effective. That’s where IMS4Field comes in. It’s a lite version of IMS customized for inspections, maintenance, and instrumentation-proof tests.
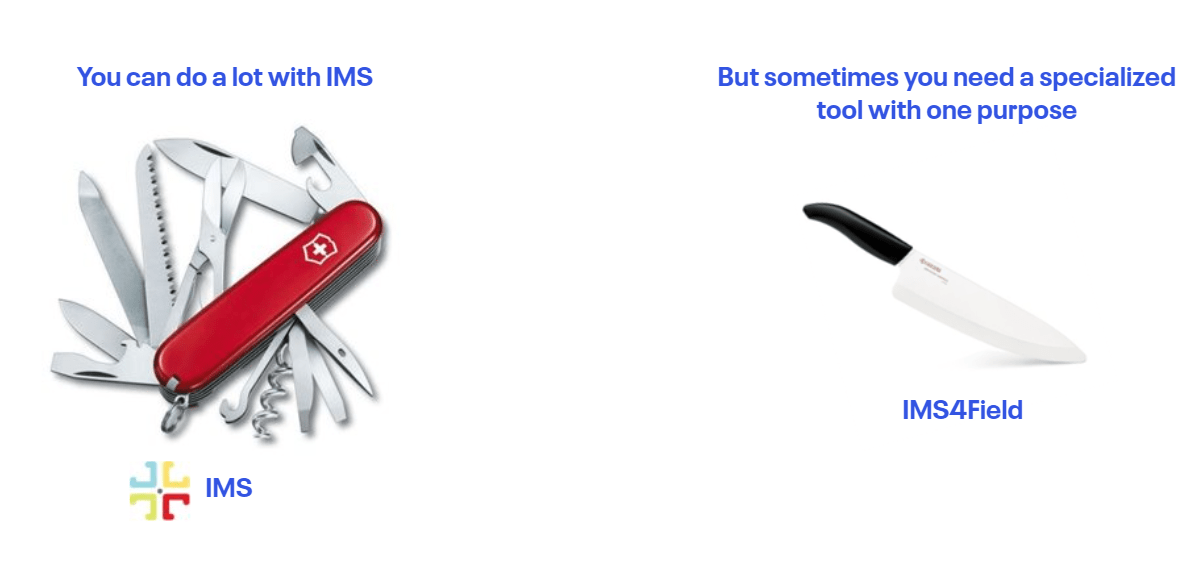
Did you know that IMS4Field is designed to make life easier for field workers? It’s true! In fact, accessing schedules is seven times faster, taking just 14 seconds with IMS4Field compared to the standard IMS’s 95 seconds. That’s a huge difference, don’t you think? So, if you’re working in the field, IMS4Field is the way to go!
How IMS4Field Works?
Let’s explain how IMS4Field and IMS work in a real-life example.
In a bustling industrial facility, John, the meticulous planner, sits at his desk and works in IMS, creating schedules. John assigns these schedules to Mark, the diligent field executor.
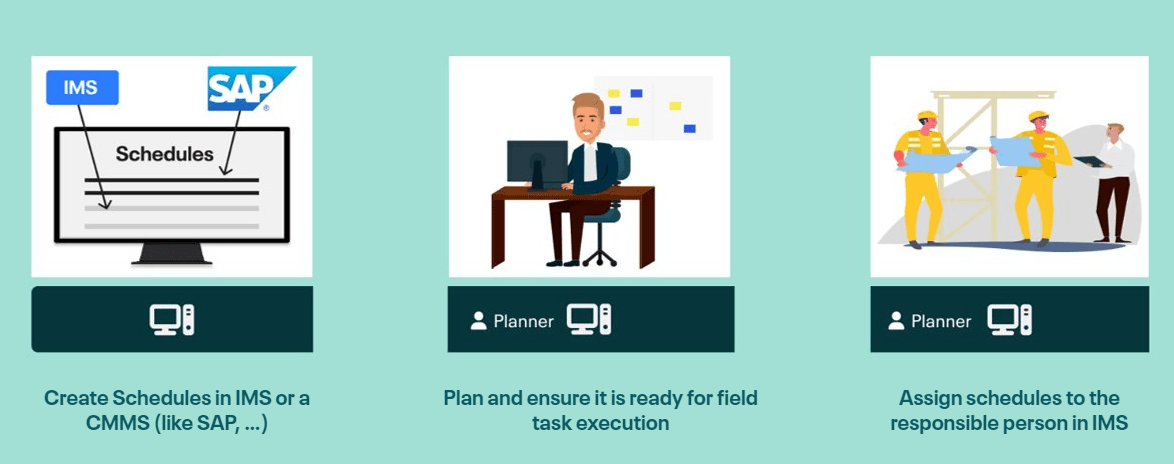
Armed with his iPad, Mark logs into IMS4Field to pull his inspection schedules from IMS. With only a few taps on his device, he can access his assigned tasks, execute them, record his findings in real-time within IMS4Field, and first-level approve them.
