Industries that rely on metal equipment and infrastructure, such as refineries and process plants, face a significant concern: corrosion. While corrosion itself is widely recognized, there is a specific type that often slips under the radar – Corrosion Under Insulation (CUI). This insidious form of corrosion quietly takes place beneath insulation materials, making it a challenging adversary to detect and mitigate. In fact, did you know that, according to a study by ExxonMobil in 2003, CUI accounts for a staggering 40-60% of piping maintenance costs?
In this blog, we will explore the underlying mechanisms of CUI and consider how Risk-Based Inspection (RBI) analyses should be conducted to estimate the associated risk of CUI to effectively manage this degradation mechanism.
Let’s start by defining exactly what Corrosion Under Insulation (CUI) is.
Corrosion Under Insulation (CUI) Definition
Corrosion under insulation (CUI) is a serious type of localized external corrosion that affects carbon and low alloy steel equipment. It occurs when water enters external insulation through holes or gaps in the insulation covering, or when moisture in the air condenses on the metal surface below the insulation (known as sweating). For this reason, CUI is commonly observed in refineries and process plants where high temperatures cause thermal cycling.
If any good quality protective coating is not present, significant wall loss (corrosion) can occur.
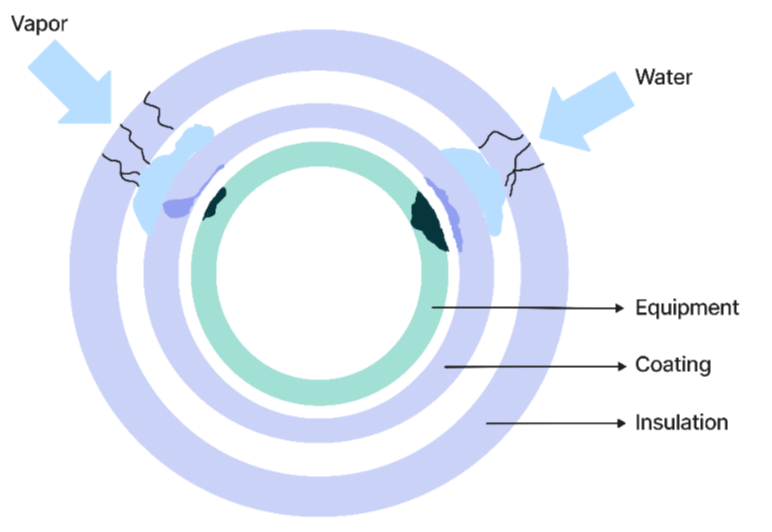
Figure 1: In the image you can see the equipment, coating, and insulation. The arrows indicate how water and vapor enters through cracks in the insulation and causes CUI.
The often random and localized nature of the attack, and the fact that it is hidden under the insulation, makes CUI difficult to detect.
But why do we need insulation in the first place, when it causes CUI to occur?
The need for insulation
Despite the risk of CUI, insulation serves a crucial purpose that outweighs its potential drawbacks. Insulation is necessary to protect underlying materials, typically steel, from the detrimental effects of environmental conditions. The benefits of insulation in terms of thermal efficiency, energy conservation, and personnel protection make it an essential component in many industrial applications. Proper insulation design, material selection, and maintenance practices can help minimize the occurrence of CUI and ensure the overall effectiveness of insulation systems.
So, we already know that insulation influences CUI occurrence, but there are more mechanisms playing a role…
Mechanisms influencing Corrosion Under Insulation (CUI)
Javaherdashti identified five key factors that significantly impact CUI:
- Insulation material
- Coating material
- Equipment (component) material
- Atmosphere (Environment)
- Design
Inspections play a vital role in the early detection and management of CUI. To ensure successful inspection management, it is important to have a comprehensive understanding of the mechanisms influencing CUI, as this knowledge guides the timing and approach of inspections.
Let’s focus some more on inspection strategy and see how each of these key factors can influence the inspection priorities based on the risk of failure. For this, we first need to dive into Risk-Based Inspections (RBI).
