Impressed current cathodic protection (ICCP) is a corrosion mitigation strategy that uses the power of electricity to inhibit the electrochemical reactions responsible for metal corrosion.
This approach is widely used in construction, marine, and oil and gas industries. The oil and gas sector relies on impressed current cathodic protection to shield buried pipelines carrying vital resources, as these are highly susceptible to external corrosion from perpetual soil and water contact.
In previous articles, we provided an overview of cathodic protection and its importance in safeguarding metal from corrosion. Now we will take you on a deep dive into the world of Impressed Current Cathodic Protection.
We will explain how ICCP works and explore the survey methods for monitoring its performance on buried pipelines.
Understanding Impressed Current Corrosion Protection (ICCP)
Corrosion is a natural process that affects metal. The degree of corrosion depends on the metal type and surrounding environment. Metal atoms have loosely attached electrons that they tend to lose.
When a metal is placed in an electrolyte, such as seawater, this tendency leads to the formation of an electric potential difference between anodic and cathodic areas on the metal surface. Corrosion happens when the metal loses electrons from the areas that act like anodes.
Impressed Current Cathodic Protection (ICCP) applies a low-voltage direct current to a metal structure, such as a buried pipeline or ship hull, to stop corrosion. This forces the entire metal surface to become a cathode, which stops the loss of electrons and prevents corrosion.
An Impressed Current Cathodic Protection (ICCP) system is composed of:
- Rectifier – an electrical device that converts alternating current (AC) from the power grid into direct current (DC).
- Anode – an inert, conductive material (e.g., mixed metal oxide or graphite) buried in the soil at some distance from the pipeline.
- Reference Electrode – a specialized electrode buried near the pipeline that measures the electrical potential between the pipeline and the surrounding soil.
The rectifier sends electrical current from the anode to the metal, making it the cathode in the electrochemical reaction. This way, the current is “impressed” onto the metal structure, hence the name “impressed current cathodic protection.”
This impressed current creates a negative electrical potential on the metal, which counteracts the natural corrosion-causing potential difference between the metal structure and the surrounding environment.
The reference electrode monitors the potential difference and provides feedback to the rectifier, allowing the system to automatically adjust the current to maintain the desired level of cathodic protection.
How Impressed Current Cathodic Protection Works on a Buried Pipeline
Without any corrosion protection, a buried metal pipeline is susceptible to electrochemical corrosion due to the differences in electrical potential between the pipeline and the surrounding soil or seawater.
This can lead to gradual deterioration and eventual pipeline failure over time. ICCP protects the pipeline from corrosion by applying a low-voltage direct current to the external surface of the buried pipeline, which becomes the cathode in an electrochemical reaction.
This current creates a protective barrier around the pipeline, preventing the corrosion-causing chemical reactions from taking hold.
Advantages of Impressed Current Cathodic Protection (ICCP):
- ICCP provides active, continuous protection against corrosion, unlike passive methods like sacrificial anodes.
- The system can be designed to provide adequate protection for the entire pipeline length, even in varying soil conditions.
- ICCP can be monitored and adjusted remotely, allowing for efficient maintenance and optimization of the system.
- ICCP is highly effective in preventing corrosion, which can significantly extend the lifespan of buried pipelines.
By understanding the principles of impressed current cathodic protection (ICCP) and applying them to pipelines, the oil and gas industry can effectively prevent corrosion, maximize the lifespan of pipelines, and reduce the costs associated with maintenance and replacement.
Survey Techniques for Assessing ICCP Effectiveness
Any corrosion to the pipeline can lead to leaks, environmental contamination, and disruptions in delivering essential resources like oil, gas, and water. For that reason, maintaining the integrity of buried pipelines is critical, and impressed current cathodic protection (ICCP) systems play a pivotal role in this endeavor.
However, simply installing an ICCP system is not enough – regular monitoring and maintenance are essential to ensure its long-term effectiveness in preventing corrosion.
