In previous posts, we discussed some of the benefits of Reliability Centered Maintenance (RCM), as well as the P-F Curve, one of the key tools used in an RCM analysis.
In today’s article, we wanted to take a step back to the beginning to talk about strategies to optimize resource allocation when implementing RCM.
Reliability Centered Maintenance (RCM) Basics
Originating in the aerospace and aviation industry, RCM is an approach developed to deal with the growing complexity of industrial processes and equipment.
This systematic approach has evolved to find applications across various industries and is used in industries where the consequences of failure can be high, such as oil and gas, pharmaceuticals, and petrochemicals.
The primary goal of RCM is to ensure the reliability and availability of critical assets while minimizing maintenance costs.
Understanding the Core of RCM
International Standards, such as SAE JA1011 and IEC 60300, define the specifics of an RCM implementation. At its core, the process aims to answer the Seven Questions of RCM:
- What are the functions and associated performance standards of the asset?
- In what ways can it fail to fulfill its functions?
- What causes each functional failure?
- What happens when each failure occurs?
- In what way does each failure matter?
- What can be done to predict or prevent each failure?
- What should be done if a suitable proactive task cannot be found?
We will go into more details on these seven questions in a future article.
The seven questions can be applied in four basic steps:
Identification of Critical Assets
RCM starts by identifying assets critical to an organization’s operations, prioritizing those with a potential for significant impact on safety, productivity, or costs. By adopting a risk-based approach, organizations can concentrate efforts on assets with higher risks, avoiding unnecessary allocation of time and capital on low-risk items.
Understanding Failure Modes
The next step is to assess the effects of different failure modes on equipment and processes and is known as Failure Mode and Effect Analysis (FMEA).
It requires detailed analysis of potential failure modes, requiring a comprehensive understanding of how and why failures occur, and the likelihood and consequences of those failures.
FMEA forms the basis for the development of maintenance strategies and preventative maintenance tasks and requires a thorough understanding of equipment design, production processes, and maintenance history. IEC 60812 is a standard that describes how to perform an FMEA.
Selecting Maintenance Strategies
An important aspect of a risk-based approach to developing a maintenance program is that if there is an elevated risk associated with equipment failure, then more maintenance should be done. If there is less risk, less maintenance can be done. If there is NO risk, NO maintenance needs to be done.
RCM uses such a risk-based approach to determine maintenance intensity. Put simply, the level of risk dictates the available maintenance budget, reinforcing the idea that higher risk justifies more maintenance.
A key concept used in RCM is that of residual risk. It is the level of risk that remains after implementing a chosen maintenance strategy given the expected degradation of a piece of equipment.
The concept of residual risk is used to evaluate the Maintenance Efficiency Index (MEI) for a given maintenance strategy. For a maintenance strategy to be beneficial, MEI should be above 1, with a greater benefit accruing with a higher MEI.
Developing Maintenance Plans
The results of the RCM study are then used to guide the development of maintenance plans and schedules with tasks tailored to the critical equipment involved. This involves interaction with maintenance departments for the creation of efficient preventive maintenance programs to minimize waste and maximize efficiency.
RCM Strategies for a Successful Implementation
The benefits of RCM lie in its ability to enhance equipment reliability, reduce maintenance costs, improve safety, and inform decision-making in industry. As organizations navigate evolving challenges, RCM remains a cornerstone for achieving operational excellence, ensuring critical assets consistently perform at their best.
However, effectively implementing RCM is not a trivial task. The process is resource intensive and there are some strategies that should be kept in mind to help with a successful RCM implementation.
Firstly, we should touch upon some potential pitfalls to avoid when developing your RCM implementation.
Potential RCM Pitfalls, and How to Avoid Them
There are a few recurring themes that can lead to an inefficient and sub-optimal RCM implementation:
- Scope Definition: RCM studies often start with poorly defined scope and boundaries. As a result, the studies tend to extend to equipment with low criticality, resulting in the significant expenditure of effort with no potential for return. To avoid this, a detailed and agreed upon scope needs to be defined at the outset of an RCM study.
- Consultation: Often RCM studies are discussed where only a few participants are involved. To avoid this a multi-disciplinary team should be used and should include representation from operations, technology, technical disciplines, and maintenance. The topics discussed in the team should be relevant to all involved.
