Barrier Management is a practice that has become particularly important in the oil and gas sectors due to its role in identifying, assessing, and mitigating risks associated with pipeline operations.
A report by GlobalData shows that by the end of 2021, there were over 4,785 active and suspended oil and gas pipelines. This demonstrates not only a rise in demand for oil and gas but also a surge in interest in risk analysis and system reliability in the Oil & Gas industry.
In this article, we explore what barrier management and safety barriers are. It discusses how they can be used to secure pipelines from potential risks and pipeline integrity threats.
Why is barrier management important in preventing pipeline failure?
Managing pipeline corrosion is a difficult challenge, as offshore and inland pipelines must be protected from the corrosive effects of the environment and the fluids that flow within them. Different installation processes, variations in pipeline diameter and thickness, and aging of hardware and materials can all contribute to the risk of pipeline damage and leaks.
These types of pipeline failures can have devastating consequences, including environmental damage, social disruption, and economic loss. To protect people, operations, and the environment from any potential leaks, safety systems must be effectively implemented to prevent threats from causing major accidents. That is exactly the focus of barrier management.
What is barrier management?
The Petroleum Safety Authority Norway (PSA) defines barrier management as “Coordinated activities for establishing and maintaining barriers so that they fulfill their functions at all times.“ To be precise, barrier management is a system for selecting and designing barriers to protect against risks and monitoring and maintaining them to ensure the safety and reliability of an asset throughout its lifecycle.
When designing barriers, the failure, hazard, and accident scenarios must be thoroughly evaluated to identify situations where each barrier has a role to play. Each threat should have at least one primary barrier that is highly effective and a system to monitor its health and effectiveness.
Secondary barriers may be used to provide mitigation if needed. For example, to control the degradation rate to an acceptable level. As every plant, facility area, or operation will have a unique risk profile, barrier management will differ accordingly. With a clear understanding of barriers and monitoring of their status in daily operations, major accidents can be avoided and lives saved.
What are safety barriers?
Safety barriers are planned measures that provide protection in the event of failure, danger, or accidents and mitigate the consequences caused by these events. They are established to prevent the occurrence of threats from leading to a major accident.
A barrier can be a device, such as a sensor, or a human intervention, like an alarm with operator action. It can also be a limitation on a contributing factor, including an increase in pressure. The selection of barriers will vary according to the type of failure, hazard, or accident that needs to be addressed. The purpose of safety barriers is to perform one or more safety functions.
For safety barriers to be effective, they must be able to carry out their barrier function. This includes going through the steps of a defensive response:
- Detecting a deviation
- Figuring out the necessary defensive action
- Carrying out defensive action
But barriers degrade in service. For that reason, every barrier needs to be monitored and verified regularly. Otherwise, it can become ineffective, and unless suitable remedial actions are taken, the risk level will rise.
Red-yellow-green (RYG) indicators are a common system used in barrier management to assess the effectiveness of barriers. The system uses three colors – red, yellow, and green – to indicate the status of a barrier.
- Red: Barrier not in place or not effective (Barrier absent)
- Yellow: Barrier is performing as expected but needs monitoring
- Green: Barrier in place and healthy (Barrier fully present)
This system is used to ensure that risks and threats are identified and managed in a timely and efficient manner.
What are the key elements of safety barriers?
A safety barrier is formed by technical, operational, and/or organizational barrier elements necessary for the individual barrier to be effective, which together realize the barrier function. In certain cases, the barrier is only formed by technical elements. Let us explain each of the terms mentioned above.
Technical barrier elements refer to the tools and systems that create a barrier function, like pipeline condition monitoring sensors. Operational barrier elements involve the processes and activities that personnel must carry out to form a barrier function, for example, the response of the personnel to an alarm.
Finally, organizational barrier elements comprise personnel with specific roles and competencies responsible for realizing the barrier function, including the competence assurance process.
What types of safety barriers are there?
Barrier management involves the use of several types of barriers:
- Mechanical barriers include material selection or design detailing such as corrosion allowance, resistant material, slope, and no crevice.
- Design barriers involve coating or liners such as external coating, non-metallic liner, and cathodic protection such as impressed current and sacrificial anodes.
- Process control barriers include process control such as dewpoint, flow, temperature, and solids.
- Chemical treatment barriers such as inhibitor injection and BFW oxygen scavenger.