Industry best practices recommend that ICCP systems undergo comprehensive surveys at least once a year. These annual assessments provide a thorough evaluation of the system’s performance. They allow you to identify any areas where the protection may be inadequate or compromised.
By conducting these surveys diligently, you can avoid potential issues and make informed decisions about necessary repairs or upgrades to the system.
1. Cathodic Protection (CP) Test Post Potential Survey
This survey measures the potential between the pipeline and surrounding soil/water to evaluate the CP system’s effectiveness.
There are two key potential measurements:
- “On” potentials with CP current applied, indicating protection level.
- “Instant off” potentials with CP current interrupted, showing true polarized potential.
Adequate protection is confirmed if either:
- “Instant off” potential is -850 mV or more negative vs copper/copper sulfate reference
- “Instant off” potential is at least 100 mV more negative than the native (unprotected) potential
If potentials don’t meet these criteria for effective cathodic protection, adjustments need to be made to the CP system. The CP potential survey provides critical data on the CP system’s availability and effectiveness, allowing pipeline operators to verify adequate corrosion protection.
2. Close Interval Potential Survey (CIPS)
This survey measures the electrical potential along the Onshore pipeline at close intervals, typically every 1-2 meters. It assesses the CP protection effectiveness along the entire pipeline and helps localize areas of insufficient protection.
3. Direct Current Voltage Gradient (DCVG) Survey
This survey measures the voltage gradient on the surface of the soil or water above the pipeline. It is a handy way to measure coating effectiveness and detect coating defects. Areas with high voltage gradients indicate potential coating damage, which can lead to corrosion if left unrepaired.
4. Wet Insulation Detection Survey
The survey aims to identify moisture intrusion in the insulation of ICCP anodes or cables. It is conducted by applying a voltage between the anode or cable and the pipeline. If the current flows, the moisture is present in the insulation. This helps pinpoint areas where insulation has deteriorated or sustained damage, potentially compromising the ICCP system’s effectiveness or leading to system failure.
5. Rectifier Station Survey
The rectifier station survey evaluates the performance and condition of the rectifier, which powers the ICCP system. The survey measures the input and output voltages and currents, and the rectifier components’ condition.
The goal is to ensure the rectifier is operating within its design parameters and providing the necessary current to the ICCP system. Any issues identified, such as high resistance connections or malfunctioning components, should be addressed promptly to maintain the system’s effectiveness.
Centralizing ICCP Data for Comprehensive Pipeline Integrity Assessments
While the ICCP systems are crucial for preventing corrosion, the data gathered through the ICCP surveys are invaluable, as they can be used to make informed choices that preserve the integrity of buried pipelines.
Meet IMS PLSS: Pipeline and Subsea Systems
Cenosco’s IMS PLSS (Pipeline and Subsea Systems) provides pipeline operators with a comprehensive platform to manage all aspects of pipeline integrity, including ICCP survey planning and data analysis.
One of the key features of IMS PLSS is its ability to generate schedules for ICCP surveys, ensuring that these critical inspections are conducted at appropriate intervals. Once the surveys are complete and data entered into the system, the repair schedules can also be triggered, based on the survey findings.
The External Corrosion module within IMS PLSS serves as a centralized hub where operators can consolidate and examine ICCP survey data alongside other pipeline integrity information. It features a dedicated section for ICCP data, where you can easily input survey findings, detect issues, and track historical trends.
This module allows you to calculate the external corrosion rate of your pipeline thus ensuring that ICCP data is seamlessly incorporated into the external corrosion calculation, promoting a holistic approach to pipeline integrity and external corrosion prevention.
Want to learn more about IMS?
Request a demo below to get a first-hand look at its capabilities!