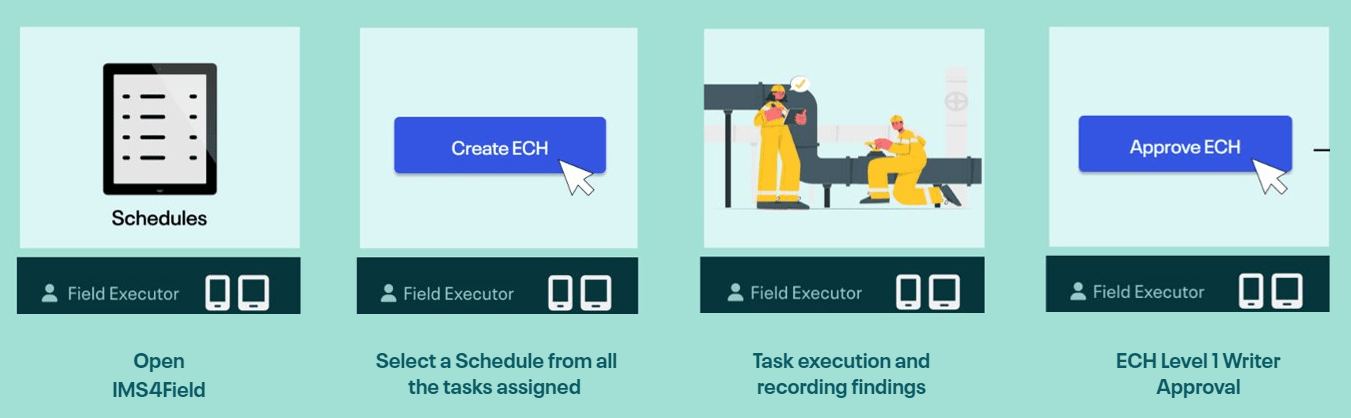
Although Mark may temporarily lose his internet connection at his present location, he can perform all his tasks as if he were working online. Upon regaining internet access, IMS4Field will automatically transmit the data Mark gathered to IMS and John.
Back at his desk, John monitors the progress of checklists on the IMS dashboard. He swiftly identifies incomplete ECHs (Equipment Condition History) and guides Mark to rectify any discrepancies. Notifications ping as ECHs await final approval. He reviews each one meticulously before giving his seal of approval. In cases where ECHs are incomplete, he flags them for revision and sets them to draft until they meet the required standards.
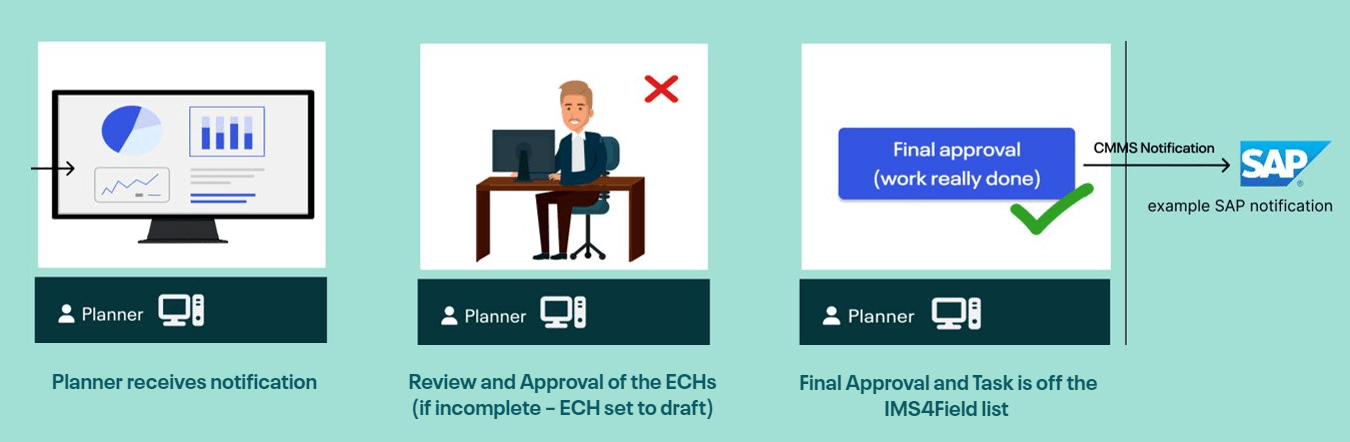
The seamless collaboration between John’s planning and Final approval in IMS and Mark’s execution in IMS4Field ensures that every task is completed with precision and efficiency. As final approvals are granted, schedules seamlessly transition from IMS to the company’s CMMS for further processing, closing the loop on a successful workflow driven by teamwork and technology.
What can IMS4Field do for you?
Imagine staying informed about every detail concerning your equipment – from overdue tasks to condition history and actionable insights – all conveniently at your fingertips. With CENOSCO’s IMS4Field, you hold the key to unlocking instant access to vital data.
