In a recent blog, we broached the subject of Optimizing Resource Allocation when implementing Reliability Centered Maintenance (RCM) to help develop an effective inspection and maintenance plan. We touched on the origin of RCM and the Seven Questions of RCM. In today’s post, we delve deeper into the fundamentals of RCM and talk about the Seven Questions of Reliability Centered Maintenance (RCM).
Changing Perspectives on Maintenance
As the world, first slowly, then quickly, industrialized in the early part of the twentieth century, the production of goods became increasingly reliant on machinery. This was due to many factors including advancements in manufacturing technology and labour shortages during World War II.
Reactive Maintenance
Industrial facilities became more mechanized and maintenance programs increased in importance due to the need to ensure that manufacturing interruptions were minimized due to equipment failures. At first, maintenance programs focused on reactive approaches to repairing machinery after it had failed.
Proactive Maintenance
With time, industrial production became more efficient through approaches such as just-in-time delivery. These innovative approaches had the benefit of reducing inventories and allowing for more efficient supply chains, but it also meant that even a relatively small failure in one part of the production process could significantly impact industrial output.
In response to these new challenges, industrial maintenance programs turned to a more proactive maintenance approach based on the belief that the longer equipment was in service, the more likely it would be to fail. The maintenance programs relied on time-based maintenance and overhauls. This approach dominated through the 1960s and 1970s.
New Failure Theories
New industrial engineering research in the 1960s and 1970s showed that the previous understanding of equipment failure was not complete. It was now understood that different types of equipment had different failure modes, and that a one size fits all/ approach to maintenance resulted in wasted capital and unnecessary downtime.
The Seven Questions of Reliability Centered Maintenance
Through the 1970s, the US aerospace industry started to look more closely at their maintenance programs and developed processes to replace their previous time-based maintenance of airplane components. United Airlines, with support from the US Department of Defense wrote one of the first textbooks on this novel approach which was known as Reliability Centered Maintenance.
This approach was codified in SAE Standard JA1011, and later IEC 60300. At its core, Reliability Centered Maintenance revolves around seven key questions that help in identifying and implementing effective maintenance tasks. Below, we delve into these seven questions with a specific example.
1. What are the functions and associated performance standards of the asset?
The first step in RCM is to understand the functions of the asset and the performance standards associated with these functions. This involves defining what the asset is supposed to do, and the criteria for determining if it is doing it well. For example, the function of a fluid pump in a chemical plant might be to transport product from one part of the plant to another at a certain rate. The performance standard could be the ability to carry a specific volume of fluid per hour without failure.
2. In what ways can it fail to fulfill its functions?
The next step is to identify the different ways in which the asset can fail to fulfill its functions. This could include complete failure, partial failure, or degraded performance. For instance, the pump could fail completely (stops working), partially (works intermittently), or its performance could degrade (slows down).
3. What causes each functional failure?
Identifying the causes of each functional failure is crucial. These could be due to wear and tear, improper use, environmental conditions, or design flaws. In our pump example, causes could include worn-out impellers or bearings, excessive head differences, exposure to extreme temperatures, or a design flaw that makes it susceptible to frequent breakdowns.
4. What happens when each failure occurs?
Understanding the consequences of each failure helps in prioritizing maintenance tasks. The impact could range from minor disruptions to major system breakdowns. If our pump fails, it could lead to a slowdown in production, or in extreme cases, halt the entire production line.
5. In what way does each failure matter?
Each failure matters in a unique way. Some failures might have safety implications, others could impact production, and some might lead to higher maintenance costs. The failure of our pump matters because it directly impacts production efficiency. Failure could lead to increased operational costs, downtime, or wasted product.
6. What can be done to predict or prevent each failure?
Predictive and preventive maintenance strategies can be employed to manage each failure. This could involve regular inspections, condition monitoring, component replacement, or redesigning parts of the system. For the pump, vibration and temperature monitoring, regular inspections, and timely replacement of worn-out parts could help predict and prevent failures.
7. What should be done if a suitable proactive task cannot be found?
If a suitable proactive task cannot be found, a reactive approach might be necessary. This could involve running the asset to failure and then repairing or replacing it. In the case of our pump, if proactive tasks are not feasible or cost-effective, options might be to run to failure and then repair or replace the pump or to have a standby pump ready for service.
RCM is More than Just Seven Questions
The Seven Questions of RCM form the foundation of Reliability Centered Maintenance (RCM). However, to effectively implement RCM in an organization, it is essential to understand additional tools and concepts. Some key fundamentals and best practices for implementing RCM include:
- Identifying Points of Failure: This involves understanding the function and failure modes of assets, and their consequences.
- Selecting the Right Maintenance Strategy: Utilizing tools such as decision logic trees, risk matrix, and cost-benefit analysis to choose the most appropriate maintenance strategy for each asset.
- Implementing and Monitoring the Maintenance Plan: Defining maintenance tasks, intervals, resources, and performance indicators for each asset, and collecting/analyzing data on asset condition and failure rates.
- Leveraging Technology and Data: RCM software can streamline the RCM process by organizing data, performing analysis, and tracking performance and reliability indicators.
In addition to these, it is important to define system boundaries, identify resource requirements, and engage and train stakeholders for a successful RCM implementation. By understanding these concepts and utilizing the right tools, organizations can reduce costs, improve safety, and enhance customer satisfaction by implementing RCM effectively.
Meet IMS RCM
IMS RCM is Cenosco’s Reliability Centered Maintenance cloud-based software. It helps prevent unplanned failure by improving asset availability through maintenance. You don’t need to have an expensive maintenance plan to ensure the safety of your people and high asset availability. With IMS RCM, you will optimize your maintenance tasks so that you can operate as safely and budget-friendly as possible.
Improve your asset availability through maintenance.
Below we lay out some of the key features of IMS RCM. Explore the many ways in which our RCM software can help you gain control of your operations.
- Exclusive access to a Reliability Strategy Library created with Shell
- Dynamic Forms
- Manage Equipment Care Optimization
- Maintenance Efficiency Index
- Change and Deferral
- … so much more
Request a Demo
Ready to learn more about IMS RCM? Fill out the form below to learn more.
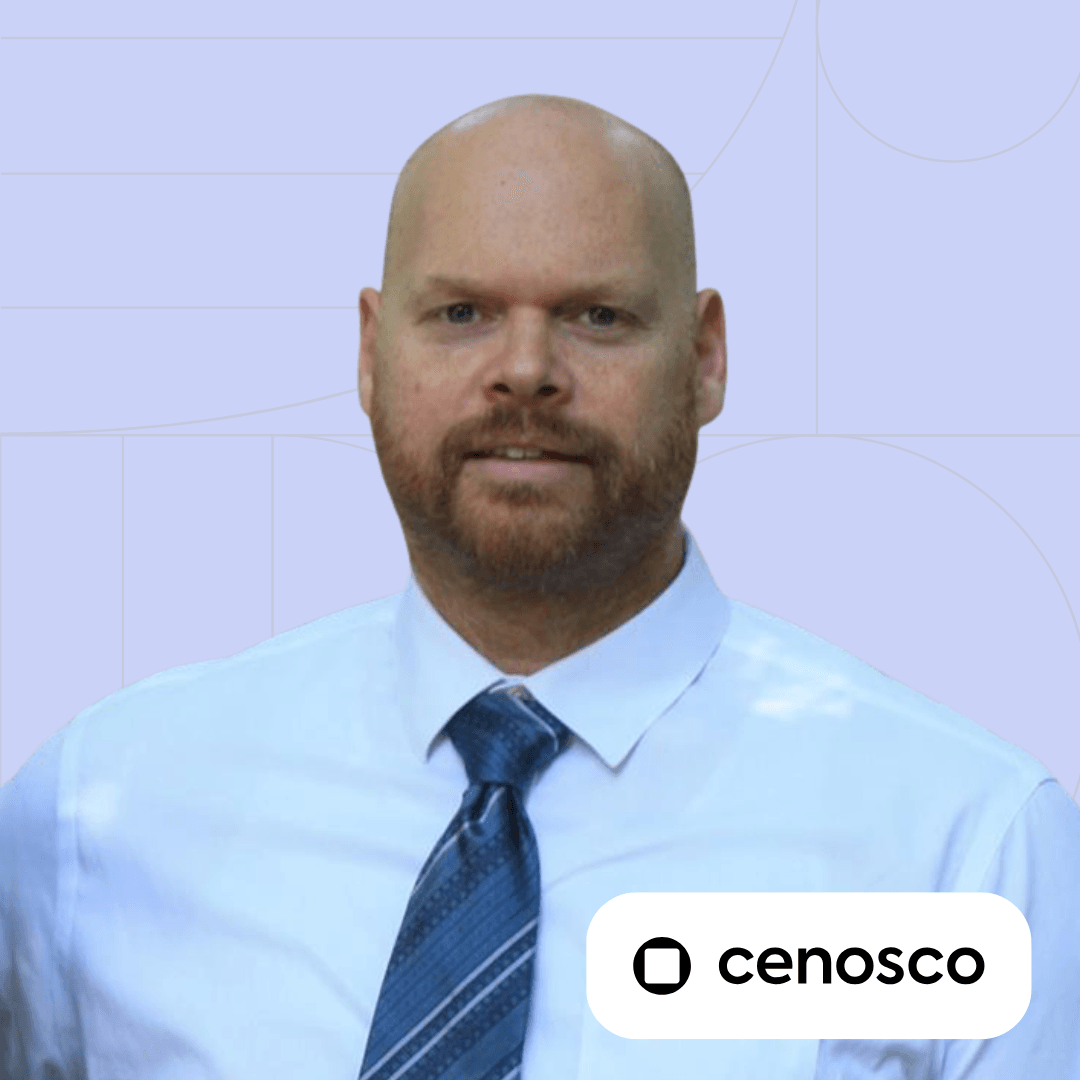
Tomislav Renić Technical Writer
Tomislav is an experienced engineer and technical communicator with over 20 years in complex systems, modeling, and project management. As a Technical Writer at Cenosco, he translates engineering concepts into clear, user-friendly documentation for software in the oil, gas, and refining industries.