In an ideal world, pressure equipment would never explode, tanks would never fail, and pipelines would never leak. In reality, such equipment can and does fail, sometimes with devastating consequences. Equipment failures can lead to loss of life, environmental disasters, and significant financial losses, especially in asset-heavy industries like oil and gas, petrochemicals, and energy generation. The need to prevent failures has driven these industries to adopt rigorous inspection and maintenance protocols, ensuring that potential issues are detected before they escalate into disasters.
While the root causes of equipment failures can often be identified retrospectively, relying on after-the-fact analysis is far from ideal. For instance, if a boiler or pressure vessel fails, investigators can collect samples of the failed equipment for laboratory analysis to determine the cause.
This investigative process provides invaluable information that can be included in future equipment designs, and monitoring and maintenance programs, but only if failure has already occurred. In most cases, waiting for equipment to fail before taking action is not a viable strategy, especially when failure could lead to severe consequences.
One of the primary methods for preventing equipment failure is to assess equipment integrity using risk-based models to establish appropriate schedules and scopes for equipment inspections. These models prioritize and schedule equipment inspections based on potential risks, factoring in the likelihood of failure and the severity of consequences.
This approach allows companies to focus their resources on the equipment that presents the highest risk, ensuring that failures are identified and mitigated before they occur. By prioritizing high-risk equipment, the costly and potentially catastrophic outcomes that can arise from unexpected equipment failure can be avoided.
An essential component of such an inspection strategy is the use of non-destructive testing (NDT) to evaluate the condition of equipment. Non-destructive testing allows inspectors to identify potential problems—such as corrosion, cracks, or defects—without causing any harm to the equipment. NDT can often be conducted while the equipment remains in service, allowing operations to continue running while safeguarding human health and the environment.
Non-Destructive Testing: What is it?
As the name implies, non-destructive testing encompasses a variety of methods that allow inspectors to identify potential issues in equipment without causing damage. These techniques are important for equipment that is still in service or that needs to be returned to service quickly. Unlike more intrusive testing methods that can damage equipment being inspected, NDT enables the early detection of wear, damage, and defects.
Using NDT, technicians can identify hidden problems like internal cracking, corrosion, or metal thinning—issues that would otherwise be undetectable from a surface inspection alone. NDT not only minimizes downtime but also helps maintain equipment longevity, improves safety, and supports regulatory compliance. Below are some of the most commonly used NDT techniques.
Visual Testing (VT)
How It Works: Visual testing is the simplest and oldest form of non-destructive testing, using visual inspection to detect surface irregularities or visible signs of wear. It may involve the use of tools like borescopes, cameras, or drones to inspect areas that are otherwise difficult to reach. In some cases, visual inspections are enhanced by artificial intelligence, which can analyze images for early signs of defects.
Applications: Visual testing is used to inspect the external surfaces of tanks, vessels, and pipelines for visible damage, such as leaks, corrosion, or other forms of degradation. Drones and robots can be deployed to inspect hard-to-reach areas, allowing for comprehensive visual assessments without needing scaffolding or extensive downtime.
Ultrasonic Testing (UT)
How It Works: Ultrasonic testing uses high-frequency sound waves that are transmitted through materials. When these waves encounter a defect, they reflect differently, allowing technicians to locate and size internal flaws. The process is similar to how ultrasound is used in medical imaging but tailored for industrial use.
Applications: UT is widely used to measure thickness, locate internal defects, and detect corrosion. It is especially valuable for inspecting pipelines, welds, and storage tanks, where issues may not be visible on the surface. Ultrasonic testing can even detect early stages of corrosion or thinning, providing an advanced warning system for potential failure points.
Radiographic Testing (RT)
How It Works: Radiographic testing involves using X-rays or gamma rays to create images of equipment components. The radiation passes through materials and creates images on film or digital sensors. Variations in density caused by flaws or defects show up as shadows on the image, enabling technicians to identify and assess them.
