Consider this staggering fact: there are approximately 2.13 million kilometers of pipelines globally, moving vital resources such as crude oil, refined petroleum, natural gas, and natural gas liquid.
However, just like any other infrastructure, pipelines deteriorate as they age which raises significant concerns about pipeline integrity and the potential damage that could result from failures. Even minor incidents can have catastrophic effects on ecosystems, jeopardize community safety, and harm the economies that rely on these pipelines. This is why we need to strive to minimize the chances of leaks, and we need to operate and maintain pipelines correctly and diligently.
In this light, pipeline integrity takes center stage: it ensures that pipelines—typically made from durable materials like steel—can operate without failure, ensuring the safe transport of the liquid inside.
In this article, we will explore the concept of pipeline integrity, examine its importance, and discuss best practices for maintaining it.
What is Pipeline Integrity?
Pipeline integrity refers to the overall condition and quality of pipelines and their components. It protects the pipeline by ensuring it is free from defects or damage, operates efficiently, and minimizes the impact in the event of a leak. In simpler terms, pipeline integrity safeguards the pipeline, making sure all its parts are working correctly, and no harmful substances escape from it.
Safeguarding pipeline Integrity includes various stages throughout a pipeline’s life cycle, including design, manufacturing, installation, operation, maintenance, and eventual decommissioning. To protect this integrity, it’s important to follow safe practices based on established standards and use strong industrial technologies for prevention, detection, and mitigation.
- Prevention involves actions and solutions aimed at stopping leaks before they happen. This is achieved through careful design, construction, operation, maintenance, training, and education.
- Detection includes methods that help pipeline operators quickly find out if a leak has occurred or is about to occur.
- Mitigation focuses on reducing the amount of material released and minimizing any damage caused by the leak. This deals with:
- Predicting the likelihood and potential location of a leak.
- Estimating the amount of material that could be released.
- Implementing measures to curtail the impact of the leak, such as closing the pipeline, deploying warning signs to prevent third-party damage, and dispatching maintenance teams to address the issue.
- Ensuring inherently safe pipeline design and operation to prevent leaks from occurring in the first place.
In turn, regulators closely monitor pipeline projects to ensure compliance and safety standards are consistently met. This stresses the need for diligent monitoring and care throughout a pipeline’s life cycle. Therefore, companies relying on pipelines must conduct regular testing, inspection, and maintenance to effectively manage risks and ensure compliance with regulatory requirements regarding their operations and performance.
Pipeline Inspections: Checking Pipeline Integrity
The most effective way to check the integrity of a pipeline is through regular pipeline inspections which should take place throughout the entire service life of the pipeline. The aim is to identify issues such as corrosion, cracks, loss of cover, third-party damage, loss of wall thickness, damage to coating, and leaks that could compromise pipeline performance.
To achieve this, inspections utilize a range of methods to evaluate the condition, strength, and overall performance of both above-ground and underground pipelines, delivering vital insights into their structural integrity.
Focus areas for Pipeline Inspections
Testing pipeline integrity involves several methods designed to assess the condition of pipelines and identify potential threats. Below is a detailed overview of the key focus areas for pipeline inspections, along with their corresponding evaluation methodologies:
Internal Condition Evaluation
- Method: In-Line Inspection (ILI)
Known as “intelligent pigging,” ILI tools traverse the pipeline to gather data on its internal condition. This method effectively detects internal corrosion, geometric anomalies, and other defects.
External Condition Evaluation
- Methods: Visual Inspections and Non-Destructive Testing (NDT)
Visual Inspections: Regular checks are conducted to identify visible signs of damage, coating deterioration, or environmental threats on the pipeline’s exterior.
NDT: Techniques such as ultrasonic testing, magnetic particle inspection, and radiographic testing are used to detect flaws without compromising the pipeline’s integrity.
Corrosion Protection Verification
- Method: Cathodic Protection Monitoring
This approach evaluates the effectiveness of cathodic protection systems by measuring voltage potentials and assessing current distribution. It ensures adequate protection levels to prevent external corrosion in buried pipelines.
Burial Depth Verification
- Method: Depth of Cover Survey
This survey measures the vertical distance from the top of an underground pipeline to the ground surface above it. It ensures pipelines are buried at depths compliant with regulatory standards, protecting them from accidental damage during excavation, third-party interference, or environmental factors.
Structural Integrity Evaluation
- Method: Pressure Testing
This test assesses the pipeline’s ability to withstand operational pressures. It may use liquid or gas as the testing medium to evaluate the pipeline’s structural integrity under simulated operating conditions.
