An Inspection Data Management System (IDMS) is software that brings together all the data related to various inspections of a refinery’s or plant’s fixed equipment. If you work in the oil and gas or chemical processing industry, you know that the sheer amount of data generated daily is large. Fixed equipment like piping, pressure vessels, heat exchangers, boilers, and storage tanks work under extreme operating conditions and are, therefore, more prone to failure. For that reason, it is especially critical to keep a close eye on them. This means that each piece of equipment has its own set of data points, such as inspection reports, installation and replacement dates, and FFS (Fitness For Service) assessments that you need to track and update continuously. Keeping up with all that data is no easy feat. On those grounds, the best advice we can give you is to get an Inspection Data Management System that follows the needs of your company, industry, and legislation standards. In this article, we discuss how an Inspection Data Management System can help you manage your equipment inspection data.
Two essential functions of IDMS
By employing an Inspection Data Management System, you will transform the way you manage inspection data for fixed equipment. The two primary functions of any such system are to help you:
- Create and keep track of equipment inspection schedules using time or risk-based methods.
- Record the results of each inspection.
Additionally, most IDMS systems today will also allow you to prioritize and optimize inspection activities with Risk Based Inspection (RBI) as well as directly create follow-up actions from the inspection finding records.
So, not only will the IDMS help you store the data, but it will make the inspections and data capturing more consistent and, therefore easier to analyze. Let us dive deeper into the two primary IDMS functionalities.
Scheduling inspections with Inspection Data Management Systems
Inspection Data Management Systems allow you to create Inspection schedules on which you will be able to write down when and what you need to inspect as well as what activities you need to perform. Scheduled activities may include an external visual inspection, taking wall thickness readings, repairs, and more.
Most Inspection Data Management Systems follow the American Petroleum Institute’s (APIs) inspection codes. That is why their scheduling processes can be similar. This means that they have the functionalities needed to set up inspections as outlined in API 510 for pressure vessels, API 570 for piping, and API 653 for storage tanks. These codes require that you inspect your equipment at a fixed interval or part of the remaining life, whichever is lower. With IDMS you can rest assured that your assets’ inspections follow legislation and industry standards.
Despite following the APIs, the way that each IDMS calculates the remnant life and corrosion rate may vary. For example, the API codes require you to calculate the remnant life by dividing the excess wall thickness (obtained by subtracting the minimum thickness from the actual thickness) by the corrosion rate. You must use the exact measurements to figure out the exact thickness but setting up the minimum thickness and corrosion rate allows for some variation. For that reason, when selecting the Inspection Data Management System, make sure that the one you chose matches the philosophy of your company.
Tracking the Results of the Inspection
Once you have completed your inspections, you will have to organize and record a bunch of data. The fact that the industry uses more than a hundred inspection methods does not make that task any easier. An IDMS can track the results of these techniques with varying degrees of complexity. Moreover, if left to their own devices, different people will enter inspection data differently, making it harder to manage and analyze.
An Inspection Data management system will help the data recording process as much as possible by allowing you to:
- Build custom inspection checklists that will help you capture the data in a consistent way,
- Add the captured data in an uploaded document, and
- Describe your findings in a textual form.
As every company’s data collection method and final requirements are different, we recommend that you choose an Inspection Data Management System that allows customizations.
IMS integrated IDMS for a more efficient inspection data management
Having easy and effective access to all the inspection data can help you make smart decisions about your operating asset maintenance (think safety for personnel and the environment!) and keep everything running smoothly. Consequentially, it can help you achieve more profitable outcomes.
In this respect, the Inspection Data Management System integrated into the IMS software is your smart friend to get the most out of the endless bits and pieces of data. This nifty, integrated solution takes the hassle out of inspection planning and recording. It will untangle the entire process of handling data and make it more efficient. With it, you can schedule and track inspection tasks, collect and keep inspection results, and even enjoy the benefits of Risk-Based Inspection (RBI) as well as schedule corrective actions.
At Cenosco, we recognize that the prime purpose of inspection data management is to make informed decisions about operating equipment. To that end, IMS offers a Schedule Dashboard which displays all pertinent inspection data from your equipment for more efficient decision-making.
Interested in getting an Inspection data management system for your company? Fill in the form below to get a demo now!
