Pipeline Corrosion occurs when a pipeline’s material begins to deteriorate or weaken over time due to chemical reactions with its surroundings.
Corrosion is a significant challenge faced by industries that use process equipment and pipelines. Failure to manage corrosion can lead to leaks, explosions, and costly downtime.
According to a study conducted by NACE International, the global cost of corrosion was estimated to be $2.5 trillion, or over 3 percent of the global GDP in 2013. Therefore, understanding and managing corrosion can help save millions of dollars in reduced capital costs and reduced downtime.
What is Pipeline Corrosion, and what causes it?
Corrosion of pipelines, pipes, or really any corrosion is, simply stated, the degradation of metals into more chemically stable oxides through interaction with their surroundings. In the case of process piping and pipelines, we are most often concerned with the fluids carried by the pipe.
Various processes can cause and contribute to corrosion:
- Chemical reactions: Interactions with the fluid being transported through pipes with chemicals in the environment can cause corrosion. For example, oxygen, carbon dioxide, hydrogen sulfide, and organic acids carried in process fluids can all lead to corrosion, as can contact with seawater or corrosive soils.
- Microbial corrosion: Certain bacteria in process fluids can produce acids that lead to pipeline corrosion.
- Abrasion: Particles or fluids flowing through pipelines can abrade the pipelines and lead to pipeline corrosion.
- Electrochemical reactions: When different types of metals are in contact with each other electrochemical reactions can occur, leading to corrosion.
- Lack of maintenance: Failure to maintain pipelines can also contribute to pipeline corrosion.
How can corrosion be managed?
Managing pipeline corrosion requires a well-informed approach, and many of the processes that cause corrosion can be modeled to produce estimates of corrosion rates.
Understanding the processes that lead to corrosion allows for the development of preventative maintenance programs to manage corrosion. A number of factors should be considered in any corrosion mitigation strategy:
- Materials Selection: Pipelines, wells, and other process equipment can be designed and constructed from various alloys, with or without protective pipe coatings. The cost of each variety of pipe can vary widely, and selecting appropriate materials can impact project viability.
- Corrosion Inhibitors: These chemicals can be added to the fluids carried in pipelines to lower corrosion rates.
- Pipe Coatings: Protective coatings, such as cement or epoxy coatings, can be applied to pipes to help prevent pipeline corrosion.
- Inspection and Monitoring: Process equipment can be inspected using nondestructive testing, visual observations, or material sampling to identify corrosion rates. Corrosion models can be calibrated using real-life observations to optimize future inspection schedules and prevent unexpected downtime.
- Scheduled Maintenance: Appropriately scheduled cleaning and maintenance of pipelines can help prevent corrosion. Activities such as pigging pipelines to remove built-up debris and the application of film-forming corrosion inhibitors can significantly reduce pipeline or pipe corrosion rates and increase equipment lifespan.
However, the first step in the mitigating strategy should always be to start predicting the internal pipe corrosion rates.
How can Pipeline Corrosion be predicted?
Basic predictive models should account for CO2 corrosion, H2S corrosion, organic acid corrosion, O2 corrosion, and microbiologically induced corrosion in predicting internal pipeline corrosion.
More advanced corrosion models are able to model the following processes:
- Water chemistry is based on released Fe2+ from corrosion.
- Multiphase flow.
- Temperature gradients.
- Water/alcohol phase distribution and condensation.
- Organic acid partitioning in water/gas/oil phases.
- Top of Line Corrosion.
Optimize your inspection schedules for internal and external corrosion
Cenosco’s IMS PLSS is a comprehensive pipeline integrity management system that helps optimize operations and enhance pipeline safety. With features like anomaly management, scenario assessment, and corrosion management, IMS PLSS enables proactive maintenance, risk assessment, and efficient decision-making. It integrates seamlessly with ERP systems, offers real-time monitoring, and provides advanced tools like 2D/3D visualization and traffic light indicators. Cloud-based and mobile-friendly, IMS PLSS ensures streamlined pipeline management, boosting asset performance and compliance while reducing downtime and inspection costs.