The data gathered from the inspections is then used in pipeline integrity assessments, which contribute to long-term planning for pipeline management, enhance safety protocols, inform maintenance strategies, support regulatory compliance, and optimize resource allocation.
Pipeline Integrity Assessments: Evaluating Pipeline Integrity
Pipeline assessments systematically evaluate the condition, integrity, and safety of the pipeline systems. While they utilize data collected during inspections, assessments go beyond merely identifying immediate issues. They involve a more in-depth analysis that includes risk-based analysis, fitness-for-service evaluations, and corrosion assessments.
This thorough examination helps experts identify defects or damage that may not be visible during routine inspections, providing a more thorough understanding of the pipeline’s overall health and reliability.
Utilizing the data of inspections, these assessments aim to answer critical questions related to pipeline integrity, including:
- What is the current condition of the pipeline?
- Are there any anomalies or defects present?
- What are the potential risks associated with identified defects?
- How do different segments of the pipeline compare in terms of risk?
- What is the pipeline remaining life?
- Will my pipeline reach the end of the design life?
- What maintenance actions are necessary to mitigate risks / extend the remaining life of the pipeline?
- Until when is my pipeline fit for service?
- Is the pipeline operating within safe pressure limits?
- When should I next inspect my pipeline?
- What is the likelihood of future issues occurring?
- How effective are existing integrity management programs?
Now, let’s delve into various assessment methods that provide insights into these important questions.
Methods of Pipeline Assessment
To effectively evaluate pipeline integrity, a range of methods is employed to assess the condition of pipelines and identify potential risks. Key assessment techniques include:
- Direct Assessment: This method measures how quickly internal and external corrosion is affecting the pipeline, allowing for proactive maintenance. It involves identifying the root cause of corrosion and determining the factors driving corrosion rates. By mitigating those drivers, the overall corrosion rate can be significantly reduced. Stress Corrosion Cracking Direct Assessment is also part of this method, which specifically evaluates the pipeline’s susceptibility to cracking caused by the combined influence of stress and a corrosive environment.
- Maximum Allowable Operating Pressure (MAOP) Assessment: This evaluation ensures that the pipeline’s operating pressure does not exceed the established MAOP limits.
- Risk-Base Assessment (RBA): Evaluating the level of risk associated with specific pipeline segments allows you to prioritize maintenance efforts effectively.
- Failure Mode and Effects Analysis (FMEA): This systematic approach identifies potential failure modes, their causes, and effects. FMEA helps you prioritize risks based on their severity, occurrence, and detectability, guiding you in taking corrective actions to prevent failures.
- Fitness-for-Service (FFS) Assessment: FFS evaluations determine whether a pipeline can continue to operate safely despite any flaws or degradation it may have experienced. This assessment considers factors such as material properties, design specifications, operating conditions, and historical performance data to ensure that the pipeline is suitable for continued use.
These assessments are not just a one-time effort; they form a continuous process that helps prevent failures and mitigate risks associated with pipeline operations.
Long-Term Vision: Investing in Pipeline Longevity with IMS PLSS
Here’s the hard truth about pipeline integrity: it goes beyond mere compliance and checklists. It’s about saving lives, protecting our planet, and keeping your business running smoothly. Let’s break it down:
- Keep your Pipelines Safe: Pipeline integrity is your shield against disasters. Regular checks catch problems before they blow up (literally) into headline-making catastrophes.
- Keep the Flow Going: Think of your pipeline like a highway. You wouldn’t let potholes grow until cars can’t pass, right? Same deal here. Spot issues early, fix them fast, and keep your business moving.
- Keep your Business Cost-Effective: Sure, integrity checks cost money. But you know what costs more? Emergency repairs and shutdowns. It’s like changing your oil regularly versus waiting for your engine to break down.
- Stay Compliant with Regulations: Regulators aren’t your enemies – they’re trying to keep everyone safe. Stay on top of your integrity game, and you’ll avoid nasty fines and reputation-damaging headlines.
- Keep the Environment Safe: We’ve only got one planet. Keeping your pipelines in top shape means fewer leaks and spills. It’s not just good PR – it’s the right thing to do.
- Think Long-Term: Treat your pipeline right, and it’ll be with you for the long haul. Regular care means you’re not shelling out for premature replacements.
The bottom line is that pipeline integrity is an investment in your future. However, as the complexity and volume of data from inspections and assessments grow, managing this information can become increasingly challenging. This is where a robust software solution that can efficiently manage this information comes in handy.
Cenosco’s IMS PLSS software rises to this challenge, providing a powerful platform that centralizes and analyzes inspection data, facilitates degradation management, and enables critical assessments such as Fitness-for-Service (FFS) and Risk-Based Assessment (RBA), along with evaluations of both internal and external corrosion. It simplifies equipment and barrier management by determining when the next integrity inspection is due and streamlining the scheduling process.