As your businesses navigate the complexities of a connected workplace, investing in tools like IMS4Field becomes the key to achieving success. IMS4Field is here to support you by offering a diverse range of capabilities by:
- Seamlessly connecting scoping with execution,
- Carrying out inspections and operator rounds,
- Replacing native applications with Progressive Web Apps (PWA), and
- Improving desktop and responsive interfaces for easier usability.
With its robust planning and scheduling features, IMS4Field can significantly boost your productivity during inspections. The real-time data capture through the IMS4Field mobile app simplifies data collection processes and enhances task visibility, empowering your field teams to achieve higher levels of efficiency. Integrated solutions promote collaboration, making IMS4Field an ideal choice for any organization looking to streamline its inspection processes.
Say goodbye to the days of cumbersome paper checklists and welcome the era of digital efficiency in your field operations. Fill in the form below if you would like to know more.
Want to see IMS4Field in action?
Fill out the form below and we will be in touch to get you started with a demo.
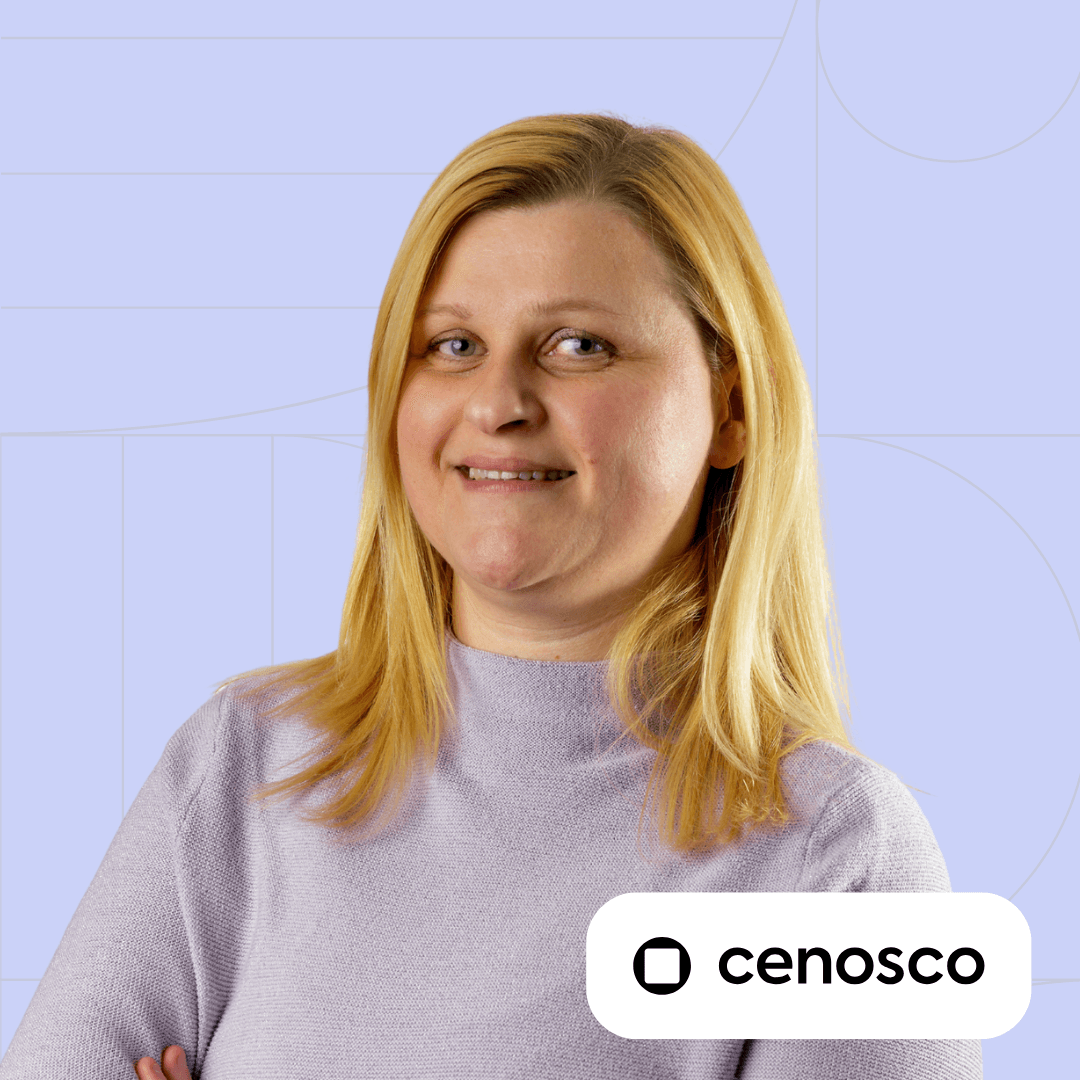
Denis Tkalec Technical Writer
Denis Tkalec is a technical writer at Cenosco, specializing in asset integrity management software since 2022. With a background in education and six years in marketing, she turns complex topics into clear, user-friendly content. Inspired by Camus’s belief that “a writer keeps civilization from destroying itself,” she brings precision and care to every manual.