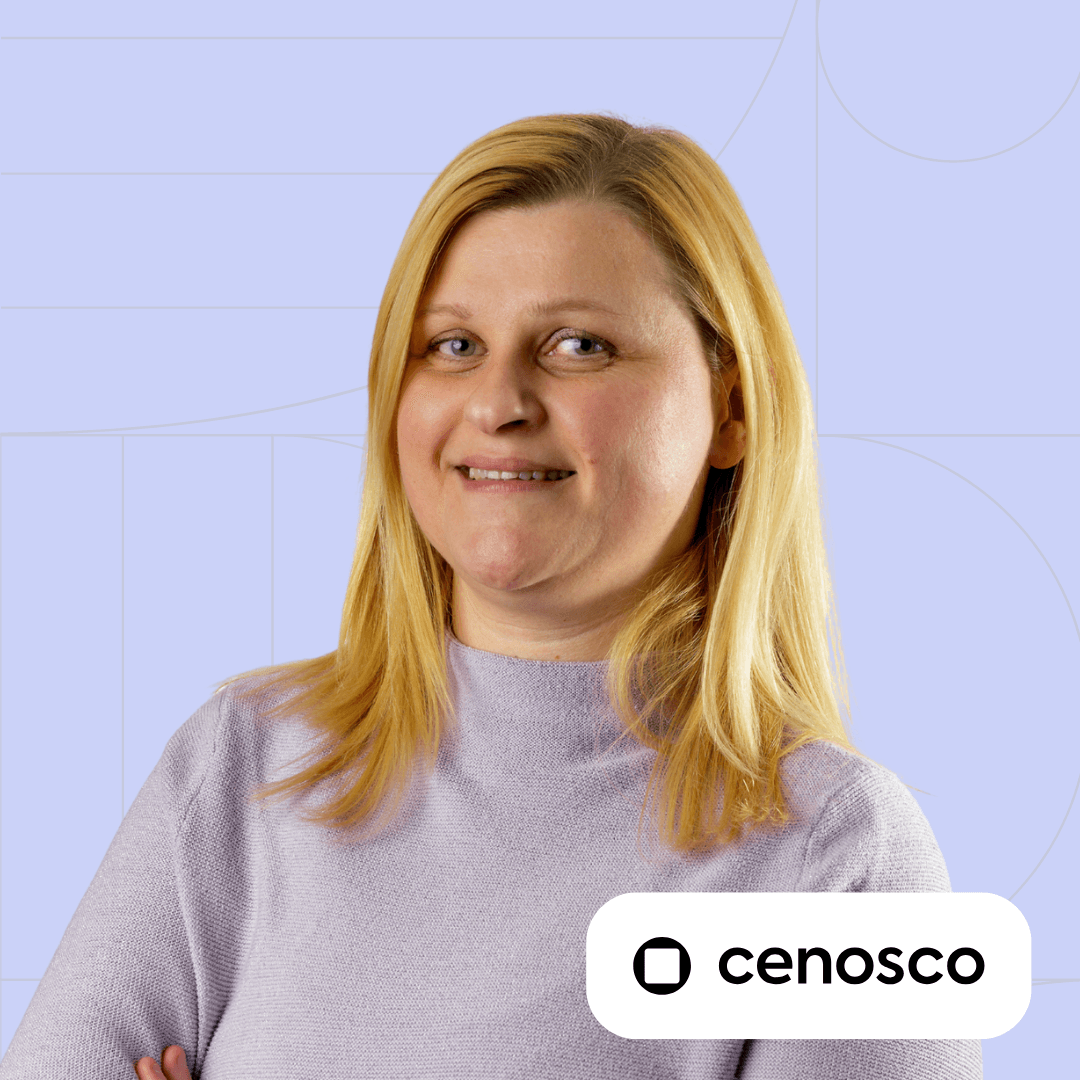
Denis Tkalec Technical writer
Denis Tkalec is a technical writer at Cenosco, specializing in asset integrity management software since 2022. With a background in education and six years in marketing, she turns complex topics into clear, user-friendly content. Inspired by Camus’s belief that “a writer keeps civilization from destroying itself,” she brings precision and care to every manual.