Our integrated platform comes with a powerful tool that calculates the remaining life of your equipment based on corrosion tolerance and corrosion rates while also guiding you in identifying necessary repairs and scheduling them to effectively mitigate corrosion, prevent failures, and extend the lifespan of your pipelines.
Request your demo today!
Take the first step towards better pipeline integrity with IMS PLSS
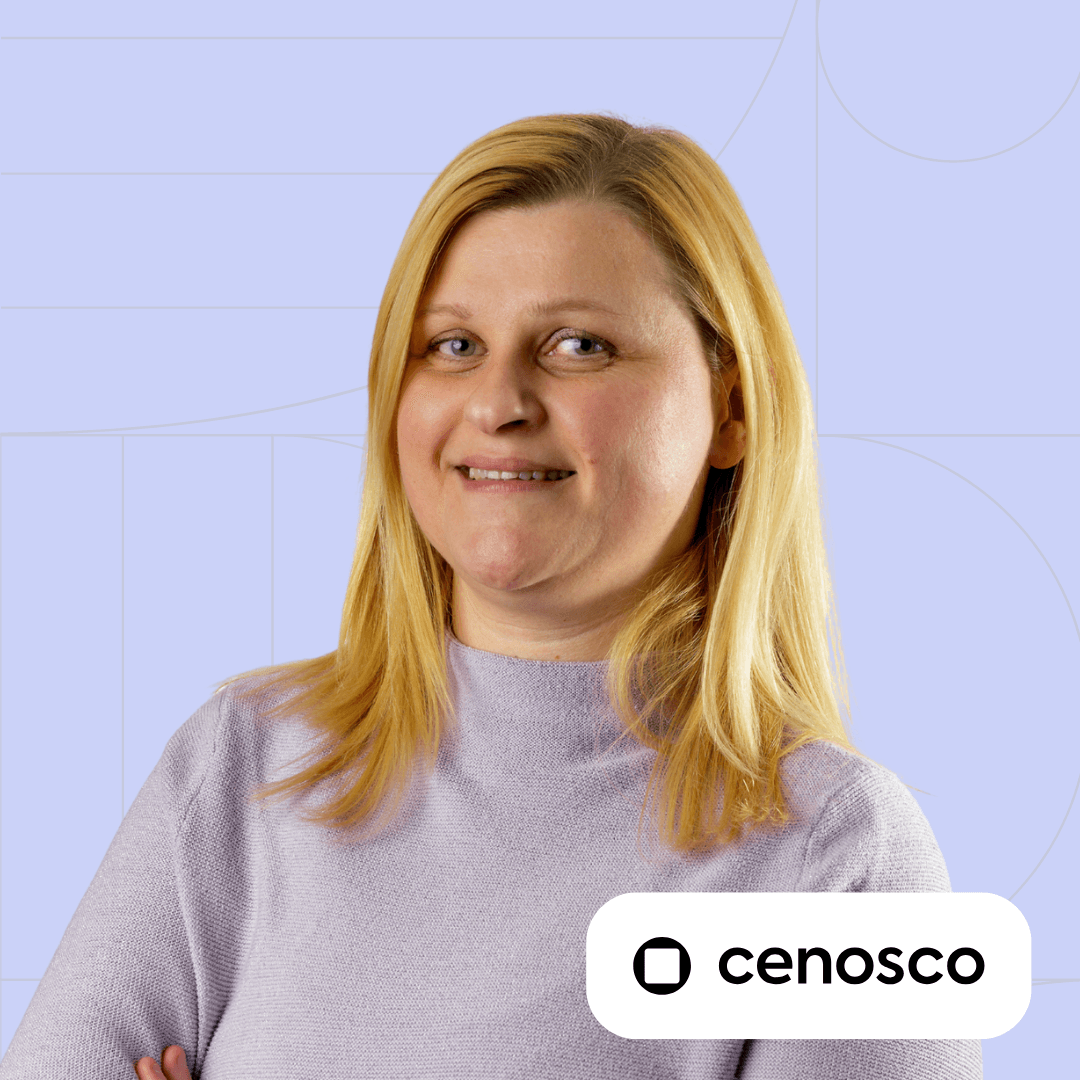
Denis Tkalec Technical writer
Denis Tkalec is a technical writer at Cenosco, specializing in asset integrity management software since 2022. With a background in education and six years in marketing, she turns complex topics into clear, user-friendly content. Inspired by Camus’s belief that “a writer keeps civilization from destroying itself,” she brings precision and care to every manual.