Applications: RT is frequently used to inspect weld integrity, detect corrosion, and locate cracks, particularly in inaccessible areas of pipe, elbows, and pressure vessels. This technique is particularly effective for assessing welds, which are often points of vulnerability in high-stress environments. Radiographic testing can also be used to inspect thick-walled components, ensuring structural integrity where it’s needed most.
Magnetic Particle Testing (MPT)
How It Works: Magnetic particle testing applies a magnetic field to the equipment surface, then spreads magnetic particles over it. When there are surface or near-surface defects, they disturb the magnetic field, causing the particles to cluster around the area of the defect, making it visible.
Applications: MPT is especially effective for identifying surface and shallow subsurface defects in ferromagnetic materials. It’s commonly used to inspect pipelines, wellhead equipment, castings, and other ferromagnetic materials. Because MPT is a relatively simple process, it’s also a cost-effective option for routine inspections of susceptible equipment.
Eddy Current Testing (ECT)
How It Works: Eddy current testing uses an electromagnetic coil to generate currents within conductive materials, which can vary in intensity in response to flaws in the base material. The tool measures the eddy currents induced in the base material, allowing technicians to detect and characterize defects or corrosion.
Applications: ECT is ideal for inspecting non-ferromagnetic materials like stainless steel, commonly found in piping systems, heat exchangers, and offshore platforms. Because it’s sensitive to small changes, ECT is often used to inspect thin-walled tubing, detecting early-stage corrosion or small cracks that could lead to more severe issues.
Benefits of Non-Destructive Testing in Industry
NDT has transformed how industries handle equipment maintenance and inspection. They offer numerous advantages, including:
- Reduced Downtime: Many NDT methods can be performed while equipment remains in service, minimizing operational disruptions and allowing for continuous monitoring.
- Cost Savings: Proactively detecting issues helps prevent expensive emergency repairs or complete equipment replacements. NDT allows companies to schedule maintenance more strategically, lowering long-term costs.
- Increased Safety: NDT enables the early detection of potential failure points, reducing the likelihood of catastrophic incidents that could endanger lives and the environment.
- Extended Equipment Lifespan: Regular inspection with NDT techniques helps maintain equipment in peak condition, extending its operational life and improving return on investment.
- Regulatory Compliance: Many industries are heavily regulated, with strict safety and environmental guidelines. NDT plays a vital role in ensuring that companies remain compliant with these standards.
The Future of Non-Destructive Testing
As technology advances, NDT methods continue to evolve. Advanced imaging, automation, artificial intelligence, and machine learning are transforming traditional inspection processes, making them faster, more accurate, and more reliable. For instance, AI-driven analysis of images from visual inspections can detect irregularities that human inspectors might miss. Similarly, robotic systems equipped with ultrasonic or eddy current testing capabilities are improving the reach and efficiency of inspections.
In the future, NDT could become even more integral to asset management, with systems that use real-time data to anticipate potential issues before they arise. These advancements could revolutionize the approach to equipment maintenance, shifting from preventive measures to predictive solutions that enable companies to preemptively address risks.
In an ideal world, equipment would never fail, but with the power of non-destructive testing, we can come closer to achieving that ideal by minimizing the risks and maximizing the safety, efficiency, and longevity of critical assets.
Implementing an Effective Inspection Management Program
Designing and implementing an inspection and monitoring program for asset heavy industries is not a trivial task. An even harder task is keeping track and making sense of the collected information. At Cenosco, our goal is to enable you to make sure that your inspection and monitoring programs are designed and implemented to ensure the integrity, reliability, and safety of your operations.
IMS – the Integrity Management System – is designed from the ground up to help design and implement effective inspection programs, using risk-based models to prioritize and schedule equipment inspections. Our unmatched corrosion modeling capabilities use the data collected from your equipment inspections program to refine your inspection intervals so that you can ensure that limited inspection and maintenance resources are allocated efficiently and effectively.
To learn more about how IMS can improve the results of your inspection and monitoring programs, fill out the form below, or click here to learn more about IMS PEI.