What does Swiss cheese have to do with barrier management?
The Swiss cheese model is a way of understanding how safety hazards arise and how to prevent them. In this model, each slice of cheese represents a safety barrier or precaution relevant to a particular hazard. Absent or failed barriers on each slice are represented as holes in the Swiss cheese.
For example, a pipeline may have physical barriers like fences and locks, as well as administrative barriers like operating procedures and regulations. When the holes in these slices of cheese line up, an accident can occur.
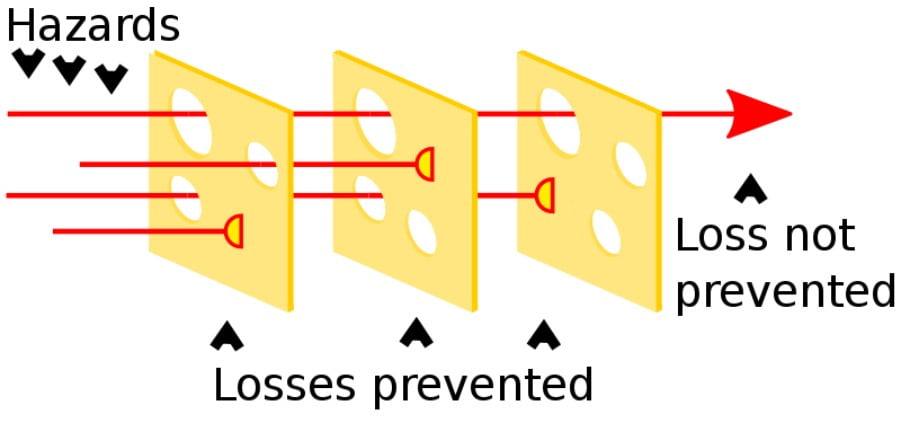
Image source: Wikipedia – https://creativecommons.org/licenses/by-sa/4.0/deed.en
Therefore, it is important to ensure that each barrier is well-maintained and effective and that any gaps are identified and addressed. Applied to the pipeline barrier management process, the Swiss cheese model helps identify the potential weak points in the system and additional controls or changes that can be made to reduce the risk of pipeline failure.
Barrier management in pipelines is an important part of managing risk. The Swiss cheese model can be used to ensure that all layers of safety are in place and working properly.
IMS PLSS: powerful barrier management solution for pipelines
IMS PLSS (Pipeline and Subsea Systems) is a pipeline integrity management software that enables you to make the most of your pipeline data. It provides a powerful barrier management solution that helps you quickly and accurately analyze that data to identify potential problems.
Based on the Swiss cheese model, IMS PLSS allows you to select the failure scenario for each piece of equipment. To protect your equipment against these risks, you can then choose barriers according to the potential cause of failure. You can also define an indicator used to infer the barrier’s effectiveness.
To provide a more comprehensive assessment of the barriers’ performance, in addition to the basic RYG system IMS PLSS uses two more colors to indicate the status of the barrier – amber and blue.
Check the table below to discover the meaning of each barrier status color in the IMS PLSS.
- Green: Barrier in place and healthy (Barrier fully present)
- Amber: Barrier in place but compromised or partly effective (Barrier partly absent)
- Red: Barrier not in place or not effective (Barrier absent)
- Yellow: The actual Barrier status, based on the indicators, is Amber/Red, but actions are defined to return the status to Green
- Blue: The Barrier’s status is unknown, i.e., no Indicators available (typically the case for a newly defined Barrier)
When you know the status of your barrier, you can apply that data to make informed decisions regarding the operation and maintenance of the pipeline, which will help to ensure reliable, safe, and efficient operations.
Additionally, IMS PLSS enables you to schedule responsive action based on data analysis, allowing you to take proactive steps to address any potential issues before they become a problem.
With IMS PLSS, you can upgrade your inspection schedules from time-based to risk-based. This will refine your pipeline maintenance strategy and achieve optimal inspection costs and improved safety.
Cenosco is an asset integrity management software company with over 20 years of product leadership in asset-heavy industries.
Their IMS Suite of solutions was designed to support users in making smart inspection and maintenance decisions to increase safety, asset availability, and lowering asset management costs. It is currently utilized to safeguard several hundred assets in over 50 countries. The IMS Suite was created in collaboration with world-renowned Oil & Gas leader Shell.