- Quality Checks: Offline reviews of collected data should be conducted to identify information gaps and partial analyses prior to the finalization of an RCM study. This allows the opportunity for focused, efficient corrections.
- Expertise and Experience: Conducting RCM studies from scratch can result in significant duplication of effort. Offline quality checks, reuse of analyses, conversion into reliability templates, and close cooperation with maintenance planners can significantly optimize resource usage.
- Starting from Scratch: Instead of starting each analysis from scratch, facilitators should make use of previously completed scenarios, generic approaches and strategy libraries to analyses to minimize the upfront work required.
- Handover: For the handover of an RCM study to execution, close cooperation between the RCM facilitator and maintenance planners should be maintained to help create efficient preventive maintenance plans for each component of the RCM study.
Above, we touched on some of the strategies used to avoid pitfalls in an RCM implementation. Next, we should think about strategies required to implement RCM successfully.
Allocation of Resources
- Initial Implementation Costs: Implementing RCM from scratch incurs high initial costs involving personnel, training, and tools. Resource-intensive steps include data collection, analysis, and expertise development, particularly in complex asset systems.
- Data Collection and Analysis: To complete an RCM study effectively, organizations need access to accurate and comprehensive data on their assets and historical performance. Collecting, validating, and analyzing this information can be resource-intensive, particularly if it has not been collected in the past.
- Complexity of Assets: The resource intensity of RCM can vary depending on the complexity of the assets being analyzed. Complex systems with interconnected components require more in-depth analysis and more resources.
Phased Implementation
The size and scope of an RCM initiative affects resource requirements. Organizations with many critical assets may find that implementing RCM across the board demands too much manpower and time.
To deal with this, an organization might adopt a strategic approach to reduce the RCM scope and focus on those assets involved in incidents and those that incur high maintenance costs. Such a phased approach, focusing on critical assets and high Maintenance Efficiency Index (MEI) maintenance strategies, can minimize resource load while facilitating learning and understanding of the methodology.
Organizational Changes
Implementing RCM often involves a shift in organizational culture and processes.
Managing change, getting buy-in from stakeholders, and ensuring that RCM practices are integrated into existing maintenance routines can be resource-intensive. It is important to highlight the urgency to do RCM, and to return guidance from RCM studies. A clear vision regarding reliability and RCM should be shared, and obstacles found should be removed.
After implementing RCM, organizations need to continuously monitor and refine their maintenance strategies based on feedback and performance data. This ongoing process can require ongoing resources for data collection, analysis, and adjustments to maintenance plans. Through a proper QA process, the learnings can be used to revise the RCM studies, resulting in the accrual of additional benefits in the future.
To fully leverage RCM, organizations may need to invest in technologies such as condition monitoring systems, predictive maintenance software, or sensors. While these technologies can lead to long-term cost savings, the initial investment can be significant.
Wrapping it up…
While implementing RCM may seem resource-intensive initially, the long-term benefits outweigh the costs. The focus on optimizing maintenance efforts results in reduced costs, increased reliability, extended asset lifespans, and improved safety. The positive side effects include improved understanding and cooperation across disciplines.
To mitigate resource costs, organizations can take a phased approach, prioritize critical assets, and leverage technology and expertise. Clear communication, commitment to long-term benefits, and formal reviews contribute to a successful and cost-effective RCM implementation.
Additionally, thorough planning, clear communication, and a commitment to RCM’s long-term benefits can help ensure a successful and cost-effective implementation.
How Can Cenosco Help?
Cenosco’s IMS (Integrity Management System) software suite includes the RCM (Reliability Centered Maintenance) software. IMS RCM helps optimize your maintenance strategy by preventing unplanned failure and improving asset availability through maintenance. IMS RCM can help you determine the best time to perform maintenance on an asset to prevent it from failing.
IMS RCM also provides access to an exclusive library of maintenance models, allowing users to create a cost-effective maintenance strategy in a single step.
Cenosco also has domain experts with decades of experience in designing and implementing RCM studies. Contact us to learn more about how we can help with your RCM implementation.