Request a Demo
Find out how IMS can transform and optimize your operations…
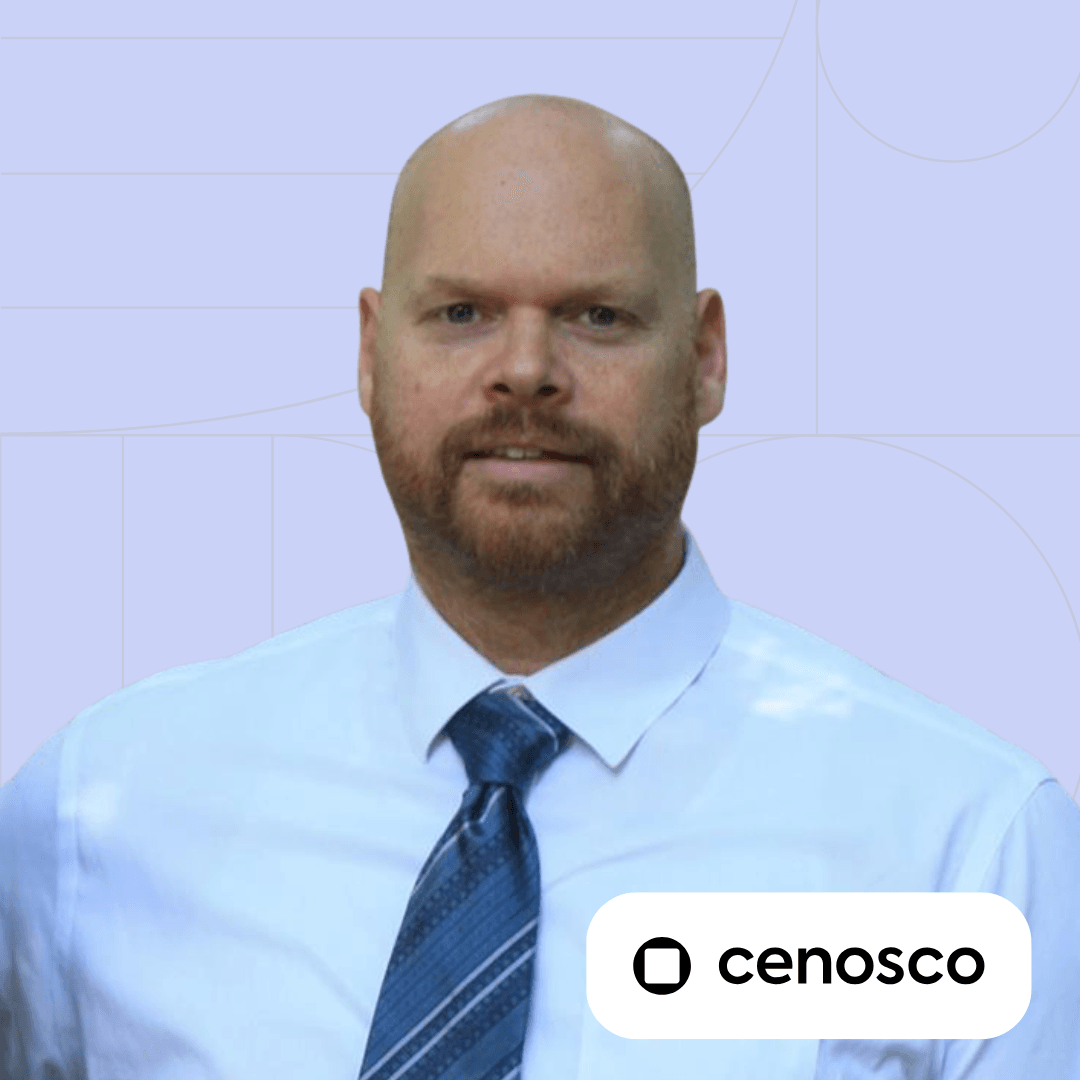
Tomislav Renić Technical Writer
Tomislav is an experienced engineer and technical communicator with over 20 years in complex systems, modeling, and project management. As a Technical Writer at Cenosco, he translates engineering concepts into clear, user-friendly documentation for software in the oil, gas, and refining industries.