Field inspection software offers a modern solution to streamline and simplify your inspection tasks. The current state of field operations often involves outdated processes. Typically, conducting an inspection, test, or maintenance from planning to completion includes several manual steps such as printing forms, filling them out, scanning documents, and then validating them. Despite technological advances, many inspection departments still rely on these traditional methods. This is true for various types of inspections, including visual inspections and non-destructive testing. The persistence of these methods highlights the need for modern solutions to streamline and simplify field operations. This is where Field Inspection Software can play a significant role in streaming and simplifying field operations.
Field Inspection Pain Points
The common pain points encountered throughout the process of field operations include:
Paper Forms
In the traditional approach to field inspections, inspectors often rely on printed or copied forms for documentation purposes. These paper forms, while serving their purpose, present several limitations. Firstly, they lack interactivity, meaning they cannot adapt or respond to the input provided by inspectors in real time. Additionally, they often fail to present historical data in a meaningful way, making it challenging for inspectors to track trends or make informed decisions based on past information. Moreover, these forms cannot validate input or provide guidance to field staff based on the measurements collected during inspections. As a result, inspectors may encounter difficulties in ensuring the accuracy and completeness of their documentation, leading to potential discrepancies and inefficiencies in the inspection process.
Data entry
Following the completion of inspections or maintenance activities using paper forms, the next step typically involves manually transcribing the collected data into the company’s asset integrity management system. This process of data entry introduces a significant risk of errors and inefficiencies. Human error, such as mistyped values or incomplete entries, can compromise the integrity of the data and undermine the reliability of subsequent analyses or decisions. Moreover, the time-consuming nature of manual data entry can delay the availability of critical information, impeding timely decision-making and potentially leading to missed opportunities or increased operational risks. Overall, the reliance on manual data entry processes represents a notable pain point in the field testing workflow, highlighting the need for more efficient and accurate data management solutions.
Lack of connectivity in the field
Many field sites, particularly in remote or challenging environments, suffer from a lack of wireless network access. This limited connectivity restricts field staff’s ability to collaborate effectively, access essential databases, or utilize online resources while performing inspections or maintenance activities. As a result, field teams may encounter difficulties in communicating with colleagues or accessing relevant information to support their work. This lack of connectivity not only hampers productivity but also compromises safety and decision-making processes. Without access to real-time data or communication channels, field staff may struggle to address emerging issues promptly or coordinate effectively with other stakeholders, potentially exacerbating operational risks or delays. Therefore, addressing the connectivity challenges in the field is crucial for improving the overall efficiency and effectiveness of field-testing operations.
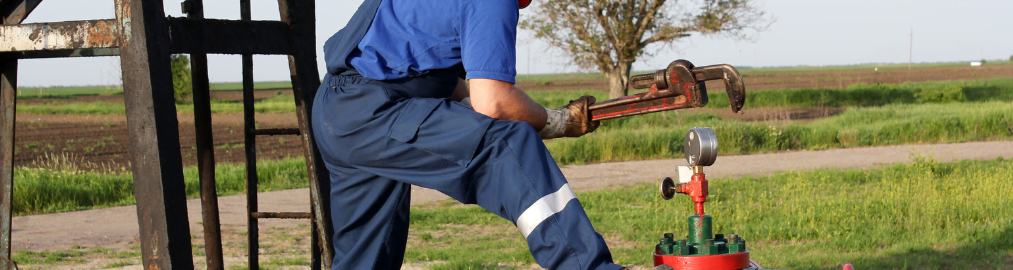
The benefits of Field Inspection Software
Transitioning to a digital solution for collecting field data offers several potential benefits, which will serve to relieve the pain points listed above. For example, transitioning from paper forms to digital alternatives provides flexibility, interactivity, and seamless data synchronization with asset management databases, ensuring real-time access to accurate information. This real-time synchronization enables comprehensive analysis by accessing historical data, helping identify trends and evaluate equipment performance effectively. Essentially illuminating the difficulties brought on by paper forms and manual data entry.