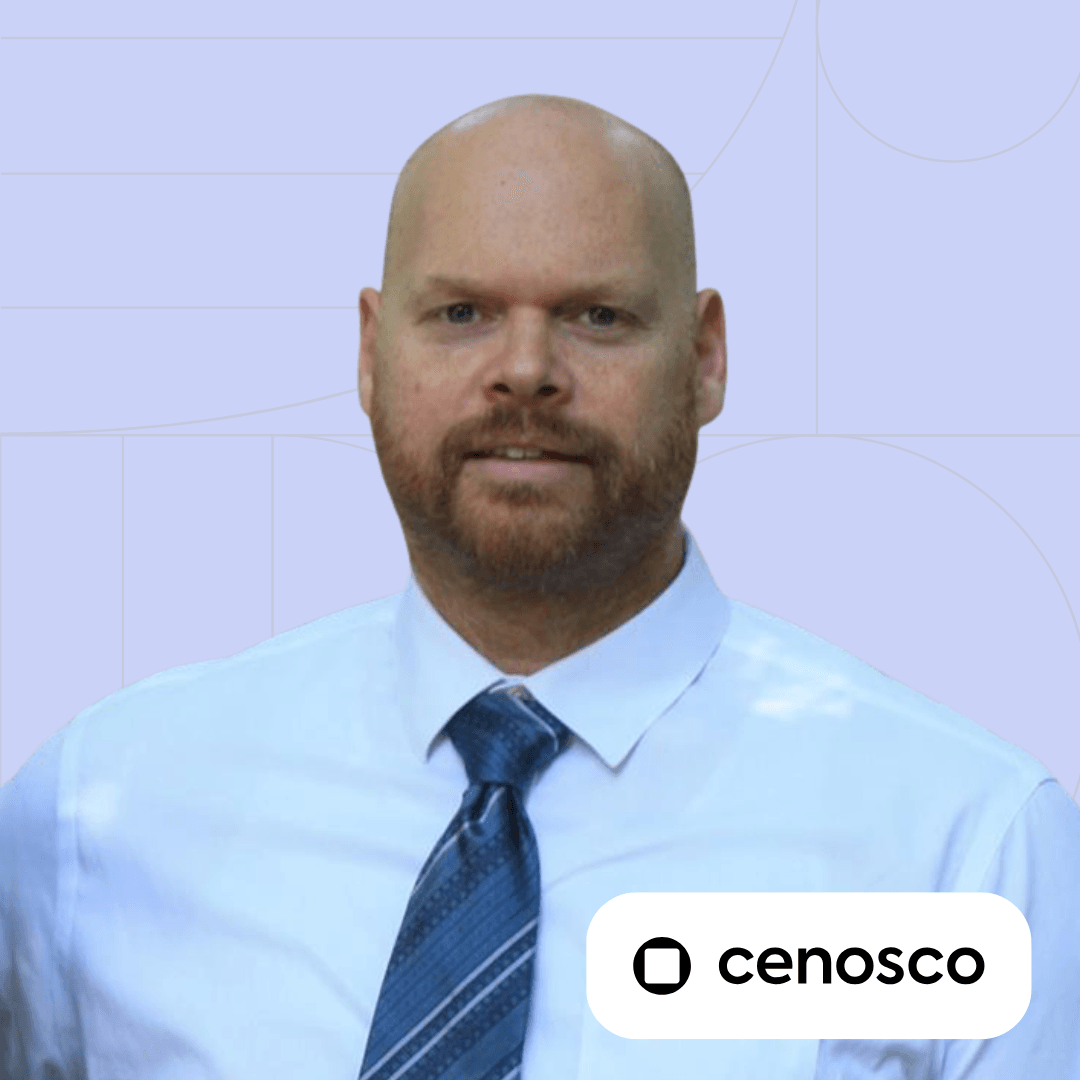
Tomislav Renić Technical Writer
Tomislav is an experienced engineer and technical communicator with over 20 years in complex systems, modeling, and project management. As a Technical Writer at Cenosco, he translates engineering concepts into clear, user-friendly documentation for software in the oil, gas, and refining industries.