Risk-Based Inspections (RBI)
Risk-Based Inspection (RBI) methodologies can be used to effectively mitigate the risk of CUI. Basically, equipment components have protective barriers, like insulation and coating, that we want to inspect. RBI is a proactive approach that prioritizes inspections based on the risk of barrier failure. These analyses occur at the component level, focusing on specific degradation mechanisms like CUI. In simple terms, the RBI process involves:
- Identifying the most plausible failure scenario
- Reviewing the inspection history
- Estimating the remaining life when age-related degradation is present
- Determining the susceptibility to failure (StF), which quantifies the probability
- Assessing the consequences of failure (CoF) for the most plausible failure scenario
The ratings of susceptibility to failure and consequences of failure are used to assess the overall criticality or risk. This criticality, along with the remaining life, is then used to determine the next inspection date and, in certain instances, an appropriate inspection strategy.
Applying RBI for Corrosion Under Insulation (CUI)
Let us now consider the five key factors influencing CUI and explore their impact on Risk-Based Inspection (RBI) analyses.
Insulation material
Insulation is often the secondary barrier against corrosion. Factors such as its age, condition, and material type are crucial as they affect its ability to retain or drain water.
In terms of RBI, the insulation material’s impact on susceptibility to failure should be taken into account.
Coating material
To ensure added protection, it is highly recommended to apply coatings beneath the insulation. In addition to a CUI-resistant coating, especially at high temperatures, cathodic protection (CP) is advised. Coating is the primary barrier against corrosion.
It is important to note here that RBI should take the remaining coating life into account, as this can allow for an extension of the equipment’s next inspection date.
Equipment (component) material
Corrosion Under Insulation (CUI) can impact carbon and low alloy steels within the temperature range of -12°C to 175°C (10°F to 350°F). It also affects austenitic stainless steels and duplex stainless steels at temperatures between 60°C and 205°C (140°F and 400°F).
Remaining life can typically be determined for carbon and low alloy steels. However, when it comes to austenitic and duplex stainless steels, CUI appears as external Chloride Stress Corrosion Cracking (Cl-SCC) at higher temperatures (beyond the metal wall temperature threshold). In such cases, determining the remaining life of the components is not feasible.
As a result, the approach for Risk-Based Inspection (RBI) in relation to CUI varies based on the equipment material and operating temperature.
Atmosphere (Environment)
The atmosphere plays a vital role in CUI by providing the necessary water for corrosion. This can come from natural sources like rainfall, seawater spray, and groundwater, as well as industrial factors such as cooling tower drift and process liquid spillage. Additionally, corrosive substances like chlorides and sulphates found in the atmosphere contribute to CUI, particularly in marine or coastal environments and industrial settings like refineries and chemical plants.
The type of atmosphere should therefore be considered during the RBI when the susceptibility to failure is determined.
Design
Design includes both equipment design and plant layout and it has the potential to eliminate the need for insulation entirely by providing protection against harsh environments and maintaining temperatures below a critical threshold. However, if insulation is still necessary, the complexities of design, such as shape and attachments, can make it challenging to apply insulation effectively.
So, design plays a vital role in either preventing CUI entirely or reducing its effects resulting from the four factors mentioned earlier. Consequently, design really influences RBI indirectly through these other four factors.
IMS guides you through Risk-Based Inspection analyses
Given the complexity involved in accurately assessing the risk associated with CUI, having guidance can be immensely helpful. IMS PEI serves as a valuable resource, providing step-by-step guidance for conducting the Risk-Based Inspection (RBI) analysis. It considers factors such as degradation mechanisms, equipment/component type, and material to determine the most suitable RBI approach.
IMS PEI offers a range of tools adopted for Corrosion Under Insulation (CUI), including a susceptibility to failure questionnaire, CUI corrosion rate calculator, coating life estimation, criticality lookup based on susceptibility to failure and consequences of failure, maximum inspection interval lookup based on criticality, and inspection strategy lookup based on criticality. The inspection strategy defines the scope of inspection coverage. The selection of the appropriate CUI RBI approach is influenced by the component material and operating temperature.
In the same way, IMS PEI will serve as your reliable companion, guiding you through RBI analyses for all your other component-degradation mechanism combinations. With its assistance, you can confidently assess the associated risks accurately without getting overwhelmed by the intricacies.
Would you like to learn more about IMS PEI and RBI?
Fill out the form below to get in touch with us and find out more.