See IMS in Action
Unlock the power of IMS, starting by filling out the form below.
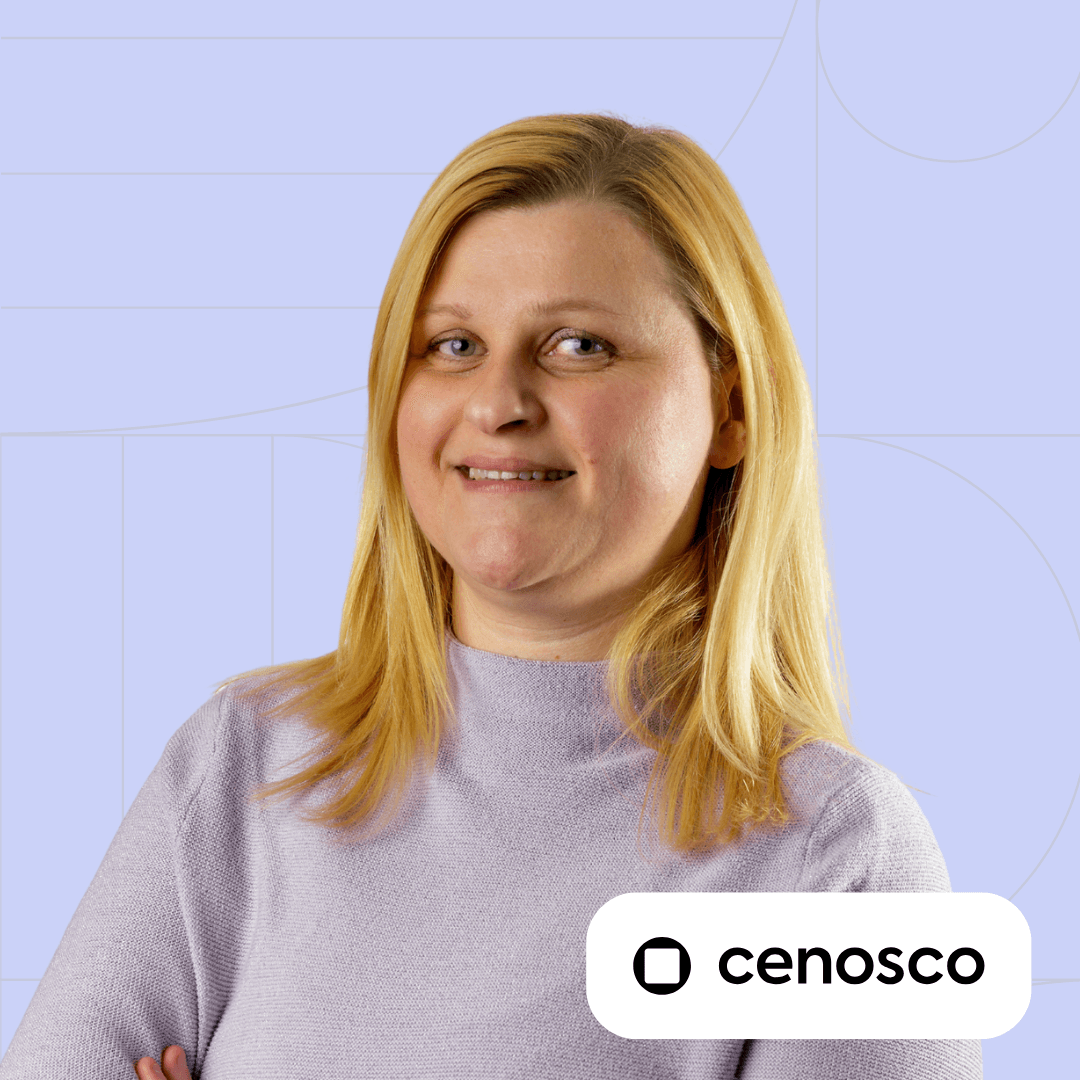
Denis Tkalec Technical writer
Denis Tkalec is a technical writer at Cenosco, specializing in asset integrity management software since 2022. With a background in education and six years in marketing, she turns complex topics into clear, user-friendly content. Inspired by Camus’s belief that “a writer keeps civilization from destroying itself,” she brings precision and care to every manual.