Moreover, digital tools enhance field inspections through offline capabilities on mobile devices, allowing necessary information to be preloaded for offline work regardless of network connectivity. Dynamic checklists and logic validation guide field workers through inspection processes, ensuring data completeness and accuracy. This transition not only improves operational efficiency but also enhances data reliability and accessibility. These capabilities will help your operations overcome the issues caused by the lack of connectivity in the field.
The value yielded by these benefits include:
1. Improving Safety
Accessing historical data allows field workers to identify potential leaks or failures early, mitigating risks before they escalate. Responsive checklists can automatically flag issues and guide field workers to complete appropriate tests and measurements, reducing the need for additional site visits.
2. Enhancing Regulatory Compliance
A comprehensive digital solution can document all necessary information for regulatory compliance, including equipment condition histories, corrective action reports, and service records.
3. Maximizing Return on Investment (ROI)
By efficiently flagging equipment issues, inspection and maintenance planners can allocate limited funds to maximize uptime and reduce unexpected downtime. Time savings from eliminating data re-entry tasks allow field workers to focus on completing field work, increasing overall productivity.
Why are outdated methods still used in Field Inspections?
Moving to a digital future for field data collection offers numerous benefits, but it also presents several potential barriers to implementation:
- Resistance to Change: Transitioning from pen and paper to a digital model may face resistance from employees accustomed to traditional methods. Overcoming this resistance requires guidance, training, and end-user inclusion to facilitate the adoption of new workflows within the digital infrastructure. A good software supplier would provide proper user enablement through training.
- Integration Challenges: Implementing a digital model for testing, inspection, and data collection necessitates fitting it into existing company processes and IT infrastructure. This integration process requires careful planning and consideration to ensure seamless operation and compatibility with established workflows. When selecting a field inspection software supplier, it’s important to consider their implementation capabilities, as these will facilitate the implementation process.
- Time Constraints: Creating digital checklists, implementing changes across the organization, and accruing benefits from the transition to digital may take time. High turnover rates in inspection companies and the need to adapt data collection procedures further contribute to implementation challenges.
- Cost Considerations: The costs associated with re-training staff, purchasing mobile devices for field operators, and investing in software pose financial challenges. Additionally, changes to workflow and data collection procedures may require significant investment.
Despite these barriers, the industry is eager to digitize, with both technology and industry readiness. Leadership plays a crucial role in driving the decision to implement digital systems. However, it is clear that given the benefits yielded from the change, overcoming these obstacles is key, and the right software provider will always be readily available to help facilitate the process.
Why you should use Field Inspection Software
Transitioning from pen and paper to a true digital model for data collection is essential for any serious organization. The old method, while effective, lacks the efficiency and effectiveness achievable with digital solutions. By migrating to digital solutions, organizations can ensure regulatory compliance, improve safety, and maximize the return on investment in their facilities.
The Leading Field Inspection Software: IMS4Field
IMS4Field offers a practical solution to enhance field data collection practices. This platform addresses common challenges in traditional paper-based methods, providing seamless data synchronization and dynamic checklist capabilities. With IMS4Field, organizations can streamline inspections, ensure data accuracy, and meet regulatory standards effortlessly. By facilitating the transition to digital workflows, IMS4Field empowers organizations to improve safety, optimize efficiency, and maximize ROI across their facilities.
Why IMS4Field?
- Transition from Paper Forms to Digital Alternatives: Digital forms offer flexibility, interactivity, and seamless data synchronization with asset management databases.
- Seamless Data Synchronization: Ensuring real-time access to accurate information by seamlessly synchronizing field data with asset integrity management databases.
- Access to Historical Data: Analyzing equipment performance and identifying trends by accessing historical test results and failure mechanisms.
- Offline Capabilities on Mobile Devices: Preloading necessary information for inspections to enable offline work on mobile devices, regardless of network connectivity.
- Dynamic Checklists and Logic Validation: Guiding field workers through inspection processes with dynamic checklists and logic validation mechanisms to ensure data completeness and accuracy.
IMS4Field Demo
Want to see IMS4Field in action? Fill out the form to get started with the demo.
Connect with us on LinkedIn