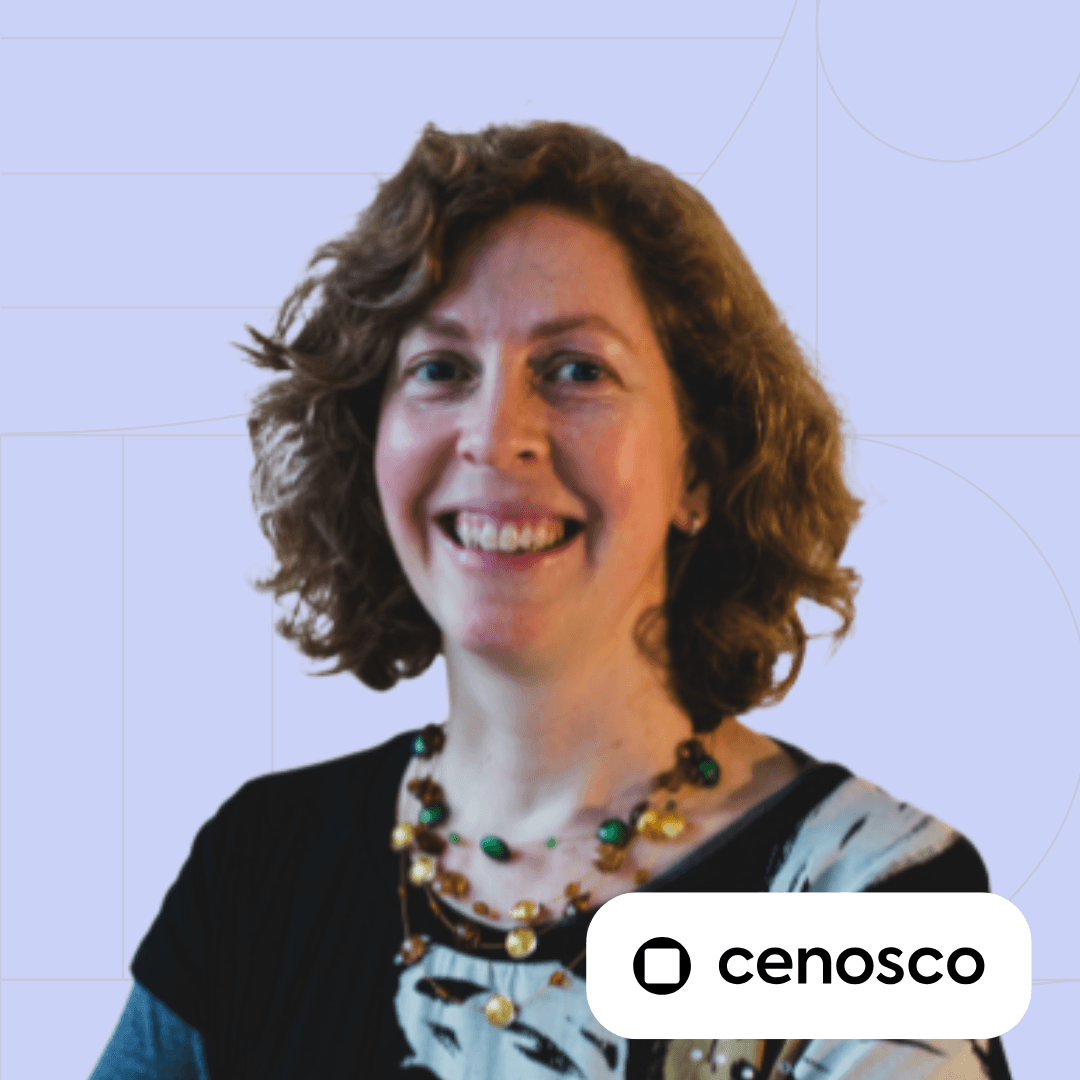
Elsa Tolsma-de Klerk Technical Writer
Elsa is an engineer with a passion for sharing knowledge. She holds a Master’s in Electronic Engineering and spent over a decade at Sasol as an Advanced Process Control Engineer, where she gained hands-on experience in optimization, control systems, and writing technical documentation. Since 2019, she’s been a Technical Writer at Cenosco, now leading the IMS knowledge base and training Academy team.