Request a Demo
Fill out the form below to get a free consultation and see IMS RCM in action.
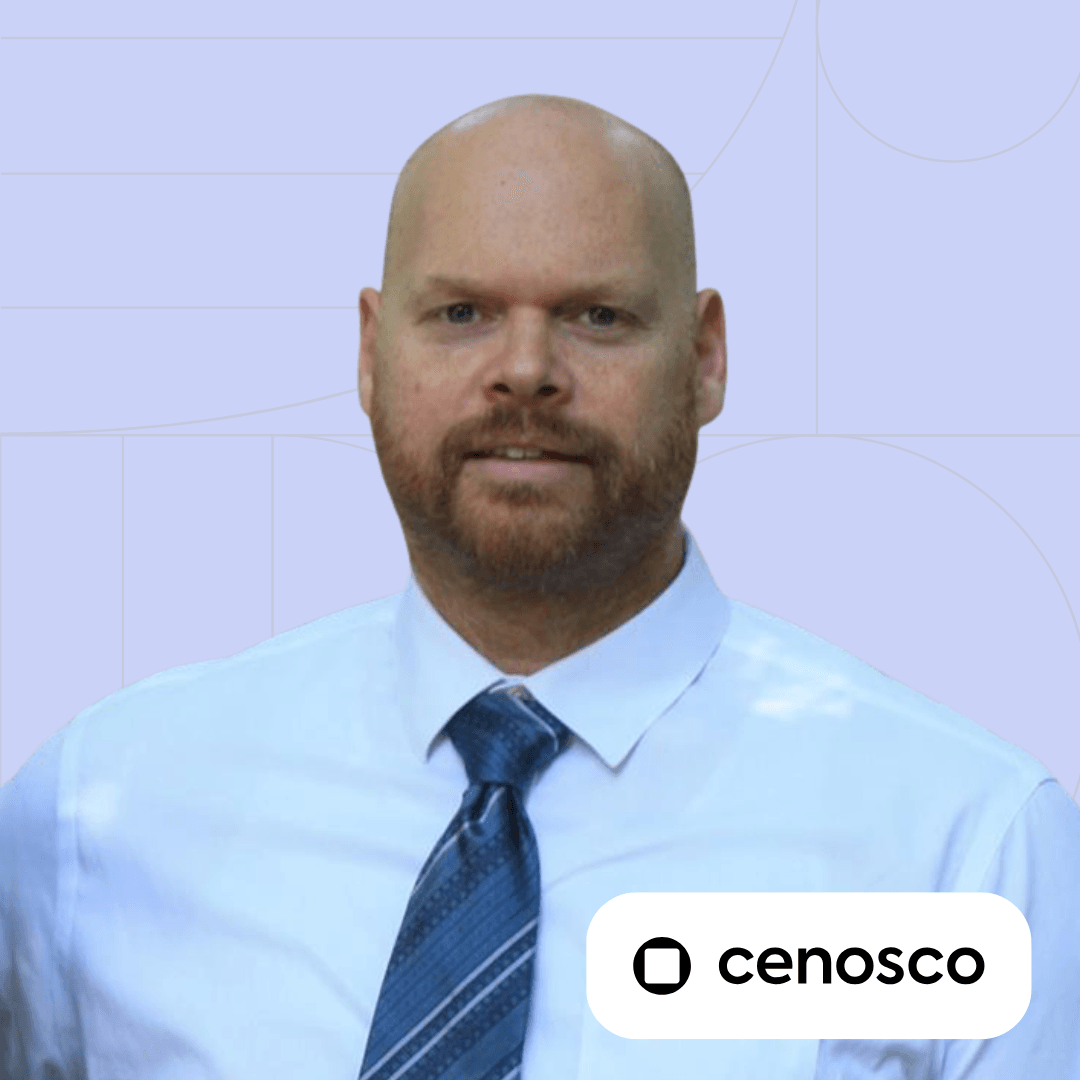
Tomislav Renić Technical Writer
Tomislav is an experienced engineer and technical communicator with over 20 years in complex systems, modeling, and project management. As a Technical Writer at Cenosco, he translates engineering concepts into clear, user-friendly documentation for software in the oil, gas, and refining industries.