Ready for a sneak peek of our IMS PLSS tool?
Fill out the form below to get a demo now!
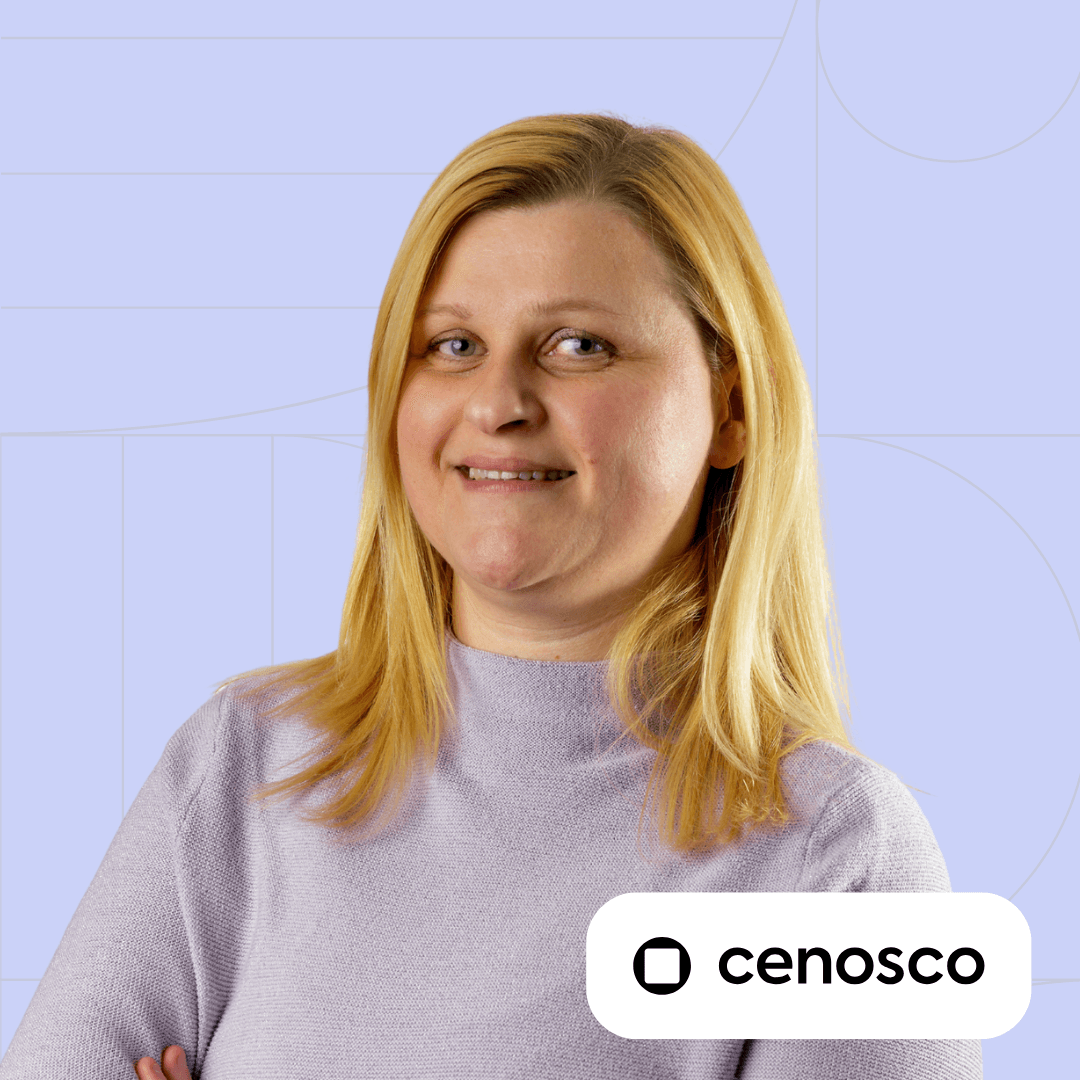
Denis Tkalec Technical writer
Denis Tkalec is a technical writer at Cenosco, specializing in asset integrity management software since 2022. With a background in education and six years in marketing, she turns complex topics into clear, user-friendly content. Inspired by Camus’s belief that “a writer keeps civilization from destroying itself,” she brings precision and care to every manual.