It may sound like a cliché, but it’s still true – organizations face ongoing challenges to maintain optimal operational uptime for essential equipment, sustaining uninterrupted production despite diminishing maintenance funds, rising equipment complexity, and a decrease in workforce. The key is, of course, to find the most cost-effective maintenance strategies in the midst of all these challenges.
In this blog, we’re going to explore how to figure out if a maintenance strategy really makes financial sense and also explore how to compare maintenance strategies in terms of cost-effectiveness.
Let’s start by considering the Reliability Centered Maintenance (RCM) approach to see where the whole cost-effectiveness question comes into play.
Reliability Centered Maintenance (RCM) and the cost-effectiveness question
The primary goal of RCM is to ensure the reliability and availability of critical assets while minimizing maintenance costs. This methodology involves addressing the Seven Questions of RCM.
Notably, Question 7 focuses on evaluating the cost-effectiveness of a maintenance strategy, but before delving into that, let’s take a look at Question 6.
Question 6: What can be done to predict or prevent each failure?
So, to answer Question 6, you need to determine what predictive and preventive maintenance strategies can be employed to manage equipment failures. This could involve regular inspections and tests, condition monitoring, component replacement, or redesigning parts of the system.
For example, for a pump, the maintenance strategy could be vibration and temperature monitoring, replacement of lube-oil, regular inspections, and timely replacement of worn-out parts.
Question 7: What should be done if a suitable proactive task cannot be found?
Then comes Question 7. This question requires you to determine if the tasks identified are suitable. If not, additional plans must be made.
Let’s focus on the first part of the question: Is the task suitable? In this sense, “suitable” means, firstly, there is enough risk reduction and, next, is it economically efficient, or cost-effective.
So, after confirming enough risk reduction, you need to determine whether or not the preventative maintenance strategy that you identified in Question 6 is cost-effective.
In the rest of this article, we will explore how we can tackle this challenge.
How to determine if a maintenance strategy is cost-effective?
Let’s assume you’ve already addressed the first six RCM questions. Therefore, you understand the full impact of equipment failure and how to predict or prevent failure. Consequently, you’re familiar with the degradation involved and know what the most suitable maintenance tasks are to implement. With this knowledge, you can then assess the three key costs:
- Base Risk Cost: The consequence cost of failure when no maintenance is performed.
- Maintenance Cost: The total cost of identified maintenance tasks.
- Residual Risk Cost: The consequence cost of failure when the mentioned maintenance tasks are implemented.
Once you know the Base Risk Cost, the Maintenance Cost, and the Residual Risk Cost, you can compare the cost difference between scenarios with and without maintenance. If the cost of the do-maintenance scenario is lower than that of the no-maintenance scenario, the tasks can be considered suitable, or the maintenance strategy can be deemed cost-effective.
Let us look at a cost-effectiveness calculation example.
Cost-effectiveness calculation example
In your plant, one of the high-priority maintenance requests involves a pump. Seeking guidance on preventive maintenance tasks, you received the following information from specialists:
- The failure of the pump entails a consequence of $100k.
- Without intervention, the pump is expected to fail every two years.
- A proposed maintenance plan suggests two tasks annually, each costing $20k.
- Implementing this plan could extend the pump’s failure interval to every five years or more.
Now, you need to determine if this maintenance strategy offers a cost-effective solution.
Let’s break it down:
- The Base Risk Cost is $100k every two years, translating to $50k annually.
- The Maintenance Cost totals $20k per year multiplied by 2, resulting in $40k annually.
- The Residual Risk Cost amounts to $100k every five years, equivalent to $20k annually.
In summary, the no-maintenance cost stands at $50k per year, while the do-maintenance cost is $40k per year plus $20k per year, totaling $60k annually. Consequently, the do-maintenance approach proves to be more expensive than the no-maintenance scenario, indicating that the maintenance strategy is not cost-effective.
So, it seems that in this case, it would be better to run to failure, i.e., do no scheduled maintenance, or a different maintenance strategy should be investigated.
Calculating the maintenance strategy cost-effectiveness
Now, let’s express the Cost-Effectiveness calculations in terms of mathematical equations:
A Maintenance Strategy is Cost-Effective when:
No Maintenance Cost > Do Maintenance Cost
Where:

Where:
- PONC = Price of Non-Conformance
- ETBF = Estimated Time Between Failure*
- ETBC = Estimated Time between Conformance
- POC = Price of Conformance
* Don’t confuse ETBF, which is the estimated time between failures if you DO NO maintenance, with MTBF, which is the mean time between failures if you DO maintenance.
To reiterate what we said earlier, it’s important to adopt a practical approach by always first assessing risk reduction, ensuring that the Residual Risk is sufficiently low, or ALARP (As Low As Is Reasonably Practical). If there’s minimal risk reduction, the maintenance strategy is not adequate, and further effort is needed to determine a better approach.
However, if the risk reduction is sufficient, it becomes relevant to calculate the cost-effectiveness.
How to compare the cost-effectiveness of maintenance strategies?
Wouldn’t it be convenient to classify the correlation between your maintenance expenses and the consequences of failure into a standardized index? This would allow for the easy assessment and comparison of the cost-effectiveness of multiple strategies, with an emphasis on the improvement of the risk reduction versus the cost involved.
Below, we define such a cost-effectiveness index:
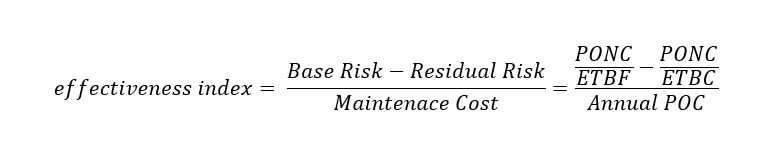
Let us use the data from our earlier cost-effectiveness calculation example for the pump maintenance strategy, and calculate the cost-effectiveness index for the pump’s maintenance strategy:

Examine this index closely. Do you notice what happens when the delta between the Base Risk and the Residual Risk, i.e., the risk reduction, equals the Maintenance Cost? Indeed! The cost-effectiveness index equals 1. This is when:
No Maintenance Cost = Do Maintenance Cost
When the maintenance strategy cost-effectiveness index equals 1, it indicates no-cost improvement. This implies that an effectiveness index below 1 signifies a loss. In such instances, it’s preferable to run the equipment to failure.
This is also what we see with our cost-effectiveness calculation example for the pump, where we have an index of 0.75, which is less than 1. For this pump example, we already determined earlier that it is most cost-effective to run to failure. Hence, the threshold for our index should be no less than 1, as maintenance strategies can only be considered cost-effective when:
effectiveness index > 1
However, it’s advisable to set this threshold slightly higher than one, as one represents just breaking even. Usually, when degradation is challenging to influence, the cost-effectiveness index tends to be lower.
Take the example of a chemical catalyst, which gradually deactivates over time, making it difficult for maintenance tasks to have a significant impact on the deactivation. Conversely, when degradation can be influenced, the effectiveness index can increase substantially. By setting a threshold of 2, we ensure a robust maintenance strategy where we know degradation is being affected.
effectiveness index > 2
An effectiveness index ranging between 1 and 2 should be regarded with suspicion, asking for closer investigation.
These maintenance strategies typically involve minor adjustments without substantial risk reduction. While there may be a learning benefit from the preventative strategies applied, the primary outcome is increased effort with minimal reduction of risk. To mitigate ineffective maintenance strategies, we should ensure a high enough cost-effectiveness index.
To conclude, having a standardized index with a defined threshold can prove highly valuable for evaluating and comparing maintenance strategies in terms of the improvement of risk reduction versus the cost involved.
IMS RCM software calculates the cost-effectiveness index
Our IMS RCM software incorporates calculations for just such a maintenance strategy cost-effectiveness index. The software guides you through relevant questions to gather necessary information, including Product Loss Equations (PLEs), for calculating Base Risk Costs, Maintenance Costs, and Residual Risk Costs.
Subsequently, the software calculates an index known as the Maintenance Efficiency Index (MEI) for each maintenance strategy and enables you to do “What If” analyses to evaluate alternatives.
Additionally, you have the option to set a desired MEI threshold for your site within the software. As a result, the software automatically calculates and displays which maintenance strategies are deemed cost-effective.
Request a demo
Want to get a first-hand look at IMS RCM? Fill out the form below.
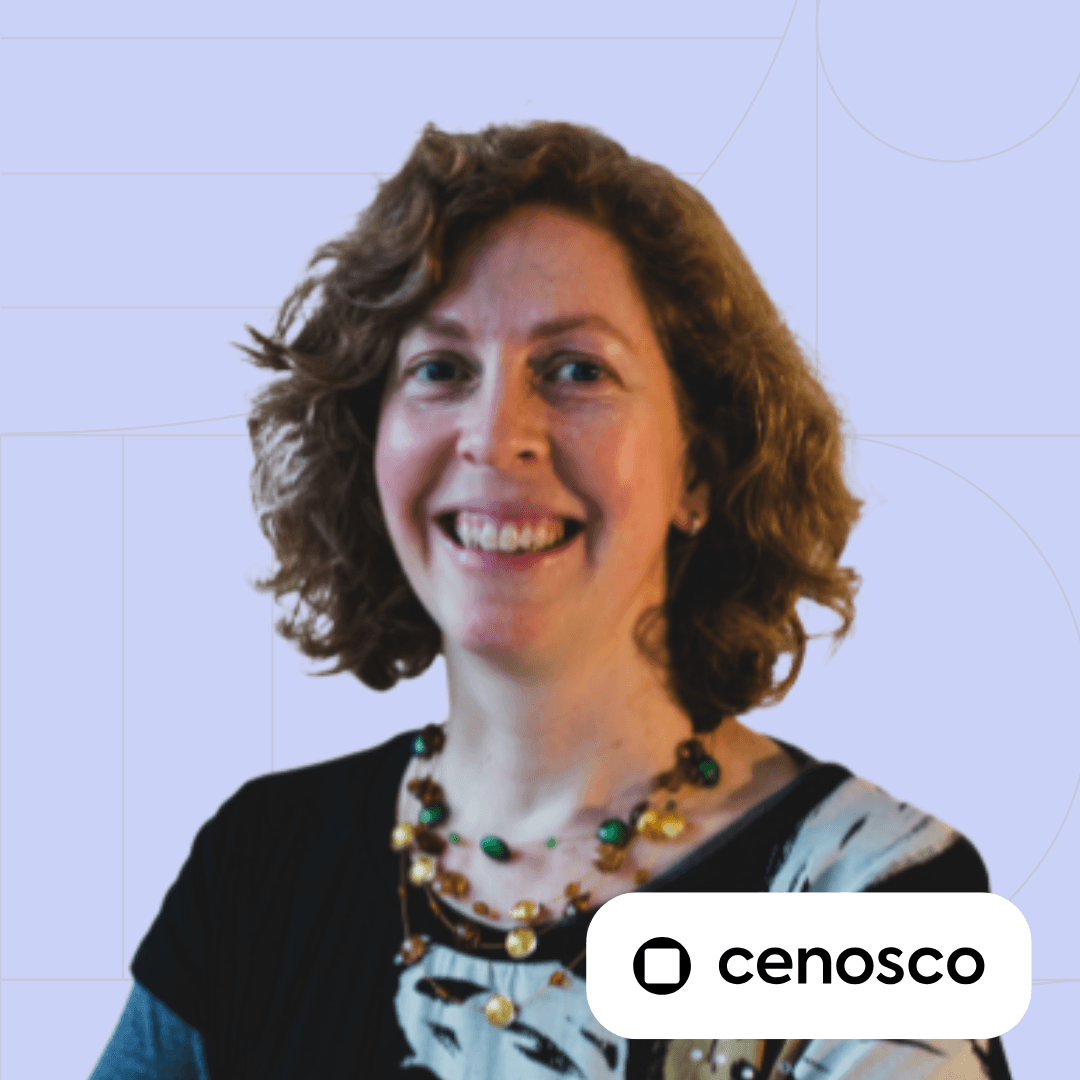
Elsa Tolsma-de Klerk Technical Writer
Elsa is an engineer with a passion for sharing knowledge. She holds a Master’s in Electronic Engineering and spent over a decade at Sasol as an Advanced Process Control Engineer, where she gained hands-on experience in optimization, control systems, and writing technical documentation. Since 2019, she’s been a Technical Writer at Cenosco, now leading the IMS knowledge